Since the publication in 1962 of Silent Spring, Rachel Carson’s landmark exposé of the devastation wreaked by pesticides on nature and human health, concerns about our impact on the environment have continued to grow. Now, as the effects of climate change are becoming increasingly apparent, companies are seeking more opportunities to reduce their carbon footprint. They’re looking at everything—including their forklift fleets.
And while reducing forklifts’ environmental impact may not be on most fleet managers’ to-do list, there are good reasons to make it a priority. Those reasons, some of which are voluntary and some of which are not, include considerations like the following: Yellow Grease Price
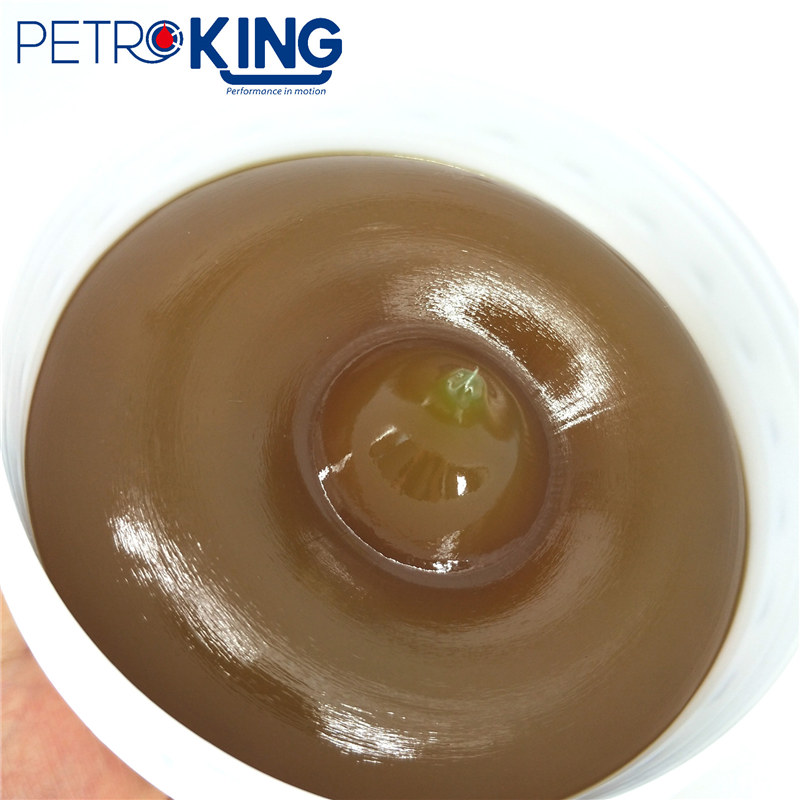
On the voluntary side of the ledger, there’s the simple desire to do the right thing for the planet. It’s not hard to draw a line from that lofty aspiration to the warehouse floor. Forklifts with internal combustion engines (ICEs) emit greenhouse gases, such as carbon dioxide, carbon monoxide, sulfur dioxide, and nitrous oxide, as well as particulates, which vary depending on the fuel source. Battery-powered electric forklifts may not produce such emissions, but hazardous byproducts, such as hydrogen gassing and acid spills while charging or watering lead-acid batteries, can harm the environment while posing safety risks to forklift operators.
Also voluntary: saving money. In many cases, sustainable options offer greater efficiency with lower financial risk than traditional approaches, and thus are more cost-effective in the long term, says Environmental Health and Safety Engineer Paige Johnson of Toyota Material Handling. For example, compared to ICE equipment, electric trucks, which do not directly produce greenhouse gas emissions, usually have higher upfront costs but a lower total cost of ownership over the equipment’s life, according to the experts we consulted. Furthermore, electricity tends to be less expensive and have more predictable pricing than fossil fuels, which are more affected by market volatility, says Paul West, senior manager, dealer sales, for UniCarriers, a division of Mitsubishi Logisnext Americas.
Some governments and utilities offer financial incentives for fleets that reduce their energy consumption or switch to low- or no-carbon energy sources like electricity and hydrogen. These incentives usually take the form of rebates, rate reductions (such as for charging during off-peak hours), or tax credits. California, Washington, Oregon, and British Columbia have adopted or are in the process of adopting an additional method: a Low Carbon Fuel Standard (LCFS) program that provides credits for using low- or no-carbon energy sources and financially penalizes companies that use high-carbon fuels to power their transportation equipment.
What financial incentives are available, who is eligible for them, and how to apply for them varies from state to state. James Nielson, senior business product manager, motive power and electrification, for Yale Lift Truck Technologies, describes the incentive picture as “dynamic” and constantly changing. Accordingly, “your lift truck dealer probably is the best resource for information about local incentives,” he says.
