With increased work volume and workload from the Infrastructure Act, “you're going to see an increase in risk and hazard to workers.”
Editor’s note: This is part of an ongoing series, BPA's evil cousin. See related reporting on how ramped-up US construction exposes workers to BADGE. Surgical Drapes
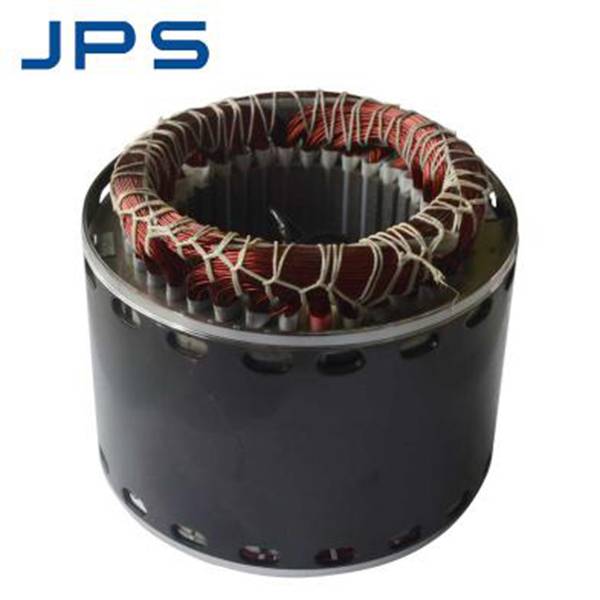
BOSTON — The River Street bridge that crosses over train lines in Boston’s Hyde Park neighborhood was built in 1883 and its undergirding steel beams are rusted beyond repair, riddled with holes and flaking brown metal chunks. Above ground tells a similar story, with rusty, pockmarked crossbars and paint peeling off the bridge’s low trusses. Closed now to vehicle traffic, the bridge is enshrouded with green plastic fencing to keep people out of the idle construction site.
The simple bridge carries not only traffic across a main road traversing the neighborhood, but it also carries electric, gas, water and telephone lines and wiring for Amtrak’s high-speed trains. It’s one of thousands across the country that will be repaired, with a new bridge built alongside it for the utility lines, with help from the federal Infrastructure Act.
One of the final steps that construction workers will take to prepare the bridge for reopening is to paint layer after layer of protective epoxy resin and other coatings to slow the inevitable march of corrosion from weathering. The protective coatings contain a bevy of toxic chemicals, including bisphenol-A diglycidyl ether, or BADGE, which is ubiquitous on construction sites. Though far less studied than its cousin, bisphenol A, BADGE may be just as harmful to human health, according to researchers.
BADGE is one of thousands of harmful chemicals that commercial painters may be exposed to, according to the National Institute for Occupational Safety and Health, or NIOSH. Paints and coatings are complex mixtures of pigments, binders or resins, solvents, filler chemicals, and, increasingly, nanoparticles. The World Health Organization’s International Agency for Research on Cancer, or IARC, has classified the occupation of painter as a definitive Group 1 cancer risk, citing increased risk of lung and bladder cancer and mesothelioma, and limited evidence for childhood leukemia associated with maternal exposure as a painter. There is not enough evidence, however, to pinpoint which chemicals are causing the increased cancer risk. Epoxy resins, within paint systems, are also complex mixtures. They typically contain two components that the worker mixes prior to applying the product. Part A contains the resin material, which is often BADGE and other diluents, and Part B contains solvent blends, polyamine hardeners or catalysts, nanomaterials and other additives including crystalline silica and flame retardants. Once the two parts are mixed, they react and form other chemicals. “We are dealing with over 100 chemicals in these mixtures, prior to mixing A and B,” and then the mixing creates new chemicals, and “every single particle in the aerosol is this complex mixture of tens and tens of chemicals,” Dhimiter Bello, professor and associate dean for research at the Zuckerberg College of Health Sciences at the University of Massachusetts Lowell, told EHN. Nevertheless, he added, “BADGE is a significant dominant exposure in epoxy systems. By all metrics we can prioritize the chemical at the very top as a chemical of concern.” Workers may be exposed to BADGE, nanoparticles (which can carry chemicals deep into the lungs) and other chemicals while mixing the two parts, applying the product, and during the time it takes for the material to cure or harden. Curing can take anywhere from a few hours to days, depending on the product. A spokesperson for the American Chemistry Council, Tom Flanagin, acknowledged in an email that, “Before the curing process, the starting building blocks, resins and hardeners may show hazardous properties and can produce irritating or sensitizing effects.” But he added that following basic precautions outlined in safety data sheets “helps epoxy systems to be handled safely.” The curing process especially worries Ken Seal, an apprenticeship training representative at the International Union of Painters and Allied Trades Finishing Trades Institute, because safety data sheets don’t provide information on the chemicals created by the reaction. “When you mix epoxies together, and you’ve got that exothermic reaction going on, there's no [safety data sheet] out there that tells me what that reaction is.” “If you've ever done an epoxy floor system, and you watched it curing, you can see a haze coming off the floor… and, wow, that's got to be dangerous,” he said. Protecting construction worker health The American Chemistry Council reports 13.1 million construction workers handle epoxy resins in the U.S. Thousands of new construction projects