A 360-degree look at resin conveying systems: types, operation, economics, design, installation, components and controls.
This Knowledge Center provides an overview of resin moisture and the drying process, including information on the best drying practices for your manufacturing facility. Polyurethane Foam Equipment
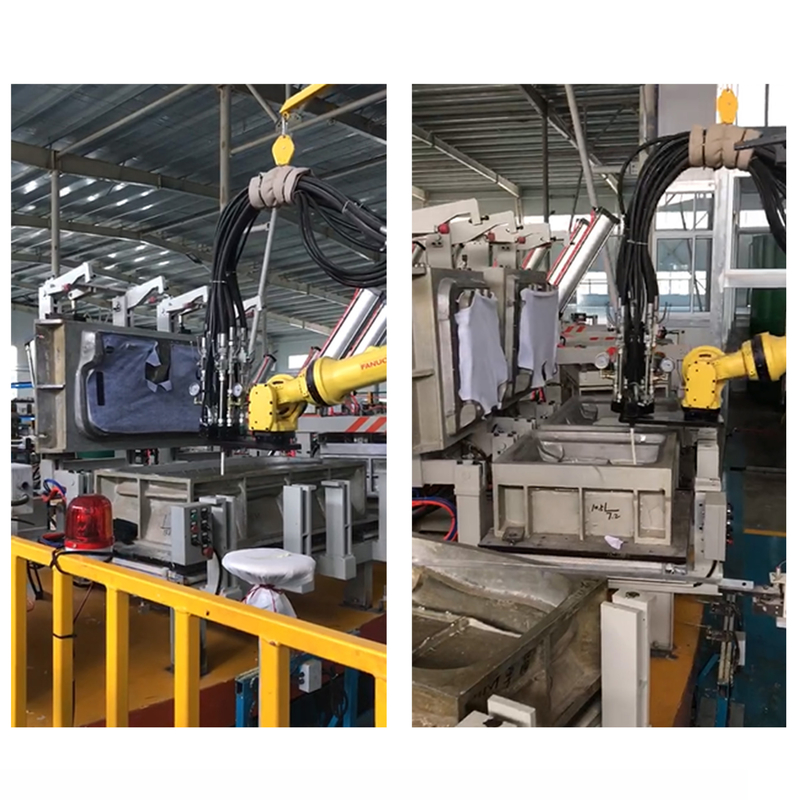
Combat the skilled labor shortage using this comprehensive resource to train your own plastics processing experts.
Deep dive into the basics of blending versus dosing, controls, maintenance, process integration and more.
This Knowledge Center provides an overview of the considerations needed to understand the purchase, operation, and maintenance of a process cooling system.
Learn about sustainable scrap reprocessing—this resource offers a deep dive into everything from granulator types and options, to service tips, videos and technical articles.
Despite earlier anticipated rollover in prices for most of the volume commodity resins, prices were generally on the way up for all going into the third month of first quarter.
While price initiatives for PE and PVC were underway, resin prices had rollover potential for first two months of 2024, perhaps with the exception of PET.
Flat-to-downward trajectory for at least this month.
A mixed bag, though prices likely to be down if not flat for all this month.
Trajectory is generally flat-to-down for all commodity resins.
Flat-to-down trajectory underway for fourth quarter for commodity resins.
Resin drying is a crucial, but often-misunderstood area. This collection includes details on why and what you need to dry, how to specify a dryer, and best practices.
Take a deep dive into all of the various aspects of part quoting to ensure you’ve got all the bases—as in costs—covered before preparing your customer’s quote for services.
In this collection of articles, two of the industry’s foremost authorities on screw design — Jim Frankand and Mark Spalding — offer their sage advice on screw design...what works, what doesn’t, and what to look for when things start going wrong.
In this collection, which is part one of a series representing some of John’s finest work, we present you with five articles that we think you will refer to time and again as you look to solve problems, cut cycle times and improve the quality of the parts you mold.
Gifted with extraordinary technical know how and an authoritative yet plain English writing style, in this collection of articles Fattori offers his insights on a variety of molding-related topics that are bound to make your days on the production floor go a little bit better.
In this three-part collection, veteran molder and moldmaker Jim Fattori brings to bear his 40+ years of on-the-job experience and provides molders his “from the trenches” perspective on on the why, where and how of venting injection molds. Take the trial-and-error out of the molding venting process.
