AIR’s eVTOL offerings now include an unmanned variation of AIR One for cargo and logistics use, featuring its agile design across different use cases.
Long-term supply agreements include KRD for windows, Latecoere for the aircraft’s doors, as well as Rallc and Alltec supplying composites expertise for fuselage development. Casting Of Ball Trailer Hook
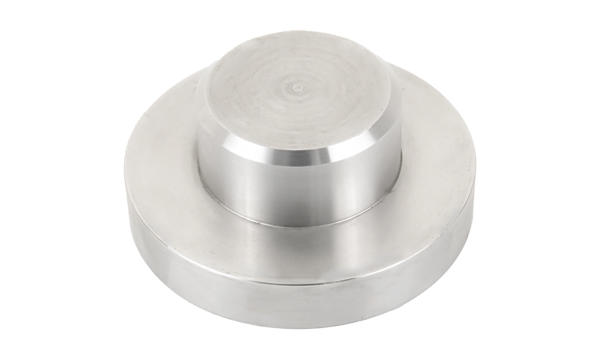
This is Archer’s second full-scale eVTOL aircraft to achieve this milestone, critical to being able to carry commercially viable passenger payloads.
Model includes new technologies produced at Performance Manufacturing Center (PMC) in Marysville, Ohio, which is part of Honda hydrogen business strategy that includes Class 8 trucks.
The composite eVTOL developer has now received two key operational certificates required from the FAA to begin operations when Midnight receives type certification.
Ragasco composite cylinders for LPG will become part of Worthington’s Building Products business, while Hexagon/Worthington Enterprises JV will target expanding storage and transport of CNG and hydrogen.
CAMX 2024: Fast and flexible AGX-V2 Series by Shimadzu provides more intelligent operability for testing tasks, supporting composites, plastics, metals and finished products.
Moldex3D users will now be able to conduct accurate 3D fiber orientation simulations using calibrated fiber parameters.
PolyMorphic Moulding technology uses 28,000 digitally controlled pins to create a shape from a 3D CAD shape in less than 20 minutes, achieving zero waste and enabling parts production 14 times faster than 3D printing.
CAMX 2024: Trilion Quality Systems is showcasing the Aramis optical strain gage, a material-independent measurement device with 3D-DIC capabilities.
An Aurora and Boeing team advances its high-speed, vertical lift concept to the preliminary design phase, which features three lift fans, a more refined composite exterior and an uncrewed cockpit.
Nesting, design, GUI and viewing features have been improved or added to the composites design software tool.
Avangrid recently donated 300 pounds of decommissioned wind turbine blades to test startup solution that recovers more than 90% of turbine blade material.
Powered by an 85% air/15% pure polyimide aerogel, Blueshift’s novel material system protects structures during transient thermal events from -200°C to beyond 2400°C for rockets, battery boxes and more.
Certification covers Tenax carbon fiber production at Heinsberg-Oberbruch, Germany, plant, adds to Teijin’s certifications for carbon fiber and PAN in Japan.
In an interview with one of Aptera’s co-founders, CW sheds light on the inspiration behind the crowd-funded solar electric vehicle, its body in carbon (BinC) and how composite materials are playing a role in its design.
Based on military feedback, Epsilon Composite developed an optimized, foldable stretcher that combines telescopic pull-wound carbon fiber tubes.
Equipment investment will enable the plastics processor to mass produce fiber-reinforced thermoplastic composites continuously, as well as adapt to specific needs.
CAMX 2024: Composite curing ovens by Wisconsin Oven provide a variety of features for comprehensive support, including temperature uniformity, energy efficiency, advanced controls and IoT, all backed by a dedicated team.
Additional financing is being secured to service automated fiber steering demand, build first RTS production facility in Gloucester.
Composite curing oven meets customer needs with ability to cure complex synthetic and composite parts.
In an interview with one of Aptera’s co-founders, CW sheds light on the inspiration behind the crowd-funded solar electric vehicle, its body in carbon (BinC) and how composite materials are playing a role in its design.
Based on military feedback, Epsilon Composite developed an optimized, foldable stretcher that combines telescopic pull-wound carbon fiber tubes.
CAMX 2024: Schmidt & Heinzmann customers are able to produce SMC or dry fiber fabric stacks more efficiently thanks to the AutoCut Pick&Place system.
Increasingly, prototype and production-ready smart devices featuring thermoplastic composite cases and other components provide lightweight, optimized sustainable alternatives to metal.
CW explores key composite developments that have shaped how we see and think about the industry today.
Knowing the fundamentals for reading drawings — including master ply tables, ply definition diagrams and more — lays a foundation for proper composite design evaluation.
Performing regular maintenance of the layup tool for successful sealing and release is required to reduce the risk of part adherence.
