Cumberland Additive’s CNC programmer in Pennsylvania spends most of his time writing programs for machine tools in Texas.
Pairing a shoulder mill with a five-axis machine has cut costs and cycle times for one of TTI Machine’s parts, enabling it to support a niche racing community. Non-Friction Finish
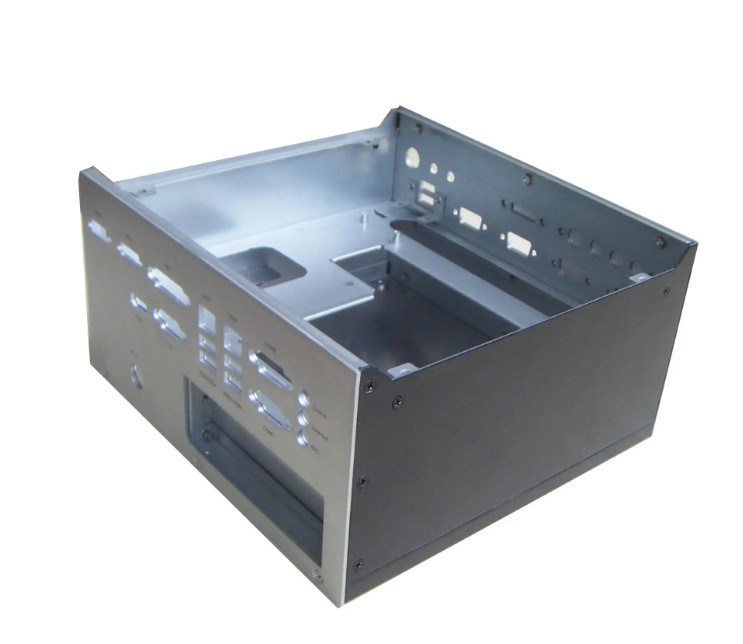
Small details and features can have an outsized impact on large parts, such as Barbco’s collapsible utility drill head.
After more than 40 years in business, this shop has learned how to adapt to stay profitable.
Recognizing the demand for automation solutions in grinding and finishing applications, this abrasives manufacturer is providing free consulting services to help shops develop automated processes.
At its 2024 Music Motion Meeting, Studer AG showed off its entry-level line of grinding machines, as well as its newest universal loading system.
Pairing a shoulder mill with a five-axis machine has cut costs and cycle times for one of TTI Machine’s parts, enabling it to support a niche racing community.
A study in repeatable and flexible workholding by one OEM for another.
Intech Athens’ inventory management system, which includes vertical lift modules from Kardex Remstar and tool management software from ZOLLER, has saved the company time, space and money.
To cut out laborious manual processes like hand-grinding, this briquette manufacturer revamped its machining and cutting tool arsenal for faster production.
Adopting PCD tooling has extended FT Precision’s tool life from days to months — and the test drill is still going strong.
Moving to five-axis machining enabled this shop to dramatically reduce setup time and increase lights-out capacity, but success relied on the right combination of workholding and automation.
Shops need to look at their people, processes and technology to get the most of out their automation systems.
Controlling variability in a closed-loop manufacturing process requires inspection data collected before, during and immediately after machining — and a means to act on that data in real time. Here’s one system that accomplishes this.
Wolfram Manufacturing showcased its new facility, which houses its machine shop along with space for its work as a provider of its own machine monitoring software and as an integrator for Caron Engineering.
Global manufacturer Fictiv is rapidly expanding its use of data and artificial intelligence to help manufacturers wade through process variables and production strategies. With the release of a new AI platform for material selection, Fictive CEO Dave Evans talks about how the company is leveraging data to unlock creative problem solving for manufacturers.
Implementing ProShop has led to a massive process overhaul at Marzilli Machine. From 2020 to 2021, revenue increased 64% without capital investment.
Hexagon has rearranged its software portfolio into five process-based suites, which include software for every step in the workflow as well as a new program that connects everything, increasing automation and collaboration.
Understanding the differences between measurement methods means their discrepancies can be explained and used as an advantage to produce better correlation.
Zeiss Quality Innovation Days brings together quality and metrology experts from all over the world to take part in industry-specific sessions.
Understanding all the things that contribute to a machine’s full potential accuracy will inform what to prioritize when fine-tuning the machine.
Fixed-body mechanical plug gages provide fast, high-performance measurement for tight-tolerance holes.
