Established in 1976 with only a saw, a manually operated mill and a lathe, Kosmo Machine Inc. quickly differentiated itself by committing to consistency and customer service. Although Kosmo now provides numerous machining and reconditioning services from its 62,500-sq-ft (5,800-sq-m) facility, it hesitates to call itself a machine shop.
Instead, Chief Operations Officer Heath Stewart and his team of 57 employees refer to the Richmond, Va., shop as a “manufacturing facility.” As such, the employee-owned company supports many industries including defense, aerospace, power generation, shipbuilding and advanced fibers technology. Its capabilities include precision machining, certified welding processes, painting and assembly, in addition to multiple reconditioning processes of “high-value” components. Cnc Pipe Bending Machine

“To remain competitive on a national level requires being a full-service provider of leading-edge manufacturing technology, which is key to our success,” Stewart says. “We have capabilities under one roof that other suppliers do not, allowing streamlined lead times.
“We perform very niche products/parts with high customer service requirements,” he continues. “Our customers’ main goals are to reduce lead times; they depend on us to help them succeed.”
Kosmo collaborates with customers throughout the planning and manufacturing processes. This includes advice and subsequent feedback as they work toward common objectives, Stewart says.
To help Kosmo meet these expectations, CEO Mike Redden points to the company’s longstanding relationship with Mazak Corp., a manufacturer of precision machine tools with U.S. headquarters in Florence, Ky.
“Mazaks are very robust, they last a long time and are highly versatile,” Redden says, noting the machines’ speed, rigidity, precision and ease of use help the company keep pace with production demands. “Besides this, we’ve built strong relationships with Mazak personnel including sales, service and the applications department.”
In fact, Kosmo has worked with some Mazak employees for more than 20 years, which Redden says builds trust and knowledge. “In the rare instance when a machine goes offline, it is never down for long because of the dependability of our relationship with Mazak.”
Kosmo’s production runs typically involve jobs between 10 and 100 parts—and occasionally reoccur—but may vary from one piece to as many as 1,000 or more. For shipbuilding, the facility produces parts for nuclear-class submarines and aircraft carriers.
Kosmo has purchased upwards of 25 Mazak machines, ranging from lathes with live tooling to horizontal and vertical machining centers with three- and four-axis milling, as well as those with full five-axis movement and turning capability. Models include the Mazak HCN-8800 Horizontal Machining Center, HCN-6000 Horizontal Machining Center and VARIAXIS i-600s.
One of the latest additions is a five-axis Mazak VARIAXIS i-700T with an 18,000-rpm milling spindle and turning capability. Kosmo purchased the machine for its versatility, according to the supplier.
“It eliminates the need for multi-machine processing and instead allows the shop to turn and mill in a single application, provide full five-axis motion and complete parts in single setups,” says Daryl Taylor, Mazak distributor of the HEH Group. “They work closely with a first-tier government contractor in the shipbuilding arena, and the VARIAXIS provided machining capabilities that are required to manufacture these parts.”
The VARIAXIS is paired with a Mazak 12-station PALLETECH Automation System and Smooth Tool Management software. This software tracks tool data in an RFID chip in the retention knobs of toolholders, which enables the machinist to take tools in and out of the machine without risking data-entry errors or loss of tool data.
“VARIAXIS allows us to turn and mill in a single application and provide full five-axis motion; they also permit single-setup part production,” Stewart says. “With the PALLETECH system, we can store fixtures and setups on 12 stations and machine incoming customers’ parts based on their demand. That reduces job setup and changeovers to minutes instead of hours. Without our VARIAXIS machines, part production would involve multiple machines and much more labor,” he adds.
Kosmo’s newer Mazak machines are equipped with the company’s MAZATROL SmoothAi control. This enables the company to push machining limits and develop new methods and strategies for metal removal, according to Stewart, who says the software has been a key factor to stay with Mazak.
“We use MAZATROL for the bulk of our programming and even to streamline the 3+2 programming on our five-axis machining centers,” Stewart explains. “G-code is used for our 3D surfacing and full five-axis motion. On top of that, the controls simplify cross-training, so our machinists can now alternate between machines of different ages and varying types because of the MAZATROL universal programming format.”
With Kosmo’s goal of attracting the highest level of customers and the most skilled personnel, Mazak has been at the forefront of its choices of machine tools. The shop purchased its first Mazak QT-15 Turning Center with a T-32 control in the early 1980s and has relied on the brand ever since.
“I have called on Kosmo for 30-plus years, and they have always been committed to Mazak,” Taylor says, noting that the shop never wavered in its dedication—even through struggles with applications or service. “At the end of the day, the partnership between Kosmo and Mazak has allowed Kosmo to make customer parts quickly and accurately, and allowed them to be profitable in doing so,” he adds.
Today, Kosmo runs one shift, mainly because of the skilled labor shortage. “We do have a state and nationally accredited in-house apprentice program for machining, which has been beneficial, while our welding curriculum is sourced at a local community college,” Redden says. “The way we contend with this shortage is to invest in technology, such as the Mazak PALLETECH automation system, and strive for more lights-out production, which is well suited to the machining of large, highly complex shapes with longer cycle times.”
Kosmo’s staff finish machine 3D-printed aerospace components from Inconel 718, Hastalloy and other difficult-to-machine high-temperature alloys. These parts contain complex geometries requiring very close tolerances, ultra-smooth surface finishes and unique fixturing techniques.
“Advancements in 3D additive manufacturing have rewritten the rules for design and engineering, allowing performance-enhanced shapes and functioning internal passages that were impossible to produce until now,” Redden asserts. “These designs often combine multiple parts into just one more efficient component requiring extended machining cycle times.”
He notes a few essential qualities shared by Kosmo and Mazak that have perpetuated success for both companies. The first is maintaining the highest degree of ethics, and the second is to always deliver quality and value on time, every time.
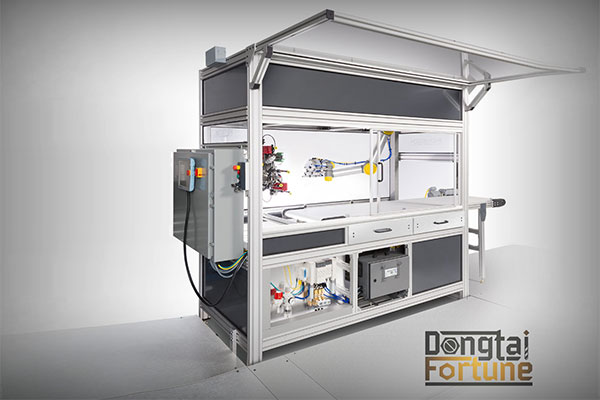
Mini Cnc Milling Machine For more information on Mazak Corp., visit https://www.mazakusa.com or call 859-342-1700. For more information on Kosmo Machine Inc., visit https://kosmomachine.com or call 804-326-6819.