Latching solenoids have many benefits. No power is drawn to maintain position, and a customisable fail-safe circuit means that if power is lost, the system returns to its safe setting. Chad VanRens elaborates
The explosion of electric vehicle development has OEM design teams searching for ways to reduce the power consumption of all vehicle components and systems. Efficiently utilising the finite amount of energy available from an EV’s batteries is crucial for achieving maximum vehicle range, and this means every single component and system must be as lightweight and energy efficient as possible. Wire Quick Connectors
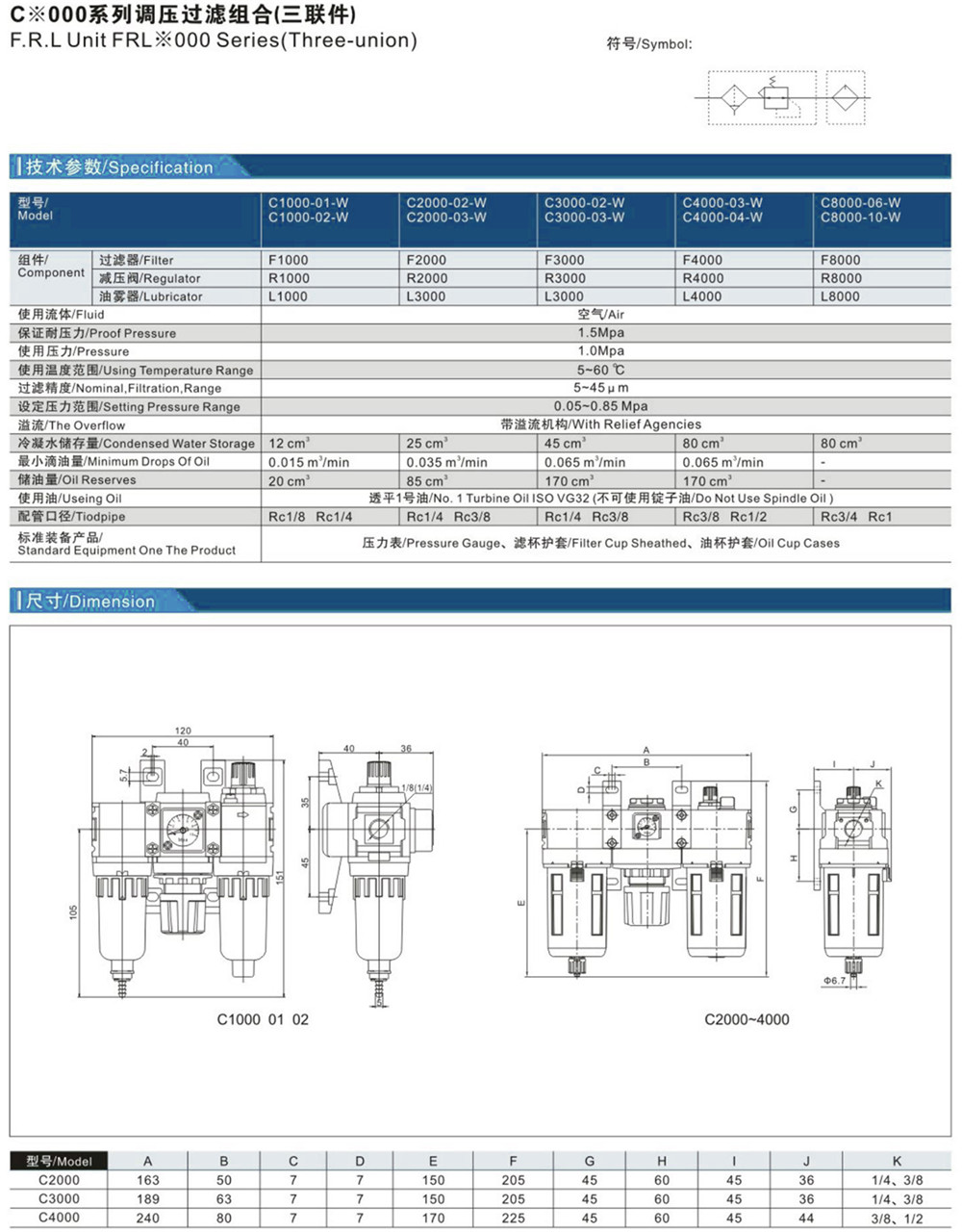
Electromagnetic components are used extensively in EVs. Replacing conventional solenoids with solutions utilising latching technology is a great way to achieve the desired energy savings. Latching solenoids are ideal for any application that does not require a high cycle rate because they draw no power in order to maintain either an open or closed state.