Mike Sepe has authored more than 25 ANTEC papers and more than 250 articles illustrating the importance of this interdisciplanary approach. In this collection, we present some of his best work during the years he has been contributing for Plastics Technology Magazine.
In this collection of content, we provide expert advice on welding from some of the leading authorities in the field, with tips on such matters as controls, as well as insights on how to solve common problems in welding.
Mold maintenance is critical, and with this collection of content we’ve bundled some of the very best advice we’ve published on repairing, maintaining, evaluating and even hanging molds on injection molding machines.
Thousands of people visit our Supplier Guide every day to source equipment and materials. Get in front of them with a free company profile.
In its 45th year, Precision Molded Plastics has carved out a technology and market niche, growing not just when opportunities arise but when they make sense, after its leader changed careers to keep the family business from changing hands.
As an injection molder, Windmill Plastics sought an economical production monitoring system that could help it keep tabs on its shop floor. It’s now selling the “very focused” digital supervisor it created, automating many formerly manual tasks.
As we mark the fifth anniversary of the Global Commitment, a collaborative effort led by the Ellen MacArthur Foundation and the United Nations, we reflect on its enduring impact in steering the plastic packaging value chain toward a sustainable future. We explore insights shared by initiative signatories, assessing the strides made and recognizing challenges faced, toward the construction of sustainable packaging frame.
Driven by brand owner demands and new worldwide legislation, the entire supply chain is working toward the shift to circularity, with some evidence the circular economy has already begun.
While still in contraction mode, the index came in at highest level since March 2023.
Despite earlier anticipated rollover in prices for most of the volume commodity resins, prices were generally on the way up for all going into the third month of first quarter.
Cooling specialist Addex to roll out new auto-profiling air ring for rotating dies, and new single-plenum air ring.
As more plastics manufacturers step into the Fourth Industrial Revolution, insights have emerged about how best to approach the digital transformation journey.
Mission PET supplements bottle-to-bottle capability with alternative applications for recycled PET.
Maker of one-stage ISBM machines will show off new sizes and styles of handled and stackable PET containers, including novel interlocking products.
Topping five other entries in voting by fellow molders, the Ultradent team talks about their Hot Shots sweep.
Serendipitous Learning Opportunities at PTXPO Underscore the Value of Being Present.
Introduced by Zeiger and Spark Industries at the PTXPO, the nozzle is designed for maximum heat transfer and uniformity with a continuous taper for self cleaning.
Ultradent's entry of its Umbrella cheek retractor took home the awards for Technical Sophistication and Achievement in Economics and Efficiency at PTXPO.
technotrans says climate protection, energy efficiency and customization will be key discussion topics at PTXPO as it displays its protemp flow 6 ultrasonic eco and the teco cs 90t 9.1 TCUs.
Shibaura discusses the upcoming Plastics Technology Expo (PTXPO) March 28-30
NPE2024: Bekum is running EPET on its first U.S.-built all-electric shuttle. it is also highlighting the new XBLOW 200 industrial machine with new clamp design, plus a new extrusion head, three-layer retrofits, energy-saving extruder and EBLOW 08 electric shuttles.
NPE: The Plastics Show, produced by The Plastics Industry Association, will host its inaugural Women in Plastics Breakfast featuring speaker Kerrie Greenfelder, PE.
Maker of one-stage ISBM machines will show off new sizes and styles of handled and stackable PET containers, including novel interlocking products.
NPE2024: Frigel North America will launch RSY Syncro and RS/MD series, as well as new innovations in at-the-press and whole plant cooling.
NPE2024: Progressive’s CVe OnDemand software now offers wireless connectivity.
NPE2024: iD Additives will also feature displays of chemical foaming agents, purging compounds, plastic mold cleaners, and water cleaning and maintenance systems.
Mixed in among thought leaders from leading suppliers to injection molders and mold makers at the 2023 Molding and MoldMaking conferences will be molders and toolmakers themselves.
After successfully introducing a combined conference for moldmakers and injection molders in 2022, Plastics Technology and MoldMaking Technology are once again joining forces for a tooling/molding two-for-one.
Multiple speakers at Molding 2023 will address the ways simulation can impact material substitution decisions, process profitability and simplification of mold design.
When, how, what and why to automate — leading robotics suppliers and forward-thinking moldmakers will share their insights on automating manufacturing at collocated event.
