Starch is a primary foodstuff and acts as a key source of carbohydrate in global food production. Commercial starch production is a wet process and filtration plays a major role in the manufacturing procedure. Trevor Sparks describes the role that filtration fulfils in the process and highlights some of the challenges that have to be addressed.
The source of energy at the bottom of the food-chain feeding every living thing on earth is the sun, and the most common path for this energy to reach humans is through starch, a white powder and a polysaccharide of glucose. Starch is produced by plants to see them through periods with less or no sun (i.e. through the night or the winter) and they store it, conveniently for us, in seeds, grains and roots. While starch is produced commercially from many different crops, it is most widely obtained from corn, wheat, rice, potato and cassava. Several million tonnes of starch are produced annually. Wheat Starch Making Machine

The starch industry is a very large, global, multi-billion dollar operation with a number of large players. In common with many other industries, it has undergone a great deal of consolidation over the past few years.
The USA remains the largest producer, and also consumer, of the products of the starch industry, but the rest of the world is gaining ground.
In addition to acting as a source of carbohydrate, starch is also used to enhance the texture and consistency of soups and sauces as a thickening agent.
As well as its many uses in food, starch is used throughout the pharmaceutical, chemical and paper-making industries for its desirable properties as a filler, binding agent, stiffener for paper/cardboard, lubricant or adhesive.
The starches produced by the major crops vary considerably, with the starch grains ranging in size from around 5 μm to >100 μm, with rice starch having the finest and potato the largest. This has a major impact on how the particular type of starch is used, but also on the methods of production. Filtration, in particular, is strongly affected by particle size and distribution.
The functionality of the starch grains can be modified by heat or chemical treatment. This can be to make them stir into soup as a thickener more readily or to give them cationic properties so that they are attracted to negatively charged cellulose fibres when making paper, for example.
Finally, vast quantities of starch are converted through hydrolysis to sugars as glucose syrup. By weight, the production of syrup is greater than native and modified starch powder.
Commercial starch production is a wet process and filtration is a vital factor in the success of this process, serving both to remove moisture more cost effectively than evaporation and also to wash away impurities or modifying chemicals. This article will review the starch industry and the importance of filtration, looking at some of the ways that it can affect the overall success of a process and to review the industry that supplies equipment for this application.
Starch producers are frequently buffeted by the external forces of Mother Nature and the Market. Annual variation in rainfall and other weather conditions can affect the output of an entire region's starch industry and a sustained period without rain can lead to its closure. The market can also be manipulated, for example by political pressures to convert the energy stored in starch into fuels (e.g. ethanol).
One response to this uncertainty is to look for ways to add value to starch by modifying its functionality and extending its possible uses. This process of modification can transform the selling price of a starch, potentially increasing it by an order of magnitude.
Figure 2 shows a simplified flow-sheet for corn starch production. While the main target of this process is usually to produce large quantities, reliably, of native and modified starch that are suitable for application (often for the food industry), there are also a number of side-products, including corn oil, gluten (which may be added to strengthen wheat flour for bread-making) and other cellulosic material that may be used for animal feed.
The process, from agricultural crop (grain or root) to starch and its derivatives is bristling with solid-liquid separation and classification steps, from screening to remove fibres and husks through to the final filtration and washing process prior to thermal drying. The latter application is the focus of this article.
Starches vary in filterability according to their type and degree of modification (listed from relatively easy to filter to relatively difficult): potato; tapioca; corn; wheat; and rice. (Wheat is unusual because of its bi-modal particle size distribution – see Figure 4 and Box – Wheat starch).
This unusual property means that wheat starch factories usually classify into A- and B-types, for example using hydrocyclones. These two streams are then treated as separate products.
