USGlass Magazine & USGNN News
The Info Source of record for architectural glass leaders. Opaque Glass Curtain Wall
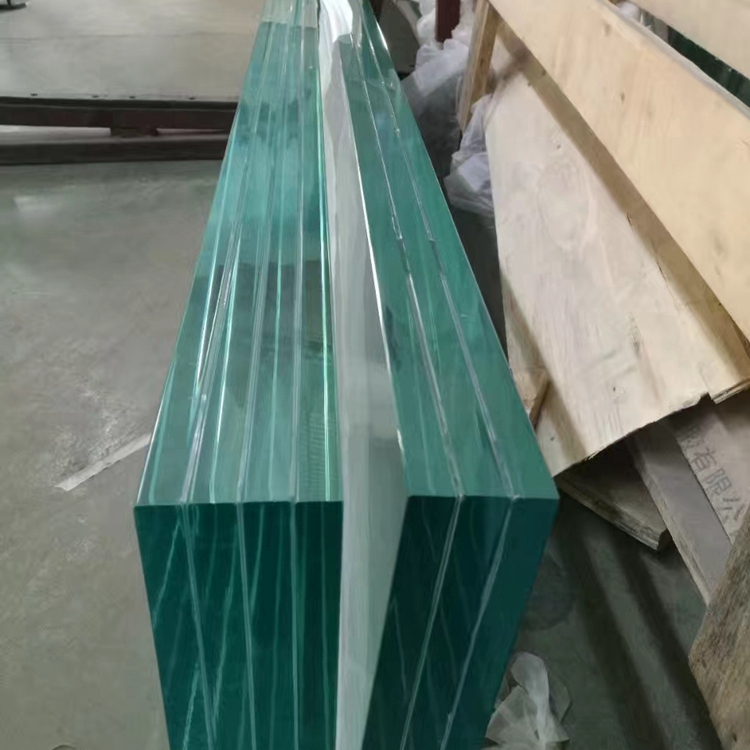
Managing a run of 24-karat gold-coated glass requires increased security, expedited production and special freight logistics. While it might sound like something out of an action movie, it’s something Viracon does approximately every two years.
The company’s first gold production run was in the late 1990s when an architect and owner wanted to market the building as having a 24-karat gold façade. Since then, more projects have requested this special coating. Viracon tracks inquiries and requests for replacement glass with the coating. Once it has enough volume to justify a production run, whether due to a major project or several small projects, the company will begin to put a plan in place.
Seth Madole, Viracon’s director of sales operations, tells USGNN™ that the company will soon implement a new product guarantee for its coatings.
“Within the next few months, we will be announcing a commitment to ensure our proprietary coatings will be available for a minimum of 15 years from the date of manufacture … Too often we see relatively new buildings that have replacement glass that doesn’t match the original glass façade, resulting in a building that looks like a patch-work quilt,” he says. “While design preferences and performance requirements change, buildings that were built years ago will continue to have service and replacement glass needs. A building owner is making a significant investment and should require the ability to continue procuring the product that created the face of their building for years to come. This philosophy leads to our offering of not only our standard products on a regular basis, but also the more unique products like the gold coating.”
Madole explains that procurement and planning of a gold coating production run takes about three to four months.
“It requires 24-karat gold metal targets which we use to apply the gold to the glass through the vacuum deposition process. Once the targets are received we will prepare the coating equipment to be capable of processing the gold material,” he says. “During the set-up and production, we have an increased presence of security due to the value of the materials being introduced into our production process.”
The coater can’t be used for standard coatings during the gold production process, which lasts less than one day. However, the company maintains the capability to produce the 24 karat product for four to six weeks in case of any losses during transport or damage during installation.
After the coating process is complete, the company expedites moving the glass through the insulating line.
“We do this to ensure the glass doesn’t sit on the production floor longer than necessary,” says Madole.
He explains that the company doesn’t use a carrier that would go to a hub and reload the glass, resulting in it being handled multiple times. The glass is shipped on dedicated trucks to reduce handling events and minimize damage and breakage.
Once the production run is complete the coater is transitioned back to produce standard coatings. This process involves reclaiming the gold coating that was sputtered on the inside of the coater to be recycled and returned.
Madole adds that while the gold coating provides aesthetic value to buildings such as Mandalay Bay, Trump Towers and some of Wynn Resorts’ properties, it also provides good overall energy performance.
“For example, the VXG-20 option, when applied to clear glass, provides 21% visible light transmission along with an impressive 0.13 solar heat gain coefficient,” he says.

Green Glass Facade We understand that ads can be annoying to website visitors but it helps us provide our content to you at no cost so we'd appreciate it if you would allow our advertising partners to appear in your browser. Thanks!