In close cooperation with One Process Machining (OPM) laboratory in Japan, CoreTech Systems has developed a useful simulation tool: Cooling Channel Designer (CCD) for conformal cooling users.
In plastic injection molding, the cooling segment can take up as much as two-thirds of the cycle time, thereby reducing production efficiency. CoreTech Systems (Farmington Hills, MI), developer of Moldex3D simulator, noted that “traditionally speaking, most of the cooling channels are designed and built by experienced engineers” and mold builders. However, since the design of many plastic products involves more complex geometry, traditional cooling channels can no longer provide the best cooling efficiency when it comes to molding these parts. The result is that conformal cooling technology has become more in demand. With its significant benefits of providing effective cooling solutions to the molding of more complex parts, conformal cooling has become more widely used. Headphone Holder Gaming
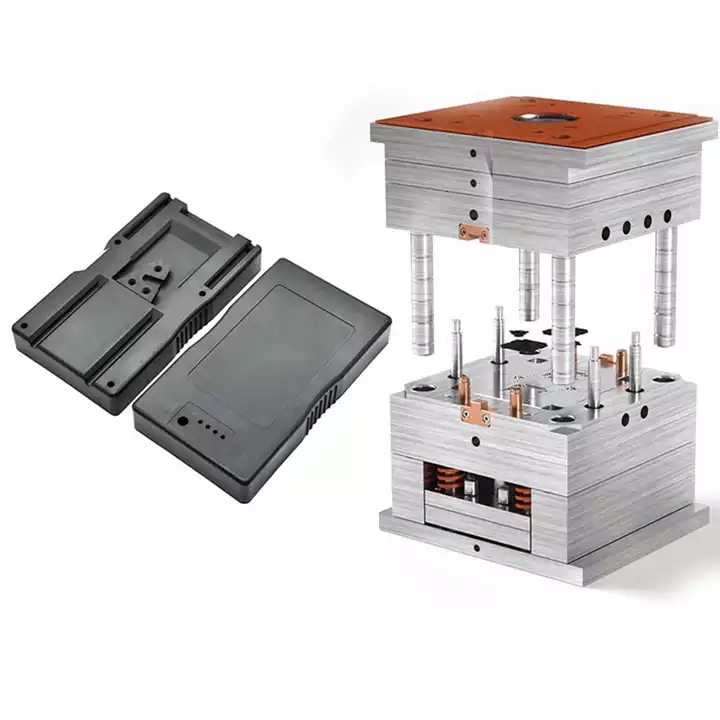
In close cooperation with One Process Machining (OPM) laboratory in Japan, Moldex3D has developed a useful simulation tool: Cooling Channel Designer (CCD) for conformal cooling users. With the Moldex3D CCD module, users can build conformal cooling channels according to the contour of a product in a fast and intuitive way in Moldex3D Designer. Moldex3D CCD provides flexible features that allow users to make cooling layout changes easily; mold designers can change the cooling design to make cooling channels closer to the molded products in the cavity. Thus, the temperature can be more evenly distributed, eliminating cold and hot spots inside the mold, which means product defects caused by poor temperature control, such as residual stress, warpage, voids, and sink marks, can be greatly decreased.
One of the unique features in CCD is the slicing function, noted CoreTech. With this function, users can slice up the imported part into several sections. Based on each intersecting surface (cross section) of the part, users are able to design a better conformal cooling system. Moldex3D Cooling Analysis can predict the required cooling time, and helps users evaluate how cooling layout design will affect overall cooling time. It also provides visibility into temperature variation inside the mold cavity. Through true 3D cooling analysis technology, Moldex3D can further predict coolant flow rate, pressure loss and vortex/dead water areas.
The integration between Moldex3D simulation and Cooling Channel Designer can enhance the performance of conformal cooling design to optimize heat dissipation and achieve uniform cooling. This will help improve product quality and help create advantages through the reduction of cycle times and costs.
CoreTech Systems is exhibiting at NPE2015 at booth W-8645.
Startup Develops Biodegradable Shotgun Wads
There’s a Simple New Way to Recycle Polystyrene
Bedford Reinforced Plastics Founder Melvin Stahl Passes at Age 88
Gerresheimer on Track to Complete $180M Medical Manufacturing Expansion in Georgia
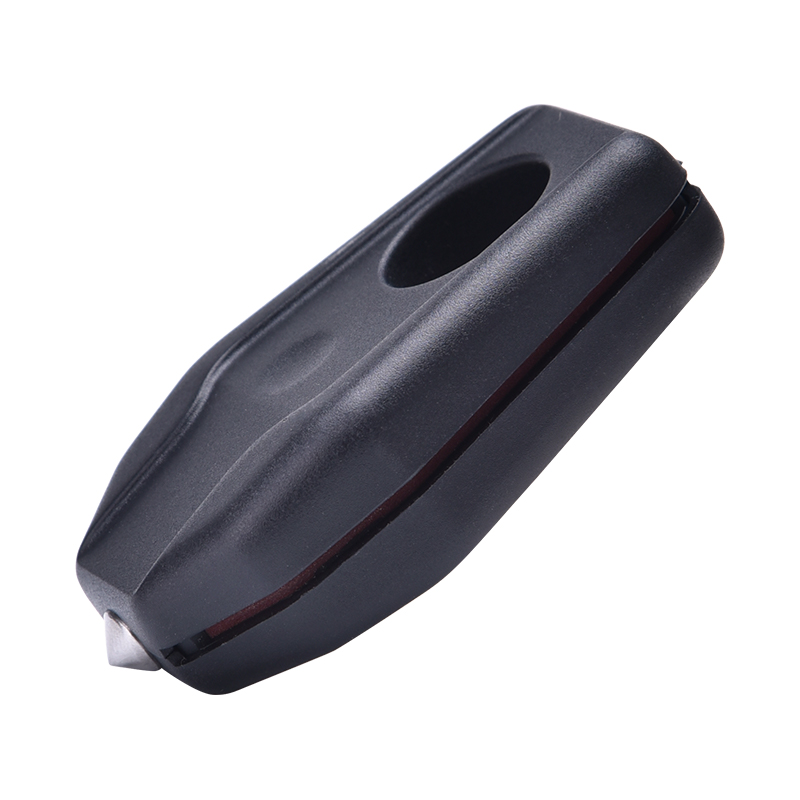
Plastic Injection Molding Parts Copyright © 2024 All rights reserved. Informa Markets, a trading division of Informa PLC.