As self-imposed and government-issued sustainability mandates approach, injection molders reimagine their operations.
August 29-30 in Minneapolis all things injection molding and moldmaking will be happening at the Hyatt Regency — check out who’s speaking on what topics today.
Get your clicking finger in shape and sign up for all that we have in store for you in 2023.
Molding 2023 to take place Aug. 29-30 in Minnesota; Extrusion 2023 slated for Oct. 10-12 in Indiana.
Finding it hard to get technical talent? Experiencing the pain of a knowledgeable, long-term employee's retirement? Learn how plastics processors are training generative AIs on their operations and unlocking the value from their tribal knowledge. Plastics processors are training generative AI models on their operations — from machine manuals to tools, polymers, procedures, maintenance records and engineering projects. Applying generative AI in the right ways can lower plastics processors' costs, improve overall equipment effectiveness (OEE) and upskill teams. In this webinar, you'll learn how to deploy AI technical assistants to your teams, what works and what doesn't, and how to use AI to build an organization that never loses tribal knowledge and fosters inter-team collaboration. Agenda: What is generative AI and how can its cognitive abilities be applied to plastics? Case study: how an injection molder trained a large language model on manuals and maintenance records to reduce downtime Case study: using generative AI in engineering teams to improve product development Live demonstration of a generative AI deep-trained on plastics knowledge Looking to the future: five predictions for an AI-augmented workforce in plastics
Innovative closures at the forefront of this trend have fostered a tooling evolution that enables cost-effective manufacturing of lightweight designs. Find out more about why global beverage brands are switching closures, specific design best practices and the significant merits of a mono-material package solution. Join this webinar to find out how these production changes can enable you to reach your sustainability goals and drive business growth. Agenda: The trend toward lightweight beverage closure designs The advantages of lightweight and tethered closures Why beverage brands are implementing tethered solutions even in the absence of mandates Tooling design best practices to mold today’s ultra-lightweight closure designs The merits of a mono material package solution
Key technologies — such as multicolor molding, film molding and PUR overmolding for both exterior and interior applications — are at the forefront of this transformation. Join this webinar to explore the vast potential of eMobility in molding large components — including those with fiber reinforcements — thereby driving the need for large injection molding cells with a clamping force of up to 11,000 tons. You will also gain insight into Engel's innovative two-stage process, a solution for future recycling processes. This webinar will provide an in-depth overview of challenging applications, production concepts and best practices, including: BMW iX front panel production cell Smart rear panels concept based on IMD and 2C molding Sustainability concepts based on two-stage process Large tonnage equipment for battery moldings
In today's manufacturing environment, robust processes that meet strict industry and regulatory standards are essential. With the advent of servo-driven ultrasonic welding technology, enhancing product quality and maintaining consistency has become remarkably effortless. Discover the fundamentals of ultrasonic welding, delve into vital components within these systems, explore how servo-driven ultrasonic welding enhances weld quality via advanced control features and gain insights into optimizing your assemblies for welding in these high-performing machines. Join Dukane to unlock the potential of ultrasonic welding in modern manufacturing for plastic devices and components. Agenda: Fundamentals of ultrasonic welding Key components in an ultrasonic welding system Using servo-driven ultrasonic systems to control your welding process Designing your parts and components for servo-controlled ultrasonic welding
This webinar will help you make informed decisions to confirm the equipment access stairs in your facility are OSHA compliant and meet the highest standards of safety and ergonomics. Agenda: Identifying opportunities to increase safety in the work place Utilizing space saving stairways Ensuring code compliance for equipment access
4.0, EUROMAP, OPC, OLE, QC, DSN, SQL, VNC, MES, ERP, FTP, CMS, SPI — are you confused by all buzzwords being tossed around in the plastics industry? Not convinced the data collection is necessary? Or are you unsure of how it could be implemented and improve your molding processes? Wittmann has been on the cutting edge of the data collection push for nearly 20 years. In this webinar, take a step back from the idea of the manufacturing facility of the future and discuss what you can do today to improve your process. Using readily-available technology, Wittmann can help reduce downtime, limit scrap and wasted material, and predict required maintenance. Let the experts at Wittmann help you understand: what data can be collected, what that data can be used for, what systems are used, and how to implement them. Agenda: Demystifying the terminology Tracking the material flow and lot information through the material handling system The data available from various auxiliary equipment, such as: dryers, blenders, mold temperature controls and robots Automating the process through changes in the data collected at the machines during production Adding visualization to increase productivity
Every three years, leaders from almost every major industry gather at NPE to advance their businesses through innovations in plastics. The largest plastics trade show in the Americas, NPE offers six technology zones, keynote speakers, workshops and opportunities to build partnerships.
