A 360-degree look at resin conveying systems: types, operation, economics, design, installation, components and controls.
This Knowledge Center provides an overview of resin moisture and the drying process, including information on the best drying practices for your manufacturing facility. Pelletizing Production Control System
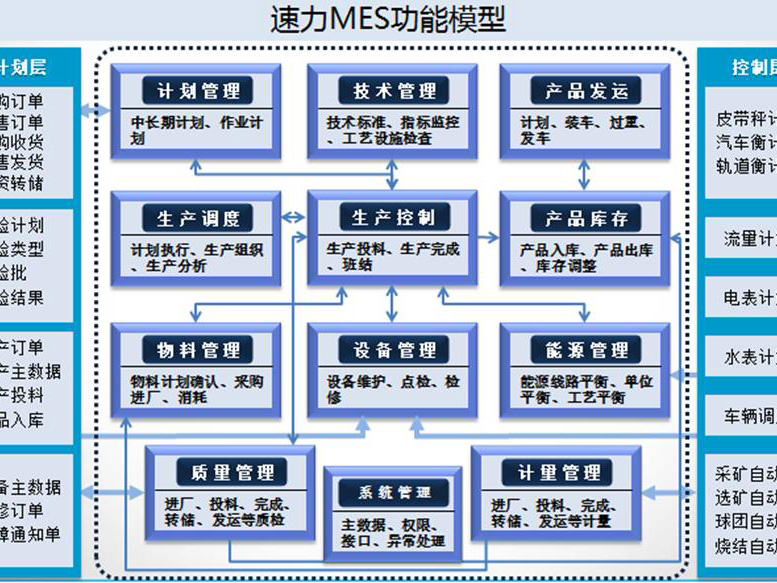
Combat the skilled labor shortage using this comprehensive resource to train your own plastics processing experts.
Deep dive into the basics of blending versus dosing, controls, maintenance, process integration and more.
This Knowledge Center provides an overview of the considerations needed to understand the purchase, operation, and maintenance of a process cooling system.
Learn about sustainable scrap reprocessing—this resource offers a deep dive into everything from granulator types and options, to service tips, videos and technical articles.
Despite price increase nominations going into second quarter, it appeared there was potential for generally flat pricing with the exception of a major downward correction for PP.
First quarter was ending up with upward pricing, primarily due to higher feedstock costs and not supply/demand fundamentals.
Despite earlier anticipated rollover in prices for most of the volume commodity resins, prices were generally on the way up for all going into the third month of first quarter.
While price initiatives for PE and PVC were underway, resin prices had rollover potential for first two months of 2024, perhaps with the exception of PET.
Flat-to-downward trajectory for at least this month.
A mixed bag, though prices likely to be down if not flat for all this month.
Resin drying is a crucial, but often-misunderstood area. This collection includes details on why and what you need to dry, how to specify a dryer, and best practices.
Take a deep dive into all of the various aspects of part quoting to ensure you’ve got all the bases—as in costs—covered before preparing your customer’s quote for services.
In this collection of articles, two of the industry’s foremost authorities on screw design — Jim Frankand and Mark Spalding — offer their sage advice on screw design...what works, what doesn’t, and what to look for when things start going wrong.
In this collection, which is part one of a series representing some of John’s finest work, we present you with five articles that we think you will refer to time and again as you look to solve problems, cut cycle times and improve the quality of the parts you mold.
Gifted with extraordinary technical know how and an authoritative yet plain English writing style, in this collection of articles Fattori offers his insights on a variety of molding-related topics that are bound to make your days on the production floor go a little bit better.
In this three-part collection, veteran molder and moldmaker Jim Fattori brings to bear his 40+ years of on-the-job experience and provides molders his “from the trenches” perspective on on the why, where and how of venting injection molds. Take the trial-and-error out of the molding venting process.
Mike Sepe has authored more than 25 ANTEC papers and more than 250 articles illustrating the importance of this interdisciplanary approach. In this collection, we present some of his best work during the years he has been contributing for Plastics Technology Magazine.
