Existing facility at Dayton International Airport will enable 500 eVTOLs per year, serving as Joby’s initial manufacturing footprint in the region.
With the involvement of two schools from the Institut Mines-Télécom, the 4-year project aims to improve the intrinsic properties of a composite material based on Elium via four concrete demonstrators. Alco Panel Sheet
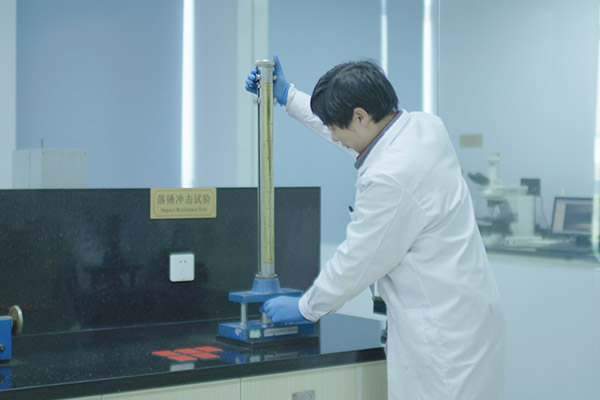
Unveiling coincided with the opening of the new CityAirbus test center in Donauwörth, Germany, ahead of the aircraft’s maiden flight later this year.
Fraunhofer IPT, Taniq and Pixargus have proven the success of a measuring head capable of optimizing the reliability, security and efficiency of FRP pressure vessel manufacturing.
Production organization approval (POA) extension gives Volocopter the ability to design and produce the eVTOL aircraft in Bruchsal once it receives type certification.
Pilot controls and wing components will be covered by Crouzet and Aciturri, respectively, as first prototype production begins.
Strategic MOU initially introduces SikaBiresin CIM 120 and SikaBiresin CIM 80 to serve crucial composites market needs for 3D printing tooling, prototyping and more.
Through this strategic collaboration, BEAD’s additive and subtractive capabilities for large-scale AM composite tooling production are made more accessible.
Plyable continues to rid composites engineers of workflow bottlenecks through an end-to-end automated system — from mold design to quotation to manufacturing fulfillment.
JEC World 2024: The RAMPF Group is bringing together three of its divisions — RAMPF Composite Solutions, RAMPF Tooling Solutions, and RAMPF Group Inc. — delivering a variety of materials and services to the composites industry.
Computed tomography (CT) provides highly accurate 3D analysis of internal microstructure, performance simulation of carbon fiber/PEEK satellite strut.
Kineco Kaman Composites India uses a bespoke Fill Accubot ultrasonic testing system to boost inspection efficiency and productivity.
HyRECM technology effectively stabilizes carbon fiber’s electrical and antenna properties, enabling development of next-gen electronics, such as the Snapdragon G3x Gen 2.
The thermoplastic composites event, taking place Oct. 9-10 in Bremen, Germany, is seeking oral and poster contributions before March 31.
Thermoplastics are evolving quickly into larger structures and clearly will have a significant role to play in the next commercial aircraft program — whenever that’s announced. This edition of “From the CW Archives” looks back on a thermoplastics pioneer.
With the involvement of two schools from the Institut Mines-Télécom, the 4-year project aims to improve the intrinsic properties of a composite material based on Elium via four concrete demonstrators.
Large carbon fiber and honeycomb core component, known as the barrel timing layer (BLT) tracker support tube, was delivered to Purdue as part of an upgrade to CERN’s general-purpose proton-proton collision detector for space research.
Project optimized design and production of UD composite tapes reinforced with a PEKK matrix, using a continuous in-situ welding (ISW) assembly system.
Startup company selected, including two special recognition awards, highlight FGF applications for children’s seats, FGF extrusion and LFAM for cores and mandrels for composite parts manufacture.
Evolution of the double vacuum debulk (DVD) process over the years continues to advance its “near autoclave quality” for low-void, highly compacted repair patches.
Newly designed digital twin by IMDEA and Technical University of Madrid researchers enables manufacturers to see inside composite materials as they are being produced, facilitating early detection of faults.
Industry 4.0 facility is integrating an additive manufacturing approach to its holistic processes to optimize composite component production rates, quality and cost.