While conventional solenoids require power during the entire on cycle, latching solenoids require only a pulse of power to change state. Once the armature is extended or retracted, no power is consumed for the duration of the on cycle because the armature in a latching solenoid is held in position either by a permanent magnet or residual magnetism (depending on the solenoid’s design).
The low power consumption of latching solenoid technology yields other benefits too. Because there is no power consumption during most of the on cycle, a higher current pulse can be used to actuate the armature, resulting in faster operation and higher force, without the excessive heat generation associated with conventional solenoids. Additionally, because the higher pulse current can generate more force, it is possible to use a smaller, lighter solenoid than would be the case if a conventional solenoid was employed.
Until recently, some OEM design teams have had concerns with using latching solenoids in applications where the actuator must return to a known position in the event of power loss. Because latching solenoids require power to actuate, a loss of power means that the armature will remain in its last commanded position.
This concern is easily settled with the use of a latch-release circuit: a simple fail-safe control strategy consisting of a circuit board and a capacitor. The circuit board monitors power availability, while the capacitor provides the necessary pulse of current to move the armature in the event of power loss. This system can be customised to actuate the armature to a predetermined, specific position.
Chad VanRens is with TLX Technologies
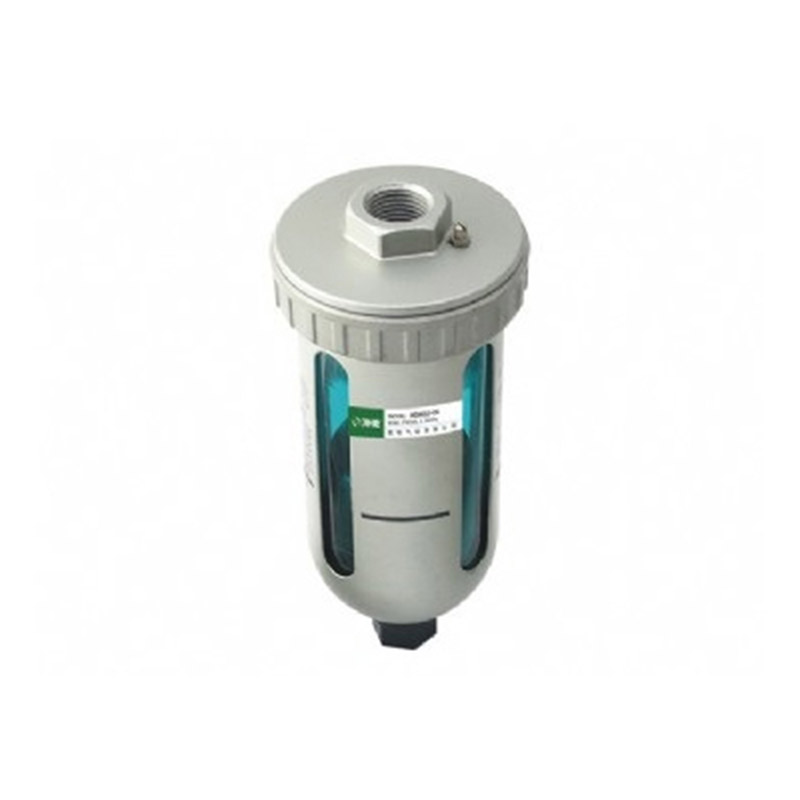
Sov Valve © Setform Limited 2019-2024 | Privacy policy | Archive