In this collection of content, we provide expert advice on welding from some of the leading authorities in the field, with tips on such matters as controls, as well as insights on how to solve common problems in welding.
Mold maintenance is critical, and with this collection of content we’ve bundled some of the very best advice we’ve published on repairing, maintaining, evaluating and even hanging molds on injection molding machines.
Thousands of people visit our Supplier Guide every day to source equipment and materials. Get in front of them with a free company profile.
There are many fundamental differences between thermosets and thermoplastics, from the way raw materials are furnished to the molder and the process in which parts are molded.
It’s all about sustainability and the circular economy, and it will be on display in Orlando across all the major processes. But there will be plenty to see in automation, AI and machine learning as well.
Polymer Resources responds to sustainability push by upgrading plant with grinding and shredding equipment to take on both postindustrial and postconsumer reclaim.
First quarter was ending up with upward pricing, primarily due to higher feedstock costs and not supply/demand fundamentals.
An integral supplier in the effort to fast-track COVID-19 vaccine deployment, Retractable Technologies turned to Arburg and its PressurePilot technology to help deliver more than 500 million syringes during the pandemic.
Megatrends such as sustainability are the driving force behind a slew of new product introductions at the May show. Catch up on what’s in store on the show floor right here.
With frequent purging, you can minimize serious contamination issues and get both better results and higher profits.
Realtime Robotics seeks to get more robots involved in manufacturing by addressing the biggest current barrier: programming costs.
Offerings range from recycled, biobased, biodegradable and monomaterial structures that enhance recyclability to additives that are more efficient, sustainable and safer to use.
Understand the differences between distributive and dispersive mixing, and how you can promote one or the other in your screw design.
Topping five other entries in voting by fellow molders, the Ultradent team talks about their Hot Shots sweep.
Serendipitous Learning Opportunities at PTXPO Underscore the Value of Being Present.
Introduced by Zeiger and Spark Industries at the PTXPO, the nozzle is designed for maximum heat transfer and uniformity with a continuous taper for self cleaning.
Ultradent's entry of its Umbrella cheek retractor took home the awards for Technical Sophistication and Achievement in Economics and Efficiency at PTXPO.
technotrans says climate protection, energy efficiency and customization will be key discussion topics at PTXPO as it displays its protemp flow 6 ultrasonic eco and the teco cs 90t 9.1 TCUs.
Shibaura discusses the upcoming Plastics Technology Expo (PTXPO) March 28-30
NPE2024: Mechanically actuated gum space adjustment requires only ordinary socket wrench.
Dr. Walter Kaminsky’s pioneering research on metallocene catalysts at the University of Hamburg sparked a global revolution in plastics production. Inducted into the Plastics Hall of Fame in 2024, Kaminsky’s legacy continues to shape the polyolefin industry and plastic recycling technologies.
Wolfgang Meyer, a German mechanical engineer and industry leader whose contributions to plastics machinery have shaped the industry. Inducted into the Plastics Hall of Fame in 2024, Meyer’s work in injection molding, blow molding and sustainability has left an enduring legacy.
Paulson has four in-booth stations demonstrating its various training solutions.
Member of PLASTICS for more than 40 years served on several committees and boards since 2005, including a stint as chairman.
NPE2024: Medical, inmold labeling, core-back molding and Industry 4.0 technologies on display at Shibaura’s booth.
Mixed in among thought leaders from leading suppliers to injection molders and mold makers at the 2023 Molding and MoldMaking conferences will be molders and toolmakers themselves.
After successfully introducing a combined conference for moldmakers and injection molders in 2022, Plastics Technology and MoldMaking Technology are once again joining forces for a tooling/molding two-for-one.
Multiple speakers at Molding 2023 will address the ways simulation can impact material substitution decisions, process profitability and simplification of mold design.
