Manufacturing is an energy-intensive activity. The U.S. government estimates that manufacturing consumes about one third of the energy used in the country, stated Scott Hibbard, vice president of technology for Bosch Rexroth Corp., Hoffman Estates, Ill., in his paper “Six keys to sustainable manufacturing.”
“By far, the majority of [the consumption] is motors,” Hibbard told Cutting Tool Engineering. Lincoln Electric Power Feed 10m
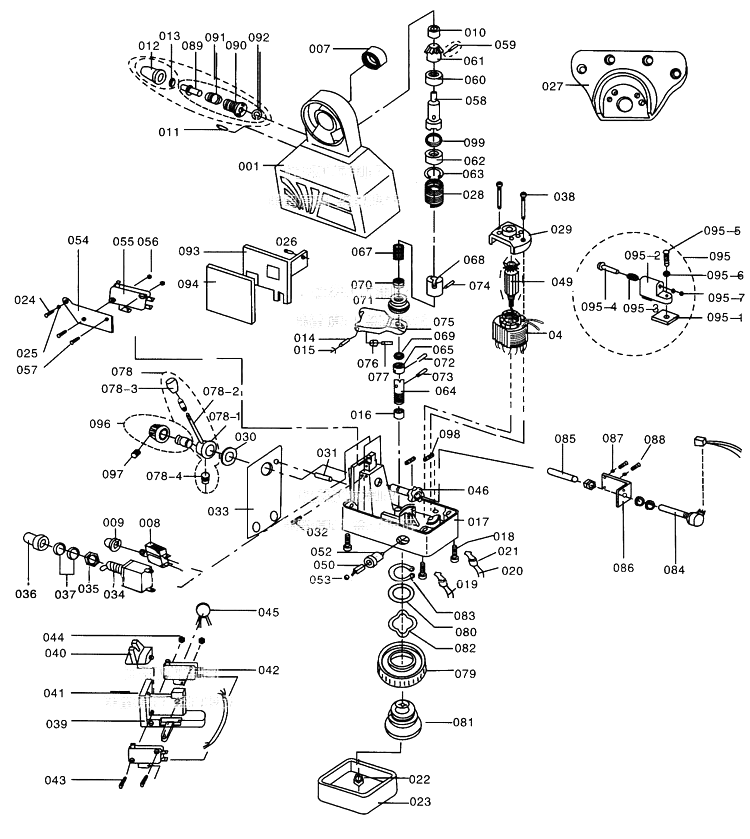
Reducing the amount of energy the motors on a metalcutting machine tool use is one way for a parts manufacturer to increase its competitiveness—or even to just remain an ongoing concern—while “greening” its operations. “Even before the economic downturn, I heard from people who make machine tools that their customers were telling them, ‘Power prices are driving me out of business and you have to find ways to cut energy use,’ ” said David Dornfeld, a professor of engineering at the University of California at Berkeley, whose research includes environmentally conscious manufacturing. “The point is you shouldn’t be [reducing energy consumption] like giving to a charity because it makes you feel good. You should be able to make some money off of this.”
According to Hibbard, a method to reduce a machine tool’s energy consumption is to replace a single-speed motor with a variable-speed or servo drive. Traditionally, variable-speed drives were used only when an end user needed a motor that operated at different speeds in an application and servodrives only when there was a high-precision requirement, such as specific acceleration or CNC positioning. “It was always thought of as way too expensive to use those,” he said. “In many applications, you can throttle down the motor with a variable-speed drive to consume less energy, especially if you’re wasting energy with friction and turning it into heat. For every dollar increase in a barrel of oil, the payback comes sooner.”
Cutting energy consumption and therefore cost is a win-win situation in today’s metalcutting environment.