From a filtration perspective, these starches behave very differently, given the enormous difference in surface area and packing density within a filter cake. The A-type is simply more filterable in terms of throughput. This can lead to a dilemma when selecting suitable filtration equipment. Choosing the same equipment for both streams can give benefits in terms of operator knowledge and spare parts handling. On the other hand, it may prove more cost effective to use more basic (and therefore lower cost) equipment or the A-type and more specialised equipment for the B-type.
This is another illustration of how the outcomes of filtration processes are ultimately the aggregate outcome of countless billions of microscopic interactions between particles too small to see.
Modification also reduces the filterability of starch, so much so that the filtration area required may double.
Figure 5 looks more closely at the filtration step – the washing/de-watering of a modified starch (starch slurry) prior to thermal drying. The outcome of such filtration processes have a great bearing on the success of the overall production process, in terms of cost, quality, production volume and environmental impact. Four examples follow.
Starch production is a wet-process and it is normally supplied as dry powder, so the removal of moisture is a critical issue. Broadly speaking, we know how much energy is required to evaporate a given quantity of water. So, if we can reduce the moisture of filter cake that enters a dryer then it is possible to calculate the benefit in terms of energy (and hence fuel cost).
To illustrate how important and significant this can be, consider a process producing 10 tonnes per hour of starch. Suppose a method to reduce the cake moisture from 30% (weight basis) to 25% is found, perhaps changing the operation of the filtration step or even adopting a new filtration technology.
Table 1 shows that the estimated annual cost savings are very significant indeed, as are the implications in terms of CO2 emissions.
Consider that a starch process is limited by the capacity of the thermal dryer, in other words, its ability to evaporate water. Using the same example (30% versus 25% wt/wt), it can be shown that the capacity of the dryer, in terms of dry starch, can be increased by approximately 30%.
The starch industry is a very large consumer of water (nearly all of which ultimately leaves the plant either in a waste stream or as water vapour from dryers/evaporators). Minimising the use of water can be a key factor in the success of a starch plant, especially in parts of the world where water is not abundant.
The effectiveness of a filter cake washing process depends upon a number of factors. In the ideal situation, fresh water would pass through the filter cake as a uniform front, replacing all of the liquid in the cake as it proceeds. In this way, with a simple 1:1 replacement, all of the necessary washing would be achieved. However, in practice, macro- and microscopic variations in the cake properties mean that this wash will pass preferentially through some parts of the filter cake, while leaving other regions relatively untouched. Macroscopic variations may include large cracks in the cake, or regions that are washed-away by the incoming slurry or wash. Microscopically, even a filter cake that looks perfectly uniform contains variations, with some regions that are slightly more permeable than others.
In this non-ideal situation, a water ratio much higher than 1:1 may be required to reach a certain level of washing result. A particular strength of horizontal plate tower press filters is that they tend to produce macroscopically very uniform filter-cakes and, given the high pressures used, can also produce cakes that are highly consolidated and uniform in their microscopic structure so that water consumption can be minimised.
Despite all of the care and attention that the starch has received before it arrives at the primary separation step, a significant amount of starch is often lost to waste through cloudy filtrate and wash filtrate.
Rather than being sold to a customer, this starch, that has had so much invested in it, is then simply sent to a waste treatment system where it costs money to treat. Indeed some plants are limited by the capacity of their waste treatment plant.
Table 2 compares the cost of product loss for two filter types, Case A requires 4m3 wash water per tonne of solid starch and the filtrate contains 0.3% solids by weight. For Case B, these figures are 2m3/tonne and 0.02% respectively. (Case B could illustrate the effect of a new filter type or even a modification of the control system and filter cloth on an existing filter, for example).
Once again, the potential savings are considerable, but may still be dwarfed by the savings in waste treatment costs.
Filtration equipment must deal with a number of different phases of material – gas, liquid, sticky filter cake and dust. Since starch is an excellent food source for microbes, this presents a challenge for hygienic design and can make the difference between selling product as food starch at around £250/€300 per tonne or industrial starch at £100/€120 per tonne.
