Vol. 227 No. 12 New rig designs Chinese land rig uses ac drawworks Last year, SPA China National Petroleum Corp mobilize
Last year, SPA China National Petroleum Corp mobilized the first of two new HH2600ED series rigs built by Honghua Co Ltd. (HH), Fig. 1. Rig No.70-1, a 2,600 hp rig, spudded its first well in Pakistan. A second rig, No. 70E-2, was completed in the third quarter of 2005. The rig is presently working in Huabei oilfield. China Brandt King Cobra Shaker Screen
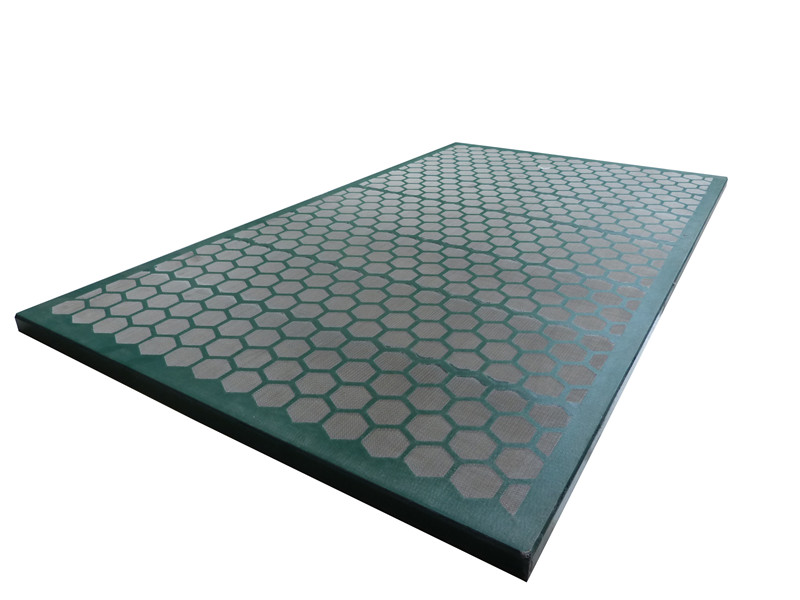
Fig 1. Honghua’s newly built rig No.70E-1, shown in Pakistan, incorporates a newly-designed, substructure swing-up mast.
Rig No.70-1, rated to 23,000 ft, comes with a number of improvements to make it one of the most efficient and advanced land rigs available. It has a newly-designed substructure, drawworks, climate-controlled driller’s cabin, system controls connected through programmable logic controllers and cabling, and other designs to reduce manual labor, optimize processes and performance, and improve safety. The sophisticated data acquisition, storage, processing, and setup system makes automatic and smart drilling possible.
The rig’s HH JC-2600ED drawworks are powered by two YJ31 motors, which are rated to 1,300 hp, Fig. 2. The AC drives provide regenerative braking, and more precise control of the drillstring than conventional SCR-drive systems. Regenerative braking eliminates the need for an auxiliary brake, allowing less weight and a smaller footprint. The hydraulic brake works only for parking, positioning and emergency stop. All parameters including tripping speed, block positioning and auto-bit-feed are digitally controlled.
Fig 2. Honghua equipped the rig with AC drawworks, set down from the rig floor, for easier rig-up and to enlarge rig floor operation area.
The AC technology allows greater control of the drilling process and improves efficiency during tripping operations. A small 40 hp AC motor is used for auto-bit-feed and emergent hoist, if the main motor system breaks down. The sophisticated single-shaft drawworks simplifies the drive and makes for easy maintenance.
HH built the mast and substructure with new designs to ease rig-up and reduce set-up time. The mast and substructure are rated for 1 million-lb load capacity. It incorporates the advantages of swing-up and slingshot substructures with the lower mast section integrated into the substructure.
The drill floor height is 35 ft, which meets the requirements for underbalanced drilling. The independent rotary drive system is integrated in the substructure, making the drillfloor wider and clearer; a 33-ft x 33-ft floor area is available.
The substructure is pinned together at ground level and raised to working position together with the mast. The mast is pinned to the substructure at eight points for stability.
The mast is a 147-ft cantilever type and can carry a Varco TDS-11 500-ton top drive. The poles used for raising the mast and substructure work as a rear part of the structure, when rig-up is completed. This simplifies the substructure and reduces weight.
The HH2600VFD rig uses the Digital Driller (D-Driller) for integrating controls and rig-data monitoring. The driller occupies a single-seat, climate-controlled cabin near the rig floor where he controls the drawworks, rotary table, mud pumps, rig power plants, BOP, and hydraulic catheads with touch-screen computer controls and a joystick. The left joystick controls the AC drawworks’ speed while hoisting, lowering, or holding full load at zero speed. The right joystick is for hydraulic brake control. Redundancy is applied in the control signals and cabling. Self-diagnosing and fail-safe functions improve operational safety. Manual override is available as required.
The system provides steady weight-on-bit while drilling based on downhole conditions and permits control of weight-on-bit and rate of penetration. Compared to a conventional auto-drilling system, which often produces bit-weight fluctuations of 2,000 lb to 3,000 lb, the new system reduces fluctuations to less than 1,000 lb. These developments have improved bit life and penetration rates.