Forklift fleets that are subject to federal, state, and local regulations that mandate limits on emissions will have no choice when it comes to greening up their operations. The California Air Resources Board (CARB), for example, has proposed a regulation that would prohibit the purchase, sale, or lease of most new ICE forklifts in the state by 2026, and fleets would have to phase out their existing ICE trucks, based on model year, beginning in 2028. The state’s ultimate goal is to eliminate carbon emissions from forklifts, with exceptions for applications where zero-emission trucks are technically infeasible.
Regulation may come from unexpected directions. Damon Hosmer, general manager, energy storage solutions for The Raymond Corp., notes that the U.S. Securities and Exchange Commission (SEC) has proposed a rule that would require companies that register with the agency to periodically disclose information about climate-related risk that could have a material impact on their business. The proposed disclosures include the volume of greenhouse gases the company’s operations emit—a requirement that will likely encompass forklifts.
In addition to striving to be a good corporate citizen and the need to comply with regulations, another compelling motivation is the importance of satisfying customers’ requirements and expectations. Johnson observes that many companies are “feeling pressure both internally and externally to set aggressive goals and targets” for environmental, social, and governance (ESG) initiatives.
Forklift OEMs are seeing this trend firsthand. Brandon Bullard, vice president of sales and marketing at Clark Material Handling Co., reports “quite an increase in demand from customers” for information, not only about specific environmental impacts but also about the company’s policies and processes for improving sustainability in everything from product design and manufacturing to waste disposal.
One reason for the growing interest in suppliers’ sustainability practices is that more companies are leaning on their suppliers to help offset their own supply chain’s environmental impact. In Hosmer’s experience, many of those discussions are at the board level, which suggests that compliance is on top executives’ radar. Some big companies are not asking suppliers to trim their carbon footprint—they are requiring it. Yale’s Nielson tells of a big-box retailer that was looking to reduce its Scope 3 emissions (defined by the United Nations as emissions from assets that are not controlled by the reporting organization) and required a food-processing supplier to reduce its emissions companywide—a mandate that affected the supplier’s warehouse operations.
Reducing a forklift fleet’s environmental impact is a long-term project. The experts we consulted recommended some practical steps to get you started on the path to a cleaner, greener forklift fleet. What follows are some of their suggestions:
How much difference does switching to electric or hydrogen power actually make? A 2023 research project at the Massachusetts Institute of Technology’s Center for Transportation & Logistics calculated that, compared to propane-powered equipment, a fleet of nine electric forklifts in one of the warehouses studied would eliminate 17 tons of CO2 per vehicle per year, and a fleet of 16 electric trucks in another warehouse with a somewhat different operating profile would save 22 tons per vehicle per year. The same number of hydrogen-powered forklifts in those facilities would eliminate 24 tons and 30 tons, respectively.
One of the biggest barriers to adopting battery-powered trucks has been their inability to perform as well as IC trucks in tough applications. That’s quickly changing, though, and electrics are now an option for some applications where, until recently, they couldn’t compete. UniCarriers, for example, offers a line of indoor/outdoor electric forklifts with long run times that West says are suitable for “the majority of businesses, even demanding applications like lumberyards and construction” where it might be difficult to reach charging stations. Hyster offers heavy-duty forklifts featuring integrated 350-volt lithium-ion batteries and lift capacities ranging from 23,000 to 36,000 pounds. The company says these big trucks perform as well as diesel equipment in the applications they’re designed for—capabilities that weren’t available just two years ago, says Herman Klaus, Hyster Co.’s director, application solutions, big trucks. That’s a big win for the environment, he says: “Every gallon of diesel you don’t burn … means 22 pounds less CO2 in the atmosphere.”
It’s worth noting that the Propane Education & Research Council (PERC) in 2022 commissioned a research study that compared emissions from propane forklifts to emissions from vehicles utilizing other power sources. The study examined greenhouse gas emissions, hydrocarbons, and pollutant emissions including sulfur oxide (SOx) and nitrogen oxide (NOx). According to PERC, the study found that modern propane-powered forklifts reduce SOx emissions by up to 76% compared with electric forklifts powered by the electric grid (which itself produces pollutants as it generates electricity), emit 97% less NOx compared with diesel forklifts, and produce 97% less hydrocarbon emissions compared with diesel forklifts.
