From cobots to machine monitoring, this Top Shop honoree shows that machining technology is about more than the machine tool. #topshops
Founded in 1950 on Long Island, New York, Stock Drive Products / Sterling Instrument (SDP/SI) began as a contract manufacturer taking advantage of its close proximity to major defense contractors. Over time, the company expanded into the aerospace, medical device and industrial markets — natural fits for a company already used to achieving the highly precise tolerances and demanding standards of defense work. Maintenance Of Tool Pre-Set
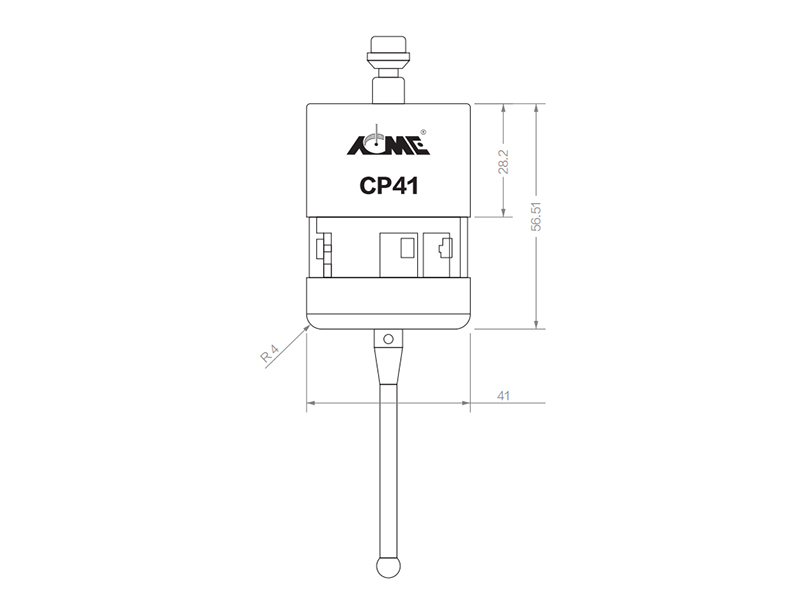
Here we see workers at SDP/SI programming a cobot to attend a Haas 500SS. The cobot is designed to alter its movement speed when near humans, making it a safer alternative to a normal robot arm. Additionally, users can program the cobot by moving it with their hand and saving the position, making it simple for even inexperienced operators to program. Photo Credit: SDP/SI
In 2013 the company began a reorganization process and consolidated four manufacturing locations into a single facility in Hicksville, New York, in 2017. This led to numerous benefits and earned the company Top Shops honors for its HR practices in 2019. Four years later, Modern Machine Shop is proud to again honor this Top Shop — this time in the category of Machining Technology.
The Hicksville facility is a 96,000-square-foot building that contains 300 machine tools worked by 200 employees. According to SDP/SI President and CEO Robert Kufner, finding that kind of space on Long Island was worth the pain. “It wasn’t easy, let me tell you,” he says. “We consolidated four locations into this beautiful new building here.”
This move centralized operations while keeping the company close to its workforce. “The owners understand that its workforce is a tremendous source of value,” Kufner says. “We have a lot of highly skilled workers here. People with decades of seniority, like Sue.”
VP of Operations Sue Anderson began at the company just out of college, working as a production control clerk. After 40 years with the company, she knows every inch of the production floor.
“We have 300 machine tools,” she says. “It’s an even blend of milling and turning. That includes a lot of DMG MORI lathes, several with dual spindles, many able to gear cut on the machine. Most have a 3-inch capacity for the bar feeders, with one that has a 4.25-inch capacity.” On top of this, the company has nine Swiss-type lathes (seven Stars and two Citizens), rounding out its turning capabilities.
The lathes at SDP/SI are equipped with bar feeders and Rota-Racks from Royal Products. This simple combination is an effective automation solution for lights-out production of round parts, as it can keep a CNC turning center running for many hours. Photo Credit: SDP/SI
Most of the milling machines are also DMG MORIs, primarily vertical machining centers. Most are 4+1-axis machines capable of turning when necessary with proper fixturing. Additionally, there are two five-axis Haas mills. “We use the five-axis machines for more complicated aerospace housings,” Anderson says. “The Super Precision Mini Mill has been here forever and can hold 0.0002 inches all day.”
While the sheer volume of machine tools is impressive, the company is also constantly investing in more equipment. “We’re reinvesting $1 million to $1.5 million every year, rotating out the older equipment and bringing in more modern machines,” Kufner says. “And I’m always asking for more,” says Anderson.
One key area of investment is automation.
One of the primary ways SDP/SI keeps production levels high is through automation. “We have pick-and-place robots tending high-volume jobs,” says Kufner. “But one of the most cherished sets of automation is the FMB bar feeder paired with a Rota-Rack from Royal.” This simple combination keeps over 100 lathes producing parts consistently with minimal human intervention. “The FMB is just a beast,” he continues. “They withstand vibration. They’re not finicky. They’re just really good machines.”