The 3D Printing Workshop @ NPE2024 – The Plastics Show, is an immersive, half-day workshop focused on the emerging possibilities for part production via 3D printing and additive manufacturing. Presented by Additive Manufacturing Media, Plastics Technology and MoldMaking Technology, the 3D Printing Workshop will build upon a successful model first introduced at IMTS 2014. Attendees will benefit from a program focused on practical applications of 3D technologies related to plastics processing. This event will conclude with a 3D Printing Industry Reception sponsored by Additive Manufacturing Media.
The Society Plastics Engineers (SPE) Extrusion Division and the SPE Eastern New England Section will co-host the Screw Design Conference-Topcon on June 19-20, 2024 @ UMass Lowell in Lowell, MA. This highly technical program will focus upon screw design principles for single and twin screw extruders with wide ranging topics relating to screw designs for feeding, melting, mixing, venting and pumping plastics products and parts. Areas of focus will include screw designs for melt temperature and gel management, gel minimization, bioplastics, recycled materials and foaming. In addition to the technical sessions, a tour of the UMass Lowel Plastics Processing Laboratories will be integrated into Day 2 of the event. This program is not just for screw designers, but to help anyone responsible for any type of extrusion operation to evaluate existing extrusion equipment; and also to prepare for future projects. Price to attend: Less than $1000! Registrations will be accepted in early 2024. Call for papers – To be considered to give a presentation, please submit a talk title and abstract on or before December 15 to: Technical Chair: Eldridge M. Mount III, e-mail emmount@msn.com Corporate sponsorships - A limited # of corporate sponsorships (15) are available on a 1st come basis. Included is a 6’ tabletop display (must fit on table), denotation in all promotional activities, and 1 no charge registration. To become a sponsor contact: Charlie Martin, Leistritz Extrusion, e-mail cmartin@leistritz-extrusion.com, cell 973-650 3137 General information: A reception on Day 1 and a tabletop display area will allow the attendees to meet and discuss state-of-the-art screw technologies with industry experts. The SPE Extrusion Division will issue a “Screw Design Certificate” to all participants who have attended the program. Students are encouraged to attend and will receive a discounted rate. For additional information contact: Program Chair: Karen Xiao, Macro Engineering, KXiao@macroeng.com
Debuting in 2010, the Parts Cleaning Conference is the leading and most trusted manufacturing and industrial parts cleaning forum focused solely on delivering quality technical information in the specialized field of machined parts cleansing. Providing guidance and training to understand the recognized sets of standards for industrial cleaning, every year the Conference showcases industry experts who present educational sessions on the latest and most pressing topics affecting manufacturing facilities today. Discover all that the 2022 Parts Cleaning Conference has to offer!
Presented by Additive Manufacturing Media, Plastics Technology and MoldMaking Technology, the 3D Printing Workshop at IMTS 2024 is a chance for job shops to learn the emerging possibilities for part production via 3D printing and additive manufacturing. First introduced at IMTS 2014, this workshop has helped hundreds of manufacturing professionals expand their additive capabilities.
Learn here how to take advantage of new lightweighting and recycle utilization opportunities in consumer packaging, thanks to a collaboration of leaders in microcellular foaming and multilayer head design.
FIG 1 Retrofit of Trexel’s B-Series gas-metering equipment to add blowing agent to the polymer melt through a port in the extruder barrel. (Images: Trexel Inc.)
Use of recycled plastics materials is a critical factor in the move toward a fully closed-loop economy in the plastic industry. Simply put, producers must reduce their energy and raw-material consumption to meet strict new legislation touted for introduction in 2025, as laid out in the proposed packaging regulation published in November 2022 by the European Commission. Cosmetic products that are contact-sensitive, for example, will contain 40% postconsumer regrind (PCR) and all other bottle packaging will contain 35% and 65% by 2030 and 2065, respectively. This is a tall order.