There are other ways fleets with IC engines can do their part. Because lower fuel consumption means lower emissions, several of the experts we consulted emphasized the importance of keeping up to date with scheduled maintenance to ensure engines use fuel efficiently. Something as simple as maintaining correct tire pressure may reduce fuel consumption by 10% to 15%. Even the way operators use the hydraulic function can make a difference. “To increase the speed of the hydraulic functions in an IC truck, you have to rev up the engine by applying more gas, which produces … more emissions,” West says.
Idling, which produces harmful gas and particulate emissions without getting any work done, is another important target. Some reasons operators let their ICE trucks idle include preventing diesel engines’ turbochargers from cooling off, keeping the operator’s compartment warm while working outdoors in cold weather, and ensuring the forklift will be available the moment a load is ready, Klaus says. He recommends looking for ways to improve efficiency so long waits won’t be necessary; even a small change benefits the environment and saves money by conserving fuel. Or consider installing a device that shuts off the engine after a certain amount of time, Klaus says, although he acknowledges that this tactic won’t work for everybody.
Charging lithium-ion batteries is more efficient and makes less demand on the electrical grid than lead-acid battery charging does, says Trevor Bonifas, general manager, motive power, for Crown Equipment Corp. But because lithium batteries charge very quickly, he notes, “you’re getting more productivity and more work done out on the floor, so you’re charging more frequently.” In some circumstances, then, those trucks may be consuming more kilowatt-hours of electricity than ones with a lead-acid battery. That’s why it’s important to understand that choosing the most efficient battery may depend on the application and its specific requirements.
Some models that were designed specifically for lithium-ion batteries have another advantage when it comes to power consumption. Yale’s Nielson explains that lithium-ion batteries weigh less and take up less space than lead-acid batteries, which allows for a smaller, lighter truck. One of his company’s new lithium-ion trucks “is about a half-ton lighter and up to 18% more efficient” than the base model with lead-acid—with no reduction in lifting capacity, he says.
Another way to reduce electricity consumption is to operate electric forklifts with regenerative braking and lowering, which feeds valuable power back into the battery. This design, coupled with lithium-ion batteries, extends the truck’s range on each charge, which means less need to draw electricity from the grid, Hosmer says.
One more option you might not have thought of: solar power. Raymond’s Energy Storage Solutions group is working with a New York state agency to test whether electricity generated by a rooftop solar array and stored in efficient, large-scale batteries can reliably power forklifts without drawing electricity from the grid. And solar can pay off in more ways than one: Companies that generate their own electricity often can sell their surplus back to the local utility, making some extra money by going green.
Experienced hands say that sometimes less-than-obvious steps can help to extend the life of consumables. Hosmer notes that driving a truck at 6 mph instead of 7 mph not only reduces wear on the drive motor but could also prolong battery life by up to 1.5 years in certain circumstances. And Hyster’s Klaus observes that, while OEMs typically recommend changing the hydraulic oil used in masts every 3,000 hours, it’s often possible to get many more hours of life through regular monitoring and sampling for cleanliness and filtration for chemical contamination.
When forklifts’ efficiency declines or maintenance costs get too high, they can be reassigned to lighter duty. They can also be sold back to the dealer, which will refurbish and resell them as used equipment, UniCarriers’ West says. When it’s no longer safe or economically beneficial to operate a truck on its second or third life, it can be sold for steel scrap and recycled.
Lead-acid batteries are highly recyclable, and protocols for safe recycling have been in place for decades. Your local dealer or battery vendor are good sources of information and assistance. The lithium-ion battery recycling infrastructure, on the other hand, is not fully developed yet. The largest component of the battery is the steel counterweight, which is easily recycled, and the computer boards inside can be recycled the same way as computers. Recycling, though, doesn’t always mean taking the battery apart: Lithium-ion batteries’ long useful life means that batteries in forklifts coming off three- to five-year leases often can be refurbished for use in other applications.
If you’re weighing whether it’s worth spending time and effort on reducing your forklift fleet’s environmental impact but aren’t yet sure, it may help to consider an initiative’s potential contribution in a broader context. Any sustainability effort should be looked at as supporting “an ecosystem that is predicated on everything functioning together in balance,” Hosmer says. “It’s not just about individual pieces of capital equipment.”
Johnson adds that a successful sustainability effort requires support and commitment from multiple levels and people within a company. In her view, organizations that set environmental targets “will have to lean on each other and navigate together” as they seek improvements. She’s optimistic that will increasingly become the norm. “We are seeing a culture shift toward caring about sustainability,” she says. “More people and companies now recognize it’s the right thing to do.”

Diesel Engine Oil Ch-4 Copyright ©2024. All Rights ReservedDesign, CMS, Hosting & Web Development :: ePublishing