Molded plastic gears have long provided alternatives to metal gears in lightly loaded drives. They transmit power quietly and often without lubrication in applications such as food processors, windshield wiper drives, and even watches. They also reduce the number of parts and resist chemicals in many applications.
Previously, plastic gears were limited to ¼-hp drives because of variations in their properties and uncertainties about how they respond to environmental conditions such as moisture, temperature, and chemicals. Sprocket Uses

Today, better molding controls combined with design practices that more accurately encompass environmental factors have boosted plastic gear drive capacity to ¾-hp.
Though plastic gears give engineers more flexibility, designing them is more complicated. Their material properties and dimensions vary with changes in environmental conditions, thereby affecting speed reducer capabilities.
Few, if any, engineers have sufficiently broad expertise to design speed reducers with plastic gears. Therefore, the first step is to assemble a team of experts consisting of at least a gear engineer, plastics engineer, and plastics supplier. Other valuable additions may include a manufacturing engineer, quality control engineer, molder, and tool builder.
The team's objective is to design each gear set for nominal operating conditions, fine-tune the design for worst-case operation, and create detailed specifications for producing prototype and production gears.
Before starting the design process, engineers accustomed to designing metal gears need to understand the major properties of plastics that affect gear performance. These include strength, elastic modulus, thermal expansion, moisture absorption, and friction characteristics.
Plastics have much lower strengths than metals. For example, bending strength ranges from 12,000 to 45,000 psi, depending on the specific material. This means larger gears to carry the same load. However innovative designs, such as those that split the torque between two or more gears operating in parallel, can minimize the size of a gear set.
Strength and stiffness vary widely with temperature extremes and exposure to water and chemicals. For example, the elastic modulus of plastic drops as much as 60% with a 90oF temperature rise, whereas the modulus of steel remains nearly constant. Nylons absorb moisture, causing some of them to lose as much as 50% of their modulus.
Gear dimensions also change with environmental conditions. The coefficient of thermal expansion for unreinforced plastics is three to twenty times that of metals. However, certain reinforced plastics offer thermal expansions close to that of metals. The thermal effects of molding, particularly gating and cooling, affects the long-term dimensional stability of gears.
Moisture absorption causes plastic parts to swell, especially those made from nylon. Swelling reduces gear tooth clearances, causing tightly meshing gears to jam. Therefore, the designer needs to compensate by increasing clearances or by selecting a material with less swelling tendency. Some chemicals cause plastics to either shrink or swell.
Friction and wear characteristics depend largely on geometry, load, speed, surface finish, material combination used in mating gears, and environment conditions. The coefficient of friction typically ranges from 0.10 to 0.40 for plastic-on-steel and 0.12 to 0.60 for plastic-on-plastic. These characteristics tend to be poorly defined.
Using two different materials in mating, dry-running gears tends to reduce wear and noise. Conversely, using the same material in both gears gives better dimensional control.
Additives such as PTFE, silicone, or graphite improve the natural lubricity of plastics, and reduce wear. But be sure the lubricants are compatible.
As you define the operating conditions for a speed reducer, be sure to include any environmental conditions that are appropriate to the application. Then select the type of reducer.
A single-stage spur gear offers high efficiency and capacity but can't achieve large speed reductions. So designers often select multiple-stage reducers, using the same gears in each stage to minimize tooling. Because torque in the last stage is highest, this approach causes all earlier stages to be oversized. Splitting a multiple-stage reducer into multiple paths, as with planetary designs, can shrink its size.
The types of shafts and bearings carrying the gears can affect gear center distance. Ball or needle bearings accurately control gear position, reducing variations in center distance. Plastic gears with molded-in shafts tend to be out of round, causing increased center distance variation.
If the gear housing material differs from that of the gears, thermal expansion and the effects of moisture and chemical absorption will alter gear alignment and center distance. These differences may also cause gear teeth to jam. A housing material with the same thermal and moisture expansion as the plastic gears inside will minimize these problems. But plastic housings are poor heat conductors and may cause gears to run hotter.
Adding functional elements to molded plastic gears reduces the number of parts, but makes it more difficult to hold tolerances, and causes out-ofround gears.
When selecting plastic gear materials, look for those with sufficient strength and stiffness to handle the expected loads. Then make sure that any changes in dimensions and frictional characteristics due to environmental conditions are acceptable for the application. Material suppliers can provide a lot of useful information on these properties for various plastics. But you may still need to test prototype gears under realistic operating and environmental conditions to verify that they'll perform as intended.
