This article provides an overview of the roadmap, opportunities, and challenges of two promising process route alternatives for the green steel transformation of blast furnace–basic oxygen furnace (BF-BOF) plants. Since these integrated steel plants are characterised by CO2 emissions nearly three times higher than mini mills—mainly driven by the blast furnace, sintering, and coking plant—this study reviews and benchmarks technology alternatives for BF-BOF plants from a refractory point of view. Additionally, examples and first research investigation results are discussed to highlight the readiness of RHI Magnesita for the green steel transformation.
Today, the iron and steel industry is the second largest global industrial CO2 emitter, mainly driven by blast furnace–basic oxygen furnace (BF-BOF) plants that represent 70% of worldwide steel production [1]. Consequently, BF-BOF plants are under increasing pressure to decarbonise their production facilities. Two main paths for process route alternatives are currently under evaluation: The first comprises a direct reduction (DR) unit, which is industrially proven with the current dominant use of natural gas and planned to be gradually shifted to hydrogen, combined with a continuous electric smelting furnace (ESF), followed by the basic oxygen furnace (BOF) process. The second approach is complete transformation to an electric arc furnace (EAF) plant based on direct reduced iron (DRI). However, both steelmaking technologies encounter their own challenges in terms of process and refractory solutions: The ESF technology is fully proven for the nonferrous industry, but for the steel industry a balanced refractory design and an appropriately sized unit is not yet available. In contrast, the EAF is well-established for steelmaking, but for tapping weights exceeding 250 tonnes additional measures are required to improve process efficiency [2]. Intermediate Frequency Furnace
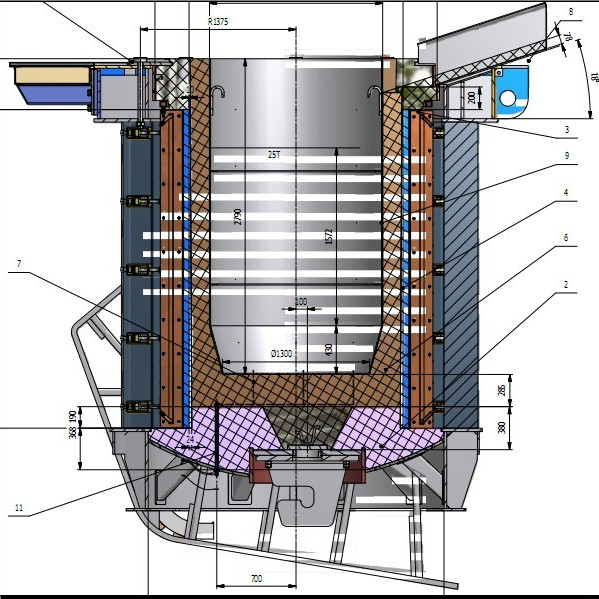
As described above, there are two main approaches for raising the CO2 abatement potential of steelmaking currently being discussed and evaluated: On the one hand, a DR unit combined with an ESF and continuing with the BOF process, and on the other hand, a complete transformation to an EAF mill mainly based on DRI. This section of the article discusses the differences between scrap-based and DRI-based steelmaking processes in EAF mills and addresses the impact of operating conditions on the EAF working lining. Figure 1 shows the typical refractory lining concept used for both DRI- and scrap-based EAFs [2].
Figure 1. Furnace areas and refractory products used in DRI- and scrap-charged EAFs [2].
There are several differences to be considered when comparing the production characteristics of a conventional scrap charged EAF to an EAF process based on high shares of DRI and/or hot briquetted iron (HBI). These divergences are mainly related to the electrical energy demand, chemical energy input, size of the hot heel, and metallurgical influences. Due to the remaining gangue oxides present in the DRI/HBI and varying levels of carbon, different power programs and adapted additions of lime, dolomitic lime, and doloma are required for the continuous charging of high amounts of DRI. The hot or cold DRI is charged via the fifth hole in the furnace roof. The remaining melt volume (i.e., hot heel) of a DRI-based EAF is up to 30% of the total melt volume to facilitate DRI melting. In contrast to conventional scrap-based furnaces, the DRI-EAF process operates under flat bath conditions. However, due to the absence of a scrap pile, power programs with a shorter arc length, which results in a lower arc voltage and slightly decreased efficiency of energy transfer to the steel melt, are defined. The oxide gangue present in the DRI not only decreases the metal yield of DRI charges, but also increases the risk of low slag basicity in the case of insufficient compensation of the acid gangue by flux additions. Furthermore, high levels of acid gangue content cause a significant increase in the specific amount and volume of process slags compared to the standard operation based on steel scrap, which also affects the lifetime of the refractory lining. Additionally, the electrical energy demand rises with a higher input of burned slag formers. As a result of these DRI-specific process conditions, the melting time as well as the tap-to-tap time of DRI heats can be significantly longer than for standard scrap heats [2].
