image: Watch a short Q&A video about this research on YouTube. view more
Watch a short Q&A video about this research on YouTube. WPC (Wood And Plastic Composite) Outdoor Decking
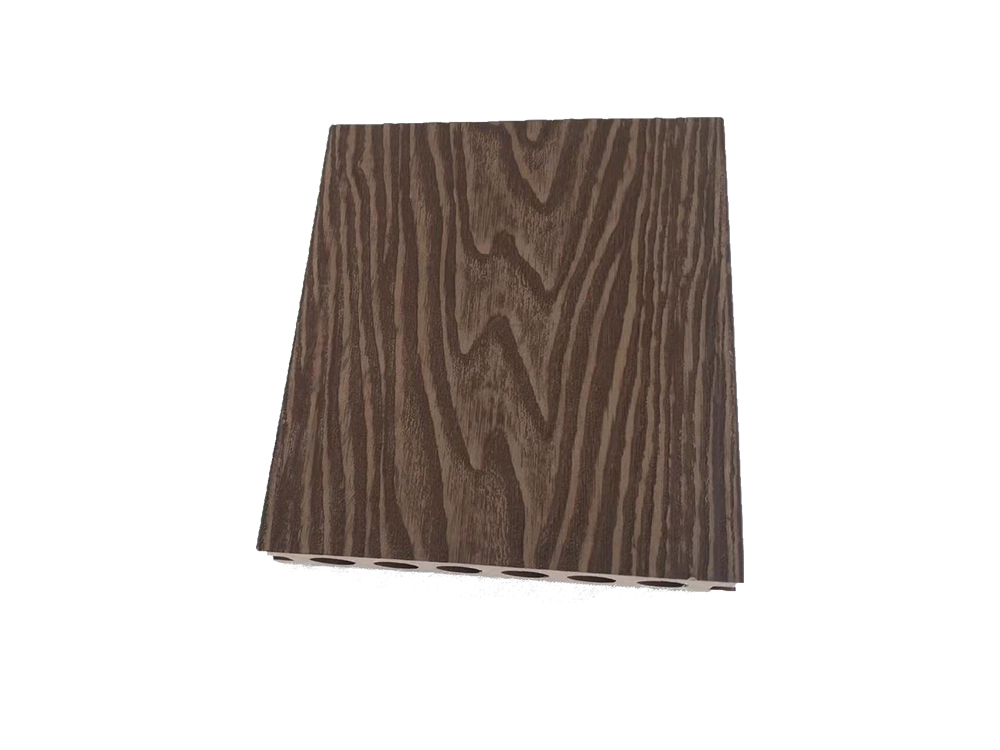
NEW ORLEANS, March 18, 2024 — Buildings and production of the materials used in their construction emit a lot of carbon dioxide (CO2), a potent greenhouse gas that contributes to global warming and climate change. But storing CO2 in building materials could help make them more environmentally friendly. Scientists report that they have designed a composite decking material that stores more CO2 than is required to manufacture it, providing a “carbon-negative” option that meets building codes and is less expensive than standard composite decking.
The researchers will present their results today at the spring meeting of the American Chemical Society (ACS). ACS Spring 2024 is a hybrid meeting being held virtually and in person March 17-21; it features nearly 12,000 presentations on a range of science topics.
Apart from a few types of cement, carbon-negative composites are scarce, according to David Heldebrant, an organic chemist who is one of the project’s principal investigators. The composite decking his team has developed “is one of the first composite materials to be demonstrably CO2 negative over its life cycle,” he says.
The materials and processes that go into constructing buildings account for 11% of all energy-related carbon emissions, according to the World Green Building Council. Significant efforts have gone into developing building supplies that can offset these emissions, such as using recycled or plant-derived products. However, in many cases, these sustainable alternatives are more expensive than traditional materials or can’t match their properties, such as strength or durability.
