Integration of speed sensors within electric drive systems has become standard practice to ensure efficient and optimized performance — enabling longer battery life and electric vehicle run times.
Unlike a combustion engine, the system’s electric motor can provide immediate torque – and thus movement for vehicles and mobile machines – even at slow rotational speeds. Therefore, it is important to integrate speed sensors which can detect close to zero speed or even real zero speed to ensure safety and performance, said Wolfgang Sexauer, Head of Sales & Marketing at Rheintacho. 13627525014
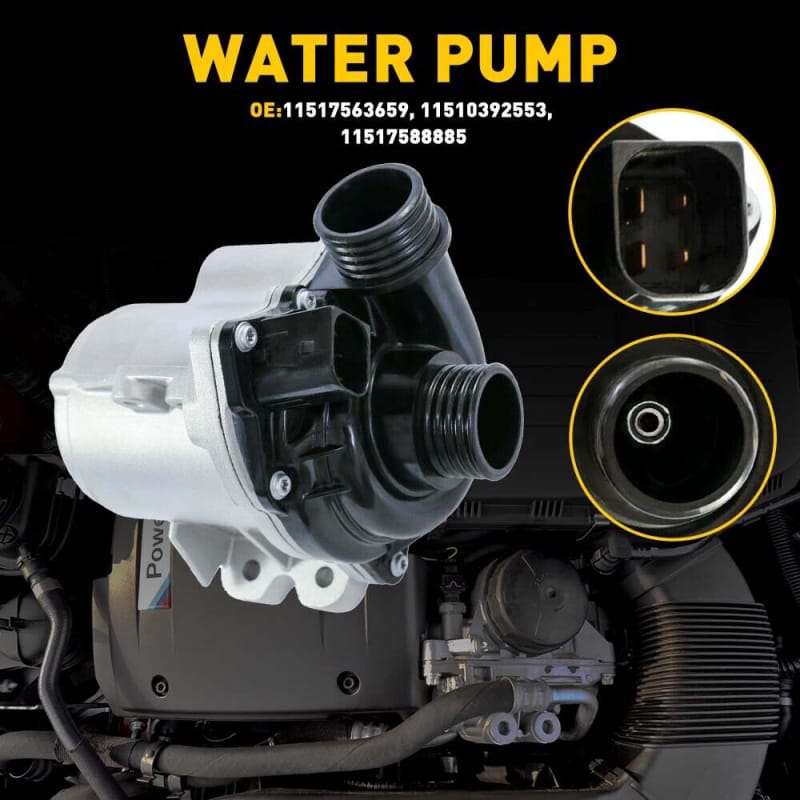
Editor's Note: Members can download a PDF version of this article.
He said there are other possible physical measurement solutions which could be used, but they only work at a higher rotational speed. Because electric motor speed has a direct impact on overall system performance, it is important to gain speed information right away, necessitating use of a sensor instead of other measurement solutions.
Electric motors are known to get extremely hot due to the speeds at which they operate. Testing conducted by Rheintacho found temperatures inside an electric motor can reach over 150 C (302 F). When higher temperatures are reached, the performance of electronics in the system can be negatively impacted.
Sexauer said once temperatures of 150 C or above are reached, there is a need for special components and other design features to ensure the desired performance is achieved. Optimal operating temperatures are around 80 C (176 F).
He also noted, that due to different driving situations, there are changing temperature situations inside an electric motor. This puts significantly more stress on all components than operating at a constant (high) temperature. As such, choosing the right components and the right designs are key to precise, long-term operation which is necessary to achieve the emissions reduction and other benefits posed by transitioning to electrification.
Integration of speed sensors can help with the implementation of autonomous driving functions as well. Joern Strasser, Business Manager for Speed Sensors at Rheintacho, said use of speed sensors is becoming mandatory to aid with control of these systems.
The speed signals produced by these sensors can be used by autonomous driving systems to determine if the vehicle is moving as desired, helping to ensure safe operation.
READ MORE - Sensors and Software in Motion Control: Key Benefits to Consider
According to Strasser, two-channel sensors are the most commonly used type in electric drives. These sensors provide both rotational speed and direction measurements to provide a better picture of motor, and overall system, performance.
He noted that the more information you get from a sensor, the more you can ensure optimal motor performance.
The below video from Rheintacho demonstrates the information which can be gained from its various speed sensors in an electric motor application.
For its speed sensors, Rheintacho uses Hall effect technology. Strasser said the company chose this sensor technology because it provides a sustainable and secure signal. It is also a more durable technology, enabling a sensor to withstand harsh operating conditions. This is beneficial because in an electric drive system, the speed sensor is located within the electric motor. A robust design is necessary to ensure the sensor performs as needed in this difficult operating environment.
Sexauer said that when using magnetic-based sensors like Hall effect, it is important to take into account the magnetic fields within the electric motor which could disrupt signals produced by the sensor. Temperature can also be a factor which influences the magnetic field.
It can be difficult to calculate and model how a sensor and electric motor will interact with one another and so sometimes it may be necessary to conduct real-world testing to ensure the sensor and motor will work well together. He said sometimes a customer will conduct this type of testing on its own and other times it will collaborate with Rheintacho to do so.
In either scenario, Rheintacho will do its part to ensure the speed sensors it provides perform as desired for customers. Strasser explained that the sensor is not a component operating on its own but part of an overall system, requiring all components “to be adjusted well to each other so you get the best performance out of them.”
