Cobot-assisted laser welding is growing more popular as metal fabricators look for the productivity associated with automated welding and the flexibility that comes with being able to remove the cobot from the configuration and use the laser welding equipment in a manual mode. Serra Laser
Like any good metal fabricator, Scott Hartrick is always looking for a better way to do something. Welder Mold Laser Welding Machine For Mould Repair

As president of Dynamic Metal Innovations (DMI), a 17-person shop in Emmaus, Pa., Hartrick not only leads the company, but he also helps out on the shop floor. That’s why it’s not unusual to find him striking an arc for a welding job. He gets a viewpoint a lot of company leaders don’t get.
Two years ago, DMI won a job that called for the fabrication of metal cabinets, made from thin-gauge steel and stainless steel (14 to 18 ga.) and measuring 3 ft. long and 2 ft. deep. The cabinets had inset features and required seam welds that had to be blended in for powder coating.
Using gas tungsten arc welding (GTAW, or TIG), Hartrick and his co-workers found that the process delivered too much heat, causing oil canning to occur in certain areas of the cabinet. To fight the distortion, the welders used torches to try to shrink the metal back to get rid of the oil canning effects.
Convinced there had to be a better way to tackle the project, Hartrick began sleuthing around the internet. Whether it was social media or a digital ad, he wasn’t sure, but Hartrick came across IPG Photonics new LightWELD hand-held laser welding equipment. He was familiar with the company’s laser power source because DMI’s first laser cutting machine had one.
“I saw some of the company’s demo videos, and I said, ‘Let’s just give this a shot,’” Hartrick said.
What especially caught his eye was the ability to incorporate a wire feeder with the hand-held laser. That was important because the cabinets had these bend reliefs at the corners, which couldn’t be fusion welded together. The gaps were too large and inconsistent. The wire feeder, however, made laser welding a suitable option for the task.
“You’re feeding that wire in, laying it down, and the wire feeder also created consistency in the welds because the wire feed would just push the gun along. So, you could kind of set the speed that the wire would lay. Then you just hold the gun, and it just pushes it along at the same rate, along the whole length,” Hartrick said. “Whereas with fusion welding, you’re going at the speed that you’re dragging the gun. If you’re slowing up or speeding up, you see that in a weld.”
Laser welding isn’t new. Lasers have been used in industrial settings since the 1980s. The technology, however, wasn’t more widespread because it was expensive and, as a result, only suitable for high-end, high-volume applications.
In recent years, fiber laser technology has emerged as one of the dominant technologies used in metal fabricating. With that, the cost of the laser power source has come down, opening up the door to manual laser welding.
Metal fabricators take note of laser welding because, like Hartrick, they recognize that the laser doesn’t create much of a heat-affected zone when laying a bead. This is because of the energy density of the laser beam, which is typically 10 kW/mm2. The energy density associated with an arc during a traditional welding process is about 50 kW/mm2, which means it takes much longer to transfer the energy to the metal to complete the weld. It’s also one of the reasons why beveling is often required with conventional arc welding; it ensures that a full-penetration weld is possible.
Fixturing has to be precise if laser welding is going to work. Serra Laser
“The laser shoots down to the depth needed and welds from the inside out,” said Glenn Kline, president of Serra Laser in Anaheim, Calif., one of the largest distributors for IPG’s manual laser welding systems, selling more than 200 systems per year. Serra Laser sold DMI its two laser welding units: one manual system and the other paired with a cobot.
Laser welding also doesn’t require clean surfaces. With aluminum arc welding, for example, contaminants and oxides need to be removed from the surface before welding can commence, but a laser beam simply shoots through the surface contaminants, even mill scale.
“It’s a true game-changer for people, and there really hasn’t been any innovations in welding in a long time,” said Kline, who spent many years selling laser cutting machines before entering the world of providing metal fabricating services.
Kline added the technological advancement that made the 2021 introduction of the LightWELD timely was IPG’s development of an air-cooled laser welding power source. Before that, many of the laser welding power sources developed overseas required some sort of water cooling, which added more complexity to a technology not yet well known. IPG, one of the world leaders in laser diode manufacturing, addresses this performance issue by adding more diodes than are needed for the actual welding application. Running the laser power source at a power setting that’s much lower than what the diodes can provide doesn’t generate much heat compared to a power source maxing out its generation capabilities. That allows for the units to be air-cooled.