funded by the Infrastructure Investment and Jobs Act will increase epoxy resin use, and worker exposures. More than 2,800 bridge projects were underway as of November 2022 with funding from the Infrastructure Act and many more projects are yet to come, along with hundreds to thousands of port, rail and clean transportation and water projects. Some 800,000 construction jobs will be created by the law, according to the U.S. Department of Labor. Why the Infrastructure Investment and Jobs Act should fund research on construction hazards “With that increased work volume and workload, you're going to see an increase in risk and hazard to workers,” Bernie Mizula, director of Environmental Health and Safety at International Union of Painters and Allied Trades Trades Institute, and a certified industrial hygienist and certified safety professional, told EHN. If substances used on job sites are “very dangerous,” he continued, “we need to remove those things and try to substitute them with something less dangerous for the workers.” If that’s not possible, there’s a “hierarchy of controls,” he added, starting with engineering solutions, like ventilation, moving next to administrative controls (such as training requirements and health and safety site programs) and finally moving to personal protection — gloves, chemical resistant suits and respirators. Often, multiple controls are needed. The International Union of Painters and Allied Trades provides a lot of training to its members about job hazards and how to protect themselves. “But we can only go so far because the employer has to have a written safety program and they have to train the workers,” Mizula said, adding that the general contractor on a construction site has overall responsibility for safety including providing a written hazard communications program and accessible means to all the safety data sheets for every chemical used on site. Regulations are not keeping up with the science OSHA spokesperson Kimberly Darby wrote in an email that, “OSHA is not pursuing regulatory action specific to epoxy resins and/or BADGE at this time. However, other current OSHA standards apply,” including regulations for hazard communication, respiratory protection and what’s known as the General Duty Clause. The General Duty Clause is a catchall, or fail-safe, that inspectors can use when clear job hazards are present but there is no specific standard requiring protective measures. However, it’s “a much higher bar for the inspector,” David Michaels, an epidemiologist and professor at the George Washington University School of Public Health who served as Assistant Secretary of Labor for OSHA from 2009 to 2017, told EHN. Plus, he added, “If OSHA went into these workplaces, it wouldn’t even be clear what they would be measuring for” because there are no standards, or monitoring methods. A chemical like BADGE doesn’t have a legal exposure limit, added Michaels, because “the OSHA standard setting process is broken.” First, it takes a tremendous amount of time and resources to develop a new standard. The agency must assess the economic and technological feasibility of controls and work with NIOSH to conduct human health studies to show that significant risks result from exposure and that a proposed standard would reduce those risks. “You have to show that people are getting sick,” he said. “You can't just say animal studies suggest people will be sick. You need human studies to be able to make the statement that you will reduce exposure.” Moreover, “OSHA knows from historical experience that every health standard will be contested in court by industries that are forced to make investments to protect workers, and they want to be sure that a standard is airtight,” he said. Related: The hidden, potential cancer-causing, danger in woodworking and art supplies The rigorous technical requirements for an OSHA standard are why the intervention-focused research of Dhimiter Bello and his wife, Anila, a research professor in the Department of Public Health at the University of Massachusetts Lowell, is so important. They not only monitored exposures to BADGE and its metabolites in humans, they studied how bridge painters were using personal protective equipment (i.e., respirators, gloves and coveralls) on job sites and how that may have correlated with their urinary levels of the chemical. The study group was too small for the Bellos to reach conclusions about the effectiveness of different types of personal protective equipment, but their research could help inform future NIOSH studies. ACC spokesperson Tom Flanagin said, "Industry understands the main risk to workers [from epoxy resins] is via skin contact, and the correct use of personal protective equipment (PPE) and skin protectant is essential.” That may not be the case on construction job sites. Mitchell Blum, a certified safety processional