When, how, what and why to automate — leading robotics suppliers and forward-thinking moldmakers will share their insights on automating manufacturing at collocated event.
As self-imposed and government-issued sustainability mandates approach, injection molders reimagine their operations.
August 29-30 in Minneapolis all things injection molding and moldmaking will be happening at the Hyatt Regency — check out who’s speaking on what topics today.
Get your clicking finger in shape and sign up for all that we have in store for you in 2023.
Molding 2023 to take place Aug. 29-30 in Minnesota; Extrusion 2023 slated for Oct. 10-12 in Indiana.
Discover possible applications in large format printing including layup tools, transport modules, film fixation devices, design components and enclosures. These are used in various industries such as automotive, aerospace, architecture and many others. Agenda: Possible applications in large format printing: layup tools, transport modules, film fixing devices, design components and enclosures. Process reliability and component quality in component production Pros and cons of the technology Sneak peek into current development projects—What will the large format printing of tomorrow look like?
Cooling time is typically the longest step of the molding process. How can you make it more productive? Learn how cooling time can be turned into production time by running two molding processes simultaneously on a single molding machine. For longer cycles, this can mean twice the productivity. In this webinar, you'll learn more about the Shuttle Mold System and how to calculate its potential productivity impacts for your application. Agenda: Learn how the Shuttle Mold System can deliver value to your business See the recent technical updates made to the system Calculate the potential impact on productivity
Finding it hard to get technical talent? Experiencing the pain of a knowledgeable, long-term employee's retirement? Learn how plastics processors are training generative AIs on their operations and unlocking the value from their tribal knowledge. Plastics processors are training generative AI models on their operations — from machine manuals to tools, polymers, procedures, maintenance records and engineering projects. Applying generative AI in the right ways can lower plastics processors' costs, improve overall equipment effectiveness (OEE) and upskill teams. In this webinar, you'll learn how to deploy AI technical assistants to your teams, what works and what doesn't, and how to use AI to build an organization that never loses tribal knowledge and fosters inter-team collaboration. Agenda: What is generative AI and how can its cognitive abilities be applied to plastics? Case study: how an injection molder trained a large language model on manuals and maintenance records to reduce downtime Case study: using generative AI in engineering teams to improve product development Live demonstration of a generative AI deep-trained on plastics knowledge Looking to the future: five predictions for an AI-augmented workforce in plastics
Turnaround time can be as low as 24 hours, although two or three days might be more typical. Rapid prototyping like this is especially useful to quickly identify critical end-use part geometries that will work in the molding process. Key components include material choice, 3D printing technology selected, use of adaptable mold bases for the mold inserts and implementation of appropriate injection molding process conditions. This presentation will review work conducted toward the assessment of a high-stiffness, high-temperature-resistant ceramic modified urethane acrylate for injection molding inserts. Agenda: Guide for 3D-printed injection mold inserts Optimization of digital light processing (DLP) printing Compatibility with various thermoplastics Real-world application success stories
Tony will address common challenges encountered at each stage and provide invaluable insights to effectively navigate these obstacles. Agenda: Bridging the gap between color and appearance: learn how to achieve harmony between the intended color and the final appearance of your plastic products. Importance of using a data-driven color management model: color measurement technology provides valuable insights and analytics that enable plastic manufacturers to optimize color formulations, troubleshoot color inconsistencies, enhance operational efficiency and drive continuous improvement in their production processes. Choosing the right toolset: gain insights into selecting the most suitable technology and processes tailored to your workflow and specific needs.
Innovative closures at the forefront of this trend have fostered a tooling evolution that enables cost-effective manufacturing of lightweight designs. Find out more about why global beverage brands are switching closures, specific design best practices and the significant merits of a mono-material package solution. Join this webinar to find out how these production changes can enable you to reach your sustainability goals and drive business growth. Agenda: The trend toward lightweight beverage closure designs The advantages of lightweight and tethered closures Why beverage brands are implementing tethered solutions even in the absence of mandates Tooling design best practices to mold today’s ultra-lightweight closure designs The merits of a mono material package solution
Every three years, leaders from almost every major industry gather at NPE to advance their businesses through innovations in plastics. The largest plastics trade show in the Americas, NPE offers six technology zones, keynote speakers, workshops and opportunities to build partnerships.
