3D printing news News Filaments vs Pellets: Which Type of Plastic to Choose for 3D Printing?
Plastics are without doubt one of the most widely used material families in additive manufacturing. Compatible with a wide variety of processes, they offer multiple properties and characteristics to parts, whether those are destined to be prototypes, tooling or end-use objects. Available in many forms – filaments, pellets, powders, resins – they meet the needs and requirements of manufacturers in all sectors. While we compared powders to plastic resins a few months ago, it’s time to take a look at two other polymer families: filaments and pellets. What are their characteristics and applications? Which 3D printing processes are they compatible with? What manufacturers are on the market, and how much do these materials cost? We tell you all about it in this new dedicated article! Engineering Pa

Filaments and pellets are two forms of material currently compatible with 3D printing, and although metallic and ceramic solutions are available today, we’ll be concentrating solely on plastics. First of all, we need to go back over the definition of a plastic pellet and a plastic filament. A pellet is a kind of small ball 0.5 cm in diameter that can be melted, molded or extruded to make all kinds of plastic objects. Plastic pellets are therefore key in the chemical industry. They can be used in additive manufacturing with specific machines.
To make filament for 3D printers, you need plastic pellets (photo credits: Capifil)
Filament, on the other hand, is a thermoplastic obtained by mixing plastic pellets or ground plastic scrap with several additives. A filament extruder is required to achieve the tube-like appearance. After several stages of cooling, the filament passes through a coiling machine to obtain a spool that can then be used by a 3D printer.
Plastics production is a huge market, with figures rising in recent years in terms of manufacturing, employment and investment. These plastics can take a variety of forms when they leave the refinery: liquids, powders or pellets. In all cases, they are then shaped to produce all kinds of parts, whether by molding, injection, thermoforming or, of course, extrusion.
Turning first to industrial plastic pellets, it’s worth noting that there are a huge number of them on the market, offering a wide range of properties and characteristics depending on their chemical composition. Also known as nurdles or pre-production plastic pellets, they are defined as “very small pellets of plastic (smaller than 5mm) that serve as raw material in the manufacturer of plastic products”. They can also be different colors.
Industrial plastic pellets are a mixture of the polymer itself and chemical additives. Several polymers are used in this process, including polyethylene (PE), polypropylene (PP), polyethylene terephthalate (PET), polystyrene (PS) and PVC. Naturally, the mechanical and chemical properties of each plastic pellet vary considerably.
Plastic pellets are widely available on the market (photo credits: DEKRA Industrial)
One of the advantages of the use of pellets in 3D printing is that they are already used in more traditional manufacturing technologies, such as injection molding. This means that if you use a qualified material in additive manufacturing, you can use the same one if you switch to injection molding, without having to go through a qualification stage. This is a considerable advantage, not only for the production of “right material” prototypes, but also for the manufacture of finished parts using materials already recognized by industry.
If we now turn our attention to filaments, the manufacturing process takes longer, since it involves transforming plastic pellets into tubes capable of being extruded. Several stages are involved: first, the moisture is removed from the pellets. Next, the pellets are melted so that they can be passed through an extruder, which gives the filament its tubular shape. Once formed, the filament is cooled in suitable baths. It is then spooled for use on a 3D printer.
In the process of transforming pellets into filament, additives are added, which inevitably alter the raw material. When using a filament to 3D print a part, an additional step is required to qualify the material. In terms of compatible plastics, you’ll find several types of polymer, from PLA to ABS, as well as elastomers and high-performance polymers such as PEEK or PEI. Depending on the filament chosen, the part’s properties will differ: if you’re looking for transparency, you’ll opt for polycarbonate, whereas if you’re looking for mechanical strength, you’ll choose PEEK.
Please note that some plastics are more difficult to transform into filament due to their chemical composition, so you’ll have a wider choice of materials if you opt for pellet 3D printing.
The KIMYA filament production plant (photo credits: Hervé Boutet)
Whether you opt for plastic pellets or filament, the preferred printing process is extrusion, or more specifically fused deposition modeling (FDM/FFF) for filaments and Fused granulate fabrication (FGF) for pellets. The principle is basically the same: the plastic material is heated and then passed through an extruder before being deposited layer by layer on a platen to form the final object. The difference lies in the tool used for extrusion.