for MB Safety Consulting Inc. who conducts safety training for AMPP, the U.S. association for coating manufacturers, told EHN that industry is unaware of the dangers of BADGE in epoxy resin coatings because there’s little research on it and no OSHA requirements. “When you look at that very specific ingredient, there's not a lot of information,” he said, adding that the recent studies on BADGE that EHN sent him “do not reflect, at this point, regulatory ideas. We don't have a reference as far as good, bad, [or] what to do.” That’s especially true about research on skin issues, he said, “which are brand new to all of us. There are many non-regulatory people, universities and governmental agencies conducting studies as to how chemicals can permeate the skin. Until there is a regulatory review, testing of the skin will not happen in the construction industry anytime in the near future.” The coating industry focuses its safety resources on protecting workers who remove old paints before applying new coatings because of the high lead content in older paints, said Blum, whose main clients are bridge painting contractors. “We’re suited up; we have a standard; we follow regulatory ideas. But on the coating application side, we are so far behind what we need to do. We don’t protect workers at this point.”The best chance at worker protection The American Chemistry Council reports 13.1 million construction workers handle epoxy resins in the U.S. Credit: Jeriden Villegas/Unsplash Meanwhile, back in Boston, the River Street bridge awaits repairs while the Massachusetts Department of Transportation completes the design phase. A general contractor hasn’t been chosen for the job, but with no OSHA limits to force contractors to protect the painters applying BADGE-laden epoxy resin coatings, union safety training — and membership — offer painters their best chance at protection. “A union employee has routes,” Seal said. “They can go to a business agent and say, ‘this is what's going on at the job site. I'm afraid I’m going to get hurt. I’m afraid I’m going to get killed.’ And then the business agent steps in and takes care of the issue. A non-union person, an immigrant person, they don't have an out.” Seal hopes the union’s training programs will help motivate its members to put safety first and shift the risk-taking bravado that permeated the trade when he started out 38 years ago. “We really hit heavily on the fact that the chemicals that you're getting in your body might not affect you during your career, but when you decide to retire, you might have issues. That's why lifespans have been really short in the construction trades.” As for his own exposures on the job, Seal tries not to worry. “Right now, my health is good,” he said. “But I still worry that I'm going to go to the doctor one day, and they're going to tell me that, hey, you have issues because of the time in life that I started the trade." This reporting is part of BPA's evil cousin: an ongoing series on the hazards and regulatory blind spots associated with BADGE, a chemical cousin of BPA. The series is generously supported by the Fine Fund.
BADGE is one of thousands of harmful chemicals that commercial painters may be exposed to, according to the National Institute for Occupational Safety and Health, or NIOSH. Paints and coatings are complex mixtures of pigments, binders or resins, solvents, filler chemicals, and, increasingly, nanoparticles. The World Health Organization’s International Agency for Research on Cancer, or IARC, has classified the occupation of painter as a definitive Group 1 cancer risk, citing increased risk of lung and bladder cancer and mesothelioma, and limited evidence for childhood leukemia associated with maternal exposure as a painter. There is not enough evidence, however, to pinpoint which chemicals are causing the increased cancer risk.
Epoxy resins, within paint systems, are also complex mixtures. They typically contain two components that the worker mixes prior to applying the product. Part A contains the resin material, which is often BADGE and other diluents, and Part B contains solvent blends, polyamine hardeners or catalysts, nanomaterials and other additives including crystalline silica and flame retardants. Once the two parts are mixed, they react and form other chemicals.
“We are dealing with over 100 chemicals in these mixtures, prior to mixing A and B,” and then the mixing creates new chemicals, and “every single particle in the aerosol is this complex mixture of tens and tens of chemicals,” Dhimiter Bello, professor and associate dean for research at the Zuckerberg College of Health Sciences at the University of Massachusetts Lowell, told EHN.
Nevertheless, he added, “BADGE is a significant dominant exposure in epoxy systems. By all metrics we can prioritize the chemical at the very top as a chemical of concern.”