The 3D Printing Workshop @ NPE2024 – The Plastics Show, is an immersive, half-day workshop focused on the emerging possibilities for part production via 3D printing and additive manufacturing. Presented by Additive Manufacturing Media, Plastics Technology and MoldMaking Technology, the 3D Printing Workshop will build upon a successful model first introduced at IMTS 2014. Attendees will benefit from a program focused on practical applications of 3D technologies related to plastics processing. This event will conclude with a 3D Printing Industry Reception sponsored by Additive Manufacturing Media.
The Society Plastics Engineers (SPE) Extrusion Division and the SPE Eastern New England Section will co-host the Screw Design Conference-Topcon on June 19-20, 2024 @ UMass Lowell in Lowell, MA. This highly technical program will focus upon screw design principles for single and twin screw extruders with wide ranging topics relating to screw designs for feeding, melting, mixing, venting and pumping plastics products and parts. Areas of focus will include screw designs for melt temperature and gel management, gel minimization, bioplastics, recycled materials and foaming. In addition to the technical sessions, a tour of the UMass Lowel Plastics Processing Laboratories will be integrated into Day 2 of the event. This program is not just for screw designers, but to help anyone responsible for any type of extrusion operation to evaluate existing extrusion equipment; and also to prepare for future projects. Price to attend: Less than $1000! Registrations will be accepted in early 2024. Call for papers – To be considered to give a presentation, please submit a talk title and abstract on or before December 15 to: Technical Chair: Eldridge M. Mount III, e-mail emmount@msn.com Corporate sponsorships - A limited # of corporate sponsorships (15) are available on a 1st come basis. Included is a 6’ tabletop display (must fit on table), denotation in all promotional activities, and 1 no charge registration. To become a sponsor contact: Charlie Martin, Leistritz Extrusion, e-mail cmartin@leistritz-extrusion.com, cell 973-650 3137 General information: A reception on Day 1 and a tabletop display area will allow the attendees to meet and discuss state-of-the-art screw technologies with industry experts. The SPE Extrusion Division will issue a “Screw Design Certificate” to all participants who have attended the program. Students are encouraged to attend and will receive a discounted rate. For additional information contact: Program Chair: Karen Xiao, Macro Engineering, KXiao@macroeng.com
Debuting in 2010, the Parts Cleaning Conference is the leading and most trusted manufacturing and industrial parts cleaning forum focused solely on delivering quality technical information in the specialized field of machined parts cleansing. Providing guidance and training to understand the recognized sets of standards for industrial cleaning, every year the Conference showcases industry experts who present educational sessions on the latest and most pressing topics affecting manufacturing facilities today. Discover all that the 2022 Parts Cleaning Conference has to offer!
Presented by Additive Manufacturing Media, Plastics Technology and MoldMaking Technology, the 3D Printing Workshop at IMTS 2024 is a chance for job shops to learn the emerging possibilities for part production via 3D printing and additive manufacturing. First introduced at IMTS 2014, this workshop has helped hundreds of manufacturing professionals expand their additive capabilities.
Formnext Chicago is an industrial additive manufacturing expo taking place April 8-10, 2025 at McCormick Place in Chicago, Illinois. Formnext Chicago is the second in a series of Formnext events in the U.S. being produced by Mesago Messe Frankfurt, AMT – The Association For Manufacturing Technology, and Gardner Business Media (our publisher).
Cooling specialist Addex to roll out new auto-profiling air ring for rotating dies, and new single-plenum air ring.
Addex is taking the wrap off two new products for blown film cooling at NPE2024, May 6-10, in Orlando, Florida, Plastics Technology has learned exclusively.
