Civica is on a mission to deliver quality generic medicines—including insulin—at low cost. A new isolator-integrated vial filling line and nest filling line allow them to produce many different forms of injectables to pivot based on greatest need.
Invest in premium equipment to deliver affordable drugs. Rotary Can Filler

It may seem counterintuitive. But it’s how nonprofit innovator Civica is approaching its mission to deliver quality generic medicines to patients in need. They are the only pharmaceutical company created for the express purpose of preventing and mitigating drug shortages.
I remember covering Civica’s talk at the PDA Annual Meeting in 2019. Having recently launched, they had identified a set of generic drugs to focus on and were working to contract with manufacturers or sub-contractors to produce drugs in established facilities. Their long-term goal was to produce their own nonprofit drugs. Just five years later (not long in the pharma world), here they are starting engineering and exhibit batches in their own new injectable drug facility in Petersburg, VA.
When they needed to purchase two filling lines for the facility, they turned to groninger, Germany-based provider of filling and closing machines, and Switzerland-based SKAN, known for their isolator technology. The new isolator-integrated vial filling line and nest filling line allow Civica to produce many different forms of injectables to be able to pivot based on greatest market need. They’re even filling a pen product in a nested tub cartridge successfully. groninger integra vial filling line with SKAN isolator.
Jason Winfield, site director of engineering & technical services at Civica, credits the executive leadership team for prioritizing the approach to “do things right the first time.”
While it may be tempting to save money upfront in production, if this leads to rejects due to filling accuracy or quality issues, that ultimately costs more down the road and negatively impacts sustainability. Rejecting substandard product is the responsible thing to do, but if you can eliminate rejects from the outset, you save all the commodities you used in the process.
Selecting lower-cost equipment from lesser-known manufacturers didn’t fit with Civica’s mission to positively impact the supply chain with quality medicines. Plus, with deviations costing thousands and market recalls costing in the millions, they wanted to engineer out nonconforming product ahead of time. “This is where I give thanks to my executive leadership team. There was never a question of quality, compliance, and reliability of products. They know that if you do it right the first time, it's more financially sound in the long run because you avoid rejected batches,” says Winfield. Check out the project video here.
Civica purchased the integra, a bulk vial filling line that processes vials up to 400 units/min with 100% In-Process-Control (IPC). A special priming mode eliminates product losses during start-up, while the IPC and run empty mode prevent losses during production and at the end of a batch, respectively. For cartridges, the In Process Control (IPC) helps prevent losses during production.
Civica currently can process over 10 different vial sizes on the line, from 2R (2 mL) through a 50 mL molded glass vial, including multiple configurations for 10 mL vials. Matt Clifton, business development manager at groninger, explains that the integra utilizes a servo-driven walking beam, and there are no format parts needed for the 2R through 30R vial range for quick changeover. “At our stoppering station, we use a vibratory bowl that does not need to be changed for any stoppers,” he adds.
You may have heard of the high five test—ideally, one isolator glove can touch the outstretched glove on the other side. For the integra, groninger worked together with SKAN to give the machine a slim design, requiring gloves on only one side of the isolator. Its compact design allows for fast decontamination and short cycle times, boosting productivity.
The groninger DFVN 2005 is a ready-to-use (RTU) nested filler with an integrated isolator that can fill and close vials, syringes, and cartridges. “We still have plans to fill prefilled syringes on that line,” explains Winfield. “But because of the nested configuration, we were able to quickly pivot to cartridges for our insulin program. Having the nested tub capability was an easy transition to the 3-mL cartridge from the prefilled syringe formats. We fill both a 1-mL stake needle as well as a 1-mL short luer lock prefilled syringe.” groninger nest filling line with SKAN isolator.
Civica has successfully filled a pen product in a nested tub cartridge, with both water and their insulin molecule. “That to me is really exciting because we were all but told it can't be done and we did it. I'm really pleased that the consistency of the fill leads to the consistency of the plunger placement, which leads to consistent matchup at the pen assembly, and it's really exciting to do something like that to serve the patients.”
They purchase a pre-sterilized cartridge in a tub complete with aluminum overseal and combi cap. “You're filling it from the back end. Then you have to either vent-tube or vacuum-assist place that stopper. So stopper placement is going to be a variability of the accuracy of your fill,” Winfield says. “If your fill is not accurate, then your plunger placement is going to be moving on the backside.”