Workers may be exposed to BADGE, nanoparticles (which can carry chemicals deep into the lungs) and other chemicals while mixing the two parts, applying the product, and during the time it takes for the material to cure or harden. Curing can take anywhere from a few hours to days, depending on the product.
A spokesperson for the American Chemistry Council, Tom Flanagin, acknowledged in an email that, “Before the curing process, the starting building blocks, resins and hardeners may show hazardous properties and can produce irritating or sensitizing effects.” But he added that following basic precautions outlined in safety data sheets “helps epoxy systems to be handled safely.”
The curing process especially worries Ken Seal, an apprenticeship training representative at the International Union of Painters and Allied Trades Finishing Trades Institute, because safety data sheets don’t provide information on the chemicals created by the reaction. “When you mix epoxies together, and you’ve got that exothermic reaction going on, there's no [safety data sheet] out there that tells me what that reaction is.”
“If you've ever done an epoxy floor system, and you watched it curing, you can see a haze coming off the floor… and, wow, that's got to be dangerous,” he said.
The American Chemistry Council reports 13.1 million construction workers handle epoxy resins in the U.S. Thousands of new construction projects funded by the Infrastructure Investment and Jobs Act will increase epoxy resin use, and worker exposures.
More than 2,800 bridge projects were underway as of November 2022 with funding from the Infrastructure Act and many more projects are yet to come, along with hundreds to thousands of port, rail and clean transportation and water projects. Some 800,000 construction jobs will be created by the law, according to the U.S. Department of Labor.
“With that increased work volume and workload, you're going to see an increase in risk and hazard to workers,” Bernie Mizula, director of Environmental Health and Safety at International Union of Painters and Allied Trades Trades Institute, and a certified industrial hygienist and certified safety professional, told EHN.
If substances used on job sites are “very dangerous,” he continued, “we need to remove those things and try to substitute them with something less dangerous for the workers.” If that’s not possible, there’s a “hierarchy of controls,” he added, starting with engineering solutions, like ventilation, moving next to administrative controls (such as training requirements and health and safety site programs) and finally moving to personal protection — gloves, chemical resistant suits and respirators. Often, multiple controls are needed.
The International Union of Painters and Allied Trades provides a lot of training to its members about job hazards and how to protect themselves. “But we can only go so far because the employer has to have a written safety program and they have to train the workers,” Mizula said, adding that the general contractor on a construction site has overall responsibility for safety including providing a written hazard communications program and accessible means to all the safety data sheets for every chemical used on site.
OSHA spokesperson Kimberly Darby wrote in an email that, “OSHA is not pursuing regulatory action specific to epoxy resins and/or BADGE at this time. However, other current OSHA standards apply,” including regulations for hazard communication, respiratory protection and what’s known as the General Duty Clause.
The General Duty Clause is a catchall, or fail-safe, that inspectors can use when clear job hazards are present but there is no specific standard requiring protective measures. However, it’s “a much higher bar for the inspector,” David Michaels, an epidemiologist and professor at the George Washington University School of Public Health who served as Assistant Secretary of Labor for OSHA from 2009 to 2017, told EHN. Plus, he added, “If OSHA went into these workplaces, it wouldn’t even be clear what they would be measuring for” because there are no standards, or monitoring methods.
A chemical like BADGE doesn’t have a legal exposure limit, added Michaels, because “the OSHA standard setting process is broken.” First, it takes a tremendous amount of time and resources to develop a new standard. The agency must assess the economic and technological feasibility of controls and work with NIOSH to conduct human health studies to show that significant risks result from exposure and that a proposed standard would reduce those risks.
“You have to show that people are getting sick,” he said. “You can't just say animal studies suggest people will be sick. You need human studies to be able to make the statement that you will reduce exposure.”
Moreover, “OSHA knows from historical experience that every health standard will be contested in court by industries that are forced to make investments to protect workers, and they want to be sure that a standard is airtight,” he said.
The rigorous technical requirements for an OSHA standard are why the intervention-focused research of Dhimiter Bello and his wife, Anila, a research professor in the Department of Public Health at the University of Massachusetts Lowell, is so important. They not only monitored exposures to BADGE and its metabolites in humans, they studied how bridge painters were using personal protective equipment (i.e., respirators, gloves and coveralls) on job sites and how that may have correlated with their urinary levels of the chemical. The study group was too small for the Bellos to reach conclusions about the effectiveness of different types of personal protective equipment, but their research could help inform future NIOSH studies.
