DDM Systems, an Atlanta-based digital manufacturing company is creating the future of precision metal investment casting technology with the convenience and versatility of advanced ceramic 3D printing. DDM’s Digital Foundry™ technology cuts out 7 of 12 process steps in the state-of-the-art investment casting process for making precision metal parts, enabling the production of advanced metal components ten times faster and at half the cost. Through a combination of proprietary and patented hardware, software and materials technologies, DDM offers a breakthrough solution for demanding customers requiring rapid delivery of the highest precision metal components found anywhere. Third party qualification of our castings assures customers that they meet all required industry standards and are ready for commercial use.
Problem: Traditional Investment Casting Technology Is Outdated Forged Parts
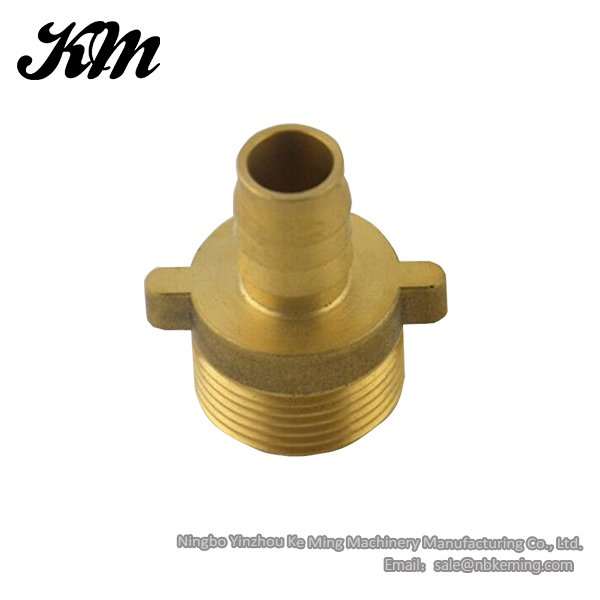
Traditional investment casting or lost-wax casting which is used for making the highest performance metal parts across diverse high-tech industries is an outdated 12-step process that hasn’t changed in decades. It relies on molded wax replicas of parts made using highly expensive tools and dies that take tens of weeks to make. The wax replicas are assembled into a tree then coated with a shell by dipping in a ceramic slurry and coarse sand. The wax is melted out to leave a hollow shell which is baked and poured with molten metal to produce castings. While this results in high quality parts, the overall process is limited by cost and lead time, causing production delays and money lost. Further, only standard part geometries are possible through wax molding, preventing access to the full range of complex parts possible with revolutionary capabilities for advanced applications.
Solution: DDM’s Digital Foundry™ Technology With 3D Printed Ceramic Shells
DDM’s Digital Foundry™ technology eliminates all the up-front investment and lead-time for tooling and replaces the seven most expensive and time-consuming steps in traditional investment casting with just a single 3D printing step. This step prints highly accurate ceramic shells that can be fired and directly poured with metal to produce castings. Through this digital foundry approach, parts are made with the same high quality but 10x faster and at 50% lower cost than traditional investment casting. Complex part geometries for advanced applications previously considered impossible also become possible due to the power of 3D printing that overcomes the limitations of standard geometries with traditional tools and dies. This opens up entirely new possibilities in prototyping and series production especially for high-tech companies in new and emerging markets. DDM Systems helps any industry that uses precision investment castings in their hardware. The company has worked with clients across the aviation industrial, automotive, fluid-flow, power generation, defense and medical industries, among others, providing more value for clients due to its innovative Digital Foundry™ technology.
Yes, I would like to receive the bi-weekly Foundry-Planet newsletter with all latest news, product and material tests and reports. Plus the special newsletters – all can be cancelled anytime and at no cost.
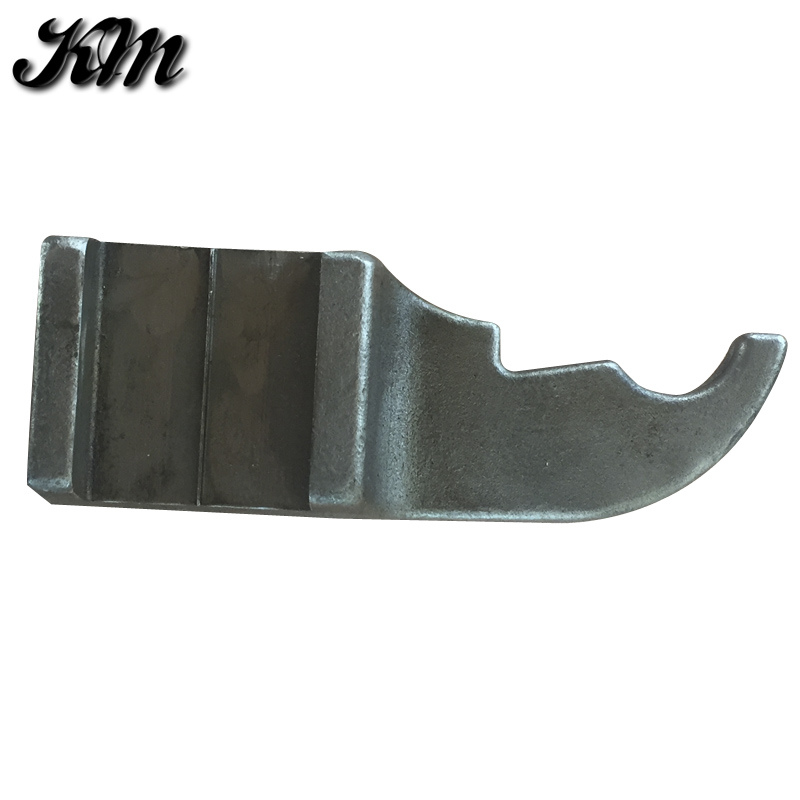
Iron Casting Foundry Check here our privacy policy.