LEGO is one of the world's most recognisable products, but how is it made?
Since production of the LEGO block in 1949, the design hasn't changed and is available in 53 colours. Best Brick Machine
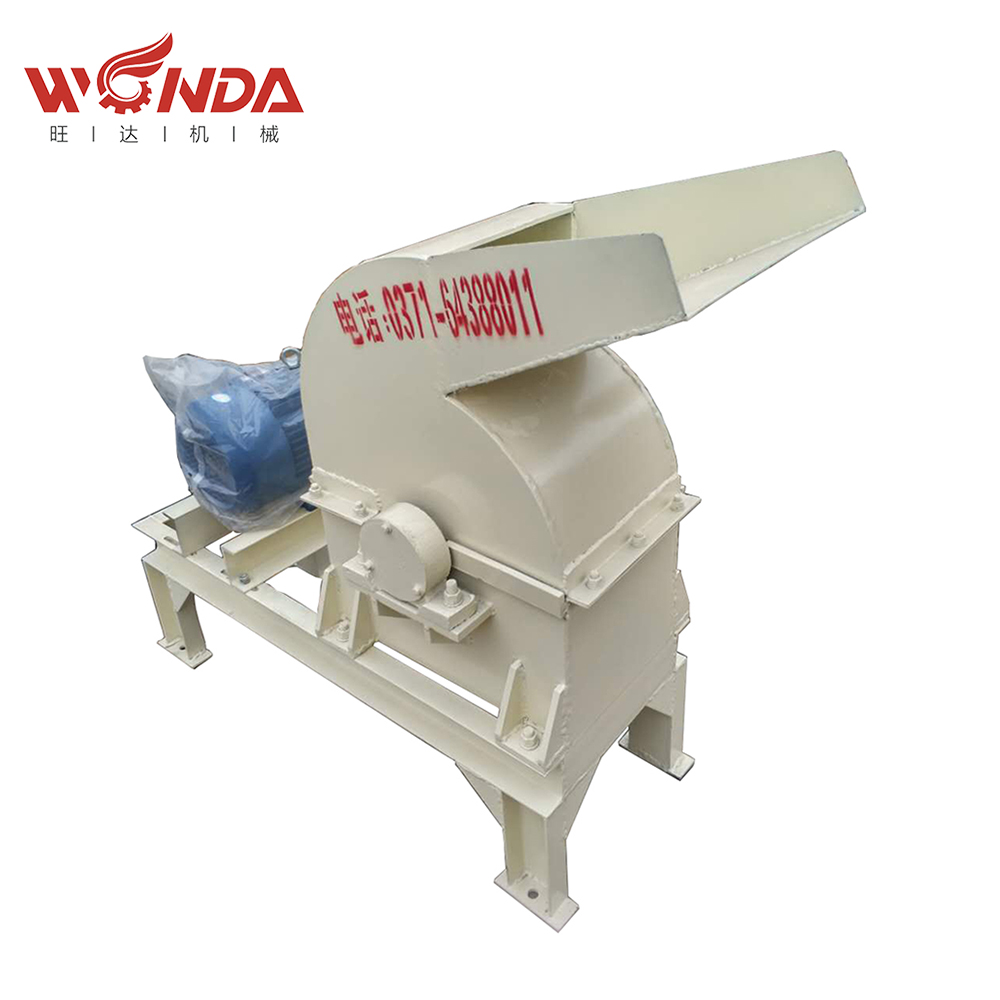
The blocks are made of a plastic granulate, which is melted and pressed in a moulding machine which creates the LEGO shape.
Automatic guided vehicles then collect and deliver the bricks to the warehouse, where they are sorted, weighed and then packed for delivery.
Watch the video to see how it is done.
Produced by David Ibekwe. Special Thanks to LEGO
LEGO is one of the world's most recognisable products, but how is it made?
Since production of the LEGO block in 1949, the design hasn't changed and is available in 53 colours.
The blocks are made of a plastic granulate, which is melted and pressed in a moulding machine which creates the LEGO shape.
Automatic guided vehicles then collect and deliver the bricks to the warehouse, where they are sorted, weighed and then packed for delivery.
Watch the video to see how it is done.
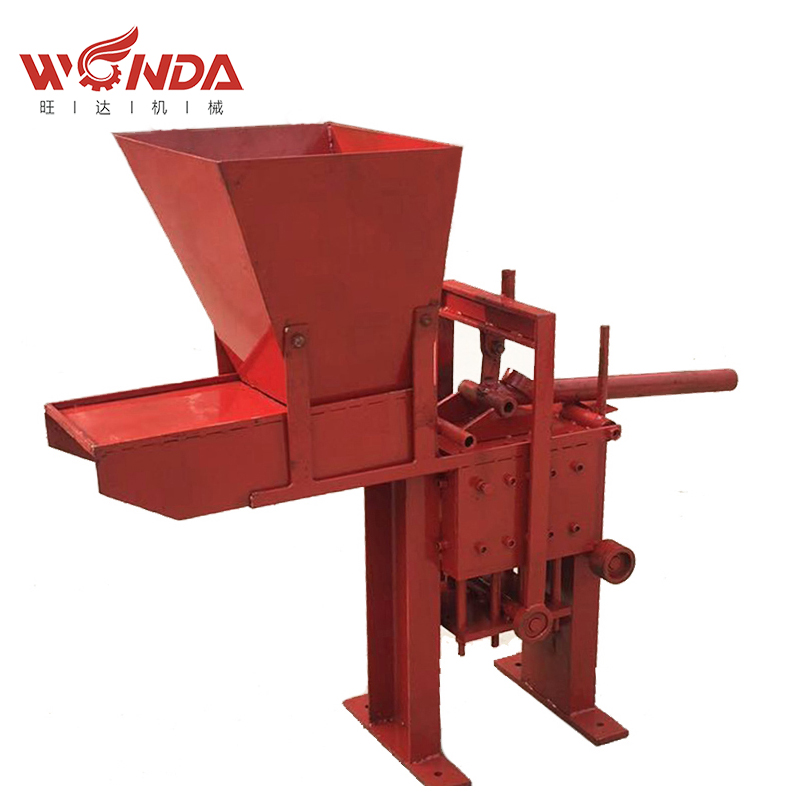
Automatic Clay Brick Making Machine Produced by David Ibekwe. Special Thanks to LEGO