With K1 PACE, Husqvarna takes a big step forward and offers customers a high-power battery cutter that can handle heavy-duty jobs. This is the first product to be launched on the company's new battery system, PACE.
The first product to be launched on Husqvarna's battery system, PACE, t he K1 PACE high-power battery cutter was designed to handle heavy-duty jobs. Husqvarna tells c ontractors to expect power and performance equivalent to gasoline-powered cutters, with the additional benefits battery powered equipment brings to both operators and the environment. Carbide Bandsaw Blade
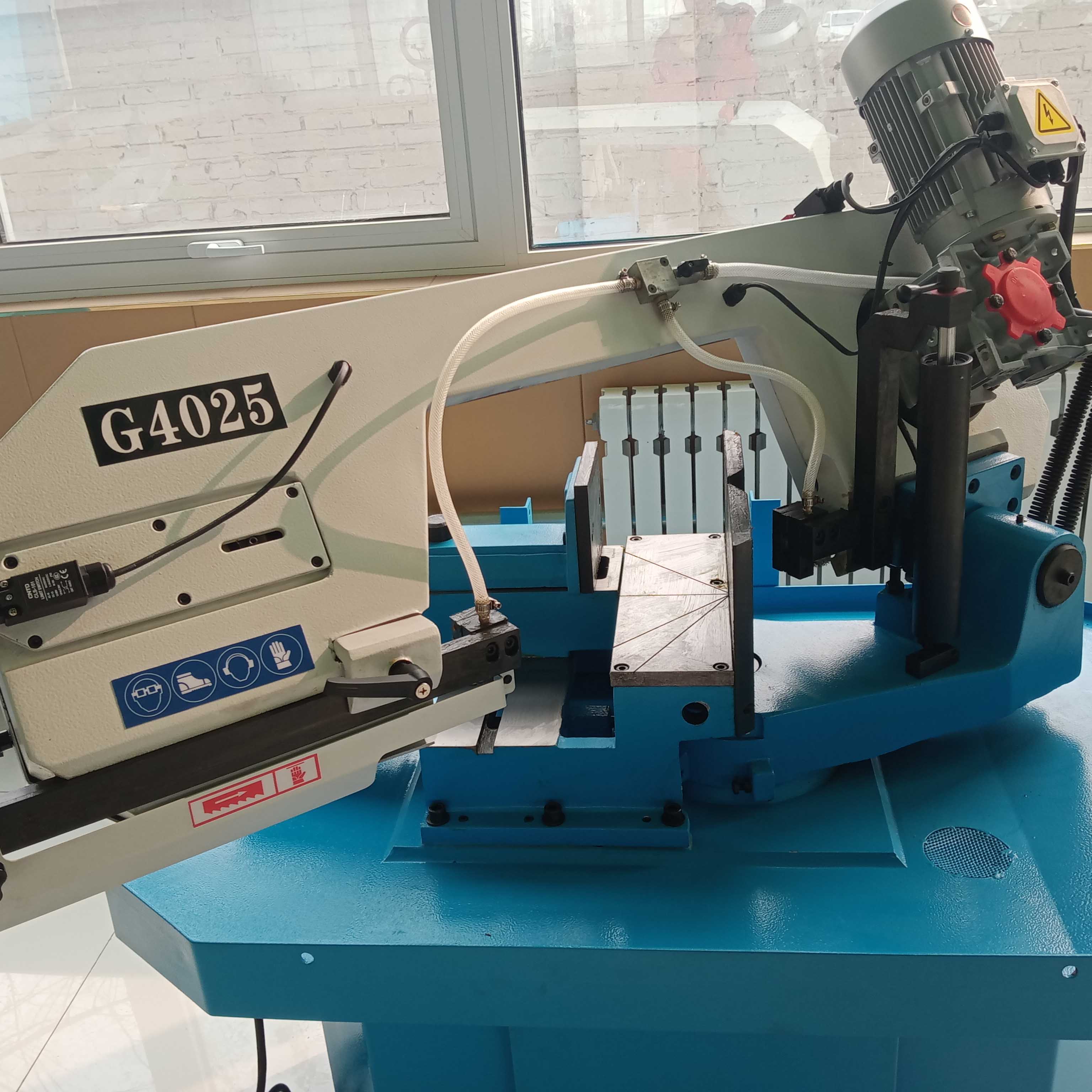
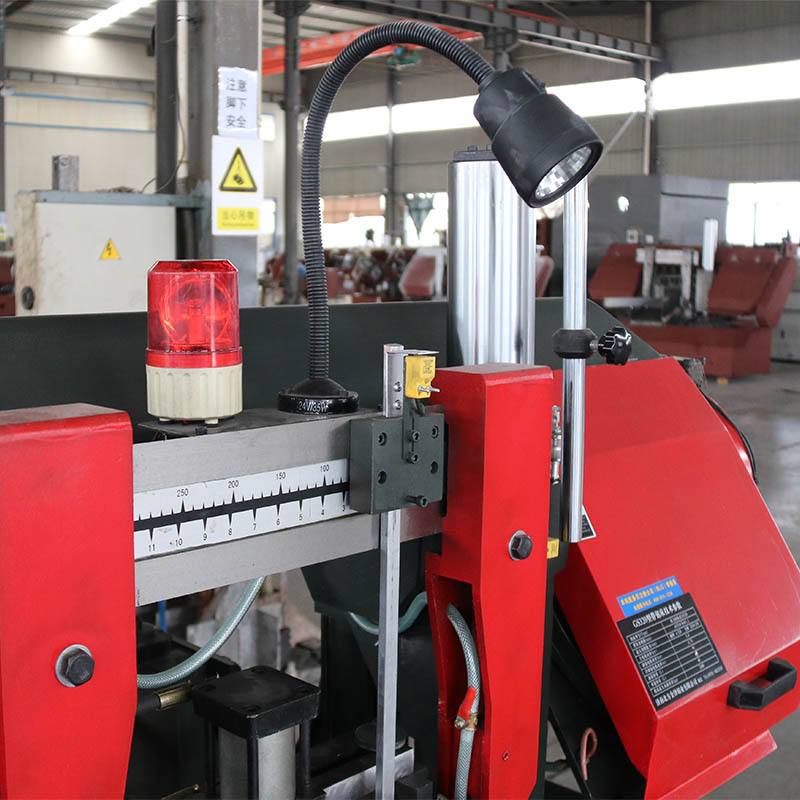
12 Inch Band Saw Machine The PACE battery system can be utilized for more machines as the battery-powered family expands. In addition to the power cutters and battery system, diamond blades in 12 in. and 14 in./300 and 350 mm have been optimized for battery operation. The machine is also equipped with X-Halt brake function capable of stopping the rotation of a blade in a fraction of a second for enhanced safety.