The basis of chaos theory is a key concept known as the “butterfly effect.” It’s the idea that a small event in one place creates a cascading set of events elsewhere. So, how is the EMS landscape changing? We’re tracking the concerns and dynamics of this landscape, and there’s a lot to learn.
In this issue, we examine the profound effect artificial intelligence and machine learning are having on manufacturing and business processes. We follow technology, innovation, and money as automation becomes the new key indicator of growth in our industry. Intelligent multimedia PCBA
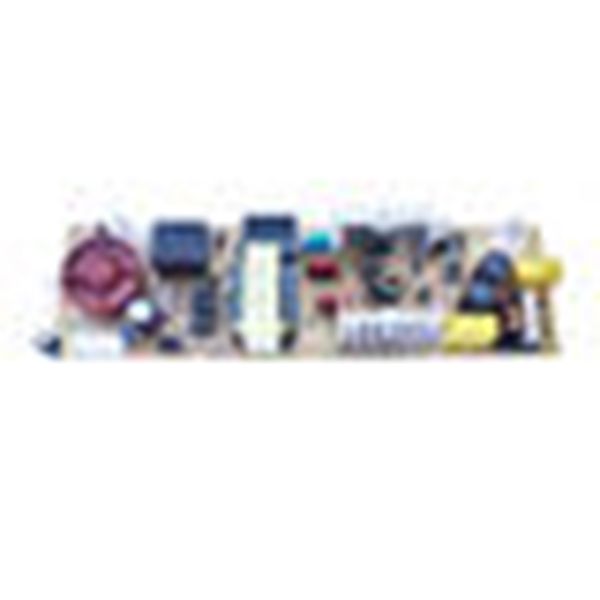
One trend is to add box build and final assembly to your product offering. In this issue, we explore the opportunities and risks of adding system assembly to your service portfolio.
Despite the many technology advances in the SMT process, there will always be a need for rework and repair of PCB assemblies. Most especially as the industry trend continues towards finer pitch and spacing, smaller and smaller components, and increasing high-reliability requirements from customers.
Not to mention that fact that the rework and repair processes are already challenging. You have to deal with already-finished boards, wherein improper soldering may cause collateral damage to around the area that needs rework. So, for this month’s issue of SMT Magazine, we interviewed Dan Patten, general manager, and Laura Ripoli, customer service manager for rework/repair, from BEST Inc.; Gary Freedman, president of Colab Engineering; and Andy Price, sales manager of Circuit Technology Center, to know more about the rework and repair of PCB assemblies, the critical challenges, and strategies to improve the process moving forward.
“We’re always making more densely populated boards and we’re making things smaller and packing more into it and so forth,” says Patten.
Price notes, “From our perspective, some of the most challenging issues that we confront daily tie in with the circuit board design. The spacing is tighter, the boards are thicker and contain heavy copper planes. Those factors along with the RoHS requirements help create many of the challenging issues that we face in trying to rework components. It also increases the challenge in getting complete solder fill in plated holes. Much of it is directly related to the circuit board design. Some of the other factors include rework and repair on boards that have gone through final processing. They may be field returns or failures that are found after conformal coating application, or through the under-fill process at BGA component sites. There’s are many problems that can arise when reworking boards with conformal coating. Often collateral issues to adjacent components can occur if the area is not prepared properly such as starved solder joints, solder shorts and other problems. Those are just a few general thoughts on some rework issues we confront.”
Price notes that board thickness is a challenge. “Years ago, board thicknesses ranged from maybe 0.062” to 0.092”. Now, we’re routinely seeing boards that are 0.125”, and even thicker. There are ground planes involved in the construction of these boards that dissipate heat when you’re trying to remove components. Then you add in the fact that you’re dealing with a higher temperature reflow with RoHS requirements. These are just challenges that we have to deal with. I don’t see it going away. I see it becoming more and more challenging,” he explains. “The prevalent issues that we see with circuit boards that are constructed like that relate to the increased heating requirement. Boards require preheating and complete bake-out prior to rework. A lot more heat is needed in the rework area to achieve reflow temperatures. When more heat is necessary you increase the potential for physical damage to the board to occur. You may see baseboard discoloration or more significant base board damage such as delamination. Increased heat at the rework site can also result in lifted lands, surface mount pads and pulled plated through hole barrels. These are issues that anybody involved in rework will see, the most expert companies will see less of it due to experience but there are some designs that are very difficult to overcome.”