Due to the above-mentioned differences, typically higher quality refractory grades and intensified maintenance, such as gunning and fettling, are applied to DRI-charged furnaces to counteract this higher strain on the refractory lining. Figure 2 illustrates the main differences in the working lining design based on the typical magnesia-carbon brick grades in operation [2].
DRI-charged EAFs are mainly operated with high- performance grades in all furnace lining areas. Furthermore, furnace maintenance such as gunning and fettling is also usually carried out with high-grade materials. In comparison, scrap-based EAFs, both for furnace installation and for maintenance, are widely and successfully run with standard grades based on significant amounts of circular raw materials. This incorporation of circular raw materials leads to a considerable reduction in the CO2 footprint of the individual refractory products and thereby contributes to decreased scope 3 greenhouse gas emissions at the steel plant [2].
Figure 2. MgO-C performance classes used in (a) DRI- and (b) scrap-charged EAFs [3].
Specific refractory consumption figures (kg of refractories consumed per tonne of liquid steel produced) and EAF lifetimes of scrap-charged compared to DRI-charged EAFs can vary significantly. Typical lifetimes for EAFs are shown below, whereby the wide variation within the furnace types is a result of the maintenance philosophy adopted, which strongly influences the lifetime [2]:
Consequently, DRI-operated EAFs often show an overall higher consumption of refractory materials and therefore higher specific refractory consumption rates, particularly driven by maintenance mixes for gunning and fettling as well as the slag zone working lining. A comparison of the consumption figures of full-year averages for all relevant refractory products is shown in Figure 3 and Figure 4 [2]. Eccentric bottom taphole (EBT) filling mixes used to fill the taphole channel after each heat tapped are excluded from this comparison. EBT filling mix consumption ranges from 1–1.5 kg refractory /t liquid steel [2].
Figure 3. Annual average specific refractory consumption figures for a scrap-charged 145-tonne EAF [4].
Figure 4. Annual average specific refractory consumption figures for a DRI-charged 130-tonne EAF [4].
Modern EAF technology is based on shallow hearth designs and multiple supersonic oxygen injectors to address the inherent problem of low melt movement. With the decreasing oxygen demand of DRI charges, efficient melt mixing is even more difficult, especially in large volume EAFs that are currently being designed for integrated steel plants.
By far the most efficient movement of the entire steel melt is generated by inert gas purging (Figure 5). Developed by RHI Magnesita in the early 1980s, approximately 9% of EAFs worldwide are now equipped with gas purging systems, especially large EAFs with tapping weights above 150 tonnes and an additional 20–35% hot heel. Over the years, refractory solutions and the gas control units have been significantly improved to reach maximum safety and lifetime [2].
The gas control units from INTERSTOP are characterised by a leak-free, modular design, and minimum space requirements (Figure 6), providing very precise and fast gas flow control over a wide range of Ar and N2 flow rates [5]. Automatic wear and leakage detection as well as customer- specified programs, data acquisition, and storage are state- of-the-art [2].
The process benefits of inert gas purging are directly related to the improved movement and mixing in the entire melt volume. The temperature distribution is significantly more homogeneous, and decarburisation is improved, especially when charge combinations of steel scrap, DRI, or hot metal are applied. The most important process improvements for DRI charging are [5]:
Figure 5. Improved melt mixing by inert gas purging (RADEX DPP system) in an EAF [2].
Figure 6. EAF gas purging system from INTERSTOP with a very compact design [2].
The corresponding CAPEX and OPEX of the gas purging system are easily exceeded by the process benefits, resulting in a return on investment after only a few EAF campaigns. A typical example of the observed process improvements for a 250-tonne EAF (200-tonne tapping weight), charged with more than 95% DRI, is given in Table I [2].
Alternative units for melting large volumes of DRI at low conversion costs in integrated steel plants are ESFs. They represent a well-established furnace technology in the nonferrous metallurgical industry and will now be adapted to the specific requirements of the steel industry to process low-grade DRI prior to charging it into the BOF [2].
Table I. Observed benefits of RADEX DPP gas purging in a 250-tonne DRI-EAF [2].
ESF technology is a well-known and long-established electric melting technology in the nonferrous metals industry. These melting units can be engineered using two different fundamental designs: The so-called six-in-line EAF, with its rectangular shell design, and the round ESF. Both are widely used today for melting and processing different ferroalloys such as FeNi and FeTiO3, but also for platinum group metals (PGM), Ni, and Cu. To meet the requirements of these industry sectors and their respective processes, the scale of these ESFs is extremely large compared to state-of-the-art steel furnaces. The dimensions of a rectangular smelter typically reach 40 m in length, 15 m in width, and almost 9 m in height, while the round units can exceed 20 m in diameter and 6 m in height. However, from a refractory engineering point of view, there is a technical limit regarding the size to ensure uniform expansion during the highly demanding heat-up phase [2].