The challenge is not only the supply, availability and quality of recycled resins but also the development of new processes to enable their use and exploit their potential. With the sudden requirement for PCR and the need for respectable quality, cost will likely be an issue. Brand owners, in particular, are looking for ways to remain cost-competitive with the virgin product configurations of today’s common packaging specifications. Lightweighting through foaming has also gained growing attention and process adoption in recent years as an alternative to downgauging, which may compromise topload performance.
Trexel, a market leader in foaming technologies for lightweighting, and W. Müller, a market leader in blow molding multilayer head design, have partnered to create a lightweighting solution for inclusion of PCR and lowering the cost of bottle production without significantly sacrificing mechanical properties. Trexel has been delivering both physical and chemical foam lightweighting solutions for injection and blow molding. Its MuCell physical foaming technology is now standard or optional on many OEM injection molding platforms. With a recent focus on packaging solutions in injection molding, plus the company’s history of foaming blow-molded automotive ducts with the accumulator-head process, Trexel has implemented a MuCell foaming solution for extrusion blow molding (EBM) on shuttle and wheel machinery. Trexel is now working with brand owners on scale-up bottle projects.
FIG 2 Left: Solid, natural color. Middle: Foamed with no TiO2. Right: Foamed with 2 wt% TiO2 in outside skin. Foaming adds opacity with less or no need for pigment.
The multilayer solution involves metering nitrogen into the barrel of the EBM machine and foaming the core layer of a three-layer sandwich such that the layer ratio (by thickness) remains similar to the solid predecessor three-layer design but with reduced weight in the PCR core. There is also reduced core extruder speed associated with a given volumetric bottle output. By specifically coupling the MuCell process with a proprietary patented additive, impact strength, topload and ESCR will pass the necessary industry tests. Typically, there has been an improvement of up to 3 times in impact performance over previous foaming technologies, which is driving the ability to make larger foam-core bottles. The system and method are license-free and may be retrofitted to the existing screw and barrel, as depicted in Fig. 1. In addition to weight savings, TiO2 and other white masterbatches can often be reduced or eliminated, because foam adds an opaque appearance, as shown in Fig. 2.
Lightweighting through foaming is an alternative to downgauging, which may compromise topload performance.
W. Müller’s multilayer head and extruder systems can be retrofitted to most monolayer systems as well as on a new system. W. Müller, which built its first three-layer head in 1990, brings significant process experience with PCR-laden products through its RECO head series. MuCell is a physical foaming process, depending partially on the pressure events in the head or multiple heads in structure of three or more layers. As noted by Jens Schlueter, president of W. Müller USA, “Although there are many standard three-layer extrusion head designs out in the market, it is essential to have the experience with how to create designs that accommodate the foaming process. Understanding melt flow, melt pressure and how to perfectly dimension the flow channels inside the head is critical to a successful foaming application. Our expertise in providing custom-designed heads for different materials and designs ensures that our customers get the right solution for their needs and particular specifications.”
Of particular importance to the process is the ability of the Trexel SCF (supercritical fluid) delivery system to respond to pressure fluctuation that may arise from the addition of some lower-grade PCR to the extruder. Trexel’s proprietary system will “learn” process patterns and react to real-time events to keep foaming levels consistent to ensure process stability and consistent bottle geometry. To enable this, simple process timing signals from the blow molding machine are used.
W. Müller has installed two lab foaming systems, one at its headquarters in Troisdorf, Germany, and the second at its U.S. office in Agawam, Mass. They are both equipped with Trexel’s latest B120 SCF delivery system and handled bottle mold for use in demonstrations. Clients may also pick from other standard molds or supply their own molds to test out the technology.
Of particular importance is the ability of the gas-injection system to respond to pressure fluctuation that may arise from addition of some lower-grade PCR to the extruder.
To retrofit the pumping system, a hole is drilled in the existing barrel in a position so there is enough residence time to dissolve nitrogen gas in the melt. Trexel has conducted background research to mathematically define the exact parameters required to ensure homogeneous gas diffusion in such processes through work with its recently patented injection molding screw designs. Because almost 10 times less gas is used in the foam blow molding process than in injection molding, there is usually enough residence time to mix gas with the existing blow molding screw design, and therefore the process will not typically require a new screw and barrel.
It is anticipated that in the future Trexel’s SCF delivery system controls will be integrated into the W. Müller control system to provide a one-stop foaming add-on which will convert an existing monolayer system to a full multilayer foam system.
