Coatings separate heat from light
Thin-film dichroic coatings can separate light from excess thermal energy, minimizing heat-related performance degradation. Cold Mirrors

Temperature-sensitive materials and processes play an important role in many electro-optics applications. Entertainment lighting, medicine, optical communication, ultraviolet (UV) curing, and fiberoptics are all areas in which control of unwanted heat energy is important. Excess heat can degrade the performance of electro-optical systems, affecting both electronic and optical performance. Thin-film dichroic coatings, or filters, can provide a solution by separating harmful excess heat from the desired light (see Fig. 1). These coatings are deposited on various substrates to filter the heat safely out of the sensitive optical system, leaving the selected cool light energy to perform its function. Such filters may be subjected to harsh environments, but the advent of ion-assisted deposition (IAD) has made them robust and stable.
Heat-absorbing filters provide relatively good transmission at visible wavelengths and have very good infrared (IR)-wavelength rejection. In many current new applications this absorbing property, combined with the relatively high thermal expansion of the filters, has posed design challenges.
When using an absorptive filter with a high-energy system it is important to displace the energy absorbed by the filter. A common way to do this is to pass cool air across the filter and then channel the heated air out of the system. If a system has a high degree of focused energy, however, even air-cooling can not prevent the inevitable failure of the filter. Another disadvantage of the IR-absorbing filter glass is that it is not color neutral.
Dielectric heat filters are made by depositing alternating layers of high- and low-refractive index materials onto a substrate in a vacuum chamber. Although there are several different ways to deposit these films, electron-beam deposition is the most common--a stream of electrons heats up and evaporates the coating materials onto substrates at the top of the deposition chamber. Substrate temperatures during electron-beam deposition vary depending on who is coating them, but they generally run at about 300°C. With ion-assisted deposition, these temperatures can be reduced considerably with consequent improvement in the quality of the deposited films. By bombarding the films with high-energy ions during the deposition process, IAD increases the refractive index of the evaporated films and reduces the porosity of the film. This greatly increases the stability and durability of the coating. The number and thickness of individual layers will vary, depending on the wavelength to be reflected.
The efficiency and durability of the heat filter is determined by many different variables, the major ones being the optical and thermal properties of the coating materials. Ideally these materials would have little or no absorption, which would help reduce heating of individual layers during a high-temperature application and reduce coating stress. Managing such stress is important. As each additional layer is deposited onto the substrate the coating film develops greater stress, which limits the number of layers that can be deposited and hence reduces the width of the blocking band and the percentage of energy reflected across that band. When designing a multiple-layer dielectric hot mirror filter for white light, therefore, one must maximize both the visible-wavelength transmission and the infrared reflection. The opposite is true for a cold mirror. Hot mirrors generally operate at low angles of incidence while cold mirrors generally operate at a 45° angle of incidence.
Depending on the light source, a combination of absorbing filter glass and reflective dielectric coatings can be useful. The limited blocking range of dielectric filters means that absorptive filters may still be required for some applications. The dielectric hot-mirror filter is coated onto a substrate with a relatively low thermal expansion, such as borosilicate or fused silica. This filter can then be placed close to the source in order to reflect the near-IR energy. The reflected band would be typically from 750 to 1200 nm, and about 90%-95%
mirror is not an absorptive filter,
stand more energy than an absorptive
An absorptive filter can be placed further down the optical path to block the longer-wavelength energy. Sometimes the hot mirror may even be coated directly onto the absorptive filter glass. When coating directly onto the absorptive filter, the orientation of the coated surface relative to the light source become very important. The hot mirror must be oriented toward the light source to protect the absorbing filter glass from the near-IR energy. The dielectric hot mirror/IR-absorbing filter combination can withstand much more heat than an IR-absorbing filter alone, but because of the thermal expansion of the substrate the combination is still limited to energies well below that of the hot mirror on borosilicate or fused silica.
A common use for a dielectric hot mirror on IR-filter glass is for night-vision displays. In this case the dielectric filter provides the required sharp cutoff at a given wavelength in the upper visible spectrum and the IR-absorbing filter provides additional out-of-band IR blocking. Infrared-absorbing glass is ideal for this application because its IR-blocking properties do not fluctuate with the changing viewing angle of an operator.
Heat filters and plastic optics
The number of applications for plastic optics is growing. Acrylic fiberoptics, for example, are commonly used as white-light illuminators. To increase the luminous output of these illuminators, manufacturers must increase the efficiency of their heat filters.
When an acrylic fiber overheats it starts to darken and absorb an increasing amount of energy including visible light. Once the fiber begins to darken, its useful life span rapidly decreases. Excessive IR or ultraviolet (UV) energy or a combination of both can initiate this failure. When designing an illuminator made with plastic fiber, therefore, it is important to know the spectral output of the light source. Equally important is knowing the absorption bands of the fiber in order to choose the correct heat filters. The acrylic fiber we measured has a considerable amount of absorption below 375 nm and above 1000 nm. In fact the fiber is completely absorptive above 1620 nm (see Fig. 2).
With a xenon arc lamp or a metal halide light source, a standard hot mirror that reflects energy between 750 and 1200 nm is typically used. If the lamp has a considerable amount of UV output, the hot mirror could be combined with a UV blocker that would cut off the energy below 400 nm. If fiber burn is still a problem, an extended hot mirror that blocks the IR radiation out to1600 nm might solve the problem.
