The wearable robot system supports 5 lbs per hand, weighs under 8.8 lbs, and aids within 2 secs of task start.
Factory worker performing overhead tasks while assisted by the robot. Robot Arm 6 Axis Industrial

Researchers have created a wearable soft robot that can help the shoulder muscles when performing repetitive arm lifts for overhead work.
The team from Harvard University developed a wearable robot that assists only when needed and turns off when not in use. This helps reduce the effort required by the wearer to lower their arms. The robot is worn like a shirt and includes a portable power unit.
Tests with workers showed that industrial tasks with the robot made their shoulder and arm muscles work 40 percent less without making other muscles, like the back muscles, work harder.
The details of the team’s research were published in the journal Science Robotics.
Work-related musculoskeletal disorders are a significant issue, causing nearly 70 million doctor visits annually in the US.
High demands in labor-intensive industries, like lifting arms 4,600 times daily in automotive assembly, contribute to this risk. In 2020, 63,100 shoulder injuries led to a median of 25 days off work, impacting productivity and costs.
According to researchers, while automation and ergonomic aids reduce injury risk, they can be costly and hard to implement. Wearable devices, such as passive shoulder supports, offer versatile solutions.
However, due to resistance, they often increase antagonistic muscle activity. Balancing assistance and resistance in these devices remains a challenge for dynamic tasks.
In contrast, soft active robots offer controllable support with minimal weight and bulk because of the soft materials used in them. As it would switch to gain a position, it can provide the needed support and then power off to not have resistance against the user, preserving natural movement.
Originally intended for medical applications, such robots work efficiently by reducing muscle activity and may find application in industrial work.
Harvard researchers designed and evaluated a portable, soft, inflatable robot for shoulder-elevated industrial tasks. Building on previous work, they developed a portable actuation unit for untethered use and integrated all components into functional apparel.
Their soft, inflatable shoulder robot features two actuators, three inertial measurement units, and a portable actuation unit integrated into wearable apparel. Collaborating with industry partners, it was designed to support 5 pounds (2.3 kilograms) per hand and weigh under 8.8 pounds (4 kilograms). It assists within 2 seconds of starting a task.
Using an advanced kinematics state-machine controller, they conducted experiments simulating common industrial tasks to assess the impact of different assistance timings and pressures on muscle activity and biomechanics.
The team conducted three experiments that analyzed user kinematics, muscle activity, and controller accuracy during overhead tasks. Additionally, researchers compared fixed and modulated assistance during a dynamic holding task, gathering user preferences.
Human participant evaluations during simulated industrial tasks showed the robot reduced agonist muscle activities (anterior, middle, and posterior deltoids and biceps brachii) by up to 40 percent, with minimal changes in joint angles (less than 7 percent range of motion) and no increase in antagonistic muscle activity (latissimus dorsi).
Researchers’ comparisons of controller parameters revealed that higher assistance magnitude and earlier assistance timing led to significant muscle activity reductions.
During a task circuit with dynamic transitions, the robot’s kinematics-based controller demonstrated robustness to misinflations, achieving a 96 percent true negative rate and a 91 percent true positive rate, indicating minimal disturbances to the user when assistance wasn’t needed.
As a final proof of concept, five automotive factory workers also tested the robot in a pilot manufacturing area, providing valuable feedback on its performance during real industrial tasks.
The prototype limitations include the system controller being triggered at fixed angles and pressures and being unsuitable for dynamic tasks. With a small sample size, future work aims to expand evaluations.
According to researchers, participants’ conservative pressure choices may not suit all tasks, suggesting the need for task-specific adjustments. Controller improvements and hardware enhancements are necessary for real-world validation.
Stay up-to-date on engineering, tech, space, and science news with The Blueprint.
