Cloward H2O, an expert in aquatic design, has shared how it engineers effective and efficient systems from both an operational (OpEx) and development (CapEx) point of view.
The firm’s approach to water treatment systems can be summarised into four main components: circulation, filtration, chemical treatment, and temperature control. With each of these components, various factors affect both OpEx and CapEx costs. However, the ultimate result is to provide recreational water that is clean, clear, and inviting for the guests and is easy and cost-effective to operate. Dispenser Pure It
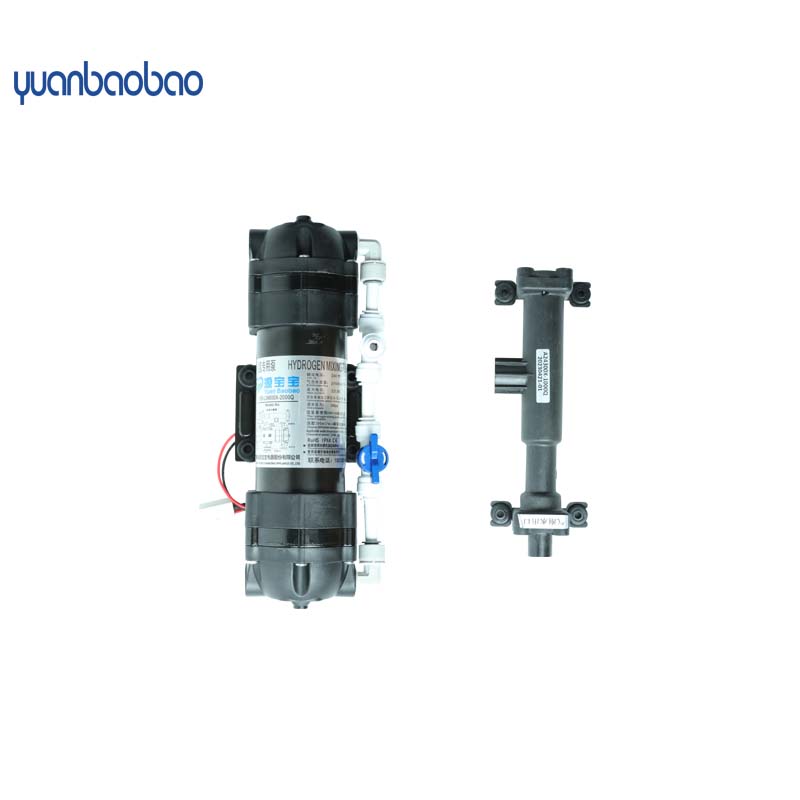
The first element is circulation, and turnover rate is one of the critical factors. This is the time required to circulate the volume of water through the treatment system fully.
“Pools with large bather loads, high water temperatures, or small children require higher turnover rates than other uses. In our case, we typically recommend 30-minute turnover rates for hot tubs, spa pools and splash pads, 2–3-hour turnover rates for family pools, 4-5 hours for adult and beach pools, and 6-8 hours for residential plunge pools,” says the company. Turnover rates determine filter sizes and power requirements for circulation pumps.
The power needed for the feature pumps and circulation accounts for a large percentage of the electrical load of a water feature. Efficiency is aided by careful selection and pump sizing to match the needed performance closely.
“We recommend premium efficiency pump motors, which have 6-12% better energy usage than standard motors. Common industry practice is to provide a certain amount of over-capacity to accommodate differences between design and constructed conditions. This leads to conditions where a pump needs to be restricted using a valve to achieve the correct operating flow and pressure.
“Using a Variable Frequency Drive (VFD) is an excellent alternative method for tuning pump operation and optimizing pump efficiency. A VFD is an electronic device that allows the operator to have automated control of a motor’s speed. Reducing the speed of the motor, whenever full speed is not required, reduces power consumption and power cost.
“We typically specify Schedule 40 PVC for the majority of the underground pipe runs. For deep excavations as well as exposed pipe in the mechanical room we specify Schedule 80 PVC. Our design standard for pipe flow velocities is nominally 5-5.5 feet per second (fps) for pressure piping, 3 fps for suction lines, and 2 fps for gravity flow pipes. We utilize balance tanks, also referred to as collector or surge tanks, for all pools with gutters or infinity edges.”
