If you want to become a faster runner, you’ll probably end up doing a lot of speedwork on a track. Or if you live in a hilly place, you might wish you had a nice flat track to run on. But how do you find one that’s open to the public? Turns out it’s easier than you might think. Many public high school tracks are available for the community to use.
I run on a local school track, and the way I found it was pretty straightforward. I phoned up the nearest high school, and asked whether they had a track that was open to the public. They said yes, so long as I come outside school hours; but they also suggested a different school in the district whose track has fewer evening events scheduled. That’s the track I now run on most often. Tracks For Skid Steer
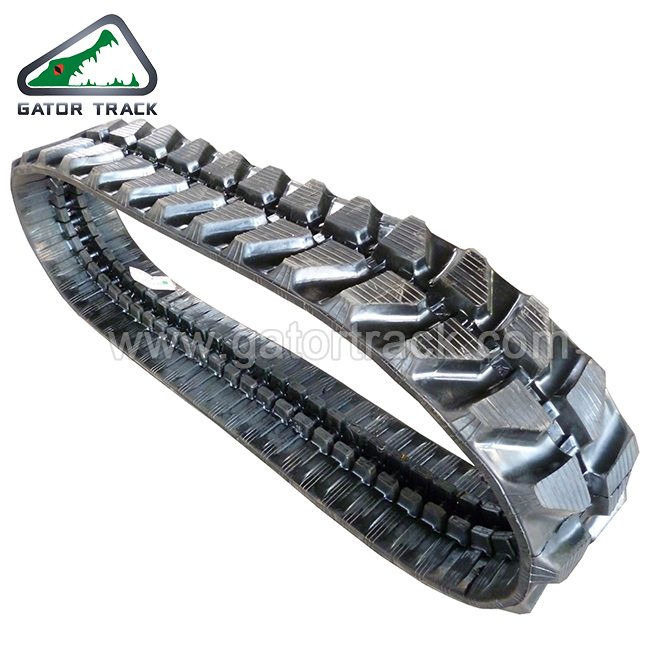
I recently found another track near me, just by looking for oval shapes on the Strava global heatmap (it highlights popular running routes). The satellite view on Google Maps is another great way to look for nearby tracks. Most regulation-size outdoor running tracks surround a football or soccer field, and they’ll usually be at a school or sometimes a park or community center. They will be an oblong shape, curved around the ends, often with a red rubber surface and white lane lines visible when you zoom in.
Another great resource for finding tracks is Run Track Run , which lists tracks and running routes across the U.S. Some of the tracks have information listed, such as the type of surface, whether it’s open to the public, and whether it’s free to use.
First, check for any posted rules or hours. School tracks are often closed to the public during school hours, but that usually means evenings, weekends, and holiday breaks are fair game. Don’t expect that every school’s track will always be open, though. Private schools might not open theirs to the public, and public schools may still set a schedule or close the track for events. If the track is part of a park, gym, or community center, check their website or call to confirm who can use the track and when.
Once you’re there, the most important rule is to stay in your lane (if there are marked lanes). Think of them like lanes on a highway: You can pass somebody if you give them enough room, and you should always look behind you before you change lanes. Don’t block a lane by stopping in the middle; find a spot off the track if you want to sit down to stretch.
The faster people will run in the innermost lane, which means if you’re walking or warming up, you should stay in the outer lanes. Pay attention to the direction, too; usually everyone runs counter-clockwise.
The track is there for anything you’d like to do, so there isn’t a specific procedure. But as a general rule, you’ll break down the work you’d like to do into quarter-mile chunks. (The innermost lane of a track is 400 meters per lap, almost exactly a quarter of a mile.)
It is totally fine to jog continuously the whole time you’re at the track, but more often people will use the track for interval work. You run fast for a short distance, then either walk or stand around while you catch your breath. Then do another fast interval, and repeat the process until you’re ready to go home.
Here’s a beginner-friendly workout you can do your first time on a track:
Runners would call the above workout “8 x 100” since you are doing eight 100-meter runs. (The walking in between is considered the recovery.) Here are common distances for intervals:
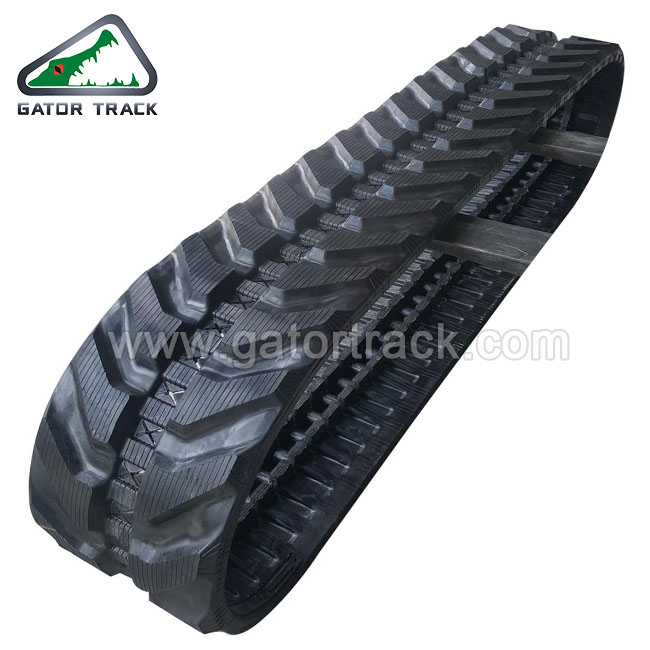
Tracks For Skid Steer Loaders In between the running portions of your workout, you can rest or walk for about the same amount of time it took you to run. For example, if you run a lap (400 meters) in about two minutes, you’d rest another two minutes before going again.