This Q&A stems from the 2024 DryPro Webinar with the same title.
Recently, Powder & Bulk Solids presented “Dust Explosion Vent Sizing Made Easy: Case Histories and Examples” as part of its DryPro webinar series. This webinar shared case histories and examples of dust explosions. Pharmaceutical Door
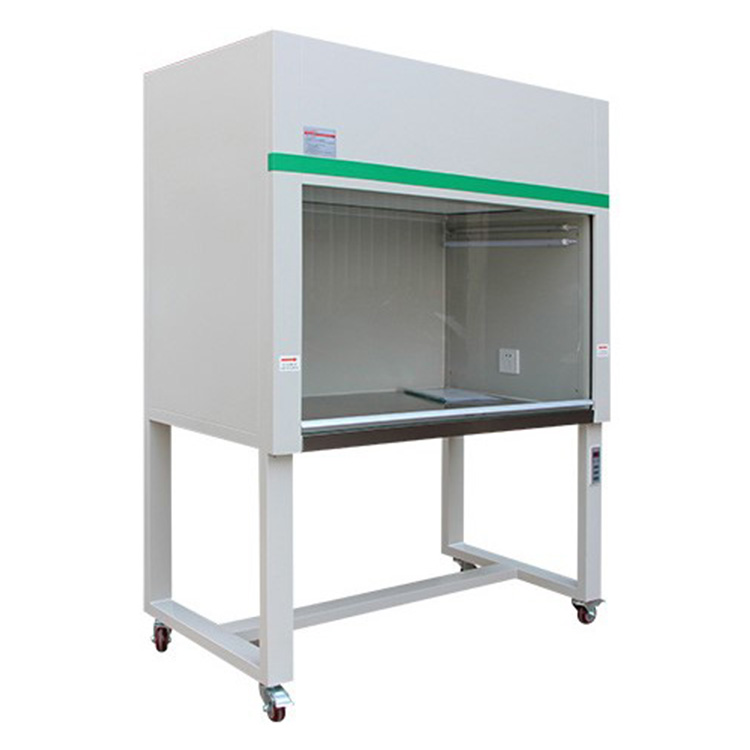
Dr. Ashok Ghose Dastidar, PhD MBA, Fellow engineer, Westinghouse Electric Co., and vice president, Dust & Flammability Testing and Consulting Services – Fauske & Associates LLC, discussed the need for explosion protection on process equipment be that a dust collector or cyclone, a spray dryer, an oven, a mixer, etc. An effective method for explosion protection is by venting the overpressure of that explosion effectively.
After the presentation, a live Q&A took place. Below are the questions and answers.
You also can access the entire Dust Explosion Vent Sizing webinar On Demand here.
Q. NFPA 654 calls for a DHA every five years, but 652 and others don't. What is the most compelling standard or Code clause to convince a company to get a DHA done?
First, if you don’t have a DHA, you have to get one; that’s in 652, 661, 664, … they’re asking you to get a DHA done. The question is the revalidate every five years. Currently 654 does have that; I think if you don’t revalidate your DHA, you should have a good management change program, which is also a requirement for NFPA 652. If you don’t have a bulletproof management of change program, having a frequent DHA could definitely be beneficial because you can catch any additional gaps generated since the last DHA or even audit any action items that were left over from the last DHA that haven’t been performed.
The way to convince people to do it is, you have to do it once, if you want to revalidate your existing one, follow 654 and do it every five years. Or, you have to have a very good management of change program. If you don’t, you need to reconduct your DHA at a higher frequency, maybe 3 years would be better.
Q. For Pmax and Kst values, how much can one leverage public databases and literature information vs. conducting one's own testing? In general, I expect that testing is advised. This is presuming that a particle size distribution is well understood.
I think a lot of literature value is present primarily for general understanding. If you find it in a table like NPF 68 and several of the other NFP standards have tables in there of Pmax and Kst values but those are just representative. They don’t necessarily reflect your particular unique particle size distribution and we know that particle size distribution greatly affects the values. The coarser the material, the less intense the explosion; the finer the material, the greater the extent of the explosion.
If you are using literature value, I would request they provide you with an actual test report and you can use that value. If you’re looking at tables that are publicly available, or values from a safety data sheet, I would actually go out and get tested.
Q. Can you discuss incompatible dusts — steel and aluminum for instance. Are there circumstances where a dust mixture will impact the Kst of the mixture in a manner that is non-linear?
This could definitely be a situation where, for example, steel and aluminum, we’re primarily looking at the steel to be oxidized, so you have iron oxide in aluminum, that is generally frowned upon by NFPA. You really shouldn’t mix metals because you have — in this particular case — the possibility of a thermite reaction which you will not be able to put out. If that material catches fire and explodes in your chamber, in your dust collector, etc. you will not be able to put it out; you’ll just have to wait for it to burn out.