Gear teeth must have adequate strength and fatigue endurance to carry normal and shock loads. Fatigue data from gear tests will help verify adequate bending fatigue strength at the tooth root. Fatigue or S-N curves typically show root bending stress as a function of the number of operating cycles. These curves should show the effects of temperature.
When such curves aren't available, use standard fatigue data as described in ASTM D671. Such data usually apply only to ambient temperatures.
The stiffness and deflection of meshing teeth depend on the elastic modulus. A high modulus (rigidity) minimizes tooth deflection, whereas a low modulus reduces shock loads and noise.
The elastic modulus depends largely on temperature, loading rate, humidity, and chemical exposure. Tensile tests or Dynamic Mechanical Analysis (DMA) measurements give temperature-related data. But the effects of the other variables are not as well defined, and usually require testing.
Dimensionally stable materials help maintain gear tooth contact ratio, tooth tip clearance, and overall geometry. Factors that affect plastic part dimensions include temperature, moisture, chemical exposure, and manufacturing process. The coefficient of linear thermal expansion (CLTE) is commonly available, and ranges widely for different materials. But it may not accurately represent temperature-induced dimensional changes. Therefore, you may need to conduct tests to determine these changes.
Moisture data are usually expressed as the percent of moisture absorption rather than as a dimensional change. Dividing the percent of moisture absorbed by four gives the approximate dimensional change in percent. Because plastic gears may encounter a variety of chemicals and lubricants, the effects of specific chemicals often require testing.
Wear is a primary concern for plastic gears that run without lubrication. These gears tend to run hot at low loads, causing tooth wear failures. Therefore, they should be made from materials with high wear resistance and good lubricity.
Gear wear information appears in fatigue or S-N curves in terms of contact stress as a function of life cycles. Wear rate may be affected by temperature and moisture, so gears must be tested under these application conditions.
Bringing in reinforcements. Fiber reinforcement such as glass, carbon, or aramid improves the mechanical properties of plastics. Glass-reinforced plastics used for dry-running gears usually contain a lubricant such as PTFE. Carbon fiber reinforced plastics may also contain a lubricant. Aramid fibers are used mostly to reduce wear.
Long fiber reinforced plastics impart high strength and fatigue endurance. They also shrink uniformly and consistently, which improves gear molding accuracy. Such reinforcements are often used in higher power, lubricated systems where excessive tooth deflection may be a problem.
With the reducer configuration and materials selected, perform a preliminary sizing of each gear set. Designers may be tempted to stop the design process at this point, proceeding to specifications, drawings, and making prototypes. But only those designs with minimal load and accuracy requirements operating in a narrow moisture and temperature range are likely to succeed with this approach.
Both gear quality and manufacturing tolerances must be selected. Higher quality gears, as defined in AGMA and ISO standards, run quieter and have lower stresses, but cost more.
The allowable tolerance variations for gears, bearings, shafts, and housing, in combination with dimensional variations, must give satisfactory clearances, tooth loads, and contact ratios under all conditions. One way to check this is to analyze tight and open mesh conditions.
After preliminary sizing and tolerance selection, the real gear design effort begins. Successful drive design with plastic gears requires analyzing both tight and open mesh -- maximum and minimum tooth engagement -- conditions.
A tightly meshing gear set operates at its minimum center distance while the gear dimensions are such that they maximize tooth engagement. This condition is characterized by maximum gear diameter and tooth thickness, minimum tip radius (needed for molding), and maximum root diameter. With a tight mesh, verify that the gear set still has adequate clearance and backlash to prevent tip interference and stalling.
After making any design modifications at tight mesh, examine the open mesh condition. Here, gears operate at maximum center distance and their dimensions minimize tooth engagement. They have minimum outside diameter and tooth thickness, maximum tip radius, and minimum root diameter. In this case, the main concern is the contact ratio. If it's less than one, change the pitch or tooth proportions, or adjust tolerances to reduce the variation in center distance (and thus the contact ratio) between tight and open mesh conditions.
Validating the gear set design can only come from realistic prototype testing. For best results, make sure that both the prototype tooling and molding conditions mirror the production environment. Additionally, the prototype gear sets must be tested under conditions that truly represent the application.