The operating principles and design of many pressure filters have their origins in the mining industry and equipment vendors have responded to the needs of the starch industry with designs that have fewer places for material to accumulate and built-in cleaning systems.
A number of factors can affect the outcome of a filtration process and in this section we will review some of the most important.
Over the past twenty years, there has been a significant increase in the number of starch factories using pressure filtration, and in particular automatic tower press filters (see Figure 7). Some continuous rotary pressure filtration devices have also shown some promise.
Uniform filter cakes are known to be more readily washable, using less wash water for the same result. Therefore, it is important to check that results from laboratory or pilot-scale trials on new equipment will scale up without compromise (it is relatively simple to make a uniform cake the size of a pizza, but more difficult if it is 5m2.
As with almost all filter applications, it is worthwhile trialing other filter cloths at bench-scale in order to see if it is possible to reduce the amount of starch lost to filtrate without reducing throughput. Recently, there have been major advances in filter cloth technology for this type of application.
Equipment selection ideally should be made in the full knowledge of how the filtration outcome translates into mission-critical outcomes:
Challenges of starch slurry handling and filtration
Also, relative to other applications, starch is an ‘easy’ material to filter in terms of the resistance to flow presented by the filter cake. However, this can lead to difficulties. Many starches are so easy to de-water that it is possible to over-fill filter equipment with starch. If left alone, the cake in a starch filter would continue to grow back through the feed piping to the feed pump.
As discussed in the Box, Challenges of starch slurry handling and filtration, starch slurries can be extremely troublesome because of their shear-thickening and fast-filtering behaviour. In general, it is best not to be too hasty in the treatment of starch; to allow it to flow into filtration equipment at a comfortable pace and to be very careful in how the feeding process is controlled (overfilling may even cause equipment damage).
Equipment vendors have responded to these challenges and may offer upgrades to existing equipment that reduce these risks, while optimising the washing step in terms of outcome and water consumption.
Given the fiercely competitive nature of the starch industry, there is a constant need to get ahead in terms of cost, quality, productivity and environmental performance. This need sits within the context of ever-increasing production volumes and a continuous search for ways to add value to the starch.
A number of trends are likely:
•The adoption of pressure filtration for the washing and de-watering, especially of modified starch, will continue.•There will also be developments in filter media, in particular in terms of cleanability and resistance to microbial growth.•Control systems will develop so that they can deal with variations in feed and continuously optimise the outcome of the filtration process in terms of wash water consumption.
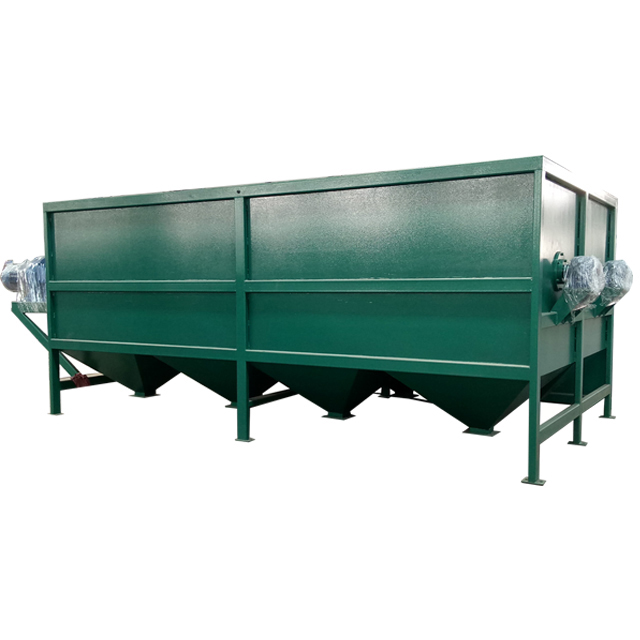
Wheat Starch Machinery Free access to this content is for qualifying individuals only. Corporate and institutional access requires an appropriate license or subscription. For more information contact institutions@markallengroup.com