For full functionality of this site it is necessary to enable JavaScript. Here are the instructions how to enable JavaScript in your web browser.
Save to read list Published by Jessica Casey, Editor LNG Industry, Thursday, 15 February 2024 14:00 Piston Air Compressor

Over the past 20 years, global consumption of natural gas linked to population growth and motivation for cleaner power sources has been steadily rising. LNG offers the capability to convert natural gas to higher energy concentration and transport its value to higher-demand markets where it can be stored and regasified for power generation, direct heating, industrial processes, and as a supplement to renewable power worldwide.
In 2019, LNG represented 9.8% of the global gas supply. This percentage will in-crease as the primary gas-producing areas develop greater LNG production capacity in order to capture higher market value for natural gas as a primary and supplemental means of power generation.
Converting natural gas to a liquid allows for the transport of greater energy content since LNG takes up about 1/600th the volume of natural gas. It can be pumped and transported using maritime vessels, highway trucks, and short liquid pipelines. For commercial use, LNG must be converted back into gaseous form at regasification plants at the receiving terminal where the LNG is delivered.
LNG production plants use a wide range of turbomachines including centrifugal compressors, gas and steam turbines, turboexpanders, and cryogenic pumps and ex-panders. Historically, LNG producers have adapted to advances in turbomachinery to maximise output. Additionally, producers have continued to gain efficiencies and cost improvements by considering variations to the refrigerant mixtures and cycle adaptations to convert natural gas to its liquefied form.
This article, based on a short course given at the 2023 Turbomachinery Symposium, reviews the LNG value chain, focusing on how compressors and pumps fit into the various LNG plant cycles. Part 1 includes production processes and compressor applications. Part 2 (coming in September 2024) will cover LNG pumping applications and equipment.
The LNG value chain includes the production, processing, and conversion of natural gas to LNG, transportation of the liquefied gas, and regasification as it travels from extraction to final delivery to end-users. The value chain includes:
The LNG value chain is relatively complex and requires many different types of turbomachinery to complete the thermodynamic processes required. It is fairly efficient, with most of the energy consumed by the liquefaction and transportation steps. Optimising the liquefaction process and employing energy recovery systems throughout the chain is important to maximising return on investment (ROI). A typical break-down of costs is shown in Figure 1.
Refrigeration is integral to the natural gas liquefaction process. Refrigeration cools the feed gas by heat exchangers between the warm feed gas and colder refrigerants. To generate the cold temperatures required for LNG production, work must be put into the cycle through compression, and heat must be rejected from the cycle via a heat exchanger. There are different types of proprietary refrigeration processes (cycles); the most common include reverse Brayton, interlinked single refrigerant cycle, mixed refrigerant, single mixed refrigerant, and dual mixed refrigerant. The operator selects the licensed process during the design and development of the LNG facility. A typical refrigeration cycle is shown in Figure 2.
Nitrogen is typically used as the refrigerant in the reverse Brayton process, but methane may also be used in this cycle. Propane, ethylene, or methane are the common choices of pure refrigerants. Mixed refrigerants are often a blend of hydrocarbons with nitrogen (Figure 3). The basic principle of using mixed refrigerants is to match as closely as possible the cooling/heating curves of the feed gas and the refrigerant, which results in a more efficient liquefaction process, requiring a lower power consumption per unit of LNG produced.
Liquefaction is one of the most expensive parts of the LNG value chain, and the turbomachinery that supports liquefaction is process critical. Capital investment and OPEX are the areas over which LNG operators have the most control, and they can optimise their development costs through process selection and capital equipment.
Raw natural gas varies in composition and contains contaminants such as water, carbon dioxide (CO2), and hydrogen sulfide (H2S). Processing removes the contaminants and adjusts the composition to meet specifications. If the gas is not transported via pipeline, it is typically liquefied for easy transportation and storage. Processing and the liquefaction process, as well as storage of natural gas, requires compressors. These compression services require different design features specific to the compressed fluid and operating conditions.
Whether raw gas is delivered to a pipeline or liquefied for transport or storage, some processing is required. Some common applications for compressors in a gas processing plant are shown in Figure 4.
If the pressure in the gas reservoir or pipeline is too low to pass through the processing plant, a feed gas or booster compressor is used to increase the pressure. Raw gas composition can vary greatly. Major constituents would be 68 – 99% methane, 0.2 – 14% ethane, 0 – 9% propane and butane, 0.5 – 18% nitrogen, 0.1 – 2% CO2, and water vapour. H2S may also be present. Materials need to be selected to resist corrosion from acid gases H2S and wet CO2.
The first processing step is to remove liquid oil and water from the raw gas. Gas is ‘flashed’ from a hydrocarbon liquid when the liquid flows from a higher pressure to a lower pressure separator or to a stabiliser column where the light ends (methane, ethane, some propane, and butane) are removed. The gas from the column overhead is compressed and returned to the feed stream. Flash gas compressors typically handle low flow rates and produce high compression ratios. These may be reciprocating, screw-type, or barrel-type centrifugal compressors. For centrifugal compressors, the variable mole weight of the feed gas and variable flow rates require variable speed control and/or a need to recycle flow around the unit.
