A system that helps position specialized equipment on the seabed and can detect the end of coiled tubing inside a riser has been developed by AnTech. The Sub-Sea MDET Detection system "makes it possible to effectively 'see' through steel tubulars by way of remote audible and visible warning systems.
"This makes the process of proper equipment positioning a much more precise and controlled activity," claims Toni Miszewski, Managing Director of AnTech Ltd. The sensors are designed to clamp on to the outside of the riser; so they don't interfere with equipment or other necessary activities being carried out on the seabed. The sensor is strapped around the riser from the wellhead, where it can detect the passing of a magnetic marker and relay this information to the cabin, giving both a visible and audible warning alarm to the operators. Angle Valve

The MDET unit was originally designed to detect the end of coiled tubing through a riser, but as the equipment has evolved, other uses have emerged. These include the location of equipment using a magnetic marker both subsea and on the surface and the positive confirmation of the passing of equipment downhole. The latter includes the detection of cement plugs.
A newly formed company will deploy a tomographical inspection tool for use with flexible risers. The technology is based on the use of high-energy X-rays, combined with computer tomography (CT). The company, TomX AS, was formed by Aker Oil & Gas, Norsk Undervannsintervensjon (NUI), and Statoil. The technology was jointly developed by Statoil and Aker Inspection & Consulting AS.
The device works by combining a large number of digital X-ray pictures to make a 3D picture of the object under investigation. This technology has been used in the medical field since the mid 1970s, but it is only in recent years that the size of the equipment has been reduced to the point where it can be used offshore.
The increasing number of flexible risers and imperfect inspection technology on the world market create a good commercial foundation for TomX. In addition to the safety aspect of verifying the integrity of a riser, tomographic inspection, in combination with statistical methods of calculation, will create a basis for extending riser lifetime. TomX's aim is to deliver services for the inspection of flexible risers exposed to high pressure and the stress of high temperatures. The service will include interpretation of inspection data and recommendations to operators. The company aims to be in a position to provide the service beginning in 2003.
Schlumberger Oilfield Services acquired Phoenix Petroleum Services, which provides tools, technologies, and techniques for optimizing production in artificially lifted wells, particularly those using submersible pumps. Schlumberger says the acquisition of Phoenix, based in Inverurie, Scotland, was designed to increase the firm's global in-well monitoring and artificial lift services.
"Phoenix is a complement to our vision of real-time, integrated field and reservoir management," claims Peter Goode, President of Schlumberger Well Completions and Productivity. Phoenix has capabilities in optimizing production in artificially lifted wells and has synergies with Schlumberger in geoscience, data management, and information technology, explained John Schneider, Managing Director of Phoenix.
BJ Process and Pipeline Services (PPS) in Aberdeen will provide a range of process and pipeline services in the North Sea for Amerada Hess, including the producer's floating platform facilityAH001, the Scott platform, and the Triton floating, production, storage, and offloading vessel.
The service company will carry out safety-testing and maintenance, including nitrogen leak detection testing, purging, and temperature-controlled pipe freezing services. The contract also allows for the possibility of BJ PPS providing selected services, including pressure testing, chemical cleaning, and oil flushing services, intelligent pigging, umbilical testing, subsea telecommunications services, pipeline pigging/cleaning, pipeline dewatering, and pipeline drying (air/nitrogen/vacuum).
BJ PPS's pipe freezing service will be carried out for Amerada Hess in order to perform critical maintenance on specific portions of pipeline while the majority of the pipeline remains online. This means that Amerada Hess will be able to maintain optimal ongoing production. The five-year, call-out contract includes options to renew.
UWG completed a hot tapping project on the Shell Baram gas field in Sarawak, Malaysia, as part of the well abandonment process. The job involved a special, low torque soft seal adaptor. The adaptor was outfitted with an isolation valve and hot tapping assembly for the testing and depletion of pressure by drilling through the wellhead annulus valves. The project required equipment that would operate remotely or manually, subsea, due to the position of the platform. The contract was awarded in May to Claxton Engineering, a subsidiary of the UWG Group.
Hot tapping requires a drilling process to establish if pressure is present and, if so, to relieve the pressure in a contained environment. Hot tapping is a routine procedure commonly performed on pipelines and tubulars. This job was unusual because the hot tap was made into a submerged wellhead annuli, and thus presented a potential high pressure, hazardous operation. Claxton designed purpose-built equipment to carry out the job.