He added that instead of wasting that energy, it can be reused within a plant similar to how a hybrid vehicle’s regenerative braking system helps charge the battery pack when the vehicle brakes or decelerates. “On machines that have a lot of accelerations and decelerations, a scheme was devised to take that energy coming back, rechop it into AC and return it to a three-phase line—the main line,” Hibbard explained. The energy is returned from the drive when, for example, a spindle or any axis drive decelerates and can either be stored within the plant or used to power other energy-consuming equipment. “We’re going from consuming to producing,” he said. “We’re feeding energy out and selling it back to the power company.”
That scenario isn’t possible on a single-speed motor that’s not controlled by a drive because the electronics are not present to retrieve the energy.
Larger machines with a 12,000- to 15,000-rpm spindle are already likely to have such a system in place because they have more power returned when the spindle brakes. Smaller machines may not have used it, but that may be changing as the price of energy rises, and companies are pressured to consume less energy from the power grid.
Hibbard described the equipment needed to reuse energy as “basically a power bridge. In other words, another set of semiconductors similar to the ones used to control the speed of the motor, except this second bridge is now rechopping and reassembling the power to match the frequency and phasing of the power lines supplying voltage to the machine.”
Another energy-saving option is to not return energy to the main line but to use a shared-bus or common power supply drive system to reconsume regenerated power within the machine by analyzing and tuning the machining cycle to make the best use of the energy. That might involve accelerating one motor while another is decelerating.
Although cycle analysis tools are commercially available to achieve the highest efficiency, end users can save energy without them. “Some of it you can eyeball,” Hibbard said. “The easiest way to do it is to set up a machine, run it, record axes acceleration, current and velocities and then look at where the energy is being consumed,” he said. Energy might be saved, for example, by slightly altering the tool change cycle so the spindle is decelerating at the same time the Z-axis is accelerating toward the tool magazine.
Hibbard noted that the energy reduction process generally begins with hiring a consultant, but simple, no-cost steps can be taken. “Turn the darn thing off when you’re not using it,” he said. “But you’ll also find that most vendors of the energy-consuming devices in the machine have some good input on what can be done to reduce energy, either with the existing equipment they have or what the payback would be in altering equipment that’s on the machine. People shouldn’t think they have to go out and spend thousands of dollars to start saving energy. They can start with what they have on their floor right now.”
Machine tool selection also provides an avenue for reducing energy consumption. Compared to building and machining with a stand-alone lathe and a stand-alone milling machine, a multitask machine can require less energy, according to Dornfeld. “A machine that combines turning, drilling and milling in one machine gives you reasonable or substantial energy savings in both the use of space as well as what went into making and operating the machine itself,” he said. “That’s not even if you include the floor space reduction and the energy it takes to makes that floor space and heat, cool and light it.”
Dornfeld said the semiconductor industry is an example of a manufacturing sector that realizes the advantage of achieving more performance from each square foot of fabrication space because of the complex and costly processes for producing semiconductors. “Some of those ideas, presented to more conventional manufacturing, have a lot of opportunity,” he said.
In every phase of a machine life cycle there will be different options to undertaking energy-efficiency measures. The most effective way is to consider these during the concept and modernization phases.
A dual-spindle machining center is another type of machine tool that improves energy efficiency by machining two identical workpieces simultaneously, according to STAMA America, Itasca, Ill. The machine builder stated that its Twin-Spindle two-spindle machining center uses only 20 percent more power than a single-spindle machine but lowers energy consumption by 40 percent per finished part, and its STAMA-Twin2 four-spindle machine reduces power use by 60 percent compared to single-spindle production.
STAMA reported that the energy savings can reach 80 percent when the machines are operated in “ECO-Mode,” realizing a saving in energy costs up to about $1,800 per year per machining center. In that standby mode, when the machine isn’t in production the peripheral units and feed axes can be shut down sequentially in phases, and the machine can be activated immediately by pushing the start button.