Thanks to ballbar testing with a Renishaw QC20-W, the Autodesk Technology Centers now have more confidence in their machine tools.
Tool-toolholder-spindle-machine combinations each have a unique vibration response. We can measure the response by tap testing, but we can also model it.
Robotic applications are expanding thanks to rubber and silicone-based systems that can handle fragile materials or parts in varying sizes and shapes.
Shops need to look at their people, processes and technology to get the most of out their automation systems.
Recognizing the demand for automation solutions in grinding and finishing applications, this abrasives manufacturer is providing free consulting services to help shops develop automated processes.
Controlling variability in a closed-loop manufacturing process requires inspection data collected before, during and immediately after machining — and a means to act on that data in real time. Here’s one system that accomplishes this.
With the acquisition of PushCorp, Walter aims to help customers be more productive with robotics and automation for their material removal processes.
At its 2024 Music Motion Meeting, Studer AG showed off its entry-level line of grinding machines, as well as its newest universal loading system.
Across a range of technical presentations aimed at small and mid-sized job shops, the first-ever Automated Shop Conference (TASC) offered insights into several automated technologies, implementation strategies, shopfloor training tips, and even the untapped power of automated coolant delivery.
Automation is no longer a luxury in manufacturing today – it’s a necessity. The Automated Shop Conference (TASC) will connect job shops with experts who offer advice and considerations for this process.
The Automated Shop Conference (TASC) will give shops of all sizes and production volumes key insights and practical guidance on how to implement automation.
Looking to automate your shop floor? The Automated Shop Conference (TASC) will connect shops with experts who can advise them through this transition.
Attend TASC, The Automated Shop Conference, in Novi, Mich on Oct. 11, 2023 for a comprehensive look into how to use automation to transform your machine shop.
Staying adaptable and leading through change for 95 years and counting, Modern Machine Shop celebrates its 95th Anniversary since its first publication in 1928.
The advance toward increasingly automated machining can be seen in the ways tooling, workholding, gaging and integration all support unattended production. This is the area of innovation I found most compelling at the recent International Manufacturing Technology Show.
The renewal of collaborations, partnerships and networking opportunities created a new level of excitement at IMTS 2022 for 86,307 registrants.
Manufacturing has a multi-talented bunch of people, but who knew so many were adept in the facial hair industry? Check out the best of the beards at IMTS!
This year’s show celebrates 10 years of co-location between IMTS and Hannover Messe.
Brent Donaldson of Modern Machine Shop sits down with Supertec's Don Staggenborg to discuss what the IMTS veterans brought to this year's show.
Meet NASA mission system engineer Mike Menzel and learn more about the James Webb Space Telescope at Mitsui Seiki USA’s booth (338700) in the South Hall from 11:00 a.m. to 11:45 a.m. on Thursday, September 15.
You cannot begin to take advantage of an available feature if you do not know it exists. Conversely, you will not know how to avoid CNC features that may be detrimental to your process.
Understanding the differences between measurement methods means their discrepancies can be explained and used as an advantage to produce better correlation.
The decision to gain or retain status as a defense supplier by pursuing CMMC compliance is especially difficult for small- to mid-sized machine shops, and the complexities and misperceptions tied to the program certainly aren’t helping. To break down those complexities, here are five key issues that small- and mid-sized job shops need to know about CMMC.
Understanding all the things that contribute to a machine’s full potential accuracy will inform what to prioritize when fine-tuning the machine.
Fixed-body mechanical plug gages provide fast, high-performance measurement for tight-tolerance holes.
Safety commands help safeguard CNC applications from common programming or operation errors.
Legacy Precision Molds takes us on a tour of their moldbuilding facility. They've recently implemented two automated 5-axis cells for metal and graphite machining that run lights out during nights and weekends.
Verifying parts is essential to documenting quality, and there are a few best practices that can make the quality control process more efficient.
Take a look inside James Engineering, a high-end CNC Deburring OEM that became a job shop when they decided to produce their own parts in-house.
Tool-holder-spindle-machine combinations each have a unique dynamic response in the same way that each person has a unique fingerprint, which can be revealed using modal testing.
Explore Tech-Max, a CNC machine shop that specializes in precision machining large and complex parts ranging from 10 in. to over 10 ft.
