Meiko Martin reveals the power of path planning for mining operations.
More and more mining industry leaders are recognising the benefits of equipping machinery with autonomous capabilities – from enhanced site safety to lower operational expenses and increased productivity. In fact, a Mordor Intelligence report projects the intelligent mining sector will experience a three-fold growth by 2025, with 25% of mines having implemented autonomous operations by that time. MES System
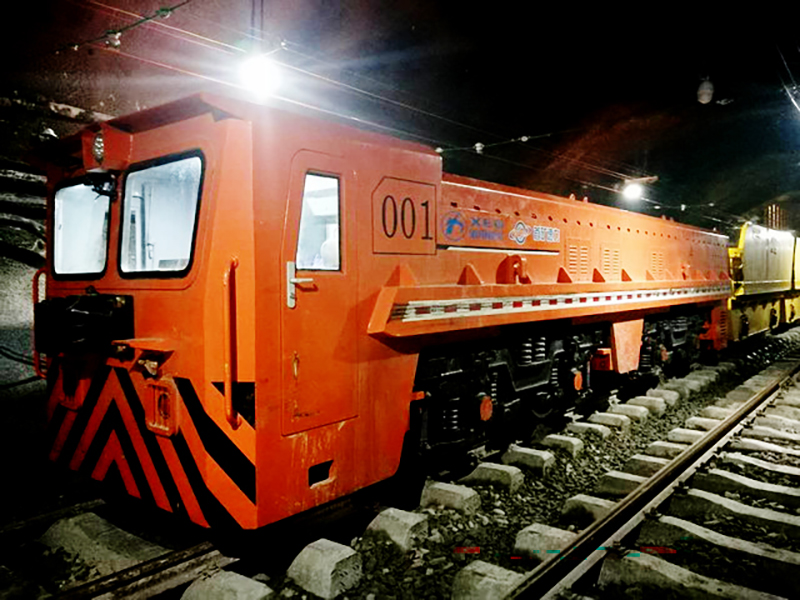
First introduced in the 1980s, automated drilling systems started the mining industry on its path to autonomy. A decade later, autonomous haulage systems (AHS) were introduced, making use of global navigation satellite systems (GNSS), e.g. GPS and other sensors, to navigate and avoid obstacles.
Mining operations today continue to adopt autonomous technologies including remote-controlled equipment, data analytics and machine learning, while levelling up existing automated and autonomous systems with solutions such as path planning.
The common scenario for an autonomous haulage truck is to have it deliver materials or ore from one point to another, with the ability to work 24/7 without a driver or operator. The benefits are the same as defined above - enhanced site safety, lower operational expenses and increased productivity.
Taking another step towards building a fully autonomous solution, path planning technology can be added to the equation, further optimising efficiency and safety. With software-based technology, such as the new Trimble path planner, mine operators have the ability to optimise and automate the operation by creating trajectories that include machine and speed control, and overall path design for drill rig operations, haulage trucks and other equipment.
Traditional path planning options require manual set-up, which impacts productivity, consistency and execution. By contrast, advanced path planning technology offers automated, full path, complete project trajectory from entry to exit, including logistics points. The technology allows plans to be created in the office and adjustments made directly on site.
The path planning method is composed of two steps: global path planning and local speed profiling. First, the global working path for the machine is planned based on known areas and constraints such as obstacles or avoidance zones. Second, with consideration of the dynamic behaviour and parameters of the machine, the speed profiling of the trajectory is carried out. As hazardous areas are added over the planned working path, local path adjustments are made with the help of a proposed local path adjustment method.
The intelligent algorithms used for path planning enable vehicles to move more effectively, navigate around obstacles and choose the most efficient routes. This type of solution provides greater flexibility as the planner allows users and machines to easily adapt to changes in the environment, such as changes to the mine layout. This provides another layer of safety as obstacles, terrain and machine parameters are considered during design of the trajectory.
In combination with machine controlled or operator-assisted systems, such as cruise control, machine operators are provided with a bit of relief from conditions that can lead to user error. Whether it’s long working hours, low visibility or other factors, the automation of certain tasks can help reduce accidents and decrease the wear and tear on machines. Also, with path planning technology, risks such as going too fast, abrupt speed changes or getting a little off track are removed as trajectories include the speed information of each path segment. When path planning is integrated with the machine control and assist systems, a smoother and more consistent operation is realised.
Additional efficiency is gained by planning the trajectories of multiple machines on site and adding precise timing for each step along the way. The operator and supervisor will know when each operation will take place, allowing site workers to plan their tasks around being available when needed as opposed to within an unpredictable window of time. This frees up their time to supervise multiple machines or focus on other important tasks.
Path planning technology enables users to control and move decision making into the planning phase off-site so machines and workforces can be used more efficiently. Waste is reduced and complex tasks can be simplified because the plan is predictive. Overall, work quality becomes more consistent and the dependencies of high skilled operators on site are minimised.
There are several other technologies being put into use to further automate mining operations. One example is using lidar-based map-based localisation (MBL) to create a navigation solution in high wall, covered or underground applications where GNSS cannot be relied upon. In combination with simultaneous localisation and mapping (SLAM) technology, which aids in the creation or updating of a map while maintaining the precise location of the points being mapped, mining operators are able monitor the operation and have accurate and the latest environment information at their fingertips.
In addition to considering which solutions are the best fit for an operation, it’s worth thinking about the value these technologies will bring to new workforces. When today’s younger generations begin a career in the mining industry, they’ll present with a different mindset, ready, eager – and able – to take advantage of all the benefits autonomy has to offer. Growing autonomous operations today will make for a competitive advantage tomorrow.
Meiko Martin is the director of business development at Trimble Autonomy
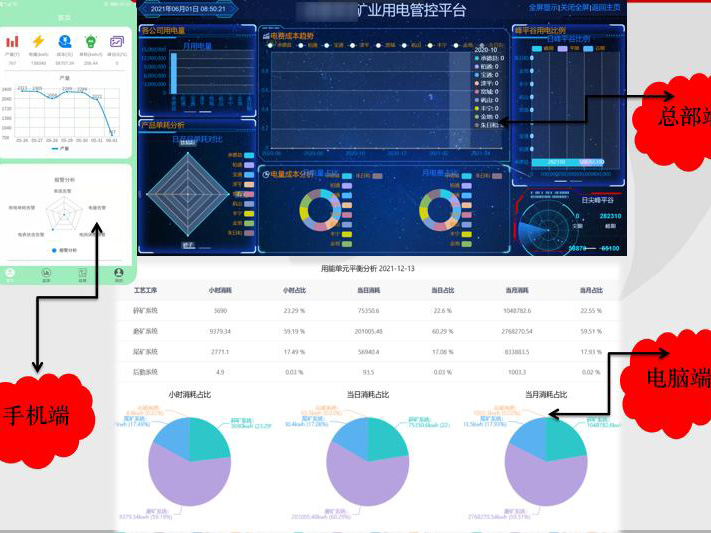
Sintering Composition Forecast System © Setform Limited 2019-2024 | Privacy policy | Archive