Welcome to an insightful conversation with Ulla Tønnesen, President – DISA Industries
In this interview, we delve into the innovative world of green sand moulding, a compelling alternative to traditional gravity and low-pressure diecasting methods. Ulla will shed light on the environmental advantages, cost-effectiveness, and unique capabilities of DISA's green sand moulding technology, addressing its role in modern manufacturing and how it's shaping a more sustainable and efficient future in casting. Join us as we explore the depths of this transformative technology and its impact on the industry.” Green Sand In Foundry
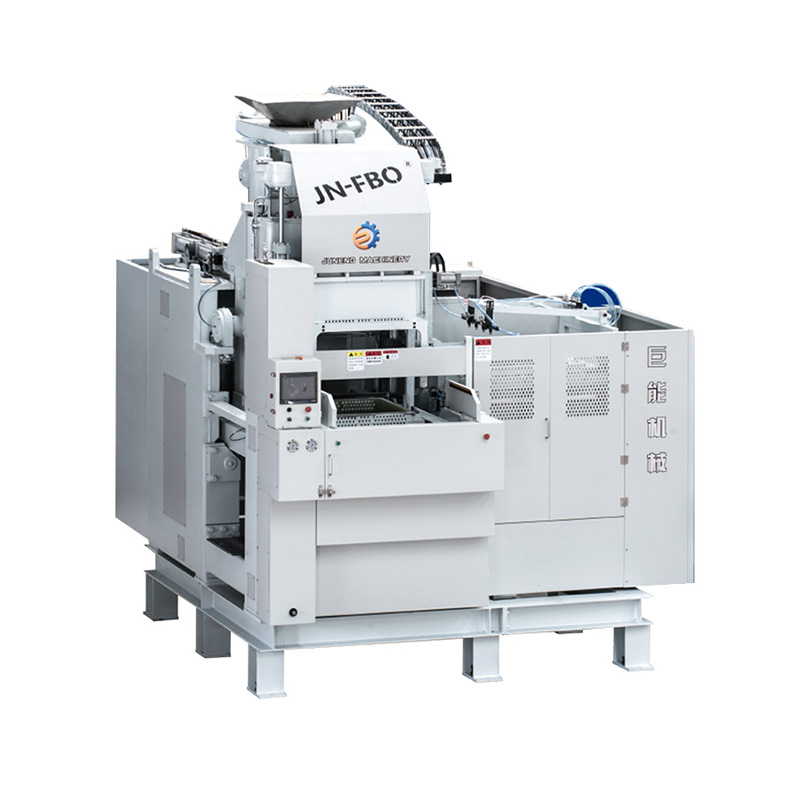
Can you elaborate on the environmental benefits of green sand moulding compared to traditional gravity and low-pressure diecasting processes?
Green sand moulding offers environmental benefits when compared to traditional gravity and low-pressure diecasting processes. Tools used on DISA machines can reach a lifetime up to 600.000 shots which means waste of tools are less compared to permanent mould techniques. Plus, the sand in green sand moulding is reused multiple times as only few percent new sand is added in each loop, reducing waste and the need for constant new material inputs.
How does the efficiency and cost-effectiveness of green sand moulding with DISA machines compare to conventional diecasting methods?
DISA Moulding technology stands out from permanent moulding in three key areas: productivity, tool costs, and flexibility.
Productivity: DISA moulding machines are capable of producing up to 555 moulds (shots) per hour, for aluminium applications typical speeds with modern dosing furnace technologies is up to 300 shots per hour. This means, a shot every 12 seconds. In many applications, more than 1 castings will be produced with 1 shot. Perfect fit for high volume castings.
Tool Costs: DISA moulding tools in most cases can be less expensive than permanent moulding tools, depending on the complexity of the casting. For instance, an LPDC/GDC tool costing €60,000 can be replaced with a DISA tool for just €15,000. Moreover, DISA tools have a much longer lifespan, up to 600,000 shots compared to 75,000 shots for LPDC/GDC tools. This translates to a total cost reduction of up to 32 times. And it is also important for prototyping. As the tooling is not getting direct contact with liquid aluminium but only with green sand, plaster and wooden tools can be used when only short series are needed for production of prototypes. Which can lead to tooling cost of € 10.000 or even less for prototyping.
Flexibility: Complete tool changing on DISA machines requires between 1 to 5 minutes. This is ultra-fast compared to other technologies which sometimes requires couple of hours or even a shift of production. DISA moulding machines are adaptable to both high-volume production and low- to medium-series production, making them a versatile solution for a wide range of casting needs.
In what ways does DISA's green sand moulding technology offer superior quality or unique capabilities compared to traditional diecasting?
Some die casting foundries assume casting quality and surface finish will generally be worse with green sand. Maybe they are thinking about old-fashioned techniques like floor moulding with rough sand where surface finish doesn’t really matter. We’re here to change that perception – because castings made by modern DISA equipment are a world away from that. I do think there’s still a myth in the market about green sand. People think it can’t produce aluminium castings to their specification. With DISA’s moulding technology, you get superb casting quality and excellent surface finish, with surface roughness’s down to 6.35µm Ra and 33.40µm Rz. We can meet demanding quality requirements – and still deliver a low casting cost.