ACC spokesperson Tom Flanagin said, "Industry understands the main risk to workers [from epoxy resins] is via skin contact, and the correct use of personal protective equipment (PPE) and skin protectant is essential.” That may not be the case on construction job sites.
Mitchell Blum, a certified safety processional for MB Safety Consulting Inc. who conducts safety training for AMPP, the U.S. association for coating manufacturers, told EHN that industry is unaware of the dangers of BADGE in epoxy resin coatings because there’s little research on it and no OSHA requirements.
“When you look at that very specific ingredient, there's not a lot of information,” he said, adding that the recent studies on BADGE that EHN sent him “do not reflect, at this point, regulatory ideas. We don't have a reference as far as good, bad, [or] what to do.”
That’s especially true about research on skin issues, he said, “which are brand new to all of us. There are many non-regulatory people, universities and governmental agencies conducting studies as to how chemicals can permeate the skin. Until there is a regulatory review, testing of the skin will not happen in the construction industry anytime in the near future.”
The coating industry focuses its safety resources on protecting workers who remove old paints before applying new coatings because of the high lead content in older paints, said Blum, whose main clients are bridge painting contractors. “We’re suited up; we have a standard; we follow regulatory ideas. But on the coating application side, we are so far behind what we need to do. We don’t protect workers at this point.”
The American Chemistry Council reports 13.1 million construction workers handle epoxy resins in the U.S.
Meanwhile, back in Boston, the River Street bridge awaits repairs while the Massachusetts Department of Transportation completes the design phase. A general contractor hasn’t been chosen for the job, but with no OSHA limits to force contractors to protect the painters applying BADGE-laden epoxy resin coatings, union safety training — and membership — offer painters their best chance at protection.
“A union employee has routes,” Seal said. “They can go to a business agent and say, ‘this is what's going on at the job site. I'm afraid I’m going to get hurt. I’m afraid I’m going to get killed.’ And then the business agent steps in and takes care of the issue. A non-union person, an immigrant person, they don't have an out.”
Seal hopes the union’s training programs will help motivate its members to put safety first and shift the risk-taking bravado that permeated the trade when he started out 38 years ago. “We really hit heavily on the fact that the chemicals that you're getting in your body might not affect you during your career, but when you decide to retire, you might have issues. That's why lifespans have been really short in the construction trades.”
As for his own exposures on the job, Seal tries not to worry. “Right now, my health is good,” he said. “But I still worry that I'm going to go to the doctor one day, and they're going to tell me that, hey, you have issues because of the time in life that I started the trade."
This reporting is part of BPA's evil cousin: an ongoing series on the hazards and regulatory blind spots associated with BADGE, a chemical cousin of BPA. The series is generously supported by the Fine Fund.
Meg Wilcox is an environmental journalist and photographer, covering climate change and energy, environmental health, fisheries management and sustainable food systems.
Editor’s note: This is part of an ongoing series, BPA's evil cousin. See related reporting on how ramped-up US construction exposes workers to BADGE.
BOSTON — The River Street bridge that crosses over train lines in Boston’s Hyde Park neighborhood was built in 1883 and its undergirding steel beams are rusted beyond repair, riddled with holes and flaking brown metal chunks. Above ground tells a similar story, with rusty, pockmarked crossbars and paint peeling off the bridge’s low trusses. Closed now to vehicle traffic, the bridge is enshrouded with green plastic fencing to keep people out of the idle construction site.
The simple bridge carries not only traffic across a main road traversing the neighborhood, but it also carries electric, gas, water and telephone lines and wiring for Amtrak’s high-speed trains. It’s one of thousands across the country that will be repaired, with a new bridge built alongside it for the utility lines, with help from the federal Infrastructure Act.
One of the final steps that construction workers will take to prepare the bridge for reopening is to paint layer after layer of protective epoxy resin and other coatings to slow the inevitable march of corrosion from weathering. The protective coatings contain a bevy of toxic chemicals, including bisphenol-A diglycidyl ether, or BADGE, which is ubiquitous on construction sites. Though far less studied than its cousin, bisphenol A, BADGE may be just as harmful to human health, according to researchers.
