Schneider Electric Altivar Soft Starter
15/05/2024 Atlas Copco Compressors UK Brushed Dc Servo Motor
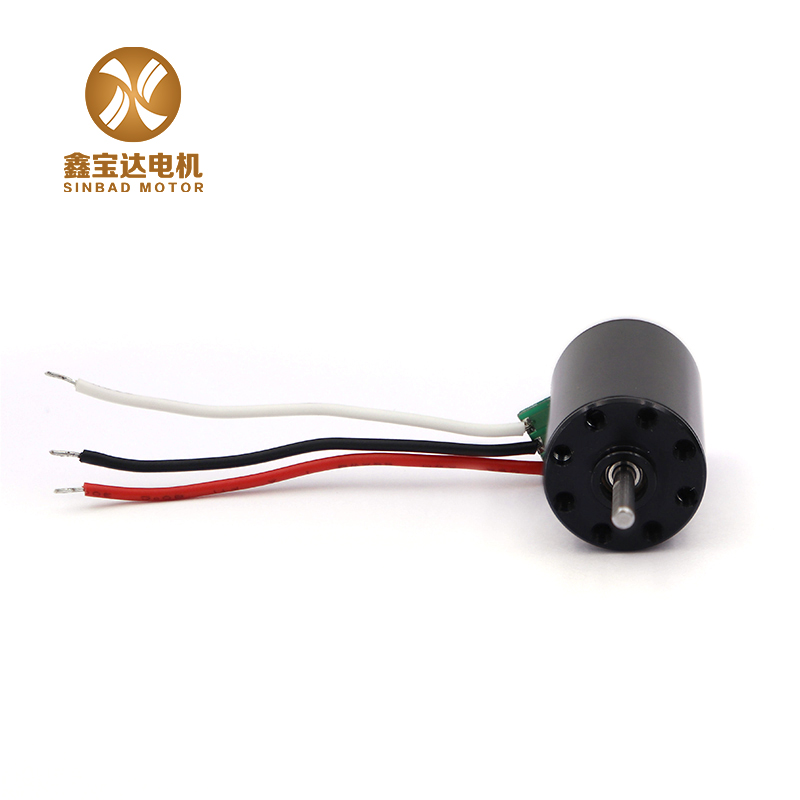
Portescap has provided a global defence manufacturer with a brushed DC motor and gear solution to control the accuracy of surface vessel-launched torpedo tubes. Portescap was awarded the contract based on its precise control, compact and low heat motor design, as well as the ability to meet stringent military specifications. Portescap’s engineers worked closely with the defence manufacturer to optimise the customised motion solution.
Accurate spindle control within a torpedo launch system is vital to manage the depth at which a torpedo will operate. When it has been launched from the tube, the torpedo’s internal system controls the dive planes on its tail to ensure fine depth modulation. However, initial launch angle precision is vital to ensure a torpedo’s ultimate depth accuracy, especially when the target range can extend over multiple miles. The spindle rotates the torpedo tube and aligns it with the firing direction, and a motor is vital to control the spindle angle for launch, ensuring that the torpedo can hit its target.
The defence leader needed a motion solution that could achieve highly accurate positional control, while also provide high durability. In the marine environment, the solution needed to provide protection against water and oil ingress, and meet Military-Standard (MIL-STD) specification, also known as MIL-SPEC. The defence
manufacturer approached Portescap based on its track record across similar projects, as well as its ability to effectively manage the high level of customisation required.
Portescap provided a brushed DC motor for this application for a number of reasons. As the torpedo tube spindles wouldn’t be in constant operation, instead requiring infrequent, high acceleration and accurate control, a brushed DC motor would ensure the durability required for months at sea. As the brush DC is simpler in design compared to a brushless DC motor, not requiring external electronic control to achieve commutation, they would be easier to maintain, which would be crucial while on operations. Portescap specified its 35NT brush motor with an R32 gearhead as a platform for customisation.
Neodymium magnet and coreless design
To ensure accurate and smooth control of the torpedo tube, as well as achieving the required acceleration, Portescap specified a brushed DC motor equipped with a neodymium magnet, generating a stronger magnetic field to boost the torque required for high acceleration. This was also combined with a coreless approach, removing the traditional iron core from the original DC brushed motor design.