Jrlon, Inc. is recognized as a dependable source and leading supplier of plastic and specialty metal products. They are one of the premier PTFE processors in the United States. Jrlon's expertise also covers a wide range of other performance plastic materials and alloy steels for custom molding, machining, gear manufacturing, technical industrial coatings, welding, and sheet metal fabrication. Driven by innovative designers and engineers, Jrlon manufactures unique products vital to a wide variety of industries.
In this episode of Made in the USA, several executives and senior staff at Hardinge give their first-person account of how they formulated the plan to shift the manufacturing of its milling and turning product lines from its Taiwan plant to its plant in Elmira, New York, the major challenges they encountered and the rewards that made it worth the effort.
The L.S. Starrett Co. has been manufacturing precision measurement tools in Athol, Massachusetts, since 1880. Attention to U.S. manufacturing often focuses on reshoring manufacturing from other countries, but Starrett never left. The facility in Athol employs hundreds and produces thousands of tools that remain vital for measurement in machining and other fields.
The latest episode “Made in the USA” podcast explores a company that uses collaborative robots, one of the key tools helping US machine shops and other manufacturers compete with lower cost countries by automating production.
When Puneet and Neelam Neotia moved from India to the United States several years ago, they brought with them a family background in manufacturing and CNC machining. Now the couple is working to get their startup machine shop off the ground, sourcing new customers and getting the word out about their shop in Clarksville, Indiana. The couple — proud to publicize their "Made in the USA" parts — is leveraging family connections and manufacturing capabilities back in India, but not in the way that some people assume.
Entrepreneur Scott Colosimo found early success in China producing parts for his Cleveland-based motorcycle company in the mid-2000s. This is the story of how IP theft issues overwhelmed the business, prompting Colosimo and his team to start over from scratch — and move production back to the United States.
So far, Made in the USA has looked into system-wide effects of broken supply chains, automation, skilled workforce issues and our perception of manufacturing jobs — examining each topic through a prism of individual experiences. For this final episode for Season 1, let’s look at one more system-wide question and bring it back to personal perspectives: Is there today a new dawn, a new moment for American manufacturing?
The Top Shops 2024 survey for the metalworking market is now live, alongside a new homepage collecting the stories of past Honorees.
To combat the skilled labor shortage, this Top Shops honoree turned to partnerships and unique benefits to attract talented workers.
Doubling sales requires more than just robots. Pro Products’ staff works in tandem with robots, performing inspection and other value-added activities.
From cobots to machine monitoring, this Top Shop honoree shows that machining technology is about more than the machine tool.
Deciding to narrow down its jobs and customers was a turning point for 2023 Top Shops Business Strategies honoree Manda Machine that has led to improvements in the front office and on the shop floor.
Thousands of people visit our Supplier Guide every day to source equipment and materials. Get in front of them with a free company profile.
Legacy Precision Molds takes us on a tour of their moldbuilding facility. They've recently implemented two automated 5-axis cells for metal and graphite machining that run lights out during nights and weekends.
Verifying parts is essential to documenting quality, and there are a few best practices that can make the quality control process more efficient.
Take a look inside James Engineering, a high-end CNC Deburring OEM that became a job shop when they decided to produce their own parts in-house.
Tool-holder-spindle-machine combinations each have a unique dynamic response in the same way that each person has a unique fingerprint, which can be revealed using modal testing.
Explore Tech-Max, a CNC machine shop that specializes in precision machining large and complex parts ranging from 10 in. to over 10 ft.
Jrlon, Inc. is recognized as a dependable source and leading supplier of plastic and specialty metal products. They are one of the premier PTFE processors in the United States. Jrlon's expertise also covers a wide range of other performance plastic materials and alloy steels for custom molding, machining, gear manufacturing, technical industrial coatings, welding, and sheet metal fabrication. Driven by innovative designers and engineers, Jrlon manufactures unique products vital to a wide variety of industries.
Onik Bhattacharyya will oversee the GF Machining Solutions product portfolio for the North American market region.
The Pre-Allocation feature simplifies the purchasing and material planning process and prevents unnecessary inventory from sitting on the shelf.
The company’s retention knobs are manufactured from American-made 8620 alloy that is treated with hot black oxide to military specifications for protection against corrosion.
The Girls Take Over Tech event enabled more than 65 students to interact with Sandvik Coromant experts and tour of the company’s advanced manufacturing facility.
The Nanojet solid-carbide reamers are designed to stop chip jamming and enhance application stability.