In the case of filaments, 3D printers use an extruder with a stepper motor and a toothed wheel to advance or retract the filament. At the end of this feeder is a heating block which, as its name suggests, heats the material. The material then passes through a nozzle, varying in diameter between 0.4 and 0.8 mm, which moves to deposit the filament on the print bed. Depending on the material you’re using, you’ll need a brass or copper nozzle, a heated chamber, a heated plate, etc. The thermoplastic will determine the type of machine you need and your printing parameters.
For pellets, the extrusion process (FGF) is a little different: the 3D printer uses a hopper system to absorb the plastic beads and push them to the melting zone. The pellets are then softened and ejected by the nozzle, which can then deposit the material layer by layer on the printing plate. This nozzle can have different diameters, generally larger than those used on FDM 3D printers that use filaments. Finally, this type of extrusion system can be installed on robotic arms to offer greater printing surface and flexibility.
The extrusion system for plastic pellets is different from that for filaments (photo credits: Pollen AM)
The use of plastic pellets enables higher deposition speeds and larger volumes to be achieved than with a filament. On the other hand, precision and resolution are less important. Pellet 3D printing is therefore preferable for large-format parts, as the filament spool does not need to be changed, and the machine is capable of extruding a larger quantity without interruption.
It should be noted, however, that the pellet 3D printer cannot shrink the material, which may result in a greater flow of plastic through the nozzle than on an FDM machine. To interrupt the flow of material, the nozzle would have to be stopped or blocked. So it’s best to turn to 3D filament printing to design more complex and detailed parts.
Overall, the applications of 3D printing with pellets or filaments are quite similar: prototyping, tooling, finished parts, the spectrum is wide. But, as you’ll have gathered, there are a few key differences to bear in mind before taking the plunge.
As far as filaments are concerned, their versatility and availability on the market mean that they can be used for a wide variety of applications. They lend themselves well to the creation of modest-sized parts, but also to projects requiring a certain level of detail and precision. Filaments are widely used in the field of rapid prototyping, enabling designers and engineers to create models and multiply tests to evaluate concepts before final production. Depending on the properties of the filament in question, it is possible to design parts for the automotive, aeronautics, food, medical and other industries. Some thermoplastics are fire and smoke resistant; others are biocompatible; some are reinforced with carbon fibers for greater strength while remaining lightweight.
Steam armchair designed by Slicelab and printed with PETG pellets on the EXT 1270 Titan Pellet 3D printer
If we look at pellets, what is particularly interesting is that it is possible to create tailor-made formulations by mixing different types of plastic. This versatility opens the door to a multitude of applications, not least in the healthcare sector, where biocompatible materials can be developed for the manufacture of customized prostheses and implants. In the automotive sector, pellets are used to create customized parts such as dashboard elements, cable trays, engine covers and mechanical components, speeding up the development process and reducing costs. They are also in demand in the design sector for larger furniture and decorative items. Last but not least, it is also possible to make pellets from recycled materials, thus promoting the circular economy, a particularly important concept in today’s society. The same recycled pellets can be used to produce filaments.
Finally, as mentioned earlier in the article, using pellets in additive manufacturing is particularly interesting for material prototyping. As the raw material is the same in both 3D printing and injection molding, an operator can 3D print prototypes, submit them for testing and certification before moving on to mass production, without having to go through additional certification stages. This saves manufacturers a considerable amount of time.
Filaments are widely available on the market and are more often than not affordable for beginners. This is because they are sold in spool form, usually 750 grams, which makes them easier to manage and store. Prices vary according to the type of filament, but in general, you can get a spool of PLA, one of the most popular materials, for around 20 to 30 euros. However, some more specific filaments, such as flexible or composite filament, can be more expensive, ranging from 30 to 50 euros per spool. What’s more, if you frequently print large objects, the cost of filaments can rise rapidly.
Pellets, unlike filaments, are generally sold in multi-kilogram bags, which means you can buy a large quantity of material at once. This can represent a higher initial investment, as prices for bags of pellets can vary from 50 to 100 euros or more, depending on the type of plastic and the quantity. However, from a purely financial point of view, pellets often win out over filaments. The price per kilo of pellets is lower than that of filaments, mainly due to the transformation process required to create the latter. On the other hand, a user wishing to purchase a small quantity of plastic pellets may find it difficult to find the amount required.
So keep in mind that, although the initial price of pellets may seem higher due to bulk purchase, it may prove more advantageous in the long run for frequent 3D printing users. This will of course depend on your needs and budget.