One is an auto-profile system for rotating dies, based on its high-resolution EGC (external gauge control) air ring, that’s capable of reducing gauge variation by 50%. It’s already in operation on a single-layer line at a Crayex plant in Georgia, and at another undisclosed film processor in South Carolina. While rotating dies are perceived by some as passé, the fact is there are many still in operation, according to Addex CEO Bob Cree, particularly on blown film lines making stretch films. Cree adds, “We see them operating in companies big and small. And many companies running rotating dies think the only way they can improve thickness variation is to buy a new line.”
The new air ring system operates similarly to Addex’s gauge-controlling EGC-based systems, which are commonly found on stationary dies, but with several added enhancements. Addex previously was able to achieve industry standard (for a stationary die) 50% reduction in gauge variation on rotating dies only by combining the EGC system with its internal bubble cooling (IBC)-based cousin, the Internal Gauge Control (IGC).
At NPE2024, Addex will debut a new External Gauge Control air ring for blown film applications utilizing rotating dies. A 12-in. air ring will have as many as 168 control zones. “Fingers” open or close to direct more or less cooling air to specific locations on the bubble as needed. Source: Addex
But with the new system, the IGC is no longer required. This significantly cuts the cost of a system down to the same range as conventional systems on stationary dies, but with the same performance achieved with the IGC add-on.
In the new air ring, air volume is controlled by a series of “fingers” that open or close to put more or less cooling air on the film, which thickens or thins the film out. On a 12-inch air ring, there are 168 control zones, with 200+ control zones on larger systems. But the real key to this new technology is a proprietary mapping algorithm. When combined with Addex’s third-generation controller, software and hardware package, the system regulates not only the air ring but also the die rotation.
Explains Cree, “On lines with oscillating haul-offs, the film is turning at the top, creating a twist that most processors have heard about, but in this case the die is fixed. It’s easier to make proper adjustments if the die is stationary, but rotating dies add another dimension to the auto-profile process that throws a huge monkey wrench into algorithm calculations.”
Adds Gautam Jagannathan, Addex’s software specialist and senior field service engineer, “Our control algorithm now has to compensate not only for the twist but also the die rotation, which turned out to be a serious mind-bender. The industry standard mapping capability is ±5 degrees for stationary dies, but we are getting ±1 degree of mapping even on rotating die systems, including both the twist and the die rotation, and that’s something that nobody else can do.”
Addex’s first foray into auto-profiling for blown film dates back to the 1990s, when it installed a system at a blown film processor that was using the company’s IGC. At that time, Cree recalls, “The control algorithms for the IGC were different from today’s EGC, so when we combined the two systems, it was a very difficult task to get them to work together without fighting each other, but ultimately we effectively reduced thickness variation by 50% on rotating dies.”
“Our goal here for rotating die was to try to hit the 50% reduction in gauge variation.”
He adds, “But it was quite expensive for the customer and was complicated for Addex to program. The customer had to buy two auto profiles, and you can imagine the math of trying to figure out how to separate those two control algorithms from each other. It was a problem, and we stopped doing it. But we knew there was an opportunity because of the number of rotating dies still in the market and the fact that other OEMs were having limited success putting auto profiling on these lines.”
So, about two years ago, Addex began talking with blown film processors with rotating dies that needed to improve film quality but couldn’t justify investing in a brand-new line to do so. “We kept hearing from our customers that they needed more quality from the lines they had —that because of the quality push in the industry and the move toward sustainability, they needed to get better film without breaking the bank. One of my biggest customers has a lot of rotating dies, so we were motivated, and we dusted off all of our old notes to take a fresh look at the problem, and installed our first auto-profiling EGC air ring-only system (no IGC) on a rotating die line at the plant in South Carolina last March. And the feedback from them was that the quality improvement was dramatic.”
Last December, Addex retrofitted its External Gauge Control air ring on this line at film processor Crayex, which runs rotating dies.