“There is a lot of thought that went into these units. IPG knows the welding side of this technology really well,” Kline said, adding that the technology is widely used in several high-tech applications, such as battery and aerospace manufacturing.
The laser welding power units are designed to be used by people without a lot of laser welding knowledge. Like conventional arc welding power sources, the controls for the LightWELD include recipes for different types of welding applications. The user just needs to refer to a welding mode chart, where information such as material, type of weld (such as fusion, wire, or spot), and penetration depth guide the user to the right alphanumeric code. That code is then plugged into the power source, setting the power, gas flow, wobble width, and wobble frequency, and selecting either pulse or continuous wave welding.
A welder also has the ability to adjust the weld recipes. For instance, if more penetration is required, the welder can increase the power by 50 W with the twist of a knob.
Despite the controls for a laser welding power source mimicking those of a conventional welding power source, the two processes are completely different.
“It’s kind of like learning to weld all over again, with your speeds and your feeds and understanding wattage instead of working in amps and volts,” Hartrick said.
Referring back to his experience using the wire feeder with the laser welding machine, Hartrick described the process as “running at the pace of the wire.” When it’s going, the welder has to go with it.
Dynamic Metal Innovations’ laser welding enclosure is used for both manual and cobot-assisted laser welding. Dynamic Metal Innovations
“I would say that it lacks control compared to processes like TIG,” he added.
For example, with TIG, a welder can start and stop, reading the puddle along the way and making adjustments. But attempting that with the hand-held laser would result in more craters.
That’s why laser welding is a good candidate for shops with an application like 30-in. straight runs. Something that is more complex is a perfect candidate for arc welding.
“You’re not going to replace TIG or MIG welding, for that matter,” he said.
Hartrick described one job that involves tack welding enclosures using TIG, doing all the seams with the hand-held laser, and then finishing up the corners with TIG welding. Laser welding those corners can get “tedious,” according to Hartrick. With TIG, a welder can finesse the torch and electrode so that the corners melt just enough. With laser welding, if the fit-up at the corner isn’t very tight, the laser beam can blow a hole through the corners.
“Fit-up is definitely important with laser welding,” he said. “If your fit-up isn’t good or if your gaps are really big, you’ll have some headaches for sure.”
Hartrick admitted that it took him almost a year to get used to laser welding. He said he understood why some people said that the best way to get up and running on a manual laser welding machine is to find an operator without welding experience. It’s a totally unique way of joining metal.
Having said that, he doesn’t regret investing in the LightWELD. Even with the learning curve and expense associated with such a sophisticated machine, Hartrick said the productivity gains that the equipment delivers are real. He said that laser welding is “four to five times” faster than TIG, which can prove to be beneficial for any shop that has struggled to find welders.
The lack of people interested in pursuing welding careers in the metal fabricating industry is universally recognized. That’s one of the reasons why many shops and manufacturers have turned to welding automation, where possible, to increase welding capacity. One of the greatest areas of interest, particularly for smaller operations, has been in the use of collaborative robots.
“As soon as this [LightWELD] came out, the next question out of everybody’s mouth was, ‘Hey, can we put it on a cobot?’” Kline recalled.
In the summer of 2022, IPG, Serra Laser, and FANUC assembled a development team to create a laser welding cobot platform. IPG modified the LightWELD control system to be used with a cobot, and FANUC provided a CRX cobot for the project. IPG developed a cobot interface for the manual laser welding equipment, and Serra Laser developed the programming icons, which it called LightBOT AP.
Kline said that the CRX cobot uses a timeline method of making a program, sort of like how someone might edit a video recording. Once the LightBOT’s icon for setting up a weld program is engaged, the user moves the cobot arm manually to different weld positions, swiping different icons during the process. These icons determine the weld recipe (using the same alphanumeric codes), the use of welding wire, the amount of power, wobble width, and wobble frequency. (An icon for laser cleaning has been included on recent editions of the LightWELD and is now available on three models currently offered by IPG.)
Kline added that Serra Laser can add the CRX cobot to any LightWELD system that’s ever been sold. The installer is able to come on-site, update the laser welding system’s software to allow for cobot control, and complete the electric connections between the LightWELD and the cobot.
“This normally takes one day, and we spend the remainder of the time on-site teaching the welder how to use the LightWELD-FANUC CRX system,” Kline said.