By clicking sign up, you confirm that you accept this site's Terms of Use and Privacy Policy
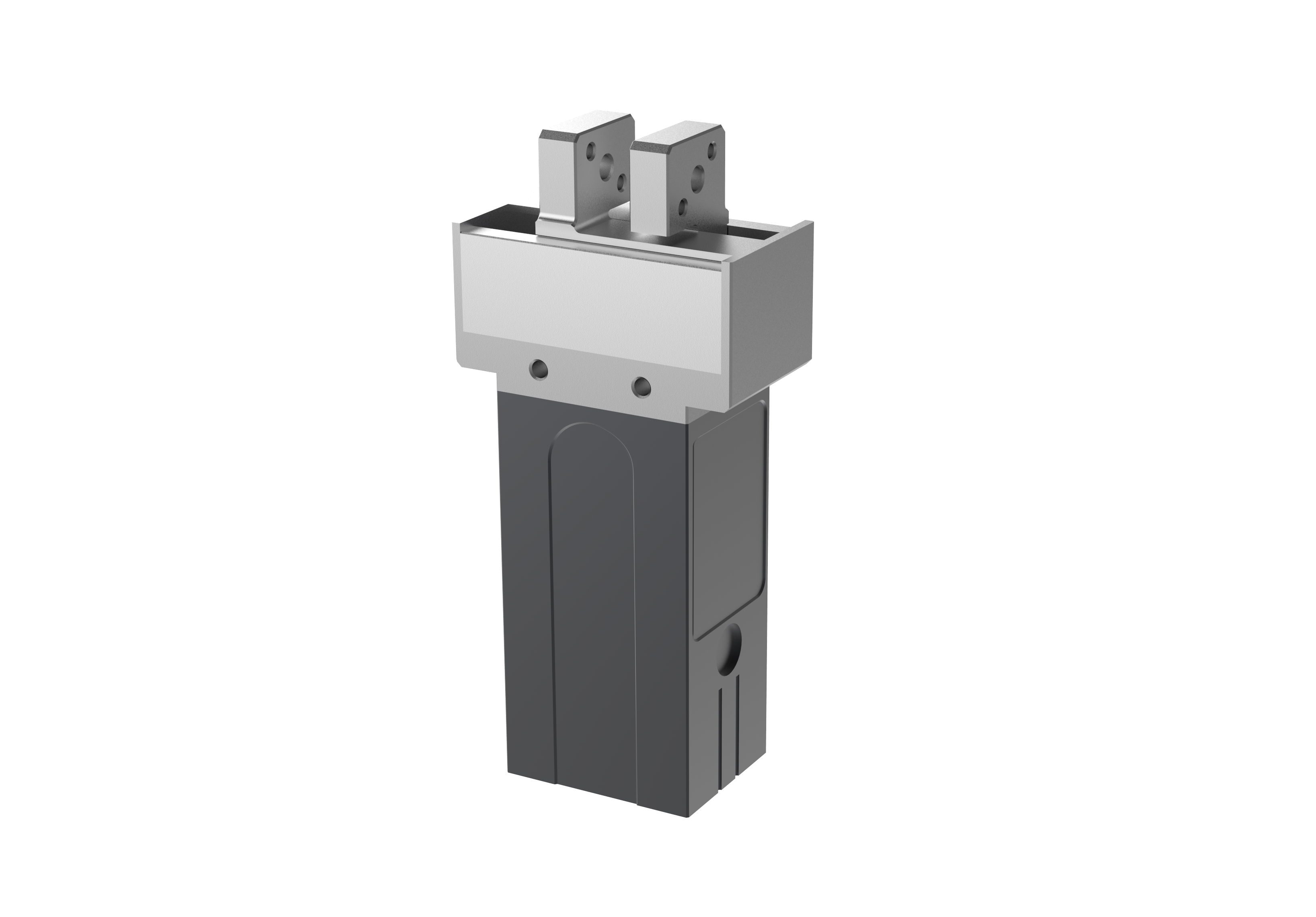
25kg Cobot Jijo Malayil Jijo is an automotive and business journalist based in India. Armed with a BA in History (Honors) from St. Stephen's College, Delhi University, and a PG diploma in Journalism from the Indian Institute of Mass Communication, Delhi, he has worked for news agencies, national newspapers, and automotive magazines. In his spare time, he likes to go off-roading, engage in political discourse, travel, and teach languages.