Jagannathan, who started up that system, adds, “Our goal here for rotating die was to try to hit the 50% reduction in gauge variation. I don’t think previous auto-profile, air-ring technologies from other vendors for rotating dies were anywhere near 50%; maybe 20-25%. But we’re seeing 50%.” And, as Cree notes, on top of boosting quality reducing film-thickness variations, this result also cuts material costs and provides a pathway for a film processor to meet its sustainability goals.
Addex, however, learned something significant on this first retrofit in South Carolina that they applied to the second, more recent system installation at Crayex in Georgia, which took place in December 2023. For the South Carolina film processor, Addex basically integrated the auto-profile air ring into the processor’s existing die rotator. But the modularity of its Gen3 control package enabled Addex to go a step further with Crayex.
Jagannathan states, “So now we are taking control of the die movement in concert with what we’re doing with the traditional mapping, and that is the system we installed at Crayex.” Jagannathan says that because of the next-generation control technology, the Crayex line appears to be outperforming the line at the South Carolina processor.
Cree adds that the South Carolina processor has ordered two more air rings now with the third-generation control package. The first of these will start up in March. In addition to the two units already in the field, Addex is beta testing the Generation 3 EGC air ring systems at a total of four locations, tweaking the technology to enhance its performance with each startup.
Fillm processor Crayex drastically reduced thickness variations once the Addex gauge-controlling air ring was installed.
Adds Bill Wilck, Addex’s production manager, “The compact Gen3 controller is really simple and easy to work with — it’s no bigger than a small bread box — and it’s also modular, so we can mix-and-match modules with capabilities to not only control the rotation of the die but also to monitor for bubble breaks, inflate/deflate the tube (for non-IBC lines) or even control the IBC.”
At NPE2024, Addex will also debut its first-ever air ring with a single-inlet plenum design. While multi-inlet air rings have conventionally outperformed their single-inlet counterparts because they provide more uniform air distribution, Addex got input from film processors that running just one hose rather than the 4, 6, 8 or 10 that are typical of multi-plenum designs would be beneficial.
Says Josiah Austin, Addex’s mechanical and field service engineer, “With air rings being height-adjustable to help generate more output, it becomes imperative you get rid of all the hoses because it can be a nightmare pulling all of them up and down. Also, we have been supplying air rings to other machine builders and they like the line to look as neat as possible. So, we figured it would be really nice if we could clean that area up.”
Image shows the internal design of Addex’s new single-plenum design to more uniformly distribute air flow. Notice one circular channel flowing clockwise all around, and a second going in the opposite direction all the way around.
Single-inlet air rings can be especially troublesome on lines without automatic thickness control. Cree says, “Automatic units can compensate for any gauge variations caused by erratic air-flow distribution, and you can actually see the required inlet related compensating control effects in the system, so lacking automatic profile control can be a problem.”
So Addex set a goal to design a single-inlet plenum that performed equal to what it had achieved with its multi-inlet conventional plenum. Its solution was to apply a regular division design inspired by Dutch artist M.C. Escher, in which irregular shapes, or combinations of shapes, interlock completely to cover a surface or plane. According to Cree, what Addex devised is a patent-pending, dual-counterflow plenum design with one circular channel flowing clockwise all around, and a second going in the opposite direction all the way around. This creates the Escher “equal and opposite” effect, resulting in uniform combined air flowing through the air ring.
Wilck adds, “Most other single-inlet plenums are shaped like a Nautilus: machined in a spiral that starts off big, gets smaller as it goes around, and is smallest at the very end. But because of all of the constantly changing radiuses, these types of plenums can be extremely expensive to make. In fact, it’s actually so expensive to make the plenum that way that it has made the single-plenum air rings significantly more expensive compared to multiple-plenum ones. The channels in this new design are round, therefore it becomes much easier to make.”
New air ring from Addex has a single-inlet plenum, eliminating the problem moving multiple hoses up and down to accommodate height-adjustable units.
