A car will often receive tiny, unpublished changes for each year of its model run. Automakers will slightly reprofile a bracket, improve a part that has a chance of failure, or simply figure out a way to make it cheaper. In the case of the 2024 model year Toyota GR Corolla, nothing much has changed except for a few peculiarities: Some new bolts, a pair of air ducts, and improved aerodynamics from four strips of specially designed aluminum tape.
In a video posted by pro drifter Ken Gushi chronicling his installation of the 2024 model year parts on his 2023 GR Corolla, the tape stands out as a particularly strange upgrade. The parts come in a 2024 upgrade kit, which includes new rear subframe bolts, new steering rack bolts, new air ducts for the air curtains, and the aforementioned strips of tape. Monel 400/600/718/725 Steel Plate
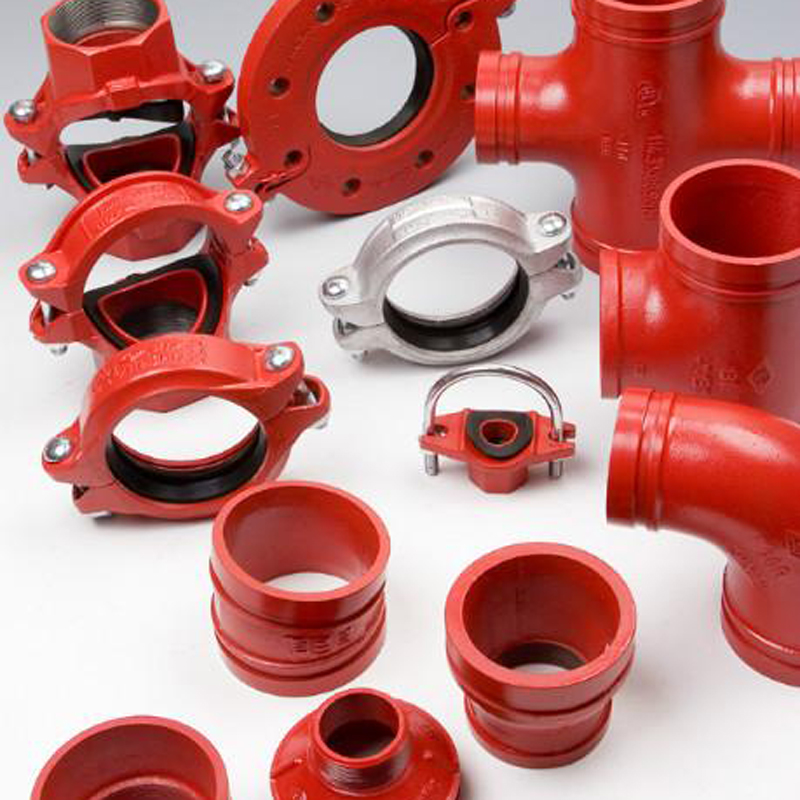
You might think that the tape would help seal an air duct or reinforce a particularly flexible part, but it actually manages electrostatic discharge. The idea, which is patented by Toyota, is that a car develops a positive charge while driving, and the air surrounding it is also positively charged. Two positively charged things repel one another, thus the airflow surrounding the car gets disturbed.
According to Car Watch, the idea has been around since the mid-2010s and was originally tested on the Toyota 86. During the development of the facelifted 86, Toyota engineers started noticing inconsistent behavior from test cars, specifically when the material for the bumpers was changed from prototype-spec to production-spec. This led to the study of electrostatic discharge, and the subsequent discovery that aluminum tape rectifies the problem and also magically improves aerodynamics.
Gushi says he felt a difference in how his Corolla drove after the upgrades. It’s hard not to say oh, really, but it’s just as hard to make a judgment without a proper apples-to-apples test. It’s certainly a minuscule change, but serial car modders will know that the smallest changes often make the biggest difference. Perhaps it’s time to start smacking aluminum tape onto all of our project cars.
More On The GR Corolla
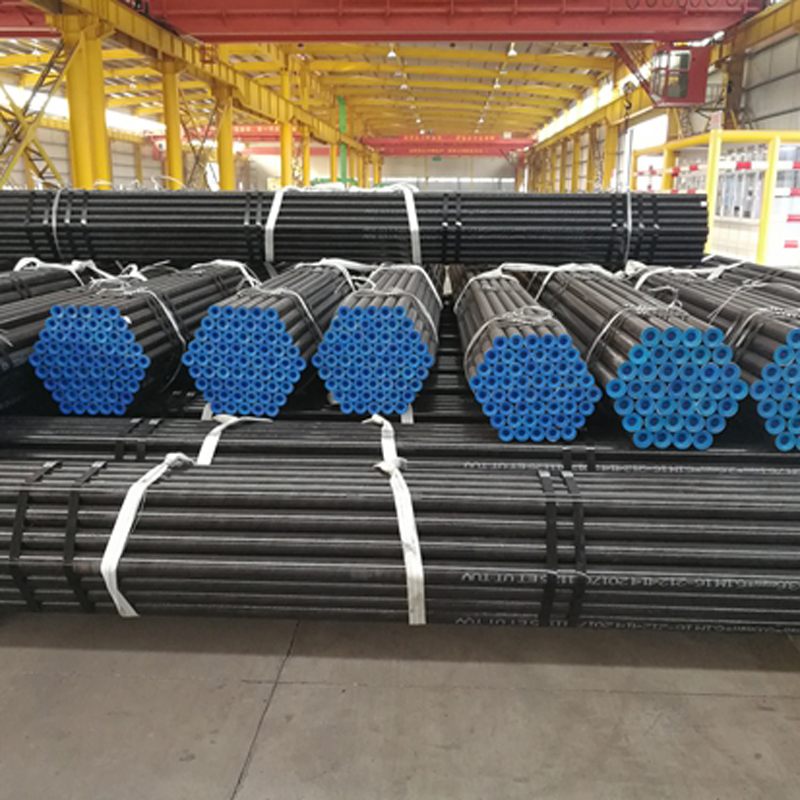
Copper Strips Get upfront price offers on local inventory.