Roy D. Cripps will lead the team at Bavius as it aims to expand its current business in aerospace structures and develop new market segments. Additionally, the company will showcase its technology during an open house event on June 11.
Titanium and high-nickel alloys burn through inserts and cutting tools more than other materials, especially during roughing. Tools are frequently changed earlier than required in titanium machining as a precaution. Learn about new metalworking fluids engineered to significantly extend tool life without risking costly aerospace parts. Agenda: Learn to select the right metalworking fluid for your aerospace application Understand the impact of fluid selection during initial new product planning Discuss challenges of obtaining metalworking fluid approvals from OEMs Consider how supplier service and support can significantly impact the bottom line
Prepare for a transformative journey into the future of your manufacturing. Join ECI Solutions for a dynamic panel discussion featuring change management and manufacturing ERP experts. This webinar will equip you with the essential tools and tactics to navigate the human side of change and ensure a smooth, high-impact rollout of your new ERP system. The presenters will cover their expert insights on ERP implementation, some pitfalls during the implementation process and how to manage them, and recommendations on building a culture of change. Don’t miss this opportunity to unlock the full potential of your ERP investment and propel your manufacturing business forward. Register now for a transformative discussion on change management for manufacturers. Agenda: Gain perspectives from leading change management professionals on strategies tailored to the unique challenges faced by manufacturers during ERP implementation Navigate the common roadblocks associated with change and discover practical solutions to overcome resistance, boost buy-in and user adoption, and maximize the ROI of your ERP as soon as it is in your business Learn how to foster a culture of openness, communication and collaboration within your organization, laying the foundation for a successful ERP transition Walk away with a clear roadmap for change management excellence in your manufacturing operations
Adding robotic automation to machine tool processes can bring a level of apprehension and confusion on how, when and where to begin. Kuka offers a wide range of automation technology and industrial partnerships to efficiently and effectively bring a project from conception to completion. Considering automation early on in your machine tool buying process can not only save you money and time but it can also ensure that your machine will be efficient when it arrives at your shop. Agenda: Save time and money by automating before you get your machine tool Simplify the process: simple PLC programming, mobile robots, articulated robots and planning simulation Finding the right automation integration partner What to expect out of your automation supplier and the questions to ask Example applications and use cases
While machine data is critical to understanding asset performance, manufacturers need additional context to develop a complete picture of production performance. By capturing operations and work order data in real-time, users can finally visualize and understand not just how their machines are doing but the true status of work-in-process (WIP). In this webinar, MachineMetrics will demonstrate the power of their work order tracking and scheduling analytics releases. Powered by cutting-edge AI, users can now monitor, track, analyze and adjust their production schedules to maximize capacity and get every order shipped on time. It’s time to stop monitoring machines, and start monitoring production. Agenda: The difference between machine monitoring and production monitoring The importance of connecting machine data with operations and work order information Key features MachineMetrics are unveiling to enable next-gen production monitoring
In today's rapidly evolving manufacturing landscape, job shops face unique challenges stemming from a severe labor shortage and the growing demand for faster job setup times. This presentation delves into the crucial importance of automation for job shops and highlights ProCobots as a provider of high-mix, low-volume automation solutions. The discussion begins by addressing the pressing issue of labor shortage, which has compelled job shops to seek efficient and cost-effective alternatives. One of the key solutions lies in the extremely fast job setup time offered by automation systems, which streamline processes and reduce reliance on manual labor. The benefits of collaborative robots (cobots) over traditional industrial robots are also highlighted, emphasizing their versatility, safety, and ease of integration into existing workflows. This presentation showcases ProCobots as a provider of effective high-mix, low-volume automation, pointing to how it can cater to the diverse needs of job shops that handle a wide range of parts and projects. Throughout the presentation, attendees are taken through the step-by-step process of automating a part for a Hurco CNC mill using ProCobots' automation software. From initial planning to seamless integration with the Hurco control, participants gain valuable insights into how automation can revolutionize job shops and drive efficiency, productivity, and profitability. By showcasing real-world examples and practical applications, this presentation aims to inspire job shop owners and operators to embrace automation as a strategic imperative for staying competitive in today's dynamic manufacturing environment. Agenda: Why automation? Collaborative robots vs. industrial robots Why ProCobots: system components and the Hurco Automation Job Manager
In a rapidly-evolving manufacturing landscape, the integration of additive manufacturing (AM) technologies into CNC machining operations is not just an innovation but a necessity for staying competitive. Phillips Corporation invites you to this insightful webinar that sheds light on the transformative impact of 3D printing in CNC shops. Join the presenters as they delve into real-world applications, financial insights and the future of manufacturing. Join Phillips for this engaging webinar on how 3D printing can revolutionize your CNC operations from enhancing design flexibility and operational efficiency to securing significant financial advantages. Whether you’re just starting to explore the potential of additive manufacturing or looking to optimize its integration, this session will provide valuable insights and practical advice for leveraging AM technology to its fullest potential. Agenda: Learn how AM streamlines production processes. drastically reducing lead times and the need for extensive inventory while optimizing labor costs Explore the design flexibility that AM offers, allowing for complex geometries and customization options not feasible with traditional CNC machining Review the compelling financial rationale for integrating AM now, detailing cost savings, efficiency improvements and the competitive edge it provides
Explore integrated solutions that make manufacturing more efficient at ZOLLER Inc.'s 2024 Open House and Technology Days. This two-day event June 12 and 13, 2024, at the company's North American headquarters in Ann Arbor, Michigan, will highlight real customers who have leveraged ZOLLER technology to optimize their manufacturing processes and boost profits.