Subsea drilling equipment was built that could be remotely operated from the surface or manually with diver assistance. The equipment also had to maintain pressure containment capability. To perform this job, Claxton had to develop special cutters for drilling through excessively hardened material. These were tested onshore on tungsten-coated valve parts.
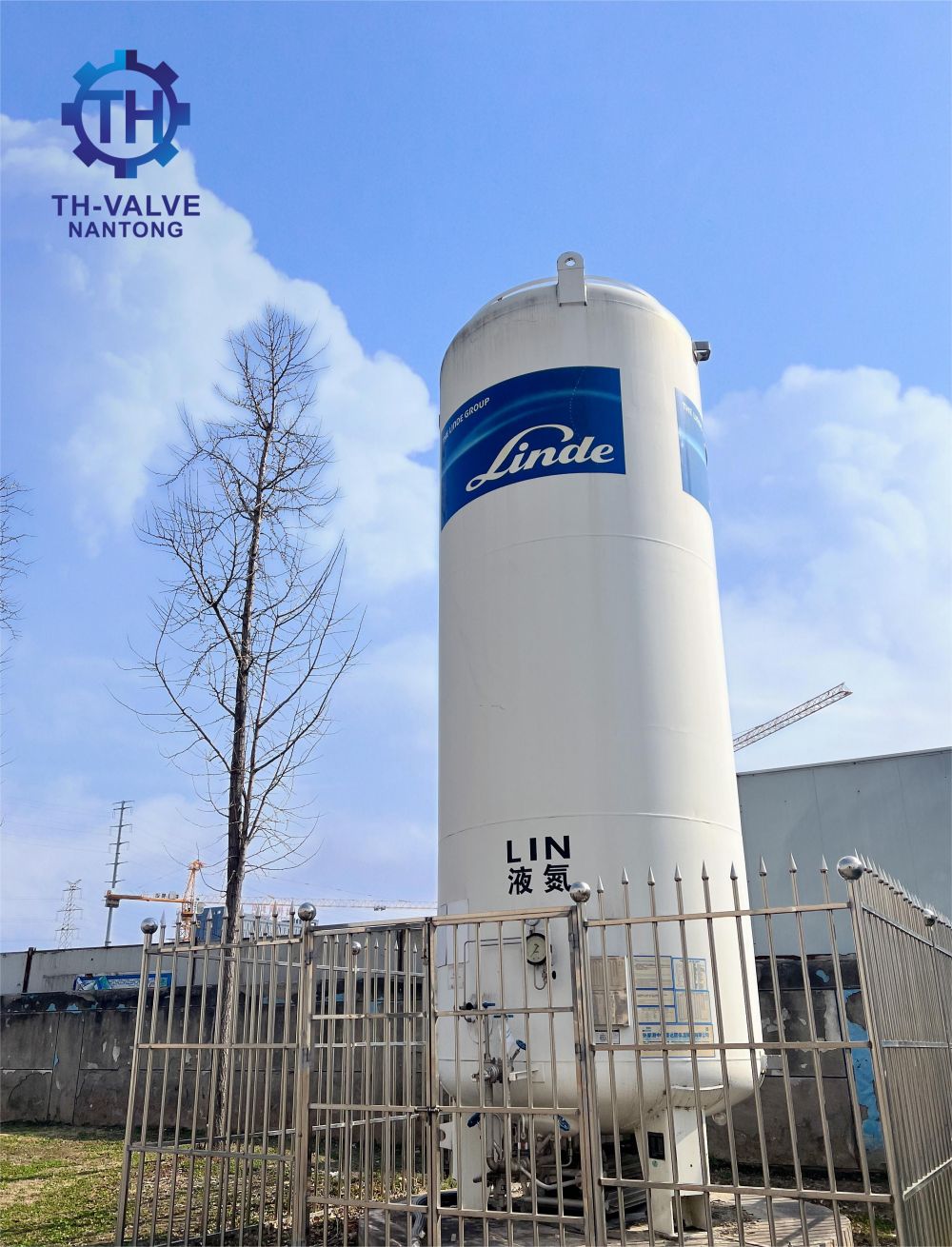
Y Type Piston Check Valve By creating a secondary valve for pressure containment, Claxton was able to conduct hot tapping operations on the wellhead, which was inclined 60 degrees from vertical, 135-ft subsea, in water depth of 180-ft. Drilling through the gate valve was completed in eight minutes with a maximum 40 psi recorded pressure in the well.