The basic question concerning the operation practice is whether the furnace will be operated in open or covered bath mode, as this makes a huge difference in terms of radiation and thermal impact on the upper sections of the furnace, especially on the roof lining. The roof lining is exposed to much higher thermal loads in combination with chemical impacts when operated in open bath mode, which must be taken into consideration when choosing the refractory material to avoid roof lining collapse and prevent the thermal application limit of the refractories being reached [2].
The general lining concepts (Figure 7) for such smelters are mainly based on high-fired, high-purity magnesia bricks in the case of ferroalloys or magnesia chrome bricks for PGM, Ni, and Cu applications, always considering the specified thermal profile of the hearth, mostly supported by bottom forced air-cooling technology. In the bath area, depending on the original equipment manufacturer (OEM) involved, different well-established cooling systems are applied. However, these different cooling systems require specific refractory solutions. That is why the given cooling design has always been the starting point for RHI Magnesita to provide the most suitable refractories in terms of both thermal as well as dimensional aspects, as this is also important to ensure safe furnace operation for the end user [2].
Depending on whether the operation mode is an open or covered bath, the refractory lining is based on either MgO or Al2O3. However, the type of alumina raw material used—bauxite, andalusite, or tabular alumina—is heavily influenced by the thermal impact in the respective area [2].
A further critical point is the hearth design, as this furnace region faces high lifting forces that can lead to an increased risk of floating bottom linings. Therefore, RHI Magnesita designs always consider a special and unique type of interlocking system to support the lining integrity in the hearth area. In addition, all planned furnace cooling technologies, the isotherm distribution of the refractory lining in the case of thermal expansion, as well as thermal profiles of multilayer designs considering OEM- and customer-relevant specifications are taken into account and investigated using finite element method tools during the engineering phase of the smelter refractory design [2].
In order to realise long-term stable operation of such a large furnace, the most important aspect, alongside the cooling technology, is thorough examination of the special requirements of furnace areas that are exposed to the highest stresses. One of the most demanding areas is the interface between the bath, slag, and off-gas, as the very acidic slags combined with super-heated baths require a very tight refractory lining based on design and engineering. The detailed engineering of such linings always demands an in-depth view on the relevant expansion calculations [2].
Figure 7. Well-established and proven lining concept used in rectangular ESFs for ferroalloy applications (e.g., FeNi) [2].
As the ESF technology is now being adapted to the steel industry, it is key to gain a deeper understanding about the chemical, thermal, and physical impact of this new steelmaking process on refractory materials. Therefore, different refractory grades, which are being considered for the slag zone area of the smelter, were tested at the Technology Center Leoben (Austria) to investigate their corrosion behaviour with a representative smelter slag. The planned smelter operation under a reducing atmosphere in combination with long settling times will ensure high yields and generate a low Fe- and FeO-content slag. Table II details the targeted smelter slag composition range, which is similar to today’s blast furnace slags and also suitable for the cement industry.
The corrosion test was performed in the high-frequency induction furnace (HF-ITO) illustrated in Figure 8, which was flushed with CO and CO2 and filled with molten synthetic slag adjusted to the composition shown in Table II. During testing, the refractory specimens were submerged in the slag-filled crucible and rotated to evaluate not only chemical resistance, but also the hot erosion behaviour of the different grades.
Figure 8. High-frequency induction furnace for corrosion testing.
Table II. Targeted smelter slag composition range.
Four basic material grades with different MgO, Cr2O3, and ZrO2 contents were selected for the evaluation. The sample compositions are listed in Table III and Figure 9 depicts the specimens after the corrosion test.
Figures 10 and 11 illustrate the micro-X-ray fluorescence results of Sample 1 and Sample 2, depicting the relative distribution of Si and Ca. The colour range demonstrates the relative amount of each element in the sample. Comparison of the images shows that both samples were coated by the CaO- and SiO2-containing synthetic slag, indicated by the white colour seen along the specimen tip. Furthermore, it can be concluded that infiltration of Sample 1, which is based on fused magnesia and contained 21 wt.% Cr2O3, extended over the entire specimen and was probably caused by capillary effects. In contrast, the infiltration depth of Sample 2, which is based on sinter magnesia and no Cr2O3, was confined to the immersion depth of the specimen. However, the amount of infiltration seemed to be higher, as indicated by the green colour. However, this may even have a positive effect as it could potentially improve the formation of a freeze layer. In Figure 12 it is evident that the material loss of Sample 1 was higher in the immersed area.