With a tungsten quartz halogen bulb source, the standard hot mirror or the extended hot mirror would reflect only a fraction of the IR spectrum of the lamp. Unlike a xenon or metal halide arc lamp, the tungsten halogen lamp has a significant output beyond 1600 nm. So for an illuminator designed from scratch with a tungsten source, a 45° cold mirror could be incorporated. A cold mirror reflects about 95% of the desired white light and transmits an average of 90% of the IR energy above 750 nm. Depending on the coating materials, the cold mirror may also pass a considerable percentage of the UV energy out of the system.
For retrofitting an existing illuminator when a cold mirror cannot be incorporated, an extended hot mirror or a combination of hot mirror and IR-absorbing filter glass can be used. With a reflective hot mirror perpendicular to the light path, a cold-coated reflector must be added to dissipate the infrared energy. A hot mirror placed directly in front of a bulb without a cold-coated reflector will overheat the bulb and reduce its life. If a cold-coated reflector is not available, some other method of cooling the lamp compartment will be required (see Fig. 3).
Heat filters for UV applications
Hot and cold mirrors are frequently used for UV curing. The mercury (Hg) line at 365 nm is commonly used. If an application requires a narrow band of energy, it is simple to design a 45° cold mirror to dissipate any unwanted energy. A cold mirror is preferred because it minimizes the number of layers required to achieve a good ratio between the desired and the undesired energy. This coating can be designed with about twenty layers and can provide more then 99% reflection at 365 nm and 90% average transmission in the visible and infrared spectrums.
Ultraviolet curing applications can also use a broad band of wavelengths. Some UV curing inks require a range of wavelengths from 220 to 440 nm in order to cure quickly. Many coating materials available for coating in this range have rather low indexes. Therefore, the number of layers required to reflect this broad range is increased, which increases the cost of the filter. A simple hot mirror on a fused silica substrate may prove to be a less expensive solution. A UV-pass hot mirror can pass 80% of the UV light while reflecting about 75% of the energy between 800 and 1100 nm (see Fig. 4).
As the demand for plastic optics and other heat-sensitive components increases so does the need for more-robust and efficient filters. Infrared-absorbing filter glass and dielectric heat filters provide many different solutions for separating the desired light from its destructive components, but it is important to remember that these filters only redirect and distribute the energy. Only a well-designed system will dissipate the energy from the heat-sensitive components. Understanding the thermal properties of all the individual components will help with the design of a cool system, reducing cost and frustration levels. o
FIGURE 1. Intensity distribution of a 4000-W metal halide light source shows the need for a hot mirror that reflects much of the energy output between 750 and 1200 nm.
FIGURE 2. Absorption characteristics of an acrylic fiber determine the appropriate choice of heat filters required to prevent overheating of the fiber and consequent optical damage. In this case the fiber shows significant absorption below 375 nm and above 1000 nm and is completely absorptive above 1620 nm.
FIGURE 3. Hot mirrors reduce transmission of energy at infrared wavelengths, while maximizing transmission at visible wavelengths. An extended hot
mirror blocks a wider range of infrared wavelengths.
FIGURE 4. Ultraviolet hot mirror reduces transmission of light at wavelengths between 800 and 1100 nm (infrared), while allowing about 80% of the light at shorter wavelengths (to about 250 nm) to pass.
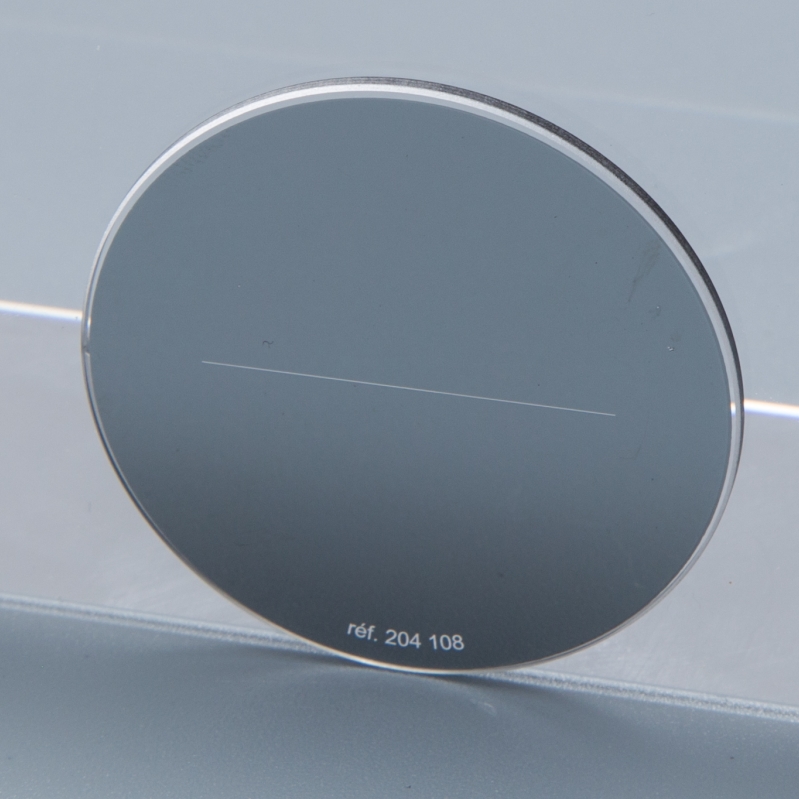
Types Of Curved Mirror ROBERT CABRERA is coatings manager at ZC&R Coatings for Optics, 1250 East 223rd St., Carson, CA 90743; e-mail: [email protected].