In the construction document phase, the Cloward team analyses head loss for all water features piping networks to verify and adapt pump motor sizes. The piping networks will provide proper circulation within the feature to eliminate dead spots and provide circulation throughout the entire volume.
Design, engineering, and operation of water-themed projects require filtration. Filters clear water and eliminate pathogen-harbouring detritus. High-rate sand filters dominate aquatics filtration. They are inexpensive since they are the industry standard for filtration. Backwashing the sand bed by backflowing water through the filter removes debris and waste but uses a lot of water.
“An alternative to sand filters has emerged over the past ten years, which has several significant advantages to traditional sand filters, explains the company. “Regenerative media filters require far less water compared to sand filters. This is due to both extended filter cycles and minimal water volume required for backwash. The typical backwash cycle for a sand filter is twice a week, whereas regenerative media filters require backwashing typically once a month.”
Sand filters are backwashed at 20 gpm per square foot for up to five minutes per filter vessel, while regenerative media filters backwash volume is the filter tank volume times two. This reduces annual backwashing water loss by over 95% compared to sand filtration.
Other benefits of regenerative media filters include:
The downside to regenerative media filters is the higher initial cost of the filter compared to sand filters. The costs have been coming down but are still higher than sand filters. The typical return on investment (ROI) is anywhere from 18 months to three years.
“Cartridge filters are also a common filtration method and are mostly used for small systems,” adds Cloward. “Each filter type, whether it be sand, regenerative media, cartridge, etc., has its place in the aquatics industry. When deciding on a filter type, it is important to weigh the various options with their respective pro’s and con’s for each application.”
Chemical treatment systems comprise four main components: a primary disinfection system, a secondary disinfection system, a pH control system, and a chemical controller.
These technologies offer a way to eliminate or render the bacteria responsible for waterborne infections inactive. Chlorine is the disinfectant most often used in the aquatic industry. Oxidation Reduction Potential (ORP) regulates the amount of chlorine added to water to maintain the right residuals. In addition, bather contamination, temperature changes, ambient pollutants, and pH can all affect the disinfection process.
This device delivers chlorine to the treatment stream at a suitable rate. Chlorine, the primary disinfectant, comes in liquid or pill form. A chemical feed pump takes from a chemical storage tank in a liquid chlorine system. Tablets are usually held in a feeder tank and dissolved in water before the chlorinated water is released into the treatment stream.
“Our first preference is to use liquid chlorine; however, the tablet form has its place as well. This decision needs to be guided by the availability of each form and the ability to move the product to the pool equipment rooms. During design, we request some guidance from the operations team as to their preference on the type of chlorine system that should be specified.”
When it comes to salt chlorine generators, the firm adds: “There is a lot of misunderstanding and misinformation regarding this technology. It is critical to understand that this technology still delivers chlorine to the water. Chlorine is provided as a component of salt (Sodium Chloride). Using an electrolysis process the sodium and chlorine atoms are split and the chlorine is used in the disinfection process, while the sodium remains in the water.
“We do not believe that salt chlorine generators are effective in commercial pool applications. We have seen the technology used in residential applications, where there is not a large bather load. We do not recommend the use of salt chlorine generators.”
More potent disinfectants are needed to tackle chlorine-resistant bacteria like Cryptosporidium in the aquatic industry. The 2014 Model Aquatic Health Code from the CDC includes secondary disinfection systems. Two secondary disinfection methods are approved: UV and Ozone.
Cloward H2O recommends ozone on almost every project due to its use as a powerful oxidizer with an ORP of 2.07 compared to chlorine, which is 1.49. Ozone is produced by a process known as Corona Discharge:
“Oxygen is exposed to a high voltage current that forces the oxygen molecule (O2) to form ozone (O3) molecules. Water flows through an injector assembly that mixes the ozone and the water in a very turbulent condition. The water is then moved to a contacting vessel where the ozone reacts with the organic compounds and organisms in the water. Ozone rips organic compounds and organisms apart. Ozone also reacts with chloramines reducing them back into usable chlorine compounds.”
These reactions happen very quickly, and the ozone is usually spent within a couple of minutes of introduction to the water.
“We base our recommendation on the ability to oxidize organic material and provide a higher degree of water quality, which will result in a reduction in the amount of chlorine usage. We have analyzed ozone in many projects as a better product than UV at controlling chloramines, which are responsible for swimmer discomfort and damage to pool facilities.”