With COVID in the past and passengers flying again, commercial aircraft production is ramping up. The aerocomposites supply chain is busy developing new M&P for an approaching next-generation aircraft program.
Electrification and a focus on sustainability lead to opportunities and innovations in composites, from battery enclosures to structural components and more.
This webinar will cover infusion technology for the manufacture of aerospace composite structures. Hexcel will give an overview of different infusion processes, types of reinforcement and resin products available along with some example applications. Agenda: Benefits of Infusion Overview of resin infusion processes Reinforcement types Resins Processing Example applications
In addition to its proven fire resistance as a pure foam and within a sandwich composite system, the new material offers efficient manufacturing of 3-dimensional geometries and opens new possibilities for direct function integration. Agenda: Manufacturing process of thermoplastic particle foams Sandwich composite component requirements of commercial aircraft interior structures (e.g. FST, Heat Release) Function integration into net shape molded foam parts (e.g. inserts) Potential use-cases in fire critical applications
Find out how outsourced, costly tooling can be produced in-house to overcome bottlenecks, reduce costs and protect IP. Agenda: Explore durable casting materials that can be 3D-printed in complex designs Discover industry-proven Sika materials now available for high-speed, additive tooling Explore the benefits of thermoset molds that ensure uniform expansion, optimum bonding with the end part, as well as high durability
Thermoplastic material systems have been used in aerospace for decades. Their use and adoption continues to grow and Trelleborg has been on the leading edge of development for many of these systems. In this webinar, Trelleborg will be presenting a range of topics from the use of in-situ, automated fiber placement of thermoplastics prepreg for structural and functional products to complex injection molding of thermoplastic interior pieces. It will explore some of the benefits these products provide and the potential for future growth and development. Agenda: Current state of thermoplastics in aerospace Thermoplastic composite use cases for high-performance electric motors and torque tubes Injection-molded thermoplastic interior pieces The future of potential for thermoplastic applications for aerospace
KraussMaffei will explain in-situ polyurethane (PUR) overmolding of injection-molded and composite parts and the development of this technology over the last decade. Waruna Seneviratne, director of the Advanced Technologies Lab for Aerospace Systems (ATLAS), will discuss how aerospace and advanced air mobility (AAM) markets can capitalize on this high-rate manufacturing solution. Agenda: What is ColorForm: process, equipment and tooling Pros and cons of the technology High technology solution examples: ColorForm automotive Market references in automotive Demand for future commercial aviation and both AAM and urban air mobility (UAM) What aerospace can learn from automotive for addressing demand for high-rate manufacturing Technological advances enabling material and process improvements for the future Role of ATLAS manufacturing innovation center for promoting advanced manufacturing and workforce development Road map for certification through manufacturing demonstrations
Discover the latest innovation in laser projection technology poised to increase accuracy, efficiency and reliability. LAP will unveil the features of its new CAD-PRO Xpert laser projection system and outline how various industries can benefit from the system's capabilities. Its cutting-edge technology platform empowers users with enhanced color range, speed and superior laser projection quality while increasing accuracy, efficiency and reliability. Explore how the advanced ergonomics of this system can reshape composite manufacturing processes across industries, ranging from aerospace and automotive to wind rotor blade production, yacht building and beyond. Agenda: Introduction of the features of the CAD-PRO Xpert Applications and advantages across industries Upgrading workplaces for enhanced digital worker guidance Modular system solutions based on the value-adding ecosystem
The International Composites Summit (ICS) is renowned as the only solely focused UK event for professionals involved in the composites industry. ICS promises to be a unique platform for knowledge sharing, networking, and exploring the latest advancements in composite materials internationally, bringing people together to do business.
Join us at the ACCE 2023 event and learn about how the automotive and transportation industries are advancing with composites playing a key role in the development of electric vehicles and sustainability initiatives worldwide. Lightweight composites are ideal materials for improving vehicle performance, reducing mass, extending range and compensating for battery weight. Polymer composites are enabling lower emission vehicles, reducing the carbon footprint and saving energy to benefit the environment now and in the future. Thermoset and thermoplastic composites are the key to EV, Mobility and Sustainability.
The International Composites Summit (ICS), THE single place to do the most cost effective and sustainable composites business in the UK, is back for its highly anticipated 2023 edition, bringing together industry leaders, researchers, and innovators from across the composites sector. ICS promises to be a unique platform for knowledge sharing, networking, and exploring the latest advancements in composite materials internationally, bringing people together to do business. The International Composites Summit is renowned as the only solely focused UK event for professionals involved in the composites industry.
CAMX is your best source for new solutions, technologies, and ideas you need for your current and future projects. CAMX makes it easy to watch live process demos, see materials and interactive displays on what may be possible in the future, and meet with hundreds of manufacturers, distributors, and suppliers.