With the involvement of two schools from the Institut Mines-Télécom, the 4-year project aims to improve the intrinsic properties of a composite material based on Elium via four concrete demonstrators.
Project optimized design and production of UD composite tapes reinforced with a PEKK matrix, using a continuous in-situ welding (ISW) assembly system.
Increasingly, prototype and production-ready smart devices featuring thermoplastic composite cases and other components provide lightweight, optimized sustainable alternatives to metal.
CW explores key composite developments that have shaped how we see and think about the industry today.
Knowing the fundamentals for reading drawings — including master ply tables, ply definition diagrams and more — lays a foundation for proper composite design evaluation.
As battery electric and fuel cell electric vehicles continue to supplant internal combustion engine vehicles, composite materials are quickly finding adoption to offset a variety of challenges, particularly for battery enclosure and fuel cell development.
Performing regular maintenance of the layup tool for successful sealing and release is required to reduce the risk of part adherence.
The composite pressure vessel market is fast-growing and now dominated by demand for hydrogen storage.
When developing new products and formulations, there are a large number of additive choices to improve a single property you are aiming for: tougheners, plasticizers, flame retardants, the list goes on. One promising additive is graphene and its derivatives, but most organizations don’t know where to begin, so development walls are hit early in the process and therefore projects can be abandoned before success. But your chances of success are drastically increased when you partner with industry experts that know what forms of graphene will meet your needs. In this webinar Mito Materials will discuss how to successfully source, formulate and deploy any graphene material in the world — and do it to your specs and timeline.
Semi-empirical techniques such as kinetic modeling play a pivotal role in setting up such systems for optimizing production without compromising quality or escalating cost. This webinar is aimed to elevate your understanding of kinetic models to unlock their full potential, empowering you to make informed decisions and extract valuable insights for your polymer processing and applications. With a history of over 50 years, kinetic models are a powerful tool for comprehending and predicting material behavior. Join our expert scientists as they explain the process of creating, interpreting and applying these models, from the lab to the production floor. You'll gain insight into how kinetic models are used in the composite production process, as well as their limitations and why relying solely on kinetic models may not be sufficient to gain the process control now required. This first masterclass gives the foundation for part two, where we look beyond kinetics and how to evaluate alternatives that challenge the status quo and enable innovative pathways to boost your production efficiency and improve sustainability. Agenda: Decoding kinetic models: the core principles of kinetic models and how they wield immense power in optimizing your manufacturing processes Application insights: strategic applications of kinetic models within polymer processing and unlocking new avenues for efficiency and performance enhancement in production Navigating limitations: insights into the derivation process of kinetic models and how to navigate inherent limitations with confidence and clarity
With advancements in raw materials technology and processing, more sustainable and economical solutions for composite tooling are increasingly available. This webinar will discuss the potential for epoxy tooling prepregs to provide additional benefits and cost savings when producing composite tools for the aerospace and automotive markets. Agenda: Principles of ply reduction: best practices Key benefits of faster lamination Proving the case What's next for the future
The burgeoning advanced air mobility (AAM) market promises to introduce a new mode of transport for urban and intercity travelers — particularly those who wish to bypass the traffic congestion endemic to the world’s largest cities. The electric vertical take-off and landing (eVTOL) aircraft serving this market, because they depend on battery-powered propulsion, also depend on high-strength, high-performance composite structures produced at volumes heretofore unseen in the aerospace composites industry. This CW Tech Days will feature subject matter experts exploring the materials, tooling and manufacturing challenges of ramping up composites fabrication operations to efficiently meet the demands of a challenging and promising new marketplace.
