There was a lot of talk about synergy, when Amut SpA (Novara, Italy), a maker of extruders, thermoformers and plastics recycling equipment, acquired packaging equipment builder Dolci Bielloni in February 2015. That synergy has come to fruition, says the company, now named Amut Dolci Bielloni, with a cast extrusion line for stretch film that achieves a consistent 750 m/min production speed.
There was a lot of talk about synergy , when Amut SpA (Novara, Italy), a maker of extruders, thermoformers and plastics recycling equipment, acquired packaging equipment builder Dolci Bielloni in February 2015. That synergy has come to fruition, says the company, now named Amut Dolci Bielloni, with a cast extrusion line for stretch film that achieves a consistent 750 m/min production speed. Plastic Lldpe Stretch Film

The concept line, which was first introduced at an open house in May, has a seven-layer configuration with six extruders. The 2000- and 3000-mm versions achieve net outputs of 1500 and 2400 kg/h, respectively.
Amut Dolci Bielloni cites the system's following features:
water-cooled motors in the extruders, oil-cooling systems in the gearboxes and long screws maximize homogenization and output;
large-diameter double cylinders in the cooling unit are specifically designed for the production of super-power stretch film;
a high-speed winder reaching production speeds up to 800 m/min is suitable for in-line jumbo, machine and hand-roll slitting;
both versions sport a compact design with a total 121-m² footprint;
energy consumption is a modest 0.4 kW/kg;
the systems have a low-thickness production capability, with a short path from the chill roll to the winder to enable fast startups.
Scrap recovery is done by inserting the fluff on one side of the extruder through a cold channel. A filtration system ensures dust-free fluff collection. The fluff is stored in a dedicated silo during startup and is recovered in-line during processing.
Layout of the extrusion system has been optimized: All of the extruders and accompanying screen changers are mounted in a parallel configuration. This arrangement makes the best use of available space while facilitating maintenance and screen changing operations, according to Amut Dolci Bielloni.
Dual workstations with touch screens allow the operator to work in the chill roll area or near the winder. All relevant parameters are displayed on both workstations.
Before unloading, each roll is weighed to verify that it meets preset parameters. Variations are reported and the line automatically resets as a result.
Quality Issues Involving China-made Plastic Syringes ‘More Widespread’ Than FDA Thought
Breaking News in Flexible Packaging March 2024
Breakthrough Bottle Cap Made from Bacteria Fermentation
Seven Ways to Grow Profits Without Adding Customers That Companies Often Overlook
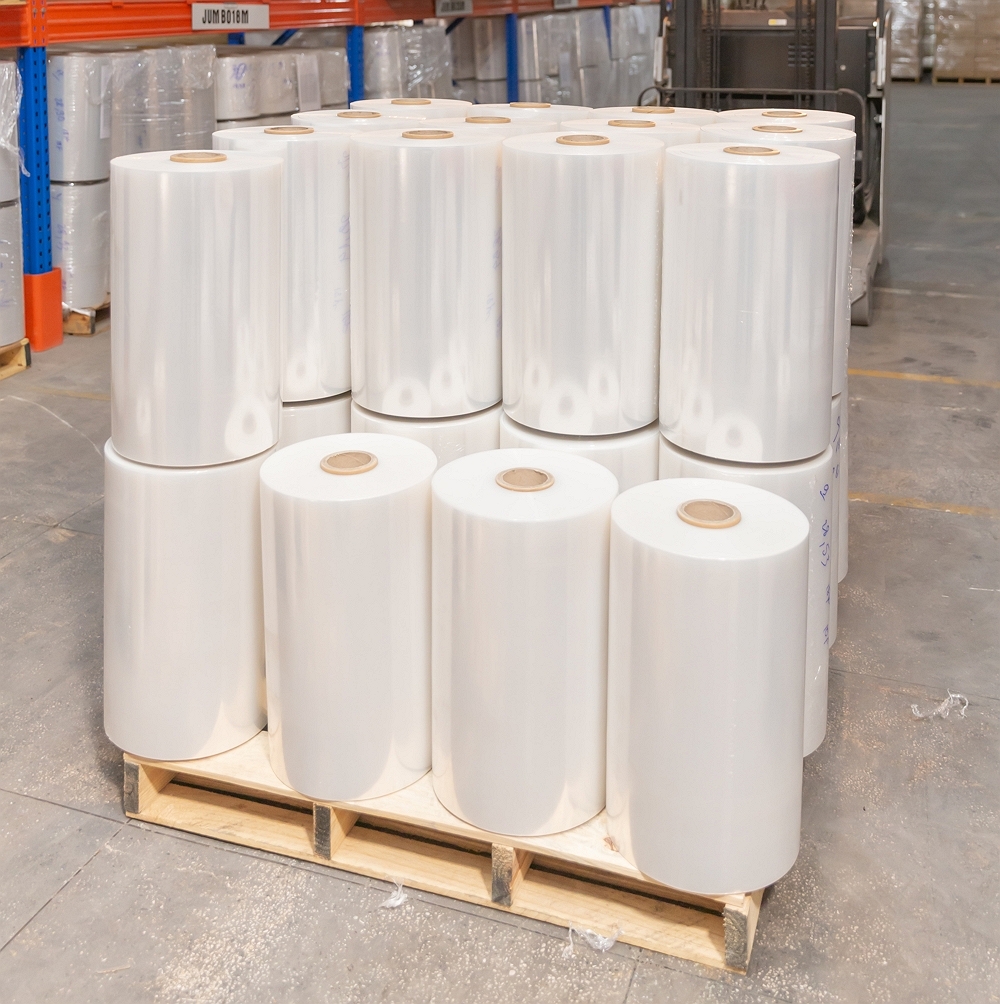
Bundling Stretch Film Copyright © 2024 All rights reserved. Informa Markets, a trading division of Informa PLC.