A spool of filament remains relatively accessible (photo credits: La Nouvelle Ecole)
In the 3D printing market, there are a multitude of filament and pellet manufacturers, each making their own contribution to this fast-growing industry. As explained above, filaments are widely prized for their ease of use and affordability. Companies such as Polymaker, 3DXtech, 3D4Makers, Nanovia, ColorFabb and Kimya offer a wide range of high-quality filaments, from PLA to PETG and ABS. The major chemists make a major contribution to this industry, some having developed their own filament brands, like BASF or Evonik.
When it comes to plastic pellets, the manufacturers are more or less the same chemical groups – Arkema and SABIC, to name but two. There are also players like Felfil, 3DXtech and Xtellar. Some have even specialized in the production of plastic pellets from recycled waste, such as the American company re3D; others, like KIMYA, focus on both pellet and filament production,
Finally, when it comes to the manufacturers of machines compatible with this type of plastic, the choice is vast, particularly when it comes to filaments. There are traditional players such as Stratasys, UltiMaker and Zortrax. More and more players are entering this market, with office, professional and industrial solutions. On the pellet side, we can mention manufacturers Arburg and Pollen AM, as well as 3D Systems, which acquired Titan Robotics in 2022, and AIM3D. The list is by no means exhaustive.
In conclusion, both types of plastic offer production advantages well suited to different manufacturing situations. Make sure you use the right material to maximize the efficiency of your additive manufacturing process!
Do you prefer filaments or pellets? Let us know in a comment below or on our LinkedIn, Facebook, and Twitter pages! Don’t forget to sign up for our free weekly Newsletter here, the latest 3D printing news straight to your inbox! You can also find all our videos on our YouTube channel.
Interviews From Users of the Technologies
Application and 3D Printer Rankings
Videos From 3D Printing Trade Shows
Your email address will not be published. Required fields are marked *
Name *
Email *
Website
3Dnatives is the largest international online media platform on 3D printing and its applications. With its in-depth analysis of the market, 3Dnatives gets over 1 million unique visitors per month and is currently available in English, French, Spanish, German, Italian. 3Dnatives works with key Additive Manufacturing market players and offers a variety of services such as a 3D printing price comparison engine, B2B consulting and B2B brand content, event management and much more!
84 countries and 60k+ stakeholders strong, SPE unites plastics professionals worldwide – helping them succeed and strengthening their skills through networking, events, training, and knowledge sharing. For more information, visit www.4spe.org.
Compare Desktop 3D Printers Compare Professional 3D Printers Compare 3D Scanners 3D Printing Directory Choose a 3D printer 3D Printing Directory Event Board Job Board Newsletter Advertising
3Dnatives Europe 157 Boulevard Macdonald 75019, Paris France
SPE US Office 83 Wooster Heights Road, Suite 125 Danbury, CT 06810 P +1 203.740.5400
SPE Europe Serskampsteenweg 135A 9230 Wetteren Belgium P +32 498 85 07 32
SPE Middle East Office N. ESO:14, Desk 34 Sheikh Rashid Tower, Seventh Floor Dubai World Trade Center P.O. Box 9204 Dubai, UAE
Interviews From Users of the Technologies
Application and 3D Printer Rankings
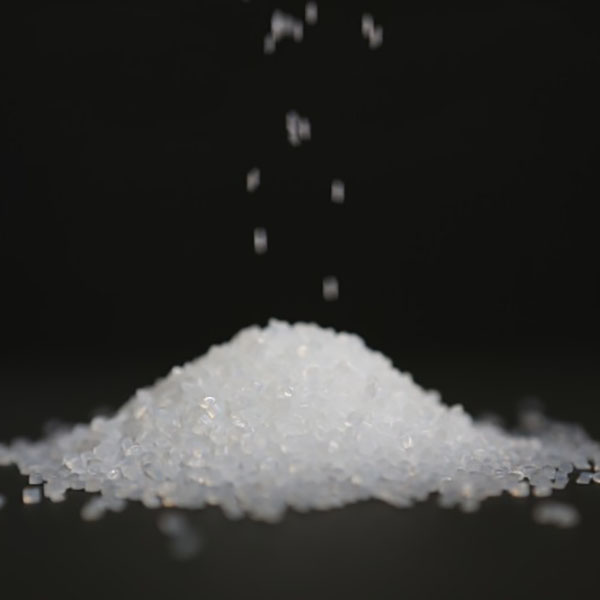
Polyamide 6 Videos From 3D Printing Trade Shows