Hartrick said the LightBOT’s flexibility makes it attractive for use at DMI. It takes fewer than five minutes to switch from cobot mode to manual welding mode and vice versa.
IPG has created a switch box that is added to the system to ensure ease of use and safety. For instance, if the user wants to go from manual welding to cobot welding with the laser, the switch box has to be flipped into cobot mode and the gun has to be in a special gun holder before the FANUC software can take control of the laser welding system. This was developed so the system can’t be fired accidentally by the cobot.
The LightBOT also offers in-process control that some metal fabricators might find useful. Kline said the cobot has the ability to shift operational parameters during actual welding. For instance, if a butt weld needs to be done, a welder usually runs into trouble at the edge of the weld, where there is a tendency to have burn-out because there is not enough material for the heat to flow through. With the LightWELD on the cobot, the welding program can have the weld start at a lower power setting, increase as the weld progresses, and wind down at the end. The power changes occur on the fly in milliseconds.
Again, just as using the laser welding system in manual mode requires tight fit-up and good fixturing, the same applies for the cobot-assisted version.
“When you have the right application for it, it makes a lot of sense to use it,” Hartrick said. “For example, the cobot can conquer those complex corners and perform fusion welding that would be too cumbersome to do by hand. The results also are repeatable and consistent every time.”
No discussion of laser welding would be complete without covering safety. The laser beam presents a real danger, particularly to the eyes, so careful operation is a necessity.
As most welders have been taught—or perhaps learned—exposure to arc welding can lead to a burn. The UV light from conventional welding can do damage, but for the most part, the body can heal itself. Laser welding involves a beam of infrared light, and if that beam penetrates the unguarded lens of an eye, it can do damage to the retina that likely can’t be repaired.
According to Kline, most of the laser welding systems Serra Laser sells are to be used in an enclosure, which prevents the laser from escaping. About 30% of the companies buy enclosures provided by Serra Laser, and the rest fabricate their own enclosures, Kline estimated.
A Laser Institute of America study suggested that 71% of incidents when using lasers were eye injuries, mainly a blind spot in the field of vision. The same report noted that many of these accidents result from an unexpected upward reflection.
That’s why eye protection when using a manual laser welding system is so important. Kline said that the safety glasses supplied with the LightWELD have an optical density rating of 7-plus, designed to keep laser energy that might pass through the lens at an absolute minimum. (An optical density rating of 7-plus means only one photon out of every 10 million can pass through the optical filter.)
Laser welding helmets also are available to protect the rest of the face from potential laser exposure. The early versions of this helmet type were just conventional welding helmets with aluminum shields around the glass filters. Today, the newest helmets are made out of carbon fiber and can withstand a direct hit from the laser for up to 10 seconds without being penetrated.
To reinforce the need for careful operation, Hartrick explained how he was working on a weld and the laser blew through the joint area to be welded, hit a piece of aluminum that was on the table, bounced off that, and hit his gloved left hand.
“The heat cauterized it immediately. There was no bleeding,” Hartrick said. Nonetheless, the wound looked pretty gnarly as it healed.
Despite any safety concerns, unfamiliarity with the technology, and the cost of such systems, metal fabricators look to have a growing interest in laser welding. They see potential benefits and are willing to make the necessary investment.
There also might be a fear of falling behind. Kline said that technology improvements in laser welding continue, one of the most recent being the ability to use a dual wire feeder that helps the process deal with gaps as large as 1/8 in. With advancements in vision systems and the application of artificial intelligence capabilities to these tools, the only certainty is that laser welding systems are going to become more user-friendly.
“A few years down the road, you won’t be able to find a shop without laser welding in it,” Kline said. “They won’t be competitive without it.”
See More by Dan Davis
Dan Davis is editor-in-chief of The Fabricator, the industry's most widely circulated metal fabricating magazine, and its sister publications, The Tube & Pipe Journal and The Welder. He has been with the publications since April 2002.
Read more from this issue
Find The Fabricator on Facebook
Find The Fabricator on X
The Fabricator is North America's leading magazine for the metal forming and fabricating industry. The magazine delivers the news, technical articles, and case histories that enable fabricators to do their jobs more efficiently. The Fabricator has served the industry since 1970.
Easily access valuable industry resources now with full access to the digital edition of The Fabricator.