RAPID + TCT is returning to the west coast after a decade away! For more than 30 years, RAPID + TCT has defined the crucial role of additive manufacturing and empowered the establishment of an industry that continues to conceive, test, improve and manufacture new products at a faster, more cost-efficient pace. SME and Rapid News Publications have teamed up to produce the annual RAPID + TCT event, which takes place June 25-27 in Los Angeles, California. The event is for those who provide technology and for those who need to understand, explore and adopt 3D printing, additive manufacturing, 3D scanning, CAD/CAE, metrology and inspection technologies.
Laser powder bed fusion is the most widely used additive manufacturing method for metal part production, and electron beam melting is a closely related technology. For metalworking facilities contemplating a move into metal AM using technologies such as these, here is a road map for success. Speakers will cover materials, safety, part design, production workflow and differences between laser and electron beam metal powder bed fusion systems.
FABTECH 2024 will be held October 15-17, 2024, in Orlando, Florida, at the Orange County Convention Center. FABTECH provides a convenient ‘one-stop shop’ venue where you can meet with world-class suppliers, discover innovative solutions, and find the tools to improve productivity and increase profits. There is no better opportunity to network, share knowledge and explore the latest technology, all here in one place. Future U.S. Show Dates and Locations 2023 – September 11-14 at McCormick Place in Chicago, IL 2024 – October 15-17 at Orange County Convention Center in Orlando, FL 2025 – September 8-11 at McCormick Place in Chicago, IL 2026 – October 21-23 at Las Vegas Convention Center in Las Vegas, NV 2027 – September 13-16 at McCormick Place in Chicago, IL
Understanding all the things that contribute to a machine’s full potential accuracy will inform what to prioritize when fine-tuning the machine.
While there are many changes to adopt when moving to five-axis, they all compliment the overall goal of better parts through less operations.
Consider what types of implementation your shop prefers when deciding between workpiece-handling and pallet-handling automation solutions.
When getting a grip on stainless steel, make sure you are very specific in how you talk about it and understand the pertinent information you need.
Consider these spindle attributes to make a choice that is balanced, usable and compliments your processes as best as possible.
While nearly all ER systems will have cross compatibility, they’ll have small differences across manufacturers that make their implementation at the shop level not as standard.
A horizontal machining center (HMC) is a machining center with its spindle in a horizontal orientation. This machining center design favors uninterrupted production work. One reason for this is that the horizontal orientation encourages chips to fall away, so they don’t have to be cleared from the table. More significantly, the horizontal design allows a two-pallet workchanger to be incorporated into a space-efficient machine. To save time, work can be loaded on one pallet of a horizontal machining center while machining occurs on the other pallet.
Downtime is the enemy of efficient manufacturing — a problem FIBA Technologies has addressed through purchasing a Soraluce FLP 14000.
Machining centers offer a wide range of possible operations, but that adaptability comes with the need to stay flexible and perform successful measurements at all times.
Compared to vertical machining centers, horizontal machining centers offer the potential for improved spindle uptime, cycle times and throughput. Although they come with a higher price tag, their higher productivity can be significant to shops of all sizes, as Valley Tool has experienced.