BADGE is one of thousands of harmful chemicals that commercial painters may be exposed to, according to the National Institute for Occupational Safety and Health, or NIOSH. Paints and coatings are complex mixtures of pigments, binders or resins, solvents, filler chemicals, and, increasingly, nanoparticles. The World Health Organization’s International Agency for Research on Cancer, or IARC, has classified the occupation of painter as a definitive Group 1 cancer risk, citing increased risk of lung and bladder cancer and mesothelioma, and limited evidence for childhood leukemia associated with maternal exposure as a painter. There is not enough evidence, however, to pinpoint which chemicals are causing the increased cancer risk. Epoxy resins, within paint systems, are also complex mixtures. They typically contain two components that the worker mixes prior to applying the product. Part A contains the resin material, which is often BADGE and other diluents, and Part B contains solvent blends, polyamine hardeners or catalysts, nanomaterials and other additives including crystalline silica and flame retardants. Once the two parts are mixed, they react and form other chemicals. “We are dealing with over 100 chemicals in these mixtures, prior to mixing A and B,” and then the mixing creates new chemicals, and “every single particle in the aerosol is this complex mixture of tens and tens of chemicals,” Dhimiter Bello, professor and associate dean for research at the Zuckerberg College of Health Sciences at the University of Massachusetts Lowell, told EHN. Nevertheless, he added, “BADGE is a significant dominant exposure in epoxy systems. By all metrics we can prioritize the chemical at the very top as a chemical of concern.” Workers may be exposed to BADGE, nanoparticles (which can carry chemicals deep into the lungs) and other chemicals while mixing the two parts, applying the product, and during the time it takes for the material to cure or harden. Curing can take anywhere from a few hours to days, depending on the product. A spokesperson for the American Chemistry Council, Tom Flanagin, acknowledged in an email that, “Before the curing process, the starting building blocks, resins and hardeners may show hazardous properties and can produce irritating or sensitizing effects.” But he added that following basic precautions outlined in safety data sheets “helps epoxy systems to be handled safely.” The curing process especially worries Ken Seal, an apprenticeship training representative at the International Union of Painters and Allied Trades Finishing Trades Institute, because safety data sheets don’t provide information on the chemicals created by the reaction. “When you mix epoxies together, and you’ve got that exothermic reaction going on, there's no [safety data sheet] out there that tells me what that reaction is.” “If you've ever done an epoxy floor system, and you watched it curing, you can see a haze coming off the floor… and, wow, that's got to be dangerous,” he said. Protecting construction worker health The American Chemistry Council reports 13.1 million construction workers handle epoxy resins in the U.S. Thousands of new construction projects funded by the Infrastructure Investment and Jobs Act will increase epoxy resin use, and worker exposures. More than 2,800 bridge projects were underway as of November 2022 with funding from the Infrastructure Act and many more projects are yet to come, along with hundreds to thousands of port, rail and clean transportation and water projects. Some 800,000 construction jobs will be created by the law, according to the U.S. Department of Labor. Why the Infrastructure Investment and Jobs Act should fund research on construction hazards “With that increased work volume and workload, you're going to see an increase in risk and hazard to workers,” Bernie Mizula, director of Environmental Health and Safety at International Union of Painters and Allied Trades Trades Institute, and a certified industrial hygienist and certified safety professional, told EHN. If substances used on job sites are “very dangerous,” he continued, “we need to remove those things and try to substitute them with something less dangerous for the workers.” If that’s not possible, there’s a “hierarchy of controls,” he added, starting with engineering solutions, like ventilation, moving next to administrative controls (such as training requirements and health and safety site programs) and finally moving to personal protection — gloves, chemical resistant suits and respirators. Often, multiple controls are needed. The International Union of Painters and Allied Trades provides a lot of training to its members about job hazards and how to protect themselves. “But we can only go so far because the employer has to have a written safety program and they have to train the workers,” Mizula said, adding that the general contractor on a construction site has overall responsibility for safety including providing a written hazard communications program and accessible means to all the safety data sheets for every chemical used on site. Regulations are not keeping up with the science OSHA spokesperson Kimberly Darby wrote in an email that, “OSHA is not pursuing regulatory action specific to epoxy resins and/or BADGE at this time. However, other current OSHA standards apply,” including regulations for hazard communication, respiratory protection and what’s known as the General Duty Clause. The General Duty Clause is a catchall, or fail-safe, that inspectors can use when clear job hazards are present but there is no specific standard requiring protective measures. However, it’s “a much higher bar for the