A self-reactivation system is also integrated into STAMA machining centers. With that, for example, users can set coolant equipment to a cyclic intermix of coolant water on the weekend’s nonproductive hours without having the full machine on power. “We can shut down the machine but the program will call up a different machine cycle to, say, activate a coolant pump to cycle coolant intermittently during the plant shutdown so it doesn’t get rancid,” said Michael Herman, STAMA’s director of sales.
To further reduce energy demand, the braking energy during deceleration is fed back to other components on a STAMA multiple-spindle machine via electrical drives. The machine’s internal energy management system uses the energy gained from braking systems and feeds that power back to the peripheral units, such as the hydraulic pump and air suction unit. STAMA noted that the machine will use this energy and not feedback or supply the public electrical network with energy.
In addition, a multiple-spindle machine doesn’t require extra floor space. “The footprint of a twin-spindle machine is as big as the footprint of a single-spindle machine,” Herman said. He noted that the company’s Twin-Spindle machining centers are suitable for production runs of 100,000 to a million pieces, depending on cycle time.
It’s important to consider the cost per square unit of floor space when selecting a machine tool and justifying its purchase. However, that is less of an issue for U.S. manufacturers because of the relative availability of open space for factories. “In Europe, they have it detailed down to the square meter what the rental is and what the power cost and consumption is,” Herman said.
A machine conserves energy when it isn’t making chips, but profitability comes from maximizing the amount of a machine’s metalcutting time. Therefore, reducing cycle time is another method for reducing power use, and one way to achieve that is by machining at a high spindle speed. “In terms of energy use per unit of material removed,” Dornfeld said, “high-speed machining looks much more efficient because you have constant power and variable power.”
Variable power is based on the chip load being taken during machining, and constant power is for running a machine tool’s peripherals. “Constant power is often greater than the power you use for cutting metal,” Dornfeld said. “In a sense, the less time you cut the more power you save. So high-speed machining looks quite good from not just the point of view of productivity, but it saves you energy.”
The work zone of a Twin-Spindle machining center from STAMA America. The machine tool builder reports that two-spindle machining lowers energy cost by about 40 percent.
Koji Ishiura, assistant sales manager for Kitamura Machinery of USA Inc., Wheeling, Ill., concurred. “Longer cycle times consume more power,” he said. To reduce cycle times, the machine tool builder says it offers machines with a box way construction for high metal-removal rates and with twin ballscrews and twin motors on each axis for faster acceleration and deceleration, especially on large horizontal machining centers. “It’s not twice as fast,” Ishiura said, “but maybe 20 to 30 percent faster than a single ballscrew.”
Whether it’s reducing energy consumption, recycling materials or minimizing consumables, “green” and “sustainable” manufacturing are often lumped together, but Dornfeld emphasized the need to distinguish between the two. He noted that sustainability has three legs: the capital requirements for assessing business investments, the impact machine operation has on the environment (which includes energy consumption and recycling) and the social impact, which is hardest to determine.
“The definition of sustainability is you shouldn’t do anything that limits the opportunities or reduces the livelihood or quality of life of someone in the future,” Dornfeld said, adding that how manufacturing fits into that definition is difficult to define. “What I’ve started to focus on is how to make manufacturing processes as green as possible. It’s certainly in our best interest to make these processes as green as possible and to have them contribute to sustainable development as much as possible.” CTE
About the Author: Alan Richter is editor of Cutting Tool Engineering, having joined the publication in 2000. Contact him at (847) 714-0175 or alanr@jwr.com.
A diagram of a gear-driven spindle from Kitamura Machinery.
Machine tool users can save energy by considering gear-driven spindles when selecting a machine tool. According to Kitamura Machinery of USA Inc., its gear-driven spindles allow Kitamura to use the appropriate-size spindle motor and save 40 to 50 percent in kilowatt hours compared to more commonly used direct-drive or integral spindles.
To achieve the same cutting capacity as a gear-driven spindle, direct-drive and integral spindles use a higher-horsepower motor, which consumes more power. By stepping through gears, Kitamura says its machining centers can generate high torque at low speeds for roughing, and run at high speeds for finishing.