At its pilot line in Newark, N.Y., Addex switched between the new single-inlet design and the multi-inlet unit, both without auto-gauge control, and notes the single-inlet plenum provided better overall thickness profile with reduced variability. “This was unexpected, and it also appeared to create less turbulence with better bubble stability,” Austin adds. “With multi-inlet plenums, you have inlet hitting another inlet, hitting another inlet, and you get repeating cases of internal turbulence. In addition, the hose length and bend variations also common to multi-inlet plenums are all gone with the single-inlet plenum, so this coupled with the equal and opposite flows leads to significantly better overall performance.”
And as with all sciences, there are fundamentals that must be considered to do color right. Here’s a helpful start.
Understanding how polymer melts in a single-screw extruder could help you optimize your screw design to eliminate defect-causing solid polymer fragments.
You rightfully worry about melt temperature, but don’t overlook head pressure, because the two are closely linked and will influence line performance.
Just like selecting the extruder size and drive combination, the L/D should be carefully evaluated.
Extruder screws and barrels will wear over time. If you are seeing a reduction in specific rate and higher discharge temperatures, wear is the likely culprit.
Understanding how polymer melts in a single-screw extruder could help you optimize your screw design to eliminate defect-causing solid polymer fragments.
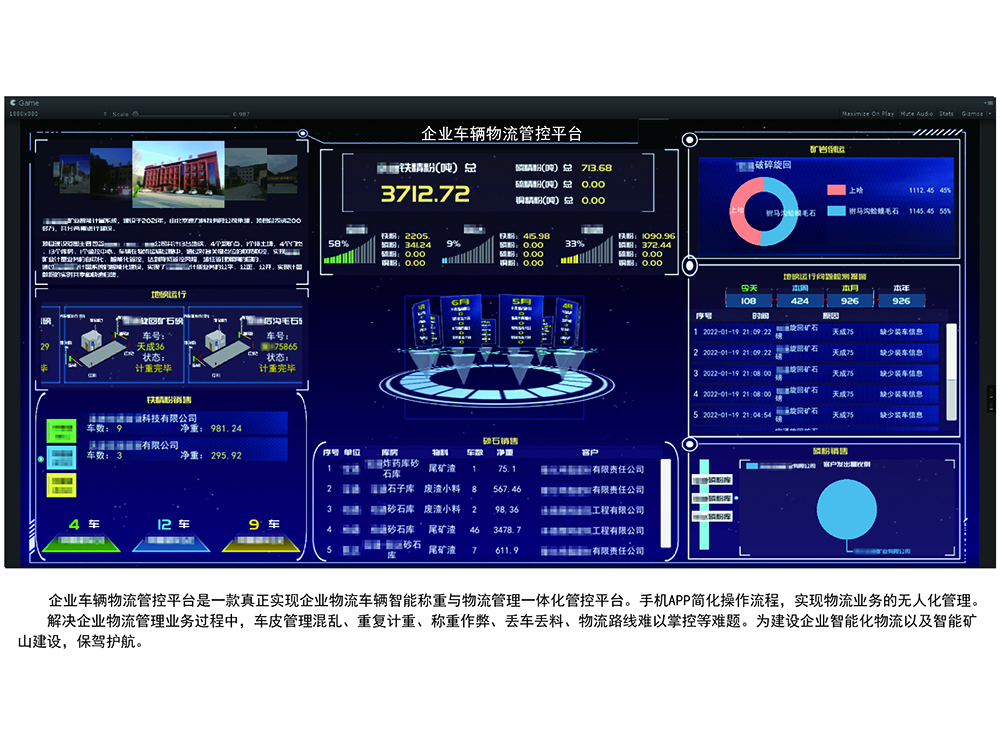
MES System Plastics Technology covers technical and business Information for Plastics Processors in Injection Molding, Extrusion, Blow Molding, Plastic Additives, Compounding, Plastic Materials, and Resin Pricing. About Us