PROVIDENCE − Most Rhode Islanders are probably familiar with the Union Paper Co. Building, a brick factory on Admiral Street across from the end of an off-ramp from Route 146.
But few know that they're likely even more familiar with the company's products. Now operating under the name Admiral Packaging, it makes "flexible packaging." Gearless Flexo Printing Press
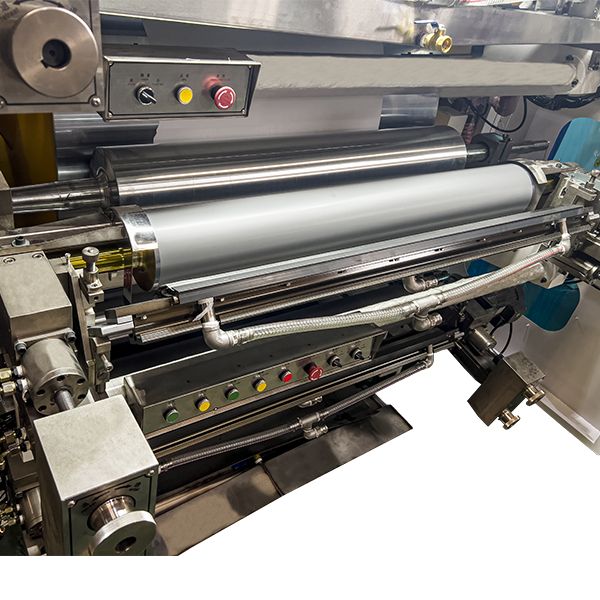
Anyone who's bought Death Wish Coffee, Joseph's Pitas or a bag of Calise Bakery rolls has held Admiral's product in their hands: the plastic bags or pouches that food and other goods come in.
The company was founded in 1898 by Moses Frank on Canal Street, though he sold paper products from a horse-drawn cart. “I believe he was kind of location-less,” said Arron Carroll, president of the company today. The company is now owned by the great-great-grandson of the founder, Harley Frank.
The factory that is currently home to Admiral Packaging was built around 1860 by the Oriental Mills Manufacturing Co., according to the Rhode Island Historical Preservation & Heritage Commission. Admiral bought the 200,000-square-foot complex in 1962, after having been a tenant there for about a decade, and now leases part of the complex to other companies.
Need a break? Play the USA TODAY Daily Crossword Puzzle.
Though "paper" is in the name of the building, the company's products today focus on plastic film, which is used to make packaging products.
Five primary processes go on in the building:
“In lamination, we’re taking two different kinds of plastics and marrying them together so that we can get the properties of both of them together in one product,” said Carroll. “We purchase plastic films of all kinds: polyethylene, polyesters."
Multiple layers of film will be "married" together into what looks like a single sheet of plastic packaging.
He takes a roll of material destined to be packaging for Death Wish Dark Roast coffee, as an example.
“This structure is actually four different layers of plastic – or three plastic layers and one foil layer – there’s a layer of aluminum foil inside this as well,” he said.
“For the inside of the package, we want something that isn’t going to impart any kind of odors or flavors into the customer's products. The foil layer provides a barrier for freshness. These outer layers are for decorative and marketing purposes.”
Admiral uses Flexographic presses – the same type used to print The Providence Journal. Separate flexible printing plates – one for each color of ink on a label – are mounted onto rollers with large sheets of adhesive tape that have to be perfectly smoothed, because air bubbles in the tape could cause a printing defect on the label.
Wide rolls of film, wide enough for several plastic bags, are trimmed down to the width of a single package.
This is the most complicated step in the process, and it can vary depending on the type of finished bag or pouch that's being made. (Pouches are more structurally complex than bags; when full, their bottoms can open a bit so that they can stand, as an example.)
The rolls of printed material need to be cut and sealed. They may have a "gusset" built in to allow standing. They may have perforations cut to allow the end of the bag to be ripped off. They may have a plastic "zipper" installed. They may have holes cut in to allow hanging a pouch from a store display. They may have notches cut that make it easier to start tearing off the end of a pouch.
Besides bags and pouches, Admiral makes "roll stock," where it laminates film together to customers' specifications, prints the label, and then ships large rolls to customers, who will convert them into bags or pouches themselves.
“Our customers are nationwide, coast to coast,” said Carroll. “We have well over a hundred customers, somewhere around 130, actually.”
Besides packages for food, Admiral makes other types, such as those used to ship blood specimens to medical facilities, as well as non-packaging film products, such as industrial tape.
Carroll estimates that the company makes 15 million to 20 million bags and pouches a year. “Also millions of feet of rolls.”
The company employs 97 people, including sales and customer-service workers, engineers, machine operators and warehouse logistics workers.
Manufacturing workers don't have a minimum education requirement but must pass a mechanical skills assessment test as well as a background check. While it requires English-language skills, Carroll said it is taking steps to be able to hire workers who speak only Spanish.
To apply, contact the company through its website, admiralpkg.com.
.jpg)
Flexo Printing Press Machine “We’re a Rhode Island company. We’re proud of Rhode Island. We have people from Rhode Island here,” said Carroll. “We want to help grow the community and help our customers grow.”