A coreless motor would also contribute to optimising precision. Coreless motors provide smooth motion by removing the effect of cogging torque, the uneven magnetic force created as an iron core rotor turns. Instead, the coreless design’s reliance on a wire coil rotor with permanent magnets positioned around it would ensure a uniform magnetic force. This would give smoother acceleration for high precision, enhanced by the lower inertia provided by the coreless design.
The selection of a neodymium magnet would increase power density, optimising torque while achieving the compact dimensions and lower mass, critical for the torpedo tube’s specification. The coreless design helps achieve this requirement, where, despite the addition of permanent magnets, the absence of the iron core would lower overall mass.
Minimising heat within the space-constrained environment was also critical. The neodymium magnets would help maintain a low heat output by reducing energy losses due to heat and friction. Their higher magnetic field strength requires less current to produce the same amount of torque, with lower heat losses as a result. Moreover, the coreless design minimises hysteresis, the resistance created through magnetisation and demagnetisation during operation, and lower eddy current losses that occur due to induction of the current against the stator’s inherent resistance. An iron core is the main source of these energy losses, so the coreless design would minimise heat generation.
While Portescap’s standard motors are built for long life, to reach the specific military specification requirements meant that Portescap’s design team worked closely with the defence manufacturer’s engineers. Further development for the prevention of liquid ingress was achieved, creating a fully sealed, impermeable unit. The military inspection approval rating required enhanced modifications to cable and terminal outputs, which Portescap’s design team also implemented to add durability
To ensure a precision control motor system that would operate in the most testing arena, close access to a motion design team was fundamental to the OEM. Combined with robust manufacturing processes, the partnership resulted in successful project completion.
For more information, please contact: Portescap SA Rue Jardiniere 157 CH 2300 La Chaux-de-Fonds Switzerland Tel: +41 32 925 62 40 Email: Nicole.Monaco@portescap.com Web: https://www.portescap.com
Process and Control Today are not responsible for the content of submitted or externally produced articles and images. Click here to email us about any errors or omissions contained within this article.
Sign-up for our weekly eNewsletter
Advertise with us | Media pack
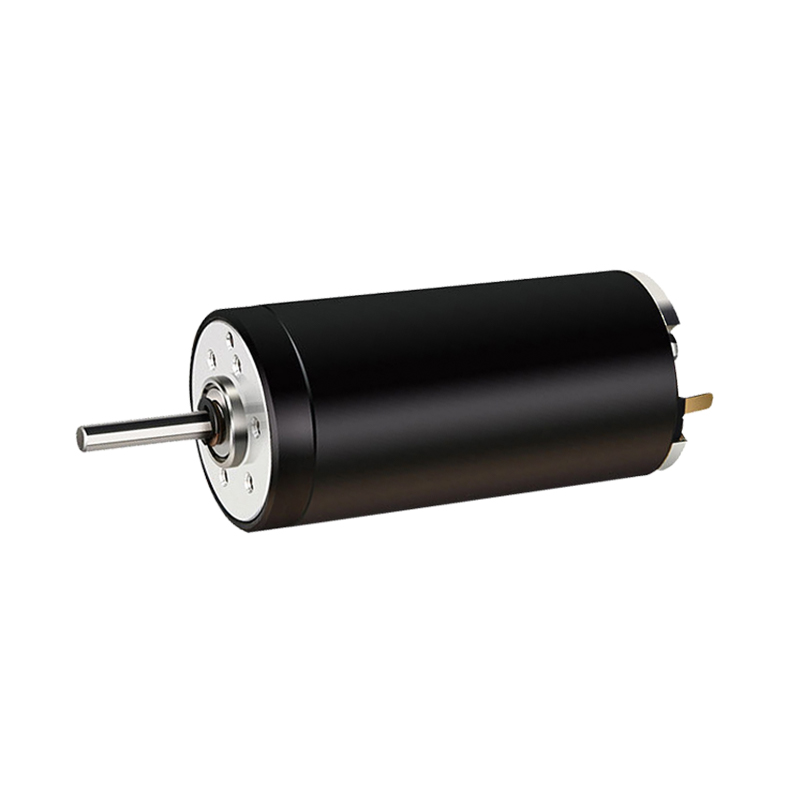
Coreless Micro Dc Motor © Copyright 1999-2024 Process and Control Today Ltd Registered in England No. 3733110 - studio44