FIG 3 Case study bottle mold for topload and drop-impact testing.
The following case study was used to corroborate and summarize recent work using the demonstration mold. A blow molding system was configured as in Fig. 2 and combined with Trexel’s handled bottle mold as shown in Fig. 3. The die tooling was downsized such that the parison layflat dimension was the same for solid and foamed extrudate – yielding the same amount of flash/top/tail. In some cases, die ovalization may change slightly from that for a solid product.
FIG 4 Parison layer structures between solid and foam test bottles. Die tooling was downsized so that the parison layflat dimension was the same for solid and foamed extrudate – producing the same amount of flash/top/tail.
Weight was then reduced in the core extruder, as shown in the center bar in Fig. 4; here the tail was too short to actually mold a product. Gas was then injected and the structure was foamed back to a thickness similar to a solid part, as shown on the right-hand bar of Figure 4. Given that stiffness is a key factor that varies as a cube function of nominal thickness, overall thickness can be manipulated to offset the reduction in density, which varies only linearly with stiffness. In essence, foam has a better stiffness-to-weight ratio than solid structures.
Blow pressure was then applied, typically lower than for solid molding, sometimes in multiple stages. The lower pressure at these thicknesses does not introduce the need for greater cooling time or a change in mold venting. In the process, minor calibration or crushing of the structure takes place to leave the final product as shown in Fig. 5. For example, the final foam parison from Fig. 4 is 2.16 mm, which is calibrated (compressed) by nearly 50% during the blow process to leave a final thickness of 1.12 mm, shown in Fig. 5.
FIG 5 Final bottle structures after blowing and foam versus solid metrics (table), showing savings in bottle weight, cost and cycle time.
The result was a foamed bottle that is 6 g lighter, with an overall density of 0.830 g/cc and a core density of 0.760 g/cc. Nominal thickness of the outside layer was the same as in the solid structure, and extra thickness to maintain stiffness came from the foamed layer. The cycle time in this instance was reduced by 2.5 sec. The final metrics of the bottle are shown in the table in Fig. 5, which notes savings in bottle weight, cost and cycle time. It should be noted there are multiple ways to quantify the savings. Cycle time may remain constant (same volumetric output) but with reduced material consumption; or alternatively there might be similar material (weight) throughput as with a solid wall, but with increased volume output — more bottles per hour. In this case study, it was a mixture of both.
FIG 6 Scanning electron micrograph of a typical three-layer foam structure, with a 1.3 mm total thickness, outer solid skin layer of 0.17 mm, foam layer of 0.92 mm and inner solid skin layer of 0.21 mm.
An important factor in the technology, as noted, is the homogeneous mixing of gas, but also the synergy of the gas desorption at the instant that pressure is released at the die exit. This creates very small bubbles with an aspect ratio typically no more than 2:1 and cell size less than 100 microns after blowing (Fig. 6). The foam parison continues expanding such that there is ample thickness in the base of the bottle. Unlike traditional nucleating agents, the proprietary nucleant additive in this process does not negatively affect impact strength (if, for example, you were to put it in an unfoamed product). The combination of those factors enables the foam technology to apply to much larger bottles than just 200 ml and pass impact tests.
Three base tests were performed on the test bottle. The drop-impact test was 11.5 ft for the foamed bottle with an ESCR test pass. Topload test results showed that for the same weight (comparing Trials 8 and 11 in Fig. 7), force per mm of thickness was the same for foamed and unfoamed bottles. Furthermore, the foamed bottle showed a 20% increase in total energy absorbed before the peak topload was reached.
FIG 7 Topload tests show that for foamed and unfoamed bottles of the same weight (trials 8 & 11), topload force per mm of thickness was the same, but the foamed bottle exhibited 20% more total energy absorbed before peak topload was reached. A solid bottle of the same thickness but higher weight showed greater topload strength.
Further work is now being conducted on different materials and shapes for brand owners. This extends to biopolymers, which will not be subjected to the regulations in Europe when they begin to roll out but would benefit from cost reduction. Work is also being conducted on wheel machines where the technology has been run successfully at full scale on larger bottles for applications like household detergents.
Trexel has shown a new and improved way to foam bottles with the ability to reduce the cost of PCR-laden bottles and/or simply to lightweight bottles as an alternative to downgauging which is limited by topload strength. Foam has an improved stiffness-to-weight ratio and provides opacity without adding masterbatch.