Table III. Chemical composition of the specimens according to the technical data sheets.
Figure 9. Basic refractory specimens after the corrosion test.
Figure 10a. Relative distribution of Ca in Sample 1.
Figure 10b. Relative distribution of Ca in Sample 2.
Figure 11a. Relative distribution of Si in Sample 1.
Figure 11b. Relative distribution of Si in Sample 2.
The relative distribution of Ca and Si in Sample 3, which is based on fused magnesia and 27.5 wt.% fused magnesia chromite, and Sample 4, containing MgO and ZrO2, after an HF-ITO test are shown in Figures 13 and 14. These demonstrate Sample 3 had a similar outcome to Sample 1, namely the specimen was fully infiltrated and coated by Ca-Si slag. According to the image of Sample 4, a thicker slag layer on the tip of the specimen was formed and the results indicated a more aggressive wear compared to the other samples.
In summary, the HF-ITO tests indicate that the presence of Cr2O3 in the sample leads to formation of low-melting phases, which affect the infiltration resistance and result in capillary effects.
Figure 12a. Erosion resistance of Sample 1.
Figure 12b. Erosion resistance of Sample 2.
According to the results, it appears Cr2O3 reduction occurred; however, further mineralogical research is required to gain a deeper understanding of the chemical reactions. The results of Sample 2 look the most promising, since slag infiltration as well as material wear caused by erosion were lower compared to the other samples. Nonetheless, further mineralogical investigations are required to fully characterise refractory materials that can withstand the chemical, thermal, and physical impact present in the ESF. As a next step, RHI Magnesia will conduct HF-ITO tests with selected nonbasic materials and different synthetic slag compositions.
Figure 13a. Relative distribution of Ca in Sample 3.
Figure 13b. Relative distribution of Ca in Sample 4.
Figure 14a. Relative distribution of Si in Sample 3.
Figure 14b. Relative distribution of Si in Sample 4.
For European steel plants in particular, the abatement of CO2 emissions is a major focus. The two described process routes can serve as technological alternatives to achieve the targeted European Union CO2 reductions in the steel industry; however, as discussed, both options have their own benefits and challenges. The smelter technology is not yet proven for steel production but it uses the already existing infrastructure of the integrated plants, since the BOF, secondary metallurgy, casting, and rolling mill are retained. The DRI-EAF route is a well-established technology, but encounters efficiency limitations depending on the DRI quality. Undoubtedly, steel mills need to consider a vast number of aspects before deciding to implement these major process modifications.
However, as a pioneer of the refractory industry with many years’ experience, RHI Magnesita aims to develop new refractory solutions to meet the requirements of the future steelmaking technologies. Investigation of the corrosion behaviour was only an initial step to better understand the chemical, mechanical, and thermal effects occurring when basic refractory materials are immersed in a smelter slag. In the framework of further R&D studies, process-adapted refractory concepts will be developed.
In addition, RHI Magnesita not only possess extensive know-how and expertise in the engineering and refractory design of mega-scale smelters, both rectangular and round, it also has numerous references in EAF applications for both scrap- and DRI-based operations. Consequently, RHI Magnesita is uniquely positioned to transfer proven concepts and learnings from one industry to another and support steel customers navigate through the green steel transformation.
[1] Kildahl, H., Wang, L., Tong, L. and Ding, Y. Cost Effective Decarbonisation of Blast Furnace – Basic Oxygen Furnace Steel Production Through Thermochemical Sector Coupling. Journal of Cleaner Production. 2023, 389, 135963. https://doi.org/10.1016/j.jclepro.2023.135963 [2] Kirowitz, J., Schnalzger, M., Janssen, T., Kirschen, M., Spanring, A., Moulin-Silva, W., Ratz, A., Kollmann, T. and Wucher, J. Electric Melting Furnaces for Green Steel Transformation of Integrated Steel Plants – Requirements, Challenges, and Solutions from a Refractory Perspective. Proceedings of the 9th European Oxygen Steelmaking Conference, Aachen, Germany, Oct. 17–22, 2022. [3] RHI Magnesita, 2021 RDW Shipment Data. [4] RHI Magnesita, 2021 Refractory Consumption Data: Europe and MENA customers. [5] Kirschen, M., Ehrengruber, R. and Zettl, K.-M. Latest Developments in Gas Purging Systems for BOF and EAF. Proceedings of METEC and 2nd ESTAD, Düsseldorf, Germany, June 15–19, 2015.

Copper Melting Furnace RHI Magnesita, Mülheim-Kärlich, Germany