Easily access valuable industry resources now with full access to the digital edition of The Welder.
Easily access valuable industry resources now with full access to the digital edition of The Tube and Pipe Journal.
Easily access valuable industry resources now with full access to the digital edition of The Fabricator en Español.
Jeff Cupples, the president of Jackson, Tenn.-based Cupples J&J Company, discusses his experience with laser cutting machines and...
© 2024 FMA Communications, Inc. All rights reserved.
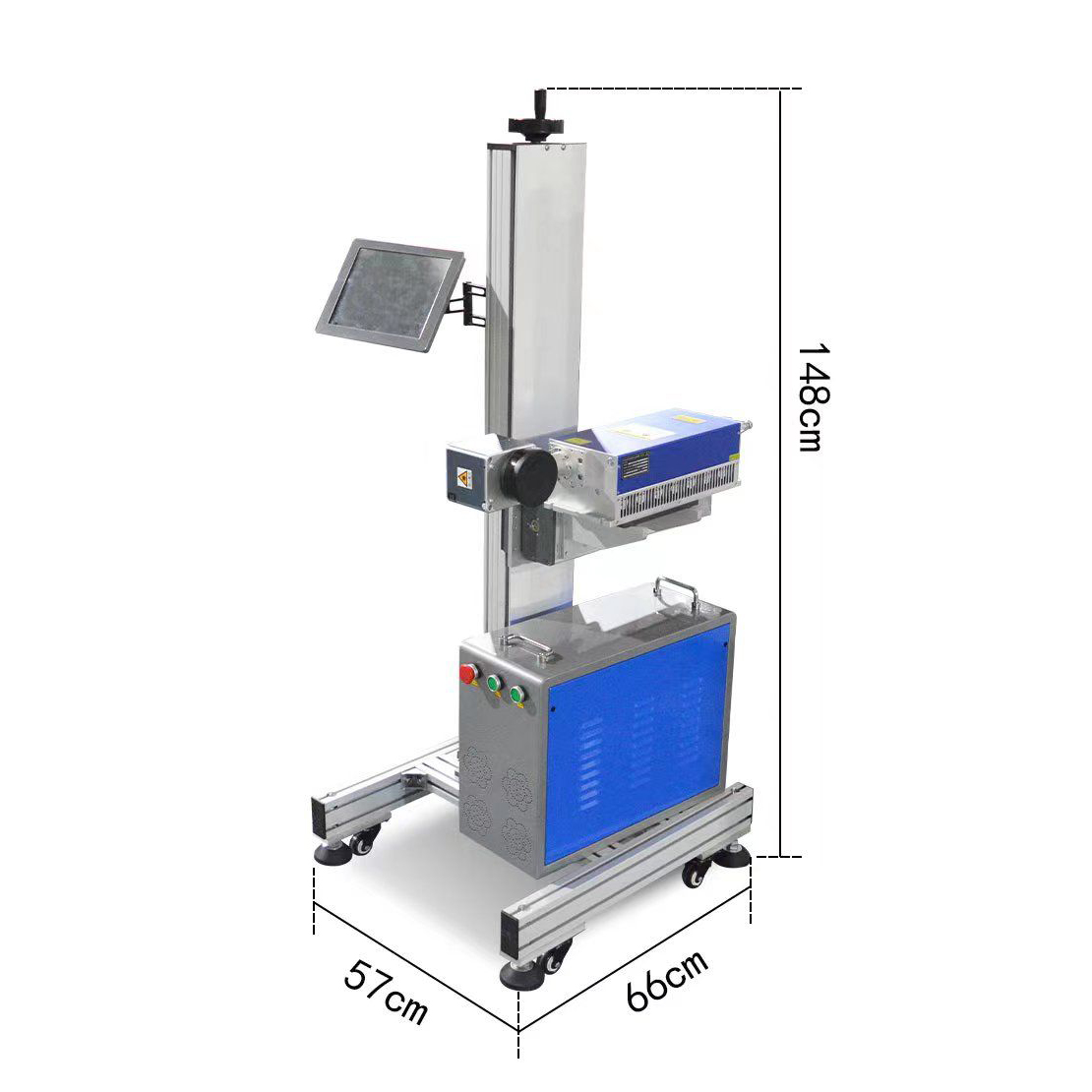
15w Uv Laser Marking Machine Not yet registered? Sign up