This surface roughness is achieved with moulding sand adjusted for best surface quality and after shot blasting where the shot blast has been optimized for aluminium.
Could you discuss the adaptability of DISA machines in terms of different production volumes and types of foundry products?
It’s obviously superb for fast, high-volume production but it’s also frequently choice for jobbing foundries with short runs and lower volumes. Remember, tool changing on DISA takes 1 – 5 minutes only. Some of our customers are producing less than 100t annually and others more than 20,000t a year. With green sand, you are generally operating one line with one dosing furnace which keeps manpower requirements down. I think something else often overlooked is the fact that green sand is also great for core-intensive complex castings. DISA machines have fast and easy core handling, it’s a very well-developed technology.
Over many years, DISA moulding solutions have been associated with high-capacity foundries preferable used for production of high volume parts. However, DISA now also have moulding solutions available designed for foundries needing less capacity and high flexibility. This includes both the DISA MATCH moulding lines and the DISAMATIC C3 moulding lines.
How does DISA support its clients in transitioning from traditional diecasting methods to green sand moulding?
DISA has a robust application department comprising seasoned experts with extensive foundry experience, enabling us to provide comprehensive support to our customers throughout the entire process—from tool design to Magma simulations, from yield enhancement studies to scrap reduction initiatives, and complete foundry optimization. Additionally, I'd like to highlight our latest development, our R&D Test Foundry in Denmark. This facility empowers us to conduct production trials not limited to aluminium but also encompassing copper alloys, steel alloys, and iron alloys. Our commitment to our clients extends further as we're in the process of installing the advanced SIMPSON Pro Claim sand reclamation system. Sustainability comes first for Norican Group and this system will allow us to conduct thorough reclamation tests, further enhancing our ability to deliver valuable solutions to our planet.
Could you discuss which types of components or products are particularly well-suited for manufacturing with green sand moulding, and what makes them ideal candidates for this method?"
While DISA Green Sand is not universally applicable to all aluminium castings, it excels in producing castings with wall thicknesses more than 2.5 mm. Additionally, with the unique bottom filling dosing technology from Striko Westofen, mechanical properties can be optimized. For applications demanding high pressure tightness or castings with extensive core requirements, DISA Green Sand stands out as an attractive alternative. Its versatility extends across a wide production spectrum, from low volume runs to high-volume production.
Many aluminium castings are well suited for the green sand moulding process, this includes but is not limited to: Compressor housings, Electronic power boxes, Gear housings, Manifolds, Valves.
Email disa.industries(at)disagroup.com Web: www.disagroup.com
Yes, I would like to receive the bi-weekly Foundry-Planet newsletter with all latest news, product and material tests and reports. Plus the special newsletters – all can be cancelled anytime and at no cost.
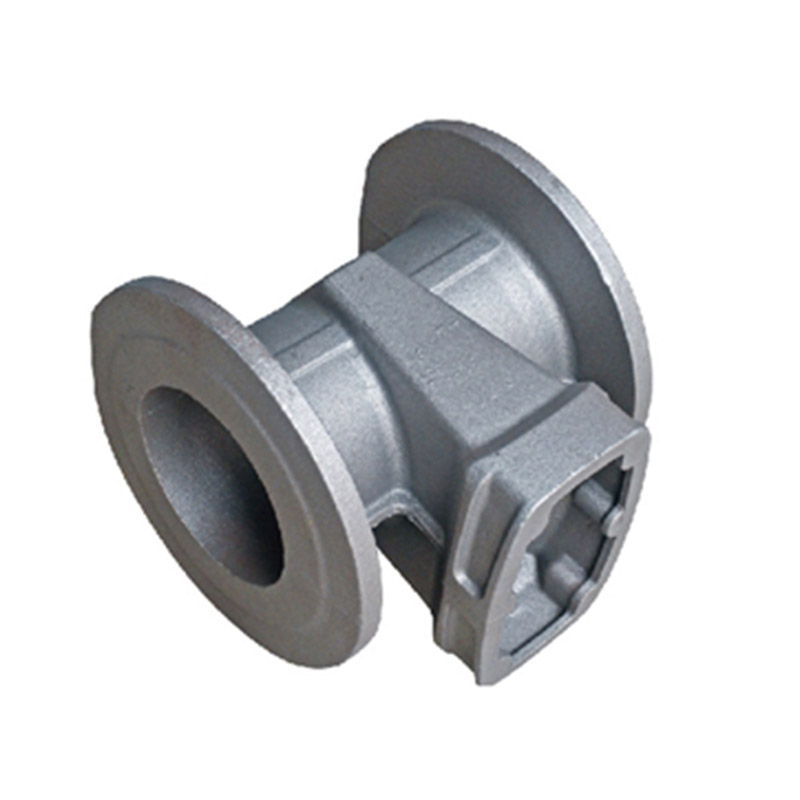
Fully Automatic Moulding Machine Check here our privacy policy.