The next step is ‘sweetening’ or the removal of acid gases, followed by dehydration. The acid gases are removed by either amine treatment (scrubbing) or membrane separation. The membrane process may require gas recompression due to large pressure drops. A solid desiccant dehydrator or molecular sieve typically uses a slip-stream of the dried gas to drive off the adsorbed water and regenerate the desiccant. This may be a small, barrel-type centrifugal compressor or a single-stage, integrally geared design.
Enjoyed what you've read so far? Read the full article and the rest of the February issue of LNG Industry by registering today for free!
Read the article online at: https://www.lngindustry.com/special-reports/15022024/turbomachinery-in-lng-production-plants-part-one/
Avenir LNG Ltd has entered into a shipbuilding contract with Nantong CIMC Sinopacific Offshore & Engineering Co. Ltd for two 20 000 m3 LNG bunker and supply vessels.
Embed article link: (copy the HTML code below):
This article has been tagged under the following:
LNG project news US LNG news Natural gas news
This content is available to registered readers of our magazine only. Please sign in or register for free.
Register for free » Get started now for absolutely FREE, no credit card required.
Already a member? Sign in here
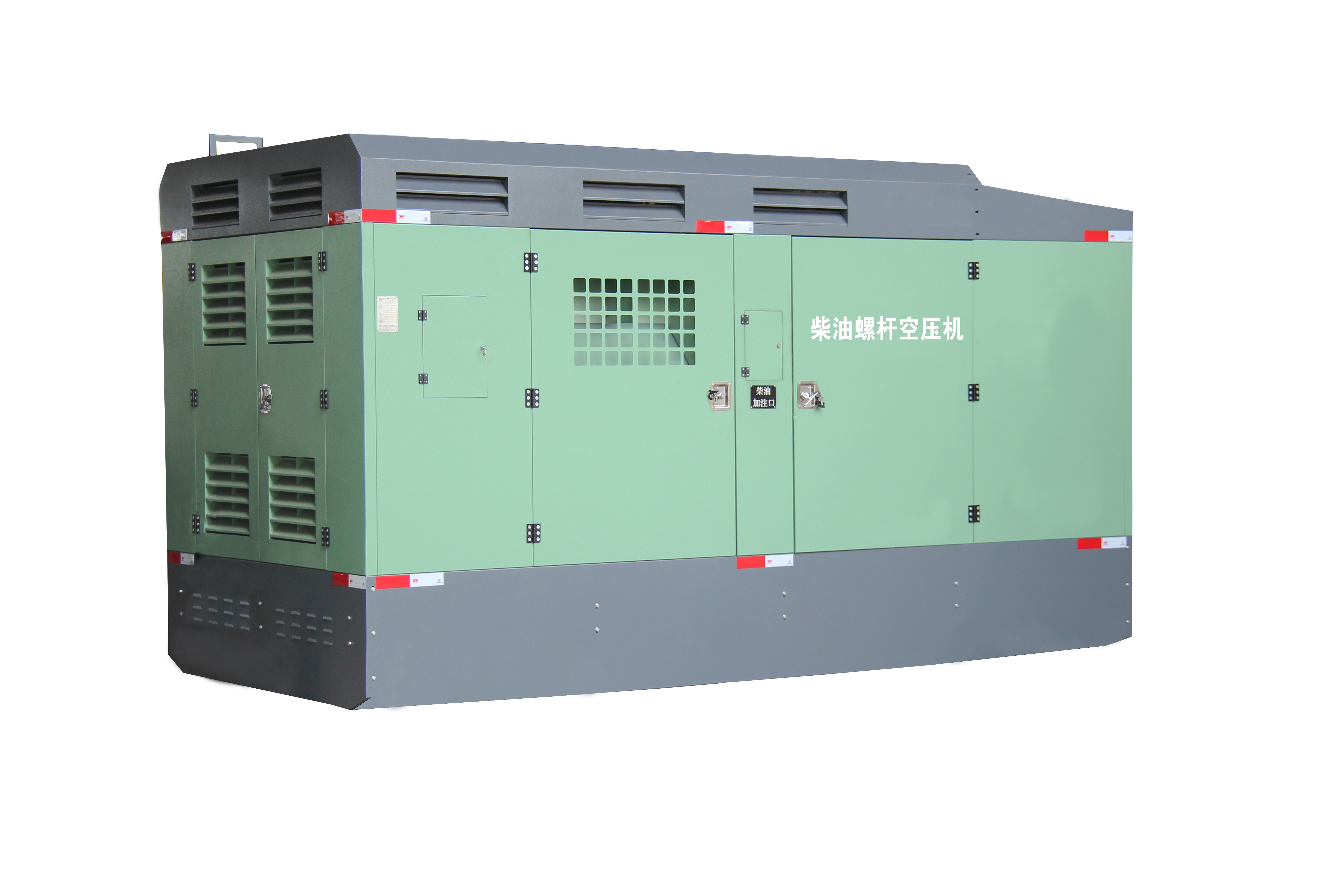
High Pressure Air Compresso Copyright © 2024 Palladian Publications Ltd. All rights reserved | Tel: +44 (0)1252 718 999 | Email: enquiries@lngindustry.com