J&R Machine uses machine-monitoring data not just to track machine uptime, but also to create a financial index that helps it shape decisions related to equipment, processes, staffing, sales and business in general.
Is it time to move up to an HMC? Let’s consider some of the peripheral equipment that HMC buyers should think about.
Is it time to move up to an HMC? Let’s look at tooling- and workholding-related concerns that those interested in acquiring an HMC will want to keep in mind.
Is it time to move up to a horizontal machining center? Let’s consider some of the structural, application and design factors that differentiate HMCs from vertical machines.
Horizontal four-axis machining enabled McKenzie CNC to cut operations and cycle times for its high-mix, high-repeat work — more than doubling its throughput.
The Fryer HR-40 features a built-in 24" rotary table for multi-sided machining.
The new FH5000 series machines include a 500-mm table capable of handling 1,000-kg loads.
Stecker Machine Company shows that getting the most value from employees means valuing your employees.
Romi Machine Tools’ new GL300 S features high-power torque and feed force and is built with a robust monoblock base for ultimate rigidity and precision.
The FH5000 Series from JTEKT Toyoda is compromised of three high-speed horizontal machining centers.
This unique fixturing system provides maximum hold with minimal clamping footprint to optimize spindle clearance and allow chips, debris and cutoffs to drop below the machining area and away from the spindle. (Sponsored)
By day, NTL Industries went from a lathe and a mill in a home garage to an 11-employee enterprise in under five years. By night, it tackles a new future.
One of our fascinations with large-format machine tools has little to do with their capabilities, but everything to do with the logistics involved with getting them up and running. Here’s how one of the world’s oldest builders of giant machine tools tackles the challenge.
Roughing operations can push a CNC spindle to its limits. Understanding how to interpret the horsepower chart can keep these operations within safe limits.
Adopting horizontal three-axis machining may require much consideration, but Alicat Scientific can attest to almost 50% cycle time reductions with a Kiwa horizontal machine.
Machining centers offer a wide range of possible operations, but that adaptability comes with the need to stay flexible and perform successful measurements at all times.
What is a horizontal machining center?
Horizontal and vertical three-axis machines differ primarily in the inclination of the spindle, with the spindles of horizontal machines parallel to the surface of the machine table and the spindles of vertical machines perpendicular to the surface, although individual constructions vary widely to support different applications.
Source: Machining 101: What are Machining Centers?
What is a machining center?
Typically, machining centers are numerically controlled machines with multipurpose capabilities. This flexibility not only allows for productivity improvements but also allows for one machine to replace several single-purpose machines.
Machining centers provide the ability to perform several operations on a workpiece, from roughing to finishing, with a single setup.
Why should you buy a horizontal machining center?
The simple answer is productivity and profit. Horizontals can easily do three times the work of a comparable VMC. This assertion assumes that the workload to keep the machine busy is available. Without question, you can get more done in far less time using an HMC. With the increase in production, shop throughput is greatly improved. Because multiple operations can be done in a single setup on an HMC, less work in process must move around the shop, increasing efficiency.
Source: Buying an HMC: What Makes Horizontal Machining Centers Different
What are some additional costs of adding a horizontal machining center?
To make full use of the higher-level machine, other parts of the process need to be raised to a higher level as well. Here is a partial list of the additional investments to be made:
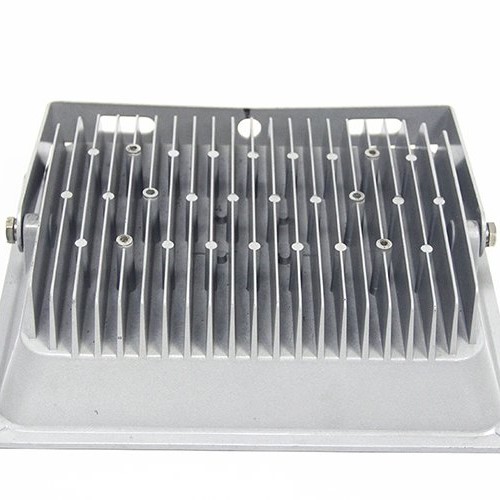
Cnc Machine Weight Modern Machine Shop is the leading publication and media brand in North America devoted to CNC machining. MMS combines unprecedented editorial access to manufacturing facilities with decades of experience to provide long-form content that is both insightful and impactful. About Us