Blue Ash, Ohio — Milacron Holdings Corp. will close a DME mold base plant in western Pennsylvania and move it to a DME factory in Greenville, Mich.
Milacron told the 63 employees at Youngwood, Pa., about the decision on March 17, and made a public announcement on March 20. The move will happen late this summer, officials said. Plastic Mould Factory
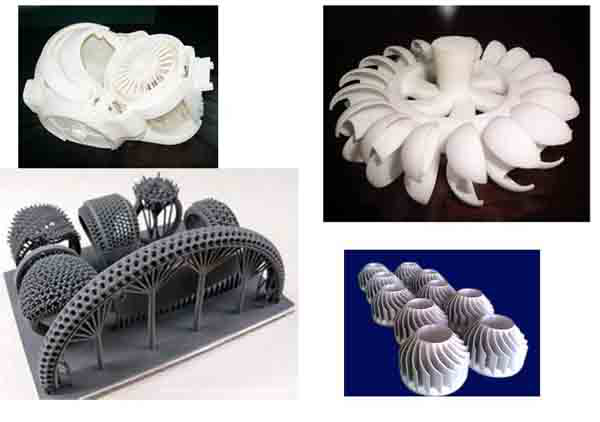
Where possible, Milacron will offer to relocate the Youngwood employees for available positions across all the company's sites, including Greenville, it said.
Pete Smith, president and general manager at DME, said Greenville will be the single U.S. operation for DME, which makes mold bases and mold components. By doing that: "We can direct our investment funds to build a new world class site at Greenville.
"Youngwood had, for many decades, been key in DME's mold base manufacturing in North America but with the introduction of new manufacturing technologies and the continued migration of mold manufacture overseas the facility was no longer able to compete cost-effectively," Smith said.
Youngwood is near New Stanton and Greensburg, Pa.,
Milacron is based in Blue Ash, a suburb of Cincinnati.
Do you have an opinion about this story? Do you have some thoughts you'd like to share with our readers? Plastics News would love to hear from you. Email your letter to Editor at [email protected]
Please enter a valid email address.
Please enter your email address.
Please select at least one newsletter to subscribe.
Staying current is easy with Plastics News delivered straight to your inbox, free of charge.
Plastics News covers the business of the global plastics industry. We report news, gather data and deliver timely information that provides our readers with a competitive advantage.

Ceramic Mold Making 1155 Gratiot Avenue Detroit MI 48207-2997