Crystalline type plastics generally provide characteristics that ensure reliable gear operation, as well as consistent shrinkage needed for precision molding. These materials include nylon 6/6, polyacetal, polyphenylene sulfide (PPS), thermoplastic polyester, long fiber reinforced plastic and liquid crystal polymers (LCP).
Most plastic gears are made from nylon and acetal. But nylon absorbs moisture with resultant changes in properties and dimensions. Acetal copolymers provide long-term dimensional stability as well as high fatigue and chemical resistance over a wide temperature range.
Thermoplastic polyesters are also more dimensionally stable than nylon. Where no lubricant is used, both nylon and polyester provide good lubricity when mated with polyacetal.
Liquid crystal polymers give high dimensional stability and chemical resistance, plus low mold shrinkage and high accuracy. To date they have been used only for small gears under light loads, such as watch gears.
Linear polyphenylene sulfides have high temperature and chemical resistance and good fatigue life. They work well in highly loaded parts molded with fine details.
Long fiber reinforced plastics provide good dimensional repeatability and shrinkage consistency in large parts. Moreover their high stiffness, plus creep and impact resistance make them suitable for gear housings.
Non-crystalline plastics have found limited success for gear applications. ABS is suitable only for lightly loaded gears. Polycarbonate usually requires glass reinforcement or a solid lubricant such as PTFE to obtain satisfactory lubricity, chemical resistance, and fatigue properties.
For drive designers, plastic gears offer several benefits including design flexibility, reduced noise, and the ability to operate without lubrication. Other benefits include lower cost and weight, higher efficiency, (improved accuracy), and chemical resistance.
Design flexibility. The design opportunities that plastic gears afford are a major advantage. They can be molded in shapes difficult to machine in metal. Other functional elements such as springs and pawls can be molded into them, thereby consolidating parts and trimming the cost, weight, and complexity of geared speed reducers.
Cost. They are molded in high volumes at low cost, typically one-half to one-tenth that of stamped, machined, or powder metal gears. They're usually ready to use as-molded and require no finishing.
Weight. Plastics inherently weigh less, typically 15 to 20% as much as steel, but plastic gears must be larger to transmit the same power.
Noise. Compared with metal, plastic gears run much quieter. Depending on the application, their sound level compares to that of metal gears one or two AGMA numbers higher in quality. Plastic gear teeth deform, compensating for noise-producing gear misalignment and tooth errors, and the material absorbs impacts that would otherwise cause running noise.
Efficiency. A low coefficient of friction means less horsepower wasted in heat. Plastic gears also lend themselves to efficient designs such as split-path planetary drives.
Lubrication. Inherent lubricity and chemical resistance mean plastic gears can be used with or without lubrication as needed for specific applications.
Accuracy. With consistent material quality, and accurate molding process control, plastic gears can achieve high precision -- up to AGMA Quality 10.
Durability. Chemical and corrosion resistance typically exceeds that of metal gears, especially in wet applications.
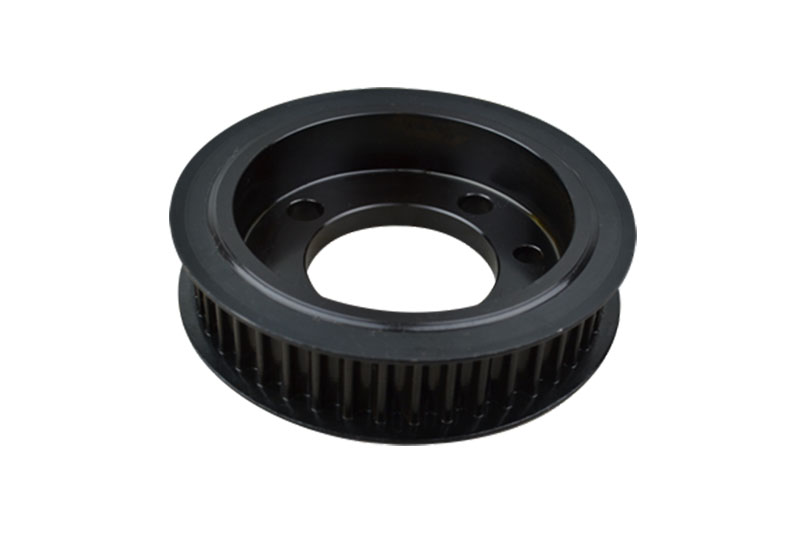
Aluminum Pulley Zan Smith is a staff engineer, Ticona LLG, Summit, N.J. | Related Article: Plastic gear design — Doing it right