Manufacturers often struggle with production anomalies that can be traced back to material deviations. These can cause fluctuations in material flow, cooling, and cure according to environmental influences and/or batch-to-batch variations. Today’s competitive environment demands cost-efficient, error-free production using automated production and stable processes. As industries advance new bio-based, faster reacting and increased recycled content materials and faster processes, how can manufacturers quickly establish and maintain quality control? In-mold dielectric sensors paired with data analytics technology enable manufacturers to: Determine glass transition temperature in real time Monitor material deviations such as resin mix ratio, aging, and batch-to-batch variations throughout the process Predict the influence of deviations or material defects during the process See the progression of curing and demold the part when the desired degree of cure, Tg or crystallinity is achieved Document resin mix ratios using snap-cure resins for qualification and certification of RTM parts Successful case histories with real parts illustrate how sensXPERT sensors, machine learning, and material models monitor, predict, and optimize production to compensate for deviations. This Digital Mold technology has enabled manufacturers to reduce scrap by up to 50% and generated energy savings of up to 23%. Agenda: Dealing with the challenge of material deviations and production anomalies How dielectric sensors work with different composite resins, fibers and processes What is required for installation Case histories of in-mold dielectric sensors and data analytics used to monitor resin mixing ratios and predict potential material deviations How this Digital Mold technology has enabled manufacturers to optimize production, and improve quality and reliability
SolvaLite is a family of new fast cure epoxy systems that — combined with Solvay's proprietary Double Diaphragm Forming technology — allows short cycle times and reproducibility. Agenda: Application Development Center and capabilities Solutions for high-rate manufacturing for automotive Application examples: battery enclosures and body panels
ACMA's Thermoplastic Composites Conference (TCC) is an insightful and collaborative event that focuses on high-performance thermoplastic composites innovations, applications, and technology. This conference is dedicated to sharing knowledge and fostering education by exploring the advancements and opportunities that exist today and those expected to shape the future. Attendees can expect to benefit from the return of ACMA's highly-regarded composites education program, featuring more than 20 dynamic sessions led by industry experts. The conference will bring together over 200 industry leaders and professionals, providing an excellent networking opportunity for attendees to connect with like-minded individuals and establish valuable professional relationships. Join your peers on March 26 – 28, 2024 in San Diego, CA!
16th Exhibition "Composite-Expo" is a unique exhibition event in Russia and is a platform for development and introduction of composite technologies and materials in different branches of industry. Many Russian and foreign companies participate in the event such as Technologiya ONPP, RT-Khimkompozit, Stupino Glass Reinforced Plastics Plant, Akzo Nobel N.V., Evonik, OCV Steklovolokno (OCV Reinforcements) are already exhibitors of the event.
Space Symposium, held at The Broadmoor and Cheyenne Mountain Resort in Colorado Springs, Colorado, USA, has brought together space leaders from around the world to discuss, address, and plan for the future of space since the inaugural event in 1984. Attendees at that original event numbered 250 space enthusiasts. At the 38th Space Symposium (April 17-20, 2023), over 10,000 people from more than 40 countries participated in the event. Space Symposium has become widely known as the premier U.S. space policy and program forum and as the must-attend event for information and interaction among all sectors of space. Called the National Space Symposium for the first 29 years, the event was renamed in 2014 to Space Symposium to reflect the event’s truly global profile.
Over 12,000 ASTM standards operate globally. Defined and set by us, they improve the lives of millions every day. Combined with our innovative business services, they enhance performance and help everyone have confidence in the things they buy and use.
WCX World Congress Experience™ provides an unmatched opportunity to see all the moving parts in today’s mobility industry — and the groundbreaking innovations that are shaping the next phase. Powered by SAE International®, the global leader in connecting and educating engineers, this event serves as the only place for the latest technology, consumer metrics, regulatory standards and technical sessions covering the entire vehicle, from hardware to software and beyond. Join your community at North America’s largest technical mobility event, and be part of the collaborative problem-solving that drives the future of your industry.
Thousands of people visit our Supplier Guide every day to source equipment and materials. Get in front of them with a free company profile.
Jetcam’s latest white paper explores the critical aspects of nesting in composites manufacturing, and strategies to balance material efficiency and kitting speed.
Arris presents mechanical testing results of an Arris-designed natural fiber thermoplastic composite in comparison to similarly produced glass and carbon fiber-based materials.
Cevotec, a tank manufacturer, Roth Composite Machinery and Cikoni, have undertaken a comprehensive project to explore and demonstrate the impact of dome reinforcements using FPP technology for composite tanks.
Initial demonstration in furniture shows properties two to nine times higher than plywood, OOA molding for uniquely shaped components.
The composite tubes white paper explores some of the considerations for specifying composite tubes, such as mechanical properties, maintenance requirements and more.
Foundational research discusses the current carbon fiber recycling landscape in Utah, and evaluates potential strategies and policies that could enhance this sustainable practice in the region.