“When we do the extra work to figure out how to not touch the part a second time, we can reduce the cost of the part by 25%.” – President and CEO Robert Kufner, SDP/SI
Automation is not just about moving the workpieces in and out of the machines, however. “Our whole concept has been doing everything we can in the envelope of the machine without taking it out,” Kufner says. This means deburring, gear cutting and numerous other secondary operations are performed in the same machine tool. By getting as much work done in a single setup as possible, the company can dramatically reduce setup time and human error.
This DMG MORI Wasino uses a standard robot-arm automation package supplied by DMG MORI. This machining cell, along with the company’s bar-fed lathes, has contributed to the 1,600-2,400 hours of unattended machining performed each month. Photo Credit: SDP/SI
Anderson had to implement numerous techniques for completing secondary processes in the machine envelope. “We added Weiler brushes and other types of honing and deburring equipment into most machine tools,” Anderson says. This has enabled them to remove both interior and exterior burrs on most parts. “Plus, the twin-spindle lathes mean we can reach the back of the part without touching it,” she adds. “When we do the extra work to figure out how to not touch the part a second time,” Kufner adds, “we can reduce the cost by 25%.”
With this automation, SDP/SI has seen excellent results with unattended machining. Most lights-out production occurs through bar feeders, in addition to a DMG MORI Wasino that performs lights-out drilling, tapping and reaming using an integrated robot arm as part of a standard Wasino automation package.
Together, these techniques enable the company to perform 1,600-2,400 hours of unattended machining per month, a massive cost saver and dramatic improvement on throughput. “Working lights-out is an important way for us to reduce cost and pass those savings on to customers,” Kufner says.
The company is also constantly investing in new approaches to automation, including cobots.
Recently, the company purchased a Universal Robots cobot to attend one of the Haas cells, as well as some nearby DMG MORI mills. The cobot is equipped with door-opening attachments and grippers to tend the machines, and it can be wheeled between the different cells as needed.
The choice of a cobot over a traditional robot came to a number of factors:
With these goals in mind, the company’s decision to go with cobots makes perfect sense. Compared to traditional robot arms, the cobots fit much easier into the niche these machining centers fill.
However, the company is investing in more than just automation. Lately, it has dipped its toes into machine monitoring.
This year, SDP/SI took some careful first steps into machine monitoring with a system from Scytec. “We recently installed it on one side of the shop just to test it out and work out the bugs,” Anderson says. “We’re currently monitoring 19 machines.” The goal of this test was to discover what tangible benefits they could derive from machine monitoring, if any.
Here we see the Scytec machine monitoring system in place in SDP/SI’s test cells. Since installing this system on 19 machines, the company has seen a 10-15% improvement in spindle utilization for those manufacturing cells. Photo Credit: SDP/SI
The company chose Scytec because of its responsive customer service. “They were on-site during the entire installation,” Kufner says. “Compared to others,” Anderson adds, “they gave us the data we wanted to see in the way we wanted to see it.”
And what were the results of this test?
“Our spindle time is up 10-15%,” Anderson says. According to her and Kufner, the majority of this improvement comes from the ways that access to data has smoothed communication between machine operators and management.
“It brings in front of everyone’s faces whether a machine is running or not running, and the operator has to identify why it’s not running,” Anderson says. “It can be hard for machinists to convey how often the machines are down from mechanical issues,” Kufner adds, “but now we get to tap into data from the machine to alleviate the stress from the operator.”
“Our spindle time is up 10-15%.” – VP of Operations Sue Anderson, SDP/SI
By making the data visible and making everyone accountable, the shop has hard numbers to point to when improvements need to be made. “It allows us to address the problems and makes us accountable to the operators,” Kufner says. “It’s not a tool to beat employees over the head with, but a way to improve things and make their lives easier.”
Fortunately, the company had already invested a great deal into improving communication. “Before the move to our current facility, there were six of seven siloed operating areas with centralized decision-making,” says Kufner. Employees felt unable to act on their own initiative and felt they did not have permission to approach problems creatively.
“We broke down those silos and communication barriers,” Kufner continues. “This created a culture of open communication and led to employees who felt empowered to have ideas and act on them, to invest in the success of the business.”
This attitude of cooperation has proven vital for the success of the machine monitoring program, and the company plans to expand it. “We plan on expanding machine monitoring to the rest of the shop floor starting the next fiscal year,” Anderson says. Thanks to the company’s success earning the trust of its employees, this investment is likely to pay off.
Different tools and machining strategies have driven this shop to seek new efficiencies beyond its most demanding work and most capable machining center.
With so many choices in five-axis machining technology, how do you know which is best for your shop? First, consider the parts. Then, look at existing processes and potential five-axis benefits.

3d Touch Probe If you haven’t looked at 5-axis machining lately, a lot has changed. Advancements in 5-axis machines, controls and software have made this technology so affordable and easy to use that it can benefit almost any shop.