www.offshore-mag.com is using a security service for protection against online attacks. The service requires full cookie support in order to view this website.
Please enable cookies on your browser and try again. DTH Bit PDC Cutter Dome PDC 1608

www.offshore-mag.com is using a security service for protection against online attacks. The service requires full JavaScript support in order to view this website.
Please enable JavaScript on your browser and try again.
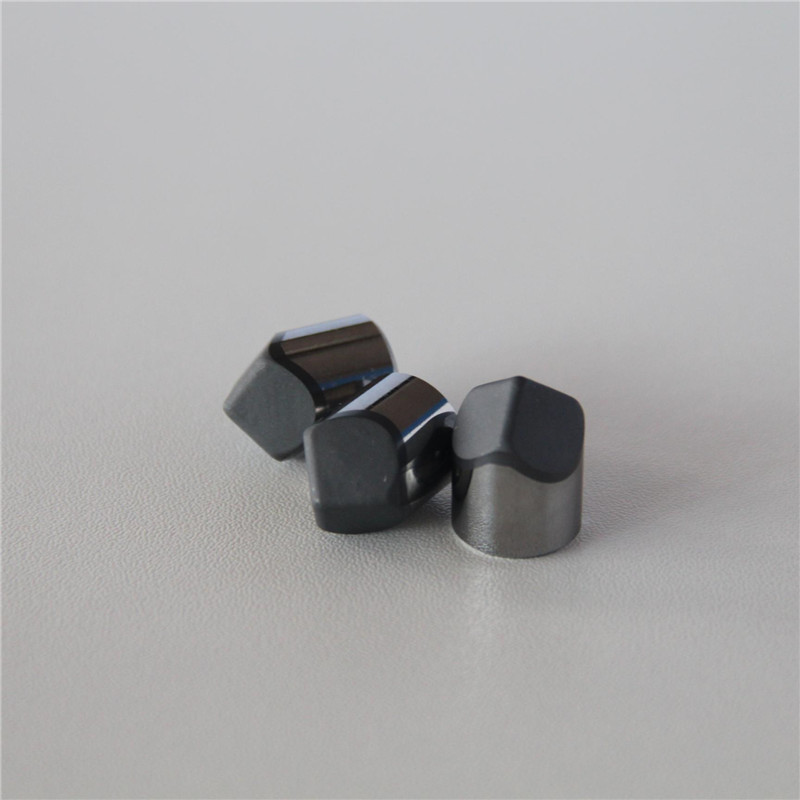
Leached Diamond Tool Cutting 1308 www.offshore-mag.com is using a security service for protection against online attacks. This process is automatic. You will be redirected once the validation is complete.