inspector,” David Michaels, an epidemiologist and professor at the George Washington University School of Public Health who served as Assistant Secretary of Labor for OSHA from 2009 to 2017, told EHN. Plus, he added, “If OSHA went into these workplaces, it wouldn’t even be clear what they would be measuring for” because there are no standards, or monitoring methods. A chemical like BADGE doesn’t have a legal exposure limit, added Michaels, because “the OSHA standard setting process is broken.” First, it takes a tremendous amount of time and resources to develop a new standard. The agency must assess the economic and technological feasibility of controls and work with NIOSH to conduct human health studies to show that significant risks result from exposure and that a proposed standard would reduce those risks. “You have to show that people are getting sick,” he said. “You can't just say animal studies suggest people will be sick. You need human studies to be able to make the statement that you will reduce exposure.” Moreover, “OSHA knows from historical experience that every health standard will be contested in court by industries that are forced to make investments to protect workers, and they want to be sure that a standard is airtight,” he said. Related: The hidden, potential cancer-causing, danger in woodworking and art supplies The rigorous technical requirements for an OSHA standard are why the intervention-focused research of Dhimiter Bello and his wife, Anila, a research professor in the Department of Public Health at the University of Massachusetts Lowell, is so important. They not only monitored exposures to BADGE and its metabolites in humans, they studied how bridge painters were using personal protective equipment (i.e., respirators, gloves and coveralls) on job sites and how that may have correlated with their urinary levels of the chemical. The study group was too small for the Bellos to reach conclusions about the effectiveness of different types of personal protective equipment, but their research could help inform future NIOSH studies. ACC spokesperson Tom Flanagin said, "Industry understands the main risk to workers [from epoxy resins] is via skin contact, and the correct use of personal protective equipment (PPE) and skin protectant is essential.” That may not be the case on construction job sites. Mitchell Blum, a certified safety processional for MB Safety Consulting Inc. who conducts safety training for AMPP, the U.S. association for coating manufacturers, told EHN that industry is unaware of the dangers of BADGE in epoxy resin coatings because there’s little research on it and no OSHA requirements. “When you look at that very specific ingredient, there's not a lot of information,” he said, adding that the recent studies on BADGE that EHN sent him “do not reflect, at this point, regulatory ideas. We don't have a reference as far as good, bad, [or] what to do.” That’s especially true about research on skin issues, he said, “which are brand new to all of us. There are many non-regulatory people, universities and governmental agencies conducting studies as to how chemicals can permeate the skin. Until there is a regulatory review, testing of the skin will not happen in the construction industry anytime in the near future.” The coating industry focuses its safety resources on protecting workers who remove old paints before applying new coatings because of the high lead content in older paints, said Blum, whose main clients are bridge painting contractors. “We’re suited up; we have a standard; we follow regulatory ideas. But on the coating application side, we are so far behind what we need to do. We don’t protect workers at this point.”The best chance at worker protection The American Chemistry Council reports 13.1 million construction workers handle epoxy resins in the U.S. Credit: Jeriden Villegas/Unsplash Meanwhile, back in Boston, the River Street bridge awaits repairs while the Massachusetts Department of Transportation completes the design phase. A general contractor hasn’t been chosen for the job, but with no OSHA limits to force contractors to protect the painters applying BADGE-laden epoxy resin coatings, union safety training — and membership — offer painters their best chance at protection. “A union employee has routes,” Seal said. “They can go to a business agent and say, ‘this is what's going on at the job site. I'm afraid I’m going to get hurt. I’m afraid I’m going to get killed.’ And then the business agent steps in and takes care of the issue. A non-union person, an immigrant person, they don't have an out.” Seal hopes the union’s training programs will help motivate its members to put safety first and shift the risk-taking bravado that permeated the trade when he started out 38 years ago. “We really hit heavily on the fact that the chemicals that you're getting in your body might not affect you during your career, but when you decide to retire, you might have issues. That's why lifespans have been really short in the construction trades.” As for his own exposures on the job, Seal tries not to worry. “Right now, my health is good,” he said. “But I still worry that I'm going to go to the doctor one day, and they're going to tell me that, hey, you have issues because of the time in life that I started the trade." This reporting is part of BPA's evil cousin: an ongoing series on the hazards and regulatory blind spots associated with BADGE, a chemical cousin of BPA. The series is generously supported by the Fine Fund.
BADGE is one of thousands of harmful chemicals that commercial painters may be exposed to, according to the National Institute for Occupational Safety