Accurate plunger placement is key to preventing rejects, and pens are a costly part of the assembly. In order to get better plunger placement, Civica could have switched to mechanical placement, but that wouldn’t offer them the same flexibility in what they could fill. “We've gotten really good feedback from our pen assembly manufacturers on that cartridge filled pen almost to unbelief. They can't believe vacuum-assist stoppering is performing that well. So, to hear our pen supplier compliment that process and those cartridges that have been filled on our line—it really made the engineering team and the MSAT team feel good here.”
A standalone Material Transfer Isolator from SKAN with an integrated skanfog decontamination system performs a fast, automated decontamination cycle to transfer material to either line. SKAN also provided glove testing equipment.
An additional technology that Civica utilizes to quantify a container’s experience on the production line is a drone from SmartSkin Technologies. The intention of the drones is to eliminate damage and improve yield by providing insight into the forces experienced on the lines that may damage glass. The SmartSkin drones can be utilized during commissioning and qualification or during a product turnover to ensure proper setup prior to sterile containers being introduced to the line.
Civica opted to purchase groninger’s overhead SCADA system. “It sends batch recipe data down to each one of the individual machines and collects the batch report that we can use for disposition, which makes for less paperwork in my cleanroom,” says Winfield. “What's great about that is if you have a fill line like our vial line that has a washer, a tunnel, a filler, a capper, and an accumulation station, I don't have to rely on an operator to make the right entry in each one of those HMIs because the SCADA is doing it from the top down. There's a lot of great details with the integration between the units.”
The lines offer Civica the flexibility it needs to produce many different products and formats in the future to address drug shortages and lower the cost of essential medicines. Additionally, both lines are designed to minimize product loss, ensuring optimal use of valuable pharmaceutical ingredients.Cartridge filling on the groninger line.
This efficiency is vital for Civica, which is preparing for its first rollouts of biosimilar insulin products on the equipment. “The lines are open to the widest possible range of products and as a standard include nitrogen capability, vacuum filling, and vacuum stoppering. Civica is targeting an under-utilized market where they need the drug products so quickly, so the intent behind both of these machines is to be able to produce whatever is needed,” says Clifton.
Both groninger and SKAN offer virtual capabilities, and the degree to which they’re used depends on a manufacturer’s openness and comfort level. “It’s certainly beneficial for emergency scenarios—such as if the SCADA is not connecting with one of the PLCs—to allow techs from either company to remote in and help as Civica continues to learn its equipment,” says Winfield. “Most of the time we find out that it was a simple IP address issue. We're learning in our automation space. But we get great support, whether it's remote or onsite, from both companies.”
One of Winfield’s primary objectives was to avoid using many vendors across filling lines and isolators. “Civica was a young company as we started the design, and we had a lot of executives who had experience with groninger and SKAN. They are industry leaders from a technology and reliability standpoint in our most important application, which is sterile filling,” he adds. “Equipment prep upstream, and secondary packaging and visual inspection downstream are also critical. But primary container closure is where my sterility assurance rests, and it is the most important thing we do.”
Notably, groninger and SKAN, who have a 20-plus year relationship, partnered to develop the integrated technology years before a customer was even involved.
Typically, a manufacturer goes through a lengthy user requirements specification and subsequent design process, choosing the best-in-class filler and isolator which will be integrated as a last step. As Clifton says, the duo developed and integrated the system based on historical user requirements they’d seenm then coupled that knowhow with the latest technologies.
Marc Suter, head of sales, North America at SKAN, says, “We’ve predefined certain interfaces, how we work together, and we have a contract in place that details who is responsible for what. That really helps going into the individual project.”
Because the line is not completely custom, Civica benefits from the companies’ experience throughout multiple builds. Suter says prototyping is done beforehand, and they even have predefined slots for pre-fabrication, so when they begin a project, they aren’t starting from scratch.
Initial design began in 2020, with groundbreaking in 2021, so the team had to overcome pandemic-related challenges. Midway through 2020, they started ordering the longest lead equipment, beginning with the filling line and the isolators, which coincided with COVID shutdowns.
Normally face-to-face ergonomic studies would be conducted in person, so they had to get creative and learn quickly. “We implemented two different ways of doing this. We implemented virtual reality for the vial line. For the second line, we built a one-to-one model,” says Suter. “groninger and SKAN met at our premises because we were able to travel across the border from Germany to Switzerland. We had our colleagues from Civica patched in remotely. We put different cameras around the model, and went around with tablets showing details—we had to be creative to overcome these challenges and keep the momentum of the project.”
Winfield notes that commodities such as single use bags and syringes were hard to procure during these startup phases. “But within two years, all four pieces of equipment—both filling lines and both isolators—were installed to the site and had FATs performed.” The stoppering station uses a vibratory bowl that does not need to be changed for stoppers.