One type of construction material — decking — is a multibillion-dollar industry. Decking boards made from a wood plastic composite are a popular alternative to lumber boards because they are less prone to damage from ultraviolet radiation and can last longer. Composite decking is typically made from a blend of wood chips or sawdust and plastic, such as high-density polyethylene (HDPE). To make these composites more sustainable, one alternative is to use fillers that are waste products or would otherwise be burned.
That’s an approach Heldebrant’s colleague Keerti Kappagantula was taking: using low-quality brown coal and lignin, a wood-derived product left over from papermaking, as the filler in decking composites. To make the pulverized coal and lignin particles mix with and stick to plastics, the research team needed to add ester functional groups to the particles’ surfaces. Heldebrant, who works at Pacific Northwest National Laboratory (PNNL) and develops specialized liquids to capture CO2, found out about this work while chatting over coffee with Kappagantula.
Satish Nune, another project investigator, and Heldebrant were excited when they heard about this. “Esters are essentially carboxylic acids, which are a captured form of CO2,” Heldebrant explains. So, the team wanted to do the same thing and put CO2 onto the surface of the particles in the composite to make the material even more environmentally friendly while improving the composites’ mechanical performance.
To test the feasibility of this approach, the team turned to a classic chemical reaction to form a new chemical bond between CO2 and a functional group called a phenol, which is abundant in wood products like coal and lignin. After undergoing the reaction, the lignin and coal particles contained 2–5% CO2 by weight.
The team then mixed varying ratios of these particles with HDPE to form brownish-black composites, and they tested the resulting properties. A composite containing 80% filler maximized the amount of CO2 content while demonstrating strength and durability that meet international building codes for decking materials. It was manufactured via friction extrusion using PNNL’s shear assisted processing and extrusion (ShAPETM) machine. The researchers used this material to form 10-foot-long composites that look and feel similar to any standard wood composites found in decking or lawn furniture.
In addition to their favorable physical properties, the new composite boards offer a substantial price and sustainability advantage. They are 18% cheaper than standard decking composite boards. They also store more CO2 than is released during their manufacture and lifetime, Heldebrant says. If the 3.55 billion feet of decking sold in the U.S. every year were replaced with the researchers’ CO2-negative composite decking, he says, 250,000 tons of CO2 could be sequestered annually, which is equivalent to the yearly emissions from 54,000 cars.
Next, the researchers plan to make additional composite formulations and test the properties. They envision that carbon-negative composites could be developed for a range of building materials, such as fencing and siding. In the meantime, the team is working to commercialize its decking boards. This new carbon-negative decking could be available at building supply retailers as soon as next summer.
The research was funded by the United States Department of Energy Office of Fossil Energy and Carbon Management (FWP 78606) and the Southern California Gas Company (SoCalGas).
Visit the ACS Spring 2024 program to learn more about this presentation, “Towards carbon-dioxide negative building composites,” and more scientific presentations.
The American Chemical Society (ACS) is a nonprofit organization chartered by the U.S. Congress. ACS’ mission is to advance the broader chemistry enterprise and its practitioners for the benefit of Earth and all its people. The Society is a global leader in promoting excellence in science education and providing access to chemistry-related information and research through its multiple research solutions, peer-reviewed journals, scientific conferences, eBooks and weekly news periodical Chemical & Engineering News. ACS journals are among the most cited, most trusted and most read within the scientific literature; however, ACS itself does not conduct chemical research. As a leader in scientific information solutions, its CAS division partners with global innovators to accelerate breakthroughs by curating, connecting and analyzing the world’s scientific knowledge. ACS’ main offices are in Washington, D.C., and Columbus, Ohio.
To automatically receive news releases from the American Chemical Society, contact newsroom@acs.org.
Note to journalists: Please report that this research was presented at a meeting of the American Chemical Society. ACS does not conduct research, but publishes and publicizes peer-reviewed scientific studies.