Debuting in 2010, the Parts Cleaning Conference is the leading and most trusted manufacturing and industrial parts cleaning forum focused solely on delivering quality technical information in the specialized field of machined parts cleansing. Providing guidance and training to understand the recognized sets of standards for industrial cleaning, every year the Conference showcases industry experts who present educational sessions on the latest and most pressing topics affecting manufacturing facilities today. Discover all that the 2022 Parts Cleaning Conference has to offer!
Thousands of people visit our Supplier Guide every day to source equipment and materials. Get in front of them with a free company profile.
Jetcam’s latest white paper explores the critical aspects of nesting in composites manufacturing, and strategies to balance material efficiency and kitting speed.
Arris presents mechanical testing results of an Arris-designed natural fiber thermoplastic composite in comparison to similarly produced glass and carbon fiber-based materials.
Cevotec, a tank manufacturer, Roth Composite Machinery and Cikoni, have undertaken a comprehensive project to explore and demonstrate the impact of dome reinforcements using FPP technology for composite tanks.
Initial demonstration in furniture shows properties two to nine times higher than plywood, OOA molding for uniquely shaped components.
The composite tubes white paper explores some of the considerations for specifying composite tubes, such as mechanical properties, maintenance requirements and more.
Foundational research discusses the current carbon fiber recycling landscape in Utah, and evaluates potential strategies and policies that could enhance this sustainable practice in the region.
In an interview with one of Aptera’s co-founders, CW sheds light on the inspiration behind the crowd-funded solar electric vehicle, its body in carbon (BinC) and how composite materials are playing a role in its design.
Based on military feedback, Epsilon Composite developed an optimized, foldable stretcher that combines telescopic pull-wound carbon fiber tubes.
While the world continues to wait for new single-aisle program announcements from Airbus and Boeing, it’s clear composites will play a role in their fabrication. But in what ways, and what capacity?
The total index reading backed down in May from its anticipated expansion, contracting again to land at 46.8.
Upon his one-year anniversary as editor-in-chief of CW, Scott Francis looks back at some of the brand’s changes and hints at where it might be heading next.
In 2018, Teijin broke ground on a facility that is reportedly the largest capacity carbon fiber line currently in existence. The line has been fully functional for nearly two years and has plenty of room for expansion.
PolyMorphic Moulding technology uses 28,000 digitally controlled pins to create a shape from a 3D CAD shape in less than 20 minutes, achieving zero waste and enabling parts production 14 times faster than 3D printing.
Proof-of-concept part used bio-based acrylontrile precursor with same performance as conventional CFRP but with significantly less CO2.
Recent conference in Denver, Colorado, emphasized the tools and knowledge composites manufacturers will need to meet customer and government sustainability goals.
Ultra-lightweight and made of recycled composites, the Eco Bracket cuts weight and cost in half and reduces CO2 emissions, in addition to providing high performance.
Brudeli’s patented plug-in Powerhybrid technology will use Hexagon Agility CNG/RNG fuel system with Type 4 tanks, enabling Class 7 and 8 trucks to meet ACT and ACF regulations.
Envalior 30% glass fiber-reinforced Akulon RePurposed material helps Ahrend achieve lighter task chair with closed-loop value chain and reduced emissions.
CW’s editors are tracking the latest trends and developments in tooling, from the basics to new developments. This collection, presented by Composites One, features four recent CW stories that detail a range of tooling technologies, processes and materials.
In the Automated Composites Knowledge Center, CGTech brings you vital information about all things automated composites.
The composites industry is increasingly recognizing the imperative of sustainability in its operations. As demand for lightweight and durable materials rises across various sectors, such as automotive, aerospace, and construction, there is a growing awareness of the environmental impact associated with traditional composite manufacturing processes.
Closed mold processes have many advantages over open molding. In this knowledge center, learn the basics and vital tools needed to produce parts accurately.
CompositesWorld’s CW Tech Days: Infrastructure event offers a series of expert presentations on composite materials, processes and applications that should and will be considered for use in the infrastructure and construction markets.
Explore the cutting-edge composites industry, as experts delve into the materials, tooling, and manufacturing hurdles of meeting the demands of the promising advanced air mobility (AAM) market. Join us at CW Tech Days to unlock the future of efficient composites fabrication operations.
Thermoplastics for Large Structures, experts explored the materials and processing technologies that are enabling the transition to large-part manufacturing.
Explore the technologies, materials, and strategies that can help composites manufacturers become more sustainable.
A report on the demand for hydrogen as an energy source and the role composites might play in the transport and storage of hydrogen.
This collection features detail the current state of the industry and recent success stories across aerospace, automotive and rail applications.
This collection details the basics, challenges, and future of thermoplastic composites technology, with particular emphasis on their use for commercial aerospace primary structures.
This collection features recent CW stories that detail a range of tooling technologies, processes and materials.