Despite disinfecting the most water, ozone does not leave a residue; hence, it is considered a secondary method. Properly applied ozone reduces chlorine and acid by 60% compared to non-ozone treatment.
In addition to ensuring that disinfectants work as effectively as possible and safeguarding the metal mechanical components and cementitious pool surfaces, proper pH levels also promote bather comfort. Usually, muriatic acid, also known as hydrochloric acid, is used to lower the pH of water. Usually, a chemical storage tank and a chemical feed pump are used to do this. The chemical controller regulates the acid dosage.
In addition to a processing unit that decodes the signals from the probes, the chemical controller comprises pH and ORP sensors. Next, based on the ORP value or pH reading, the processing unit will signal the appropriate chemical feeder to administer acid or chlorine. Additional sophisticated features that compute additional factors for preserving the proper chemical balance in the water vary depending on the chemical controller type.
Usually, pools and hot tubs will be heated in the winter, and then they can be cooled in the summer, depending on the local climate.
“Because there can be a use for both heating and chilling of the water, we generally recommend, use of a heat exchanger. Although gas and electric heaters are very common in our designs as well. A heat exchanger effectively utilizes the water source at whatever temperature it might be pumped into the mechanical system.
“Designing and setting the water body at the correct temperature is critical to bather comfort. Guests can almost always tell if the pool is even 1 degree too cold.”
“Clean and safe water is the end goal of aquatic engineering. Proper water treatment happens through correctly applied engineering principles for filtration, circulation, oxidation, and sanitation. We use state-of-the-art technologies, industry best practices, and customized solutions to ensure crystal-clear water on every project.”
Earlier this year, Cloward H2O shared its approach to the design of very large lagoons to ensure effective water treatment. The firm has been designing lagoons since it was founded in 1985. One of its first major projects was a saltwater lagoon at Hilton Waikoloa Village, which opened in 1988.
Get the latest attractions industry news direct to your inbox, every day.
Blooloop is taking climate action
Become part of the Blooloop community:
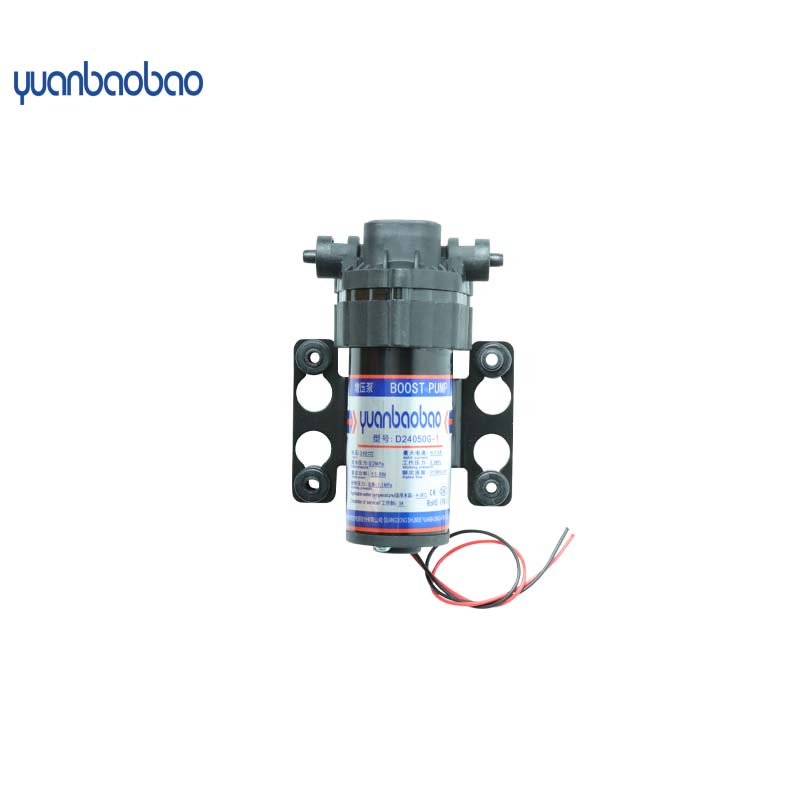
Pump To Boost Water Pressure Your web browser is out of date. Update your browser for more security, speed and the best experience on this site.