Follow us: X, formerly Twitter | Facebook | LinkedIn | Instagram
Title Towards carbon-dioxide negative building composites
Abstract Carbon capture utilization and storage require new approaches to CO2 sequestration, namely ones that could safely, and profitably sequester hundreds of thousands of tonnes of CO2 per year while finally being able to return the all-elusive profit. We present here, a new CCUS approach that produces CO2-negative composites, comprised of lignin or lignite fillers that have been functionalized with CO2, where they are mixed within a high-density polyethylene (HDPE) matrix. CO2 fixation at the particle’s surface is achieved by base-mediated Kolbe-Schmitt reactions, resulting in a durable C-C bond on polyphenols in lignin and lignite. After acidification, the carboxylation stores approximately 2-5% CO2 by weight on the particles. Manufacturing of the composites was performed using conventional injection molding with 50 wt.% filler, and a new shear-assisted processing and extrusion process with 80 wt.% filler. In each approach, the produced composites have mechanical properties that meet international building codes for decking, which represents a multi-billion-dollar market that could sequester hundreds of thousands of tonnes of CO2 per year. We present a full techno-economic and life cycle assessment of an envisioned process, detailing how composites produced with recycled HDPE and renewable energy provide favorable economics and a negative global warming potential over a twenty-year period. We conclude with a discussion of the remaining scientific and manufacturing efforts needed for commercialization and an assessment of other serviceable markets in which composites could be produced.
Disclaimer: AAAS and EurekAlert! are not responsible for the accuracy of news releases posted to EurekAlert! by contributing institutions or for the use of any information through the EurekAlert system.
ACS Newsroom American Chemical Society newsroom@acs.org
Emily Abbott American Chemical Society e_abbott@acs.org
Copyright © 2024 by the American Association for the Advancement of Science (AAAS)
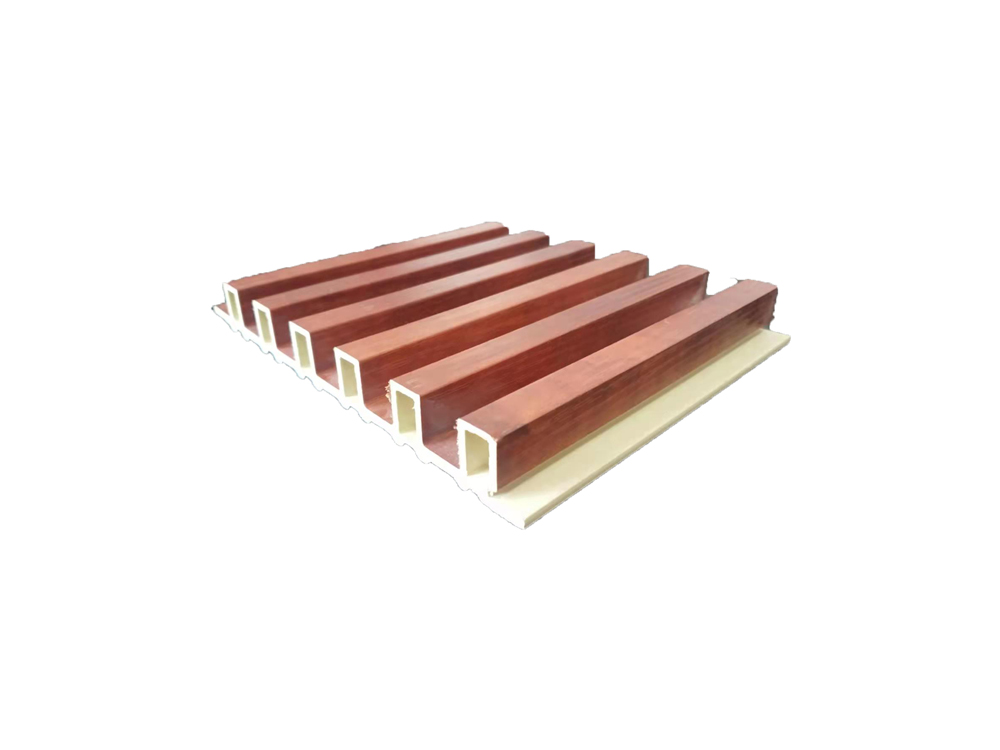
Building Material Copyright © 2024 by the American Association for the Advancement of Science (AAAS)