Ability to pass topload and drop-impact tests enables foaming to be used in much larger bottles.
Trexel has addressed a key shortcoming of previous renditions of the foaming technology — in particular, drop-impact resistance has been addressed, while topload strength can be maintained by increasing thickness at the foamed lower density. Foaming will not be suitable for every product, such as monolayer, very thin, heavily embossed or with ultrahigh drop-impact requirements. But the list of successful applications is ever growing and gaining attention.
Foaming can be retrofitted to old machines or installed as new. In the former instance, W. Müller and Trexel have partnered to provide the ability to change a monolayer machine to make multilayer foam structures with minimal capital investment and no royalties.
ABOUT THE AUTHOR Sam Dix is the R&D director at Trexel and previously of Zotefoams PLC. He has dedicated over 20 years to developing innovative lightweighting solutions for the plastics industry. This has included a wide range of hardware, systems and processes for customers worldwide. Contact: S.Dix@trexel.com; 781-266-7391; trexel.com.
And as with all sciences, there are fundamentals that must be considered to do color right. Here’s a helpful start.
Trexel and Husky are cooperating on molding recyclable opaque white preforms for PET bottles, which provide a light barrier using foam instead of pigment.
When evaluating ERP solutions, consider the power of interactive production scheduling to effectively plan and allocate primary and secondary equipment, materials and resources on the overall production capacity of the business and conclude that this is a key area that cannot be overlooked.
Here’s a quick guide to fixing four nettlesome problems in processing PET bottles.
At K 2022 this month, W. Müller is presenting a system for PCR processing in a three-layer coextrusion, using an energy-saving barrel-heating system.
Agreement with MuCell Extrusion allows Trexel to pursue foam blow molding in packaging as well as automotive.
MuCell technology gains new momentum in blow molded packaging through this partnership of a leader in physical foaming with supercritical gases and a leader in coex blow molding hardware and controls.
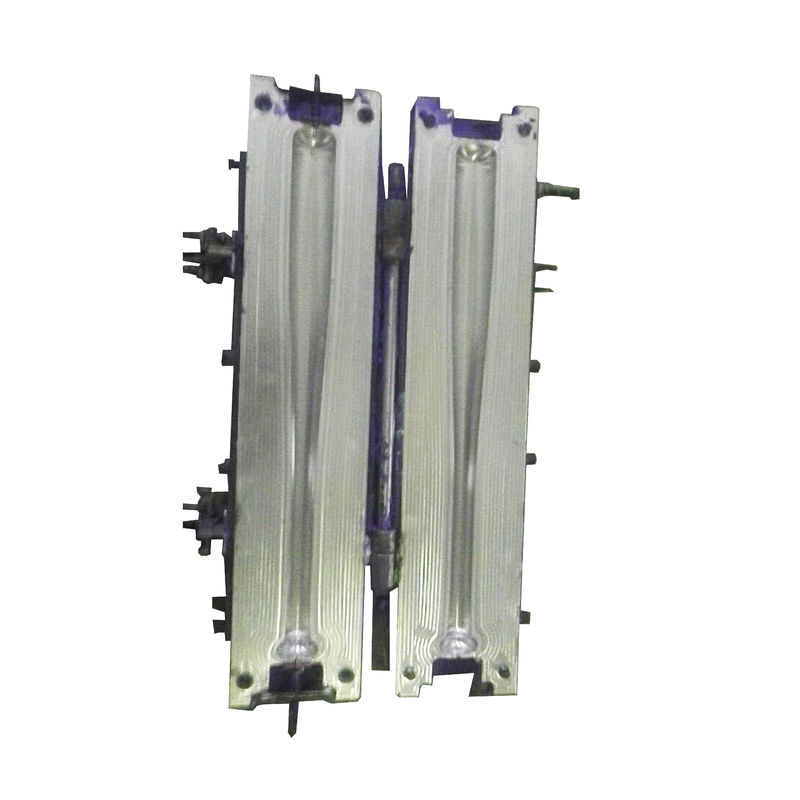
Polyurethane Spray Foam Machine Plastics Technology covers technical and business Information for Plastics Processors in Injection Molding, Extrusion, Blow Molding, Plastic Additives, Compounding, Plastic Materials, and Resin Pricing. Learn More