ESAB has introduced its first collaborative robot for MIG and pulsed MIG welding applications on steel, stainless steel, and aluminum alloys. Operators teach the cobot welding paths using a software app running on a smartphone or tablet, along with a Smart Puck to hand-guide the torch and record its position with the push of a button.
The cobot is designed to automate high-mix, low-volume applications for small and medium-sized fabricators. It features a Universal Robots UR10e industrial robot arm, along with ESAB’s Aristo 500ix pulse power source, RobustFeed U82 wire feeder, an air- or water-cooled torch, and accessories. Welding System Integrators

A Siegmund 32- by 48-in. welding table organizes components and enables moving the cobot around a shop.
The FABRICATOR is North America's leading magazine for the metal forming and fabricating industry. The magazine delivers the news, technical articles, and case histories that enable fabricators to do their jobs more efficiently. The FABRICATOR has served the industry since 1970.
Easily access valuable industry resources now with full access to the digital edition of The FABRICATOR.
Easily access valuable industry resources now with full access to the digital edition of The WELDER.
Easily access valuable industry resources now with full access to the digital edition of The Tube & Pipe Journal.
Enjoy full access to the digital edition of STAMPING Journal, which serves the metal stamping market with the latest technology advancements, best practices, and industry news.
Easily access valuable industry resources now with full access to the digital edition of The Fabricator en Español.
Dr. Chris Kuehl, an economist with Armada Intelligence and a contributor to FMA's Fabrinomics e-newsletter, joins The FABRICATOR...
© 2023 FMA Communications, Inc. All rights reserved.
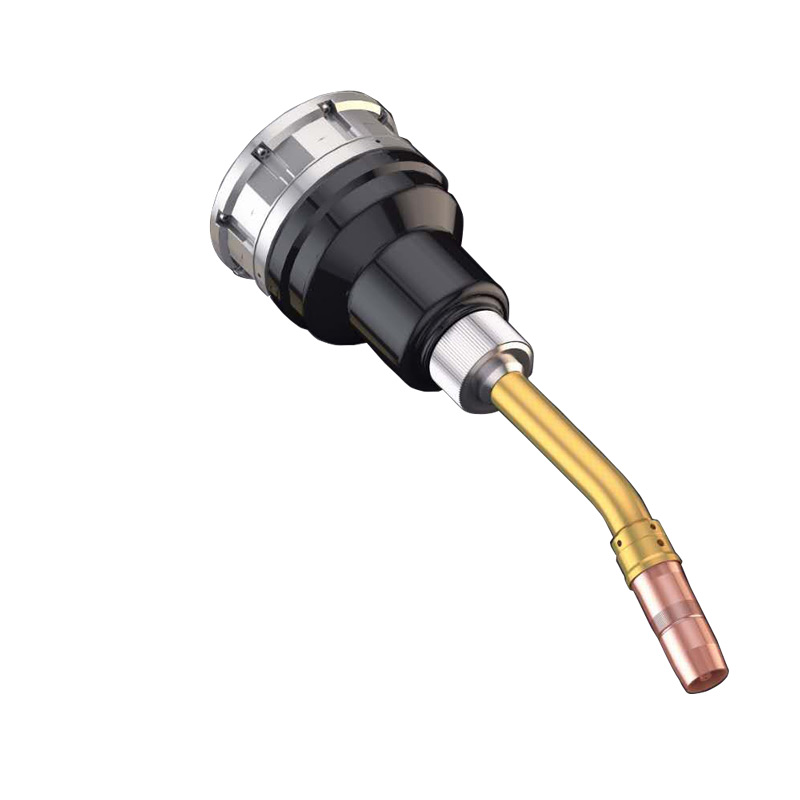
Vesco Robotic Welding Institute Not yet registered? Sign up