This fascinating tool, made by Detroit-based precision tool manufacturer Cogsdill, is called a DBFM (Diamond Burnish Face Mill tool).
It mounts into a standard milling arbor, and each of the posts have a spring-loaded diamond insert in the tip. When the tool comes into contact with the metal workpiece, the springs force the diamonds against it, and it then produces a mirror-like finish. Cnc Machined
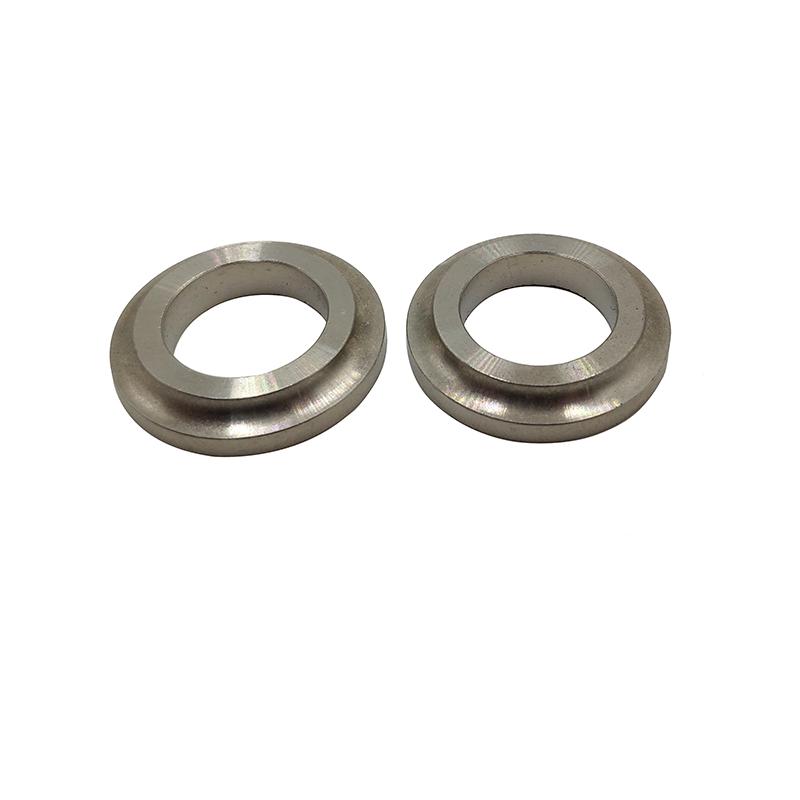
As an example, the top half of the workpiece below shows a merely milled surface, whereas the bottom half has been finished with the DBFM.
Titans of CNC Machining got their hands on a DBFM, and used it to finish a disco ball that they milled out of a chunk of aluminum:
Test it out; it only takes a single click to unsubscribe
Don't have an account? Join Now
Already have an account? Sign In
By creating a Core77 account you confirm that you accept the Terms of Use
Please enter your email and we will send an email to reset your password.
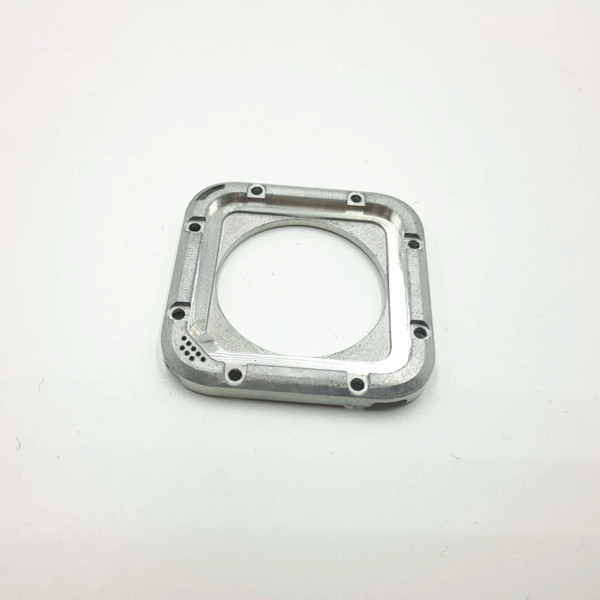
Cnc Machined Parts Test it out; it only takes a single click to unsubscribe