By mounting a conical twin-screw co-extruder on top of a parallel machine, battenfeld-cincinnati helped boost Decco’s output without expanding production space.
Business is booming for an extruder of door and window profiles in Poland. Decco supplies 350 customers in 30 countries, and it is constantly expanding its product portfolio supported by the addition of innovative profile systems to satisfy evolving customer tastes. The extruder, based in the northeast Polish city of Suwalki, has creativity to spare, but lacks sufficient floor space to pursue its ambitions. Extrusion system supplier battenfeld-cincinnati found a solution for Decco through a piggyback design. Plastic Door Panel Board Machine
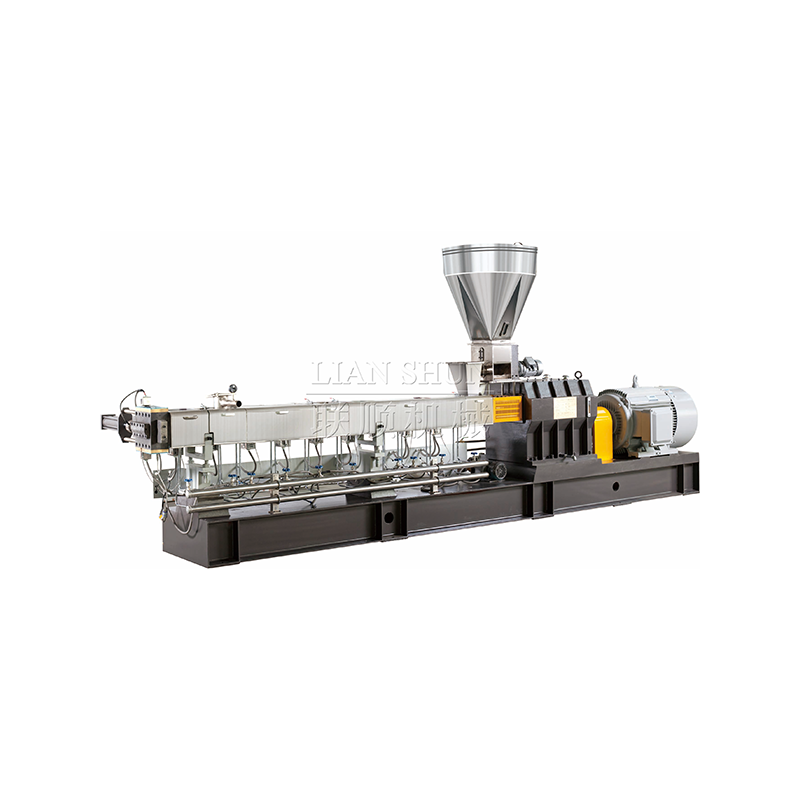
In a piggyback configuration, a conical twin-screw conEX NG 65 co-extruder, with up to 250 kg/h output, is mounted on top of the main twinEX 78-34 extruder, which reaches an output up to 290 kg/h. Floor space is required only for the twinEX extruder. In addition to saving space, the piggyback construction benefits from a common control cabinet and an energy-efficient design. Tooling integration is facilitated by the co-extruder’s flexible frame structure, said battenfeld-cincinnati.
Decco is a longtime customer, having worked continuously with Austrian-made extrusion systems since 2004. It took delivery of two piggybacked co-extrusion systems in 2019, and was so pleased with the result that it placed orders for several more machines. The space-saving design was not the only incentive.
“Just as important are the energy efficiency and performance of the two extruders, which guarantee economical manufacturing of high-quality profiles,” said Decco Managing Director Piotr Domaszewski in a press release distributed by battenfeld-cincinnati. The twinEX extruder’s 34 D processing length and optimized screw geometry are especially beneficial in high-output PVC processing. The Intracool screw-cooling system and in-barrel Air Power Cooling provide accurate temperature control and, thus, high melt and product quality. Part of the new NG generation, the conEX extruder is equipped with intelligent process technology that includes an extended preheating zone and optimized screw design to ensure high output rates with low shear input. In addition to minimal machine wear, the well-balanced ratio of mechanical and thermal energy input into the melt enables different materials to be processed with a single screw configuration.
Sustainability is a core concern at Decco, and the co-extrusion systems it is now acquiring will enable the production of multi-colored profile designs incorporating recycled material in the middle layer. In addition to its own production scraps, which Decco collects and shreds, the company also uses PVC regrind from third parties.
Decco currently runs 20 extrusion lines at its plant.
Editor in chief of PlasticsToday since 2015, Norbert Sparrow has more than 30 years of editorial experience in business-to-business media. He studied journalism at the Centre Universitaire d'Etudes du Journalisme in Strasbourg, France, where he earned a master's degree. Reach him at [email protected].
Shibaura Debuts Medical Molding Machine at Plastec West
Plastic or Paper? A Nuanced Sustainability Story
California Legislators Want to Ban Plastic Bags. Period.
BASF Pulls Out of Chinese JVs Over Uyghur Abuse Claims
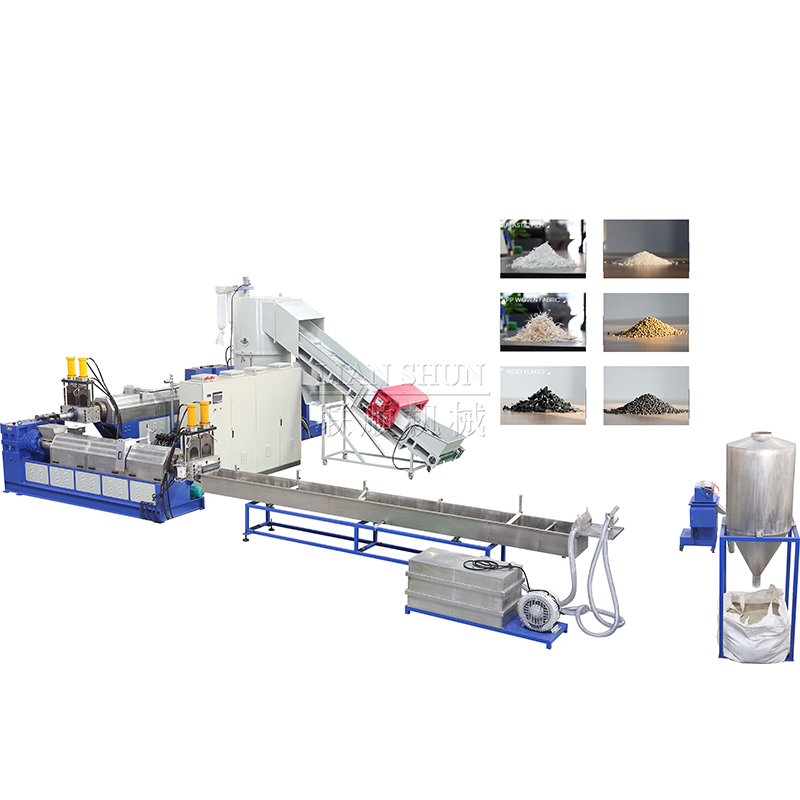
Hdpe Pipe Production Line Copyright © 2024 All rights reserved. Informa Markets, a trading division of Informa PLC.