In other situations, there really isn’t a good method because certain times they’re not additive. Usually it’s more like a cliff face, where depending on if you have an inert material and a fuel material, it might not linearly affect the Kst and Pmax. It might be more of a cliff face. You’ll end up decreasing slightly until you get to a concentration of inert then you’ll fall off a cliff and won’t be exposable anymore. When you combine two different fuels you can’t use a weighted average to estimate that there’s a Kst that is between the two. Sometimes if you have an oxidizer and a fuel, the oxidizer could exacerbate the Kst of the original material. It’s really by experimentation.
Q. Are considerations of the panel geometry taken into account, i.e., if the panel is on a hinge the moment of inertia of the panel would appear to be a consideration?
Yes, absolutely. Hinged panels vs. burst rupture panels are addressed and the standard does talk about them so you can go through that section. The panel manufacturer has to demonstrate the effectiveness and functionality.
Q. In the design guidelines, are there still considerations for placement vent in relationship to the bags in a collector?
I typically in the past, what we wanted to do is that the vent should not be placed in a location such that the bags can get sucked out of the vent because that will decrease the flow through the vent panel. My most recent review of the standard, I didn’t see that but it was present in the past. So I would still follow that procedure, because you don’t want the vent panel to be blocked by bags. What most dust collector manufacturers do is that the area nearest area of the vent is void of bags so that nothing will obstruct the vent panel from opening, and the flowing of unburned or burned material out of the vent panel won’t be obstructed from bags.
Q. What conditions allow indoor venting?
Primarily indoor venting is only allowed if you have the release of the vent directed to the outside. The dust collector could be located against the outside wall so you have a very small duct so you don’t necessarily need to consider it and the vent panel is just as good as if it was outside. Or if you’re not close to an outside wall, about 1-2 feet, you have to have a duct. And that duct, depending on bends and straight pipes, offers a penalty on the size of the vent area. So you can duct it to the outside.
The third option is to have a flameless vent. If you’re sure that the gases that will be released after combustion aren’t going to be toxic, you can vent to the inside. Sometimes the ducting that results in panels are so large that you can’t conveniently put them on the dust collector at all so that wipes out ducting as an alternative to keep the dust collector inside. Sometimes a flameless vent is not possible because you’re releasing toxic materials, or you have hot burning metals in there and you can’t use flameless vents on hot burning metals. Your only other option at this point is to use suppression, which uses discharge cannons and a detector and injects in fire-suppressant powder.
Q. Chicken wire is sometimes used to prevent bird infestation that could impair opening of explosion vents. Is there a requirement to consider this thin gauge wire when calculating vent size?
There are no requirements per se to calculate that allotment. The idea is that you don’t use it at all; you’re not supposed to use it. I’ve seen people use Styrofoam panels on the vent outside so that they’re insulated especially if you’re up north in IL, WI, MN, they will put on some sort of insulation panel. Unless that insulation panel is provided by the vent manufacturer, or the dust collector manufacturer, I wouldn’t do anything on your own. Because those typically are not calculated for conveniently in the system and can impede the way the vent panel opens.
Q. If the NFPA standard changes between the design and installation of a process, which standard prevails (older or newer)?
If the design standards change and you already have a vent panel on, I think most AHJs (authorities having jurisdiction) which are fire marshals, building inspector, OSHA official, insurance company, they would be fine with you having a vent panel designed using the equations that were available at the time of the panel’s implementation. However, if you were then to repurpose that dust collector for a different dust or if you were to change anything around that dust collector so that would be considered a material change, they would probably request that it be redesigned using the most recent equations for that panel venting. So it depends on if it’s an existing collector and it was built/sized appropriately at the time and you haven’t touched it in the sense of making modifications physically or the type of dust you’re handling, you’re fine and leave it alone. If you have changed anything, you probably will have to comply with the most recent one. But it will be your AHJ’s call. And most will want you to be at the most recent one.
Q. Is entry into the restricted zone for fireballs absolutely prohibited or simply restricted?
It’s prohibited. The only time that you should allow entry in that location is if you know through some hot work program or tag out/lock out situation that the dust collector was off and there is no way something could enter inside the collector. Because you don’t know at anytime or what time the dust collector could explode. Which is why you would want the deflector plate on or flameless vent on in the event that you have an occupied location near that dust collector.
Kristen Kazarian has been a writer and editor for more than three decades. She has worked at several consumer magazines and B2B publications in the fields of food and beverage, packaging, processing, women's interest, local news, health and nutrition, fashion and beauty, automotive, and computers.
Q&A: Dust Explosion Vent Sizing Made Easy: Case Histories and Examples
Converting Pleated Cartridge Filters to Filter Bags for 1-Micron Efficiency
Corn-Sugar Chemical Plant Scores $213M Loan
Skin Sunscreen Foundation Recalled for Microbial Contamination

Clean Room Partition Copyright © 2024 All rights reserved. Informa Markets, a trading division of Informa PLC.