Thermoplastics are evolving quickly into larger structures and clearly will have a significant role to play in the next commercial aircraft program — whenever that’s announced. This edition of “From the CW Archives” looks back on a thermoplastics pioneer.
The GBI: Composites Fabricating contracted in February to the same degree as January, maintaining its position in a contraction zone.
3D printable material will meet ESD, flammability and other requirements to allow for flexible manufacturing of ducts, without tooling needed today.
With the 2024 Summer Olympics in Paris, this year’s JEC World is bound to be abuzz with talk of this year’s event — from the use of composites in sporting equipment to the roles they play in AAM.
CW Top Shops honoree Cobra International reflects on its growth over 45+ years, as well as current work expanding its automotive and UAV capabilities, increasing energy efficiency and new SMC production lines.
Hufschmied moves beyond optimized milling and drilling tools to develop SonicShark inline quality control system and Cutting Edge World cloud platform for optimized tool use and processes.
CW parent company names Julia Hider correspondent for robots and autonomy and CW’s Hannah Mason correspondent for sustainability in manufacturing. Each role will cover a broader topic scope across industry.
New melt spinning pilot plant offers a well-equipped environment for the development and application of research into new spinning processes, fiber functionalization and sustainable fibers.
Wingtips and morphing winglets integrated into a C-27J flying test bed, and a full-scale composite fuselage, are undergoing testing for Clean Sky 2 programs.
JEC World 2024: EuCIA is offering demonstrators of its Eco Impact Calculator LCA tool, and holding discussions about its initiatives in composite materials circularity, including a recent position paper and the EU-funded REFRESH project.
Completed in December 2023, the pilot production line at Mitsui Chemicals Nagoya Works began trials in January and will supply carbon fiber samples within fiscal 2024.
During the one-day virtual event on April 17 from 11 a.m. to 3:30 p.m. ET, seven industry experts will provide insight into hot topics like waste reduction, energy efficiency, bio-materials and recycling.
Explore the cutting-edge composites industry, as experts delve into the materials, tooling, and manufacturing hurdles of meeting the demands of the promising advanced air mobility (AAM) market. Join us at CW Tech Days to unlock the future of efficient composites fabrication operations.
During CW Tech Days: Thermoplastics for Large Structures, experts explored the materials and processing technologies that are enabling the transition to large-part manufacturing.
In the Automated Composites Knowledge Center, CGTech brings you vital information about all things automated composites.
CompositesWorld’s CW Tech Days: Infrastructure event offers a series of expert presentations on composite materials, processes and applications that should and will be considered for use in the infrastructure and construction markets.
The composites industry is increasingly recognizing the imperative of sustainability in its operations. As demand for lightweight and durable materials rises across various sectors, such as automotive, aerospace, and construction, there is a growing awareness of the environmental impact associated with traditional composite manufacturing processes.
CW’s editors are tracking the latest trends and developments in tooling, from the basics to new developments. This collection, presented by Composites One, features four recent CW stories that detail a range of tooling technologies, processes and materials.
This CW Tech Days event will explore the technologies, materials, and strategies that can help composites manufacturers become more sustainable.
Closed mold processes offer many advantages over open molding. This knowledge center details the basics of closed mold methods and the products and tools essential to producing a part correctly.
CompositesWorld’s CW Tech Days: Infrastructure event offers a series of expert presentations on composite materials, processes and applications that should and will be considered for use in the infrastructure and construction markets.
Explore the cutting-edge composites industry, as experts delve into the materials, tooling, and manufacturing hurdles of meeting the demands of the promising advanced air mobility (AAM) market. Join us at CW Tech Days to unlock the future of efficient composites fabrication operations.
Thermoplastics for Large Structures, experts explored the materials and processing technologies that are enabling the transition to large-part manufacturing.
Explore the technologies, materials, and strategies that can help composites manufacturers become more sustainable.
A report on the demand for hydrogen as an energy source and the role composites might play in the transport and storage of hydrogen.
This collection features detail the current state of the industry and recent success stories across aerospace, automotive and rail applications.
This collection details the basics, challenges, and future of thermoplastic composites technology, with particular emphasis on their use for commercial aerospace primary structures.
This collection features recent CW stories that detail a range of tooling technologies, processes and materials.