Each manufacturer prefers to have its own unique solution to which the speed sensor must be appropriately tuned, making any degree of coordination between Rheintacho and its customer an important part of the process. Because the company has its own testing facility, he said customers can send their design information to Rheintacho who will then determine the best method for integrating the sensor to ensure no signal failures.
Going forward, Strasser sees the creation of customized solutions becoming more commonplace. This trend has already begun but will continue to grow to meet ever-evolving customer needs. As such, he does not see the company having many standard products but instead product groups from which customized solutions can then be developed.
He also expects sensors to become more complex in the coming years. This will likely be due to the implementation of new safety regulations which could bring about the need for four-channel sensors capable of also providing position and possibly even acceleration measurements.
Temperature is another measurement which could be included in future speed sensors. Given the effect temperature can have on system performance, this would help further improve monitoring capabilities for customers. And by including all of these measurements into a singular device, it would help to cut down on installation costs for customers – as well as space, which is at a premium in today’s vehicles, especially electric vehicles.
Sexauer noted that today, some customers are integrating two Rheintacho sensors into a single electric motor to get all of the signal measurements they desire. “But customers would be much [happier] if we could offer a technical solution to integrate those into one sensor,” he said.
Both Strasser and Sexauer anticipate further growth for the speed sensor market in the future because of the many benefits they can provide. Sexauer said that when he started with Rheintacho about 20 years ago, there were predictions speed sensors would not be used for electric drives because there are other ways to measure speed and customers would therefore not want to spend the money on a sensor.
However, this has not been the case. In fact, use of speed sensors has only increased over the years and will likely continue to do so as use of electric drives also increases. Continued advancements in sensor technology have helped it remain the measurement solution of choice.
Sexauer said the other measurement method is also not as affordable because of the sophisticated electronics required. And from a safety point of view, he said it is more valuable to detect movement at the actual place of the movement which is possible with a speed sensor.
Aldo Lopez, Business Development Manager for North America at Rheintacho, agreed with his colleagues’ predictions for the future. He believes the many changes taking place in the company’s various customer markets will be beneficial for the sensor industry, particularly the transition to more automated and electrified vehicles.
READ MORE - Construction Equipment Digs Deeper into Electrification
“I think the amount of sensors will increase…to fulfill all of the autonomous [vehicle] requirements,” he said. “All of the safety requirements for autonomous vehicles will demand companies to implement two or three times more signal sensors than they are using currently with conventional vehicles.”
With the many market opportunities and technological advancements anticipated in the next 10 years, Strasser concluded that “it will be a very challenging and interesting decade for us.”
Editor's Note: Members can download a PDF version of this article.
Sara Jensen is executive editor of Power & Motion, directing expanded coverage into the modern fluid power space, as well as mechatronic and smart technologies. She has over 15 years of publishing experience. Prior to Power & Motion she spent 11 years with a trade publication for engineers of heavy-duty equipment, the last 3 of which were as the editor and brand lead. Over the course of her time in the B2B industry, Sara has gained an extensive knowledge of various heavy-duty equipment industries — including construction, agriculture, mining and on-road trucks —along with the systems and market trends which impact them such as fluid power and electronic motion control technologies.
You can follow Sara and Power & Motion via the following social media handles:
X (formerly Twitter): @TechnlgyEditor and @PowerMotionTech
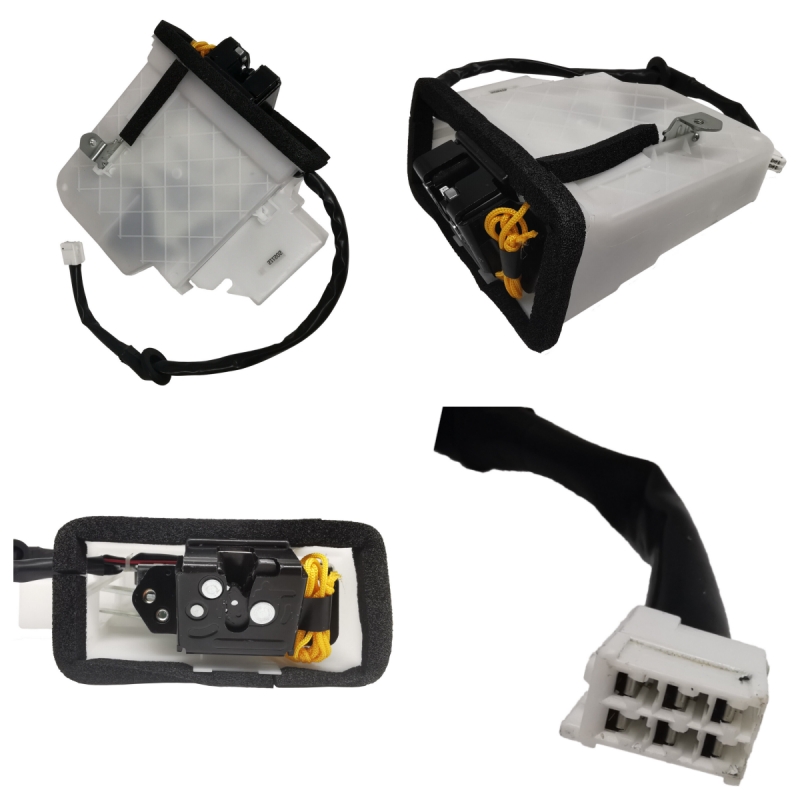
Nissan Accessories LinkedIn: @SaraJensen and @Power&Motion