Machining and drilling processes in composites present unique challenges due to the heterogeneous nature of these materials. Composite structures, often composed of different layers and materials, require specialized techniques to maintain integrity and precision during machining or drilling. Traditional methods used for metals can cause delamination, fiber pullout, or damage to the composite structure. Therefore, specialized tools, such as diamond or carbide-tipped equipment, and specific cutting parameters are employed to ensure clean cuts without compromising the material's integrity.
Steptics industrializes production of CFRP prostheses, enabling hundreds of parts/day and 50% lower cost.
Designed through the European Fibremach project, the equipment provides a greater increase in precision and machining efficiency and integrates a monitoring system that ensures part quality.
The Italy-based companies merge technological know-how to develop novel systems for the processing and assembly of light alloys and carbon fiber components.
AI startup offers automation innovations for high-mix, high-variability, manual surface finishing applications.
Hufschmied moves beyond optimized milling and drilling tools to develop SonicShark inline quality control system and Cutting Edge World cloud platform for optimized tool use and processes.
This edition of From the CW Archives revisits CW’s first plant tour — a visit to the F-35 FAL in Fort Worth, Texas — and a story by Ginger Gardiner a few years later. Both offer lessons on how to perform stacked drilling through composite and metallic materials.
JEC World 2024: Compcut is presenting its advanced composites saw (ACS) and precision composite router (PCR), in addition to inviting attendees to bring their own materials for demonstration purposes.
CompositesWorld’s CW Tech Days: Infrastructure event offers a series of expert presentations on composite materials, processes and applications that should and will be considered for use in the infrastructure and construction markets.
The composites industry is increasingly recognizing the imperative of sustainability in its operations. As demand for lightweight and durable materials rises across various sectors, such as automotive, aerospace, and construction, there is a growing awareness of the environmental impact associated with traditional composite manufacturing processes.
CW’s editors are tracking the latest trends and developments in tooling, from the basics to new developments. This collection, presented by Composites One, features four recent CW stories that detail a range of tooling technologies, processes and materials.
Breiana Whitehead, pioneering Australian kite-foil sailor, spearheads board design intricacies with ATL Composites to enhance her performance ahead of the July 2024 competition.
CAMX 2023: Hufschmied’s machining systems, particularly the company’s 194/195 T-Rex cutting tools and carbide cutting blades, are being presented for use on plastics, composites and other materials.
The RoboMach HA is a high-accuracy robotic machining system that can work with a range of materials, including cured composites.
Multi-phase expansion includes 9,900-square-foot addition to facility and purchase of new equipment to better serve aerospace, marine, composites and other industries.
Fraunhofer IFAM and Airbus Operations in Stade demonstrate reduced manual handling and non-productive time in flow-oriented manufacturing of vertical tail plane.
The Augsburg AI Production Network — DLR Center for Lightweight Production Technology (ZLP), Fraunhofer IGCV and University of Augsburg — use ultrasonic sensors to correlate sound to quality in composites machining.
As the advanced air mobility market begins to take shape, market leader Joby Aviation works to industrialize composites manufacturing for its first-generation, composites-intensive, all-electric air taxi.
Four-year, 12-million-euro LaiLa project with Helmut Schmidt University combines R&D with industry collaboration to solve real production pain points, validate solutions in digital lab/model factory at CTC and transfer knowledge to supply chain including customized training.
A stalwart in Italy’s “Motor Valley” opens its doors for a discussion and exploration of the company’s history in composites manufacturing for high-performance cars and other applications.
Part of the company’s larger strategy for reducing cycle times and labor costs on its composite-intensive rockets, a customized machine center from Multiax America solves composite machining challenges.
Machining composite materials is a challenging task. Proper tool selection, machine settings and process innovations help make it manageable.
nebumind software builds digital twins from manufacturing data to trace defects, compare manufactured parts, qualify processes, develop tolerance windows for process monitoring and more.
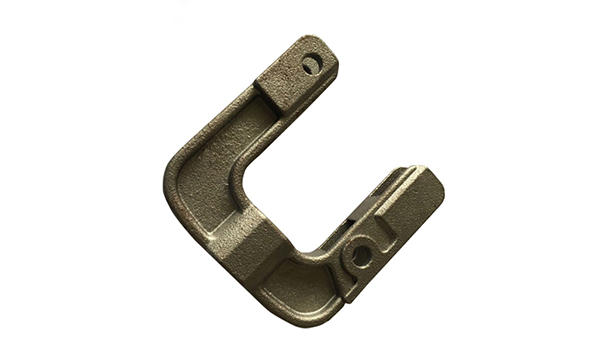
Aluminium Cold Forging CompositesWorld is the source for reliable news and information on what’s happening in fiber-reinforced composites manufacturing. About Us