Researchers have proven it’s possible to recycle CNTs at the macroscopic scale with nearly 100% retention of mechanical and electrical properties, removing a hurdle to sustainable CNT-based fiber, sheet and textile adoption.
The recycled carbon nanotube sheets retain their key mechanical properties, including their flexibility. Source | IMDEA Materials Institute
Researchers at IMDEA Materials Institute (Madrid, Spain) have recently demonstrated the recyclability of high-performance carbon nanotube (CNT) sheets while maintaining their essential mechanical and electrical properties.
Outlined in the paper, “Network structure enabling re-use and near full property retention in CNT sheets recycled from thermoset composites,” published in Carbon, the findings represent an advance in sustainable nanostructured materials and holds promise for CNT fibers, sheets and textiles to play a pivotal role in the future transition to green energy.
“Even 3 years ago, there was little interest in recycling CNT-based materials and this research is the first attempt in this direction,” contends Dr. Anastasiia Mikhalchan, senior research associate at IMDEA Materials Institute. “It demonstrates that high-performance materials made from carbon nanotubes can be reused as structural reinforcement or electrical conductors. This is due to the fact that neither their continuity, alignment and mechanical properties, nor their conductivity, is affected by this recycling process.”
“These [materials] will be able to displace widespread CO2-intensive materials, such as conventional carbon fibers and some metals like copper, decreasing our future CO2 emissions footprint,” Mikhalchan continues. “The work uses carbon nanotubes rapidly grown and directly assembled into freestanding network materials by means of a floating catalyst chemical vapor deposition [FCCVD] synthesis process.”
According to IMDEA, these CNT fibers and sheets possess high structural toughness and flexibility as well as high mechanical, electrical and thermal properties which enables their use in structural reinforcement in composite laminates, as well as printable strain/stress sensors, electrical conductors, flexible battery anodes, etc.
With the global CNT production capacity increasing annually, recycling CNT-based materials has become a pertinent topic. The research conducted by IMDEA Materials is expected to catalyze the scale-up of manufacturing high-performance CNT materials and accelerate their adoption by industry.
This work is supported by the Rice University-led Carbon Hub Initiative of which IMDEA Materials’ Multifunctional Nanocomposite research group, led by Dr. Juan José Vilatela, is an active member. The team behind this breakthrough, alongside Dr. Mikhalchan, includes former IMDEA Materials intern Sergio Ramos Lozano, IMDEA Materials PhD student Dr. Andrea Fernández Gorgojo, professor Carlos González and Dr. Vilatela.
The structural properties of composite materials are derived primarily from the fiber reinforcement. Fiber types, their manufacture, their uses and the end-market applications in which they find most use are described.
From infrastructure solutions to consumer products, Polish recycler Anmet and Netherlands-based researchers are developing new methods for repurposing wind turbine blades and other composite parts.
The historic Martin Aircraft factory is advancing digitized automation for more sustainable production of composite aerostructures.
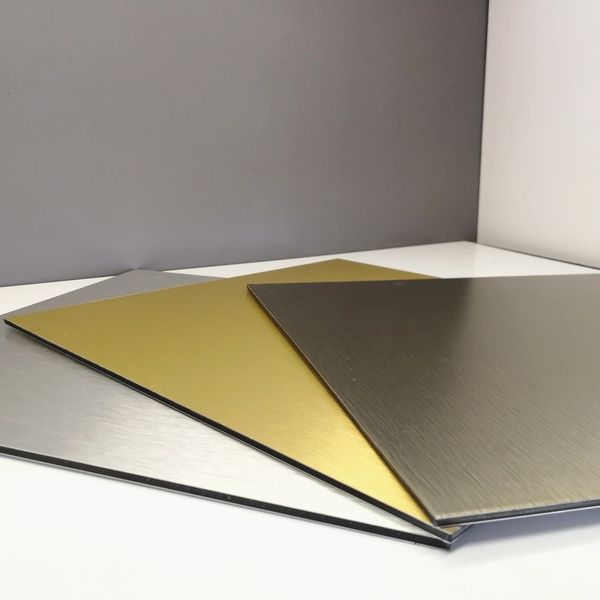
Alum Composite Panel CompositesWorld is the source for reliable news and information on what’s happening in fiber-reinforced composites manufacturing. Learn More