One of the problems that Freedman had seen very often was trying to repair things that don’t need repair on boards, such as barrel fill that doesn’t quite meet IPC spec. “One of the things that I had been driving for years when I was with Digital, Compaq and HP was trying to refine the barrel fill specifications. We have had some success in driving that movement with IPC. If you look at a through-hole solder joint, it’s many times stronger than an SMT solder joint. Yet, we’re happy to pass SMT solder joints with very little solder. When it comes to through-hole, people are so quick to take a soldering iron to it. It might just be the wrong thing to do,” he points out. “What we want to do is minimize the number of heat cycles on a circuit board. Besides the number of heat cycles, we also want to minimize the number of touches. Any time you touch a board, you’re likely to damage it, either through flexure or shearing of parts on the back side, or on the front side, with the soldering iron. Or, I see operators with picks all the time, poking and prodding to see if things are soldered. Like I said, anytime you can minimize the number of touches to a board, you’re better off. I’m one that is much happier to pass a board that doesn’t quite meet IPC than to have it go through a repair cycle. Chances are, the repaired board will be of a lesser reliability.
“A through-hole solder joint is many times stronger than a surface mount solder joint. We get very particular about these massively strong solder joints and yet we’re very willing to pass SMT solder joints that have almost no solder. I certainly understand that there are different mechanics involved in expansion of contraction, etc. We turn a blind eye to SMT, whereas with through-hole we get overly particular. I said that there are two issues: number one is the number of heat cycles we apply to a solder joint. That, in part, defines intermetallic characteristics and reliability. The other thing is the number of touches to a board. Any time a board is subjected to rework, you’re more apt to create damage than if the board is left alone.”
For years, Freedman had done a lot of work on reliability of solder joints, including through-hole solder joints, as well as a lot of modeling and testing of solder joints to revise their specification requirements and to also influence IPC.
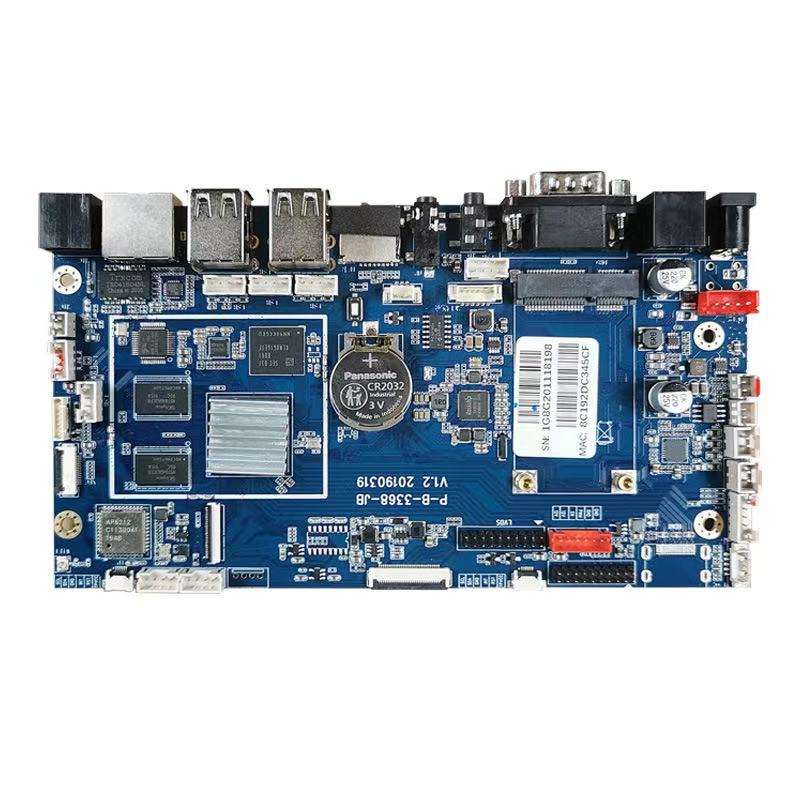
Pcb Pcba Difference “And we have done that to some degree,” he says. “If you have a very thin board, IPC’s very happy with a minimum amount of solder joint. If you have a thick board, they want a very thick solder joint, and yet, if you do the modeling and the reliability testing, you’ll find that even a 20% solder joint in a thick board has more than enough reliability. I’m not advocating that we go down to 20%, but I’m saying let’s get real about what’s actually required. I think we need to move out of the middle ages of soldering in terms of through-hole and consider doing more work in terms of modeling and reliability of the through-hole joint specification.”