© 2023 Power Automedia. All rights reserved.
We swung by American Autowire’s booth at SEMA and took a look at what was new and fresh off the presses and we weren’t disappointed. Representative Don Buck walked us through their latest wiring kit for a popular old SUV from back in the day. American Autowire’s 1971–80 Scout II Classic Update Kit boasts many features and connectors, making it the most complete system of its type in the industry. Air Suspension Leveling Valve
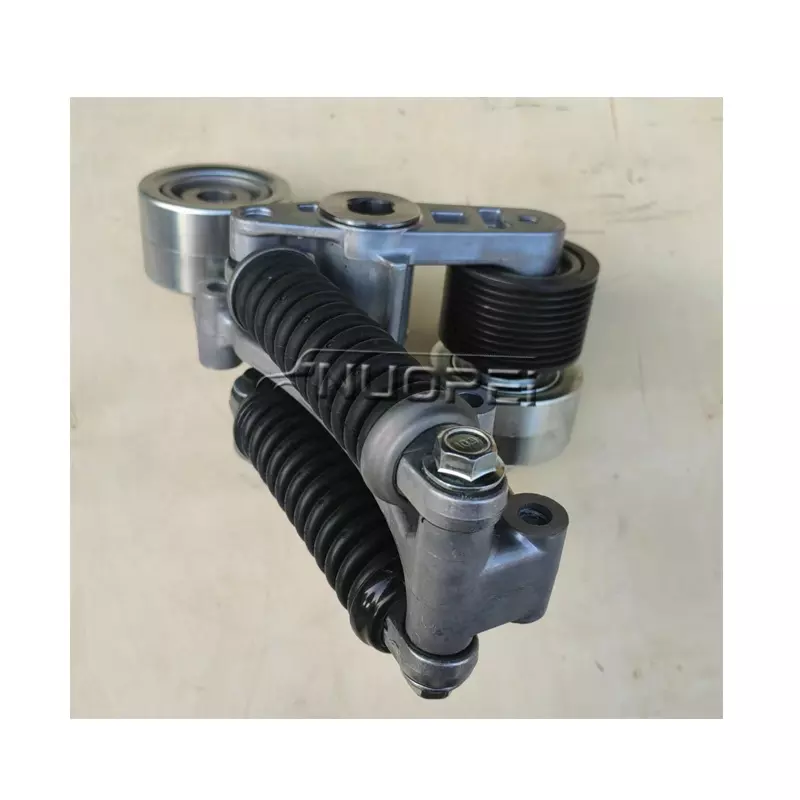
Don broke it down for us, “We debuted our new complete front-to-rear wiring kit. It works with the Traveller model as well as the Scout, and can accommodate the 345 cubic-inch V8, six-cylinders, or restomod applications. It’s compatible with stock or custom gauges and aftermarket heat/AC as well. Additionally, connections for exterior lights, steering column, ignition switch, and headlight switch are included.”
Let’s zoom in for more details.
American Autowire also has kits for the most popular make and models as well. Click here for more details and pricing.
Build your own custom newsletter with the content you love from Off Road Xtreme, directly to your inbox, absolutely FREE!
© 2023 Power Automedia. All rights reserved.
We will safeguard your e-mail and only send content you request.
We'll send you the most exciting Off Road articles, news, truck features, and videos every week.
We promise not to use your email address for anything but exclusive updates from the Power Automedia Network.
We will safeguard your e-mail and only send content you request.
Thank you for your subscription.
We think you might like...
We think you might like...

Oem22988765 Thank you for your subscription.