Roll forming lines can be configured in two ways to create length-specific formed parts. One method is pre-cutting, which involves cutting the steel coil before it enters the roll former. The other method is post-cutting, where a profiled shear cuts the sheet after it is formed. Both methods have their advantages, and the choice depends on specific factors related to your production requirements.
With advancements in technology, both pre-cut and post-cut lines have become highly effective and efficient configurations for roll forming. The integration of servos and closed loop controls has revolutionized post-cut flying shears, providing them with increased speed and accuracy. Moreover, anti-flare fixtures can now be controlled by servos, allowing a pre-cut line to achieve comparable flare tolerances to a post-cut line. In fact, some roll forming lines are equipped with both pre-cut and post-cut shears, and with the help of advanced control features, the entry shear can make the final cut of the order, eliminating the scrap that has traditionally been associated with post-cut lines. This technological progress has truly transformed the roll forming industry, making it more efficient and sustainable than ever before. Steel Sheet Roll Forming Machine
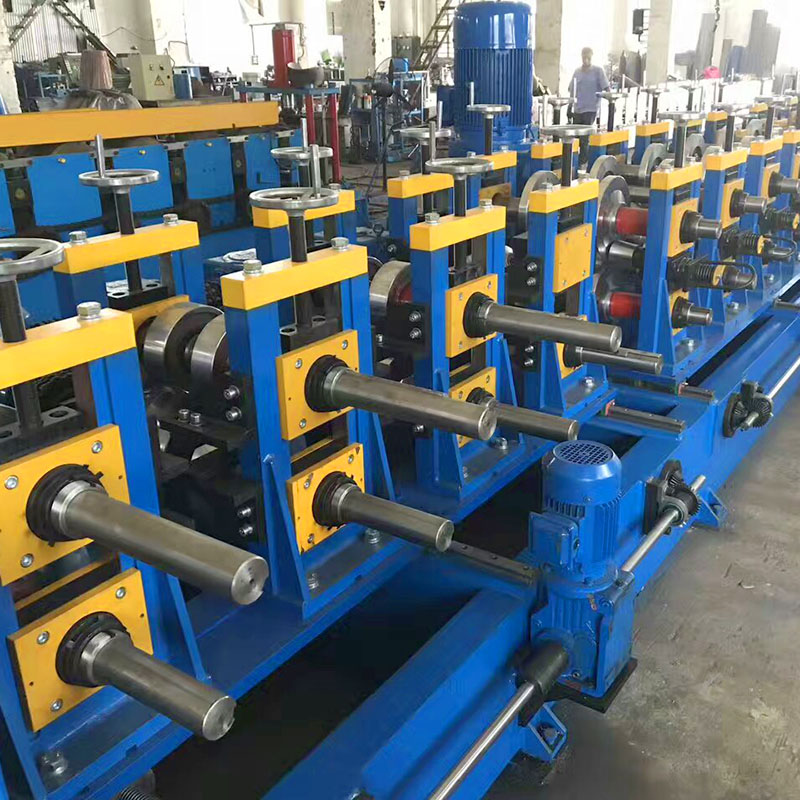
The companies of the Bradbury Group are known for the cutting-edge technology and reliability built into every product – and for the exceptional service that helps satisfy customers worldwide. Bradbury strives to set the standard for automated production and systems integration in the metal processing industry. Bradbury believes its leveling, cutoff, punch, folding and roll forming machines and automated systems set the highest standard for productivity, reliability and safety in coil processing.
You must have JavaScript enabled to enjoy a limited number of articles over the next 30 days.
Copyright ©2024. All Rights Reserved BNP Media.
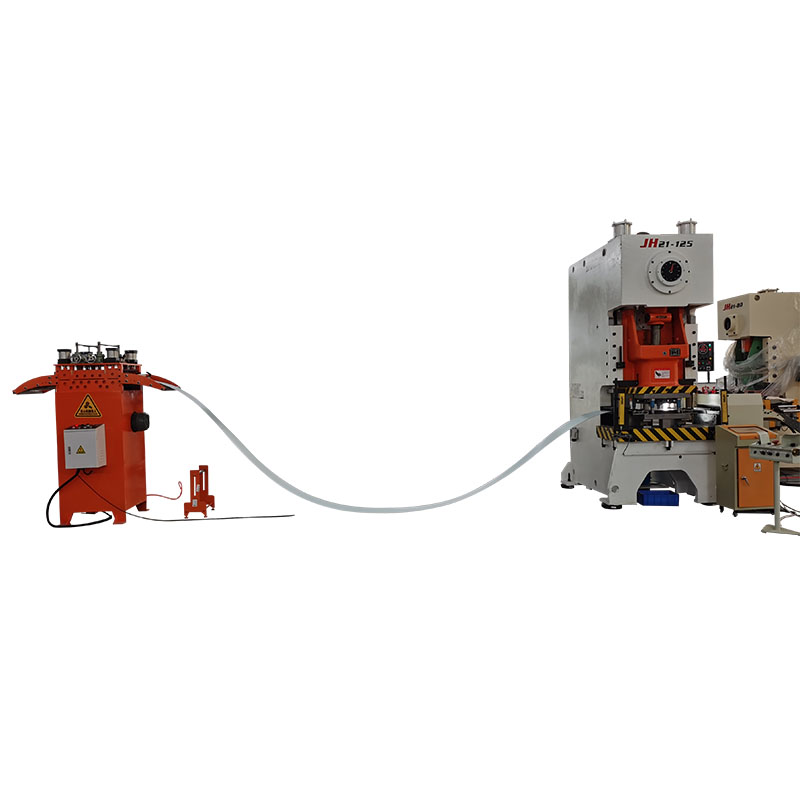
Steel Frame Making Machinery Design, CMS, Hosting & Web Development :: ePublishing