With three high and three low gears, the company’s gear-driven spindles are typically powered by 18-hp motors to create 116.1 ft.-lbs. of torque. That compares with 23.6 ft.-lbs. of torque for a 30-hp motor driving a 20,000-rpm integral spindle from another machine builder, according to Kitamura’s Koji Ishiura. “In the U.S., manufacturers cannot cut labor much so they have to cut their costs somewhere else,” he said. “One place is power consumption.”
In recognition of the energy efficiency of gear-driven spindles, in 2000 Kitamura received the 20th Japan Industrial Machining Union Award from the Japan Machinery Federation in the category of “best energy saving technology.”
Bosch Rexroth Corp. (800) REXROTH www.boschrexroth-us.com
David Dornfeld University of California at Berkeley dornfeld@berkeley.com
Kitamura Machinery of USA Inc. (847) 520-7755 www.kitamura-machinery.com
STAMA America (630) 233-8101 www.stama-america.com
Cone-shaped pins that support a workpiece by one or two ends during machining. The centers fit into holes drilled in the workpiece ends. Centers that turn with the workpiece are called “live” centers; those that do not are called “dead” centers.
Microprocessor-based controller dedicated to a machine tool that permits the creation or modification of parts. Programmed numerical control activates the machine’s servos and spindle drives and controls the various machining operations. See DNC, direct numerical control; NC, numerical control.
Fluid that reduces temperature buildup at the tool/workpiece interface during machining. Normally takes the form of a liquid such as soluble or chemical mixtures (semisynthetic, synthetic) but can be pressurized air or other gas. Because of water’s ability to absorb great quantities of heat, it is widely used as a coolant and vehicle for various cutting compounds, with the water-to-compound ratio varying with the machining task. See cutting fluid; semisynthetic cutting fluid; soluble-oil cutting fluid; synthetic cutting fluid.
Rate of change of position of the tool as a whole, relative to the workpiece while cutting.
Machining with several cutters mounted on a single arbor, generally for simultaneous cutting.
Turning machine capable of sawing, milling, grinding, gear-cutting, drilling, reaming, boring, threading, facing, chamfering, grooving, knurling, spinning, parting, necking, taper-cutting, and cam- and eccentric-cutting, as well as step- and straight-turning. Comes in a variety of forms, ranging from manual to semiautomatic to fully automatic, with major types being engine lathes, turning and contouring lathes, turret lathes and numerical-control lathes. The engine lathe consists of a headstock and spindle, tailstock, bed, carriage (complete with apron) and cross slides. Features include gear- (speed) and feed-selector levers, toolpost, compound rest, lead screw and reversing lead screw, threading dial and rapid-traverse lever. Special lathe types include through-the-spindle, camshaft and crankshaft, brake drum and rotor, spinning and gun-barrel machines. Toolroom and bench lathes are used for precision work; the former for tool-and-die work and similar tasks, the latter for small workpieces (instruments, watches), normally without a power feed. Models are typically designated according to their “swing,” or the largest-diameter workpiece that can be rotated; bed length, or the distance between centers; and horsepower generated. See turning machine.
CNC machine tool capable of drilling, reaming, tapping, milling and boring. Normally comes with an automatic toolchanger. See automatic toolchanger.
Any machining process used to part metal or other material or give a workpiece a new configuration. Conventionally applies to machining operations in which a cutting tool mechanically removes material in the form of chips; applies to any process in which metal or material is removed to create new shapes. See metalforming.
Machining operation in which metal or other material is removed by applying power to a rotating cutter. In vertical milling, the cutting tool is mounted vertically on the spindle. In horizontal milling, the cutting tool is mounted horizontally, either directly on the spindle or on an arbor. Horizontal milling is further broken down into conventional milling, where the cutter rotates opposite the direction of feed, or “up” into the workpiece; and climb milling, where the cutter rotates in the direction of feed, or “down” into the workpiece. Milling operations include plane or surface milling, endmilling, facemilling, angle milling, form milling and profiling.