Richmond is a young, but growing pharma hub. One of the challenges Winfield knew they were going to encounter was with hiring and training personnel. “We knew that we needed to be a center of excellence with training our staff,” he says.
Now that they’ve performed engineering batches with the actual molecule on the both the nested and vial lines, they’re in the process of hiring and developing more staff. He appreciates groninger’s multilevel training opportunities with onsite trainers. “Our training program is ongoing. But people love knowing the impact we're having to patients and the opportunities we have to serve. Nearly every day they're telling you something different they learned to do, or they'll bring an idea of how we could potentially make an improvement. That engagement is what builds our culture in Petersburg that we're excited about.”
The equipment suppliers also felt the passion for improving access to life-saving medication on U.S. soil. This marks the first time groninger and SKAN have worked together to benefit a nonprofit in the U.S. “There was a lot of buy-in to the patient-centric mission—that was the unique flavor overall for this project, the direct concern for patients,” says Clifton. “I think that Civica felt like they owed it to the patient, in addition to the automation portion, to deliver efficiency. I think they wanted to present a different model. In addition to the model, there were no compromises, they didn’t look to minimize scope or quality.”
Suter adds, “What's struck me—even without starting to produce insulin yet—is they’ve already made an impact on the industry. You’ve seen competitors dropping their prices already because of the example they're setting. I’m just waiting for the moment when our lines are up and running and filling the affordable insulin. I'm really looking forward to that.”
Winfield says, “The SKAN isolator for me is the number one in the industry, and groninger’s capabilities with their syringes, both from filling accuracy and plunger placement, is I think next to none on that prefilled syringe line.”
“With respect to space, we designed the space the right way. It's like no other facility in the world. People have room to move, to move their pallets around. We have a third bay where we’re putting a third filling line in dedicated for cartridges in the insulin pen,” says Winfield. “The executive team said, ‘That's it. We're not going to cram anything else into this facility because if we do, we risk quality and compliance, ease of operations, ergonomics, and safety. We'll go somewhere else.’ I'm excited to hear about that.”
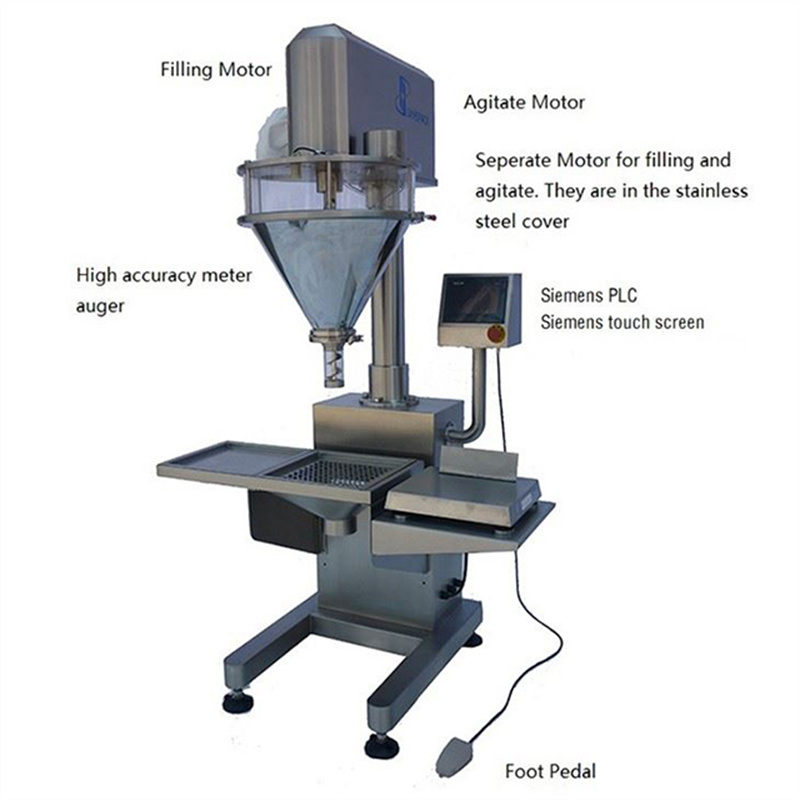
Carbonated Can Filling Machine He feels that the vial filler sits in a small footprint relative to what else is out there, but that small footprint didn’t take priority. “It was really the ease of operations, the reliability of the machines, and also the U.S. presence that we have from both companies to support any mechanical challenges that just happen in operations.”