With public awareness of the problems of ocean pollution at an all-time high, there is a major drive to ensure a greener approach to the transportation of goods by sea.
Did you know that some 80 percent of world trade is conveyed by shipping? While air cargo transports over US $6 trillion worth of goods annually (Source: IATA), shipping remains the most effective way of transporting bulk goods such as mineral ores, fuels, and cereals, while also carrying a vast range of goods for consumers and manufacturers. Portable Gas Analyzer

To reduce pollution by ocean-going vessels, the International Maritime Organization (IMO) has gradually introduced stricter emissions levels for Sulphur Oxide (SOx) and Nitrogen Oxide (NOx). In the latest Tier III standard, which applies to ships with keels laid from January 1 2016, marine engines must emit pollutants at levels no greater than 3.4g/kWhr.
These limits currently apply to the North American Emission Controlled Area (ECA) and were introduced in the North and Baltic Seas for vessels with keels laid from 1 January 2021. Companies selling marine two-stroke are working to ensure customers can easily and efficiently meet the latest standards.
To help it ensure its engines meet these strict emissions standards, the world’s largest producer of marine diesel engines has adopted the highly accurate ABB AZ10 Zirconia combustion oxygen analyzer.
To meet the stricter emissions limits, the engine manufacturer needed to ensure the efficiency of the Exhaust Gas Reduction (EGR) system used by its two-stroke engines. This takes a proportion of the exhaust and mixes it with carbon dioxide (CO2), feeding it back to the air inlet. With a higher heat capacity than oxygen (O2), the CO2 reduces the peak engine temperature, leading to a reduction in the formation of NOx.
In a series of experiments, the marine diesel engine manufacturer found that mixing the exhaust air with the inlet air can reduce the oxygen inlet percentage by roughly 3-6% percent, rather than natural air’s 21 percent, reduced NOx production by 85 percent.
For maximum emissions reduction, the key to managing this oxygen intake is highly accurate measurement. Beyond this the instrument also needed a low response time and the company were keen to find a solution which would reduce the use of expensive gases for calibration.
In comparisons between devices supplied by the major vendors, the ABB AZ10 achieved an accuracy better than ±0.05 percent of the actual O2 level.
The device’s use of low-drift sensor technology means that it experiences a drift of only 1.0 percent O2 per month, compared to other vendors’ drift of 2 percent O2 per month.
Savings on cost and calibration
As a further benefit, calibration of the AZ10 uses air rather than expensive calibration gases. ABB also provides a calibration certificate with every cell, meaning that the user doesn’t have to carry out any calibration. The optional auto-calibration unit also allows calibration to be performed manually or automatically.
Another useful feature is the on-board “Fuel Gauge”. This lifetime indicator gives the user advanced warning of the operational efficiency of the device, allowing time to schedule repair or replacement of the cell.
Featuring an easy cell release and site-serviceable probe, the AZ10 can be repaired quickly and easily on site with basic tools. The customer can replace the ABB sensor in a few minutes.
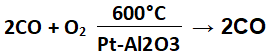
Oxygen Gas Probe The ABB AZ10 carries marine certification IACS E10 Rev. 5.0 2006 Test Specification for type approval and ABS certificate 15-LD1262098-PDA.