Runs endmills and arbor-mounted milling cutters. Features include a head with a spindle that drives the cutters; a column, knee and table that provide motion in the three Cartesian axes; and a base that supports the components and houses the cutting-fluid pump and reservoir. The work is mounted on the table and fed into the rotating cutter or endmill to accomplish the milling steps; vertical milling machines also feed endmills into the work by means of a spindle-mounted quill. Models range from small manual machines to big bed-type and duplex mills. All take one of three basic forms: vertical, horizontal or convertible horizontal/vertical. Vertical machines may be knee-type (the table is mounted on a knee that can be elevated) or bed-type (the table is securely supported and only moves horizontally). In general, horizontal machines are bigger and more powerful, while vertical machines are lighter but more versatile and easier to set up and operate.
Workpiece is held in a chuck, mounted on a face plate or secured between centers and rotated while a cutting tool, normally a single-point tool, is fed into it along its periphery or across its end or face. Takes the form of straight turning (cutting along the periphery of the workpiece); taper turning (creating a taper); step turning (turning different-size diameters on the same work); chamfering (beveling an edge or shoulder); facing (cutting on an end); turning threads (usually external but can be internal); roughing (high-volume metal removal); and finishing (final light cuts). Performed on lathes, turning centers, chucking machines, automatic screw machines and similar machines.
Alan holds a bachelor’s degree in journalism from Southern Illinois University Carbondale. Including his 20 years at CTE, Alan has more than 30 years of trade journalism experience.
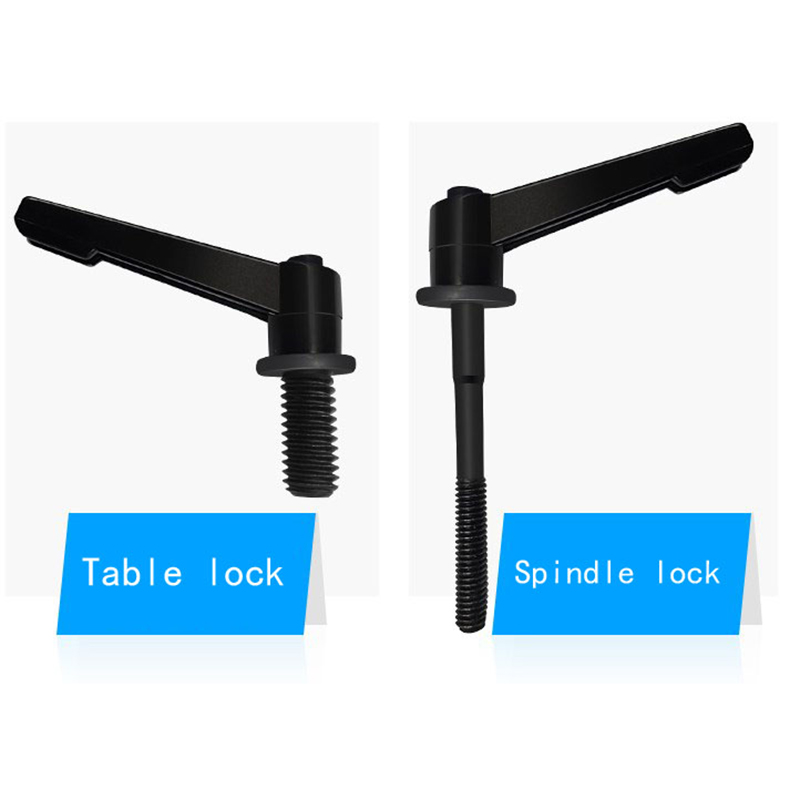
Small Power Feeder © Copyright 1995 - 2024. Cutting Tool Engineering. All rights reserved.