The drilling monitors show views of drilling, tripping and trends. The drilling view monitors WOB, torque, ROP, hook load, pump strokes and pressure, well depth, bit depth, flow rate, and tank volume parameters etc. The tripping view monitors trip tank volume, flow rate, block position, etc. The trend page displays selected functions with graphs and logs that can be stored for backup reference. Other views monitor drawworks-drum spooling, the racking platform, shale shakers and pumps.
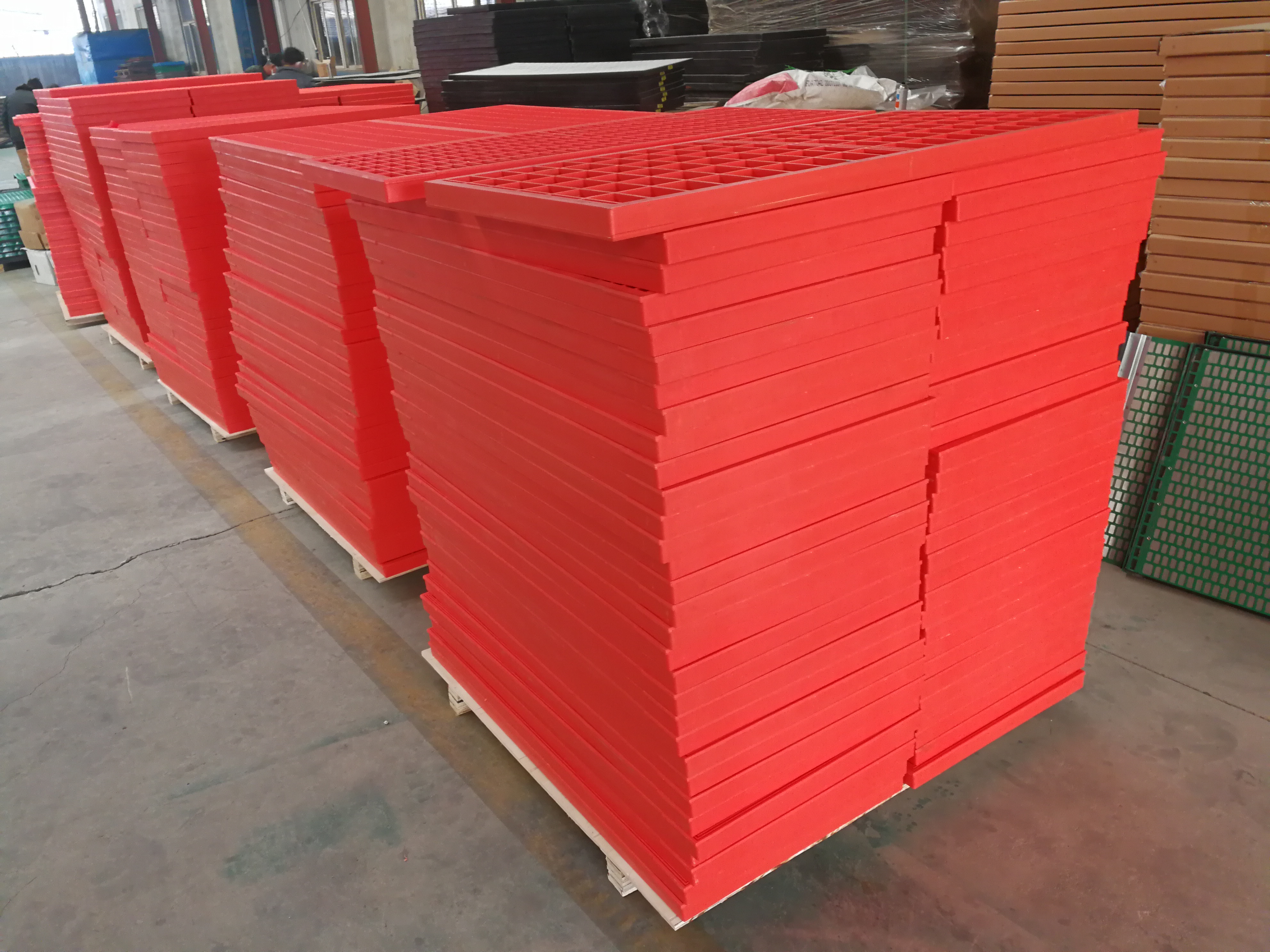
Derrock Each HH2600VFD rig uses a 371D2-in. rotary table, independently powered by an YC23, 800-hp AC motor. This rotary table system replaces the conventional mechanically-powered, vertical-chain rotary drive. Two F-1600 mud pumps are used and are driven by a YC31A, 1,600-hp, AC motor via V-belt drive. Four electronic controlled Caterpillar 3512B generator sets, each rated at 1,200 kW, supply AC power for mud pumps, rotary table, and auxiliary equipment. One Caterpillar electronic controlled 3412E, rated at 400kW, works as the auxiliary generator set.