Air Operated Valve Solves Paint/Varnish Production Problems Elastomer swelling, leaking eliminated (Image source: Plast-O-Matic Valves, Inc.)
A chemical manufacturer was experiencing significant problems with corrosion and quality control in a mixing system used for specialty varnishes. The process originally relied on a series of brass solenoid valves to add solvents, which change frequently depending on the batch requirements. While the valves functioned properly with some of the chemicals, they were subject to serious corrosion by others, and failed after a few thousand cycles. In extreme cases, the resulting leaks could potentially require costly clean up and reporting measures. Ball Type Foot Valve
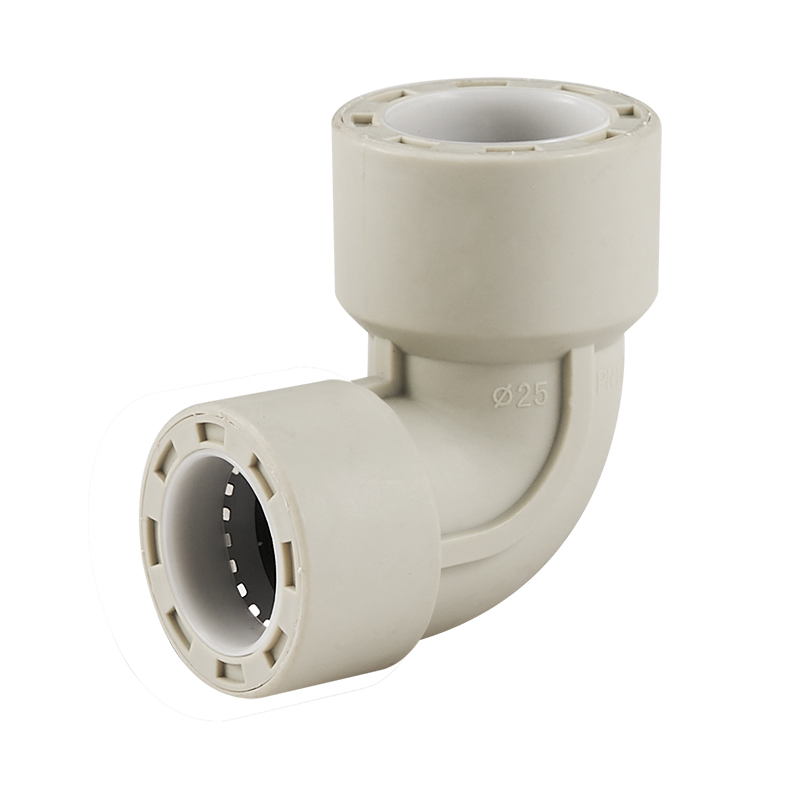
System engineers converted the valves to a series of low-cost, electrically controlled thermoplastic ball valves. Unfortunately the problems continued, as the discount actuators were subject to occasional failures. But a more troublesome issue involved the multiple elastomer o-rings used in the ball valves. When highly aggressive solvents were used in a batch, some of the formulas attacked the materials and the o-rings would swell, binding the valves. In addition, any resulting leaks carried the same costly implications.
The manufacturer contacted Plast-O-Matic about building ball valves with perfluoroelastomer o-rings such as Kalrez, which are virtually impervious to chemical attack. Unfortunately the number of o-rings required pushed costs to an exorbitant level.
As an alternative, Plast-O-Matic’s Technical group recommended switching to air-operated PTFE diaphragm valves with no wetted elastomers. Series BSDA differs significantly from multi-turn diaphragm valves as it uses compressed air to open a piston, and an isolated spring to close it automatically when the air is diverted by the process control system.
Although Series BSDA is tested to over 1,000,000 cycles in laboratory conditions, it has redundant leak prevention via a patented “Fail-Dry” early warning vent. In the unlikely event that the PTFE diaphragm is compromised, a second, sealed chamber isolates any leaking liquid and allows it to be conveyed to a safe location. The valve may be turned off, or it may be determined to continue operations until maintenance can be conveniently scheduled.
The varnish process uses BSDA valves with Kynar PVDF bodies on the solvent lines, and PVC body valves on the less aggressive feed lines. Plast-O-Matic recommends periodic scheduled inspections of the diaphragms, which can be easily replaced if wear is evident. To date the valves have cycled over 250,000 times with no failures.
A major southern grow operation needed a valve to open and close automatically on a series of remote fertigation pipelines. The lines were in a location where compressed air and electricity were both unavailable and impractical. It was essential to have the valve close whenever the water supply dropped below operational pressure, to prevent the percentage of nutrients from exceeding safe levels and harming the crop.
The City of Bremerton, Washington needed to build a system to bring its pH levels in line with the Lead and Copper laws, with the flexibility to compensate for a variety of water sources. Dealing with pH levels below neutral, the Engineering Division of Bremerton Public Works and Utilities had to provide a system for injecting caustic soda into the water main.
An Air Release Valve is open when the system is depressurized. At start up, the liquid process forces most of the air in the pipeline to high points, where the ARV allows it to escape. Once liquid rises, the valve closes and will not allow anything – gas or liquid – to pass in or out. It will not vent gas as it occurs during daily operations. It will reopen only when the system is depressurized and liquid level drops.
To fully understand the valve and the piping possibilities, the first step is to understand all of the capabilities of a 2-port valve.
In this chemical bulk handling application, a ball-type check valve was specified as a foot valve to provide continuous pump prime. The centrifugal pump will not self-prime, and if it runs dry will result in seal failure. Prolonged operation in a dry condition is likely to result in catastrophic failure.
Crop fertigation piping systems typically deliver precise batches of nutrients to crops through a supply line, and remove overflow via a drain/flush line. Although system parameters vary from site to site, a typical installation uses a mix of water and nutrients between 30-90º F.
impeller.net – Inform. Select. Buy.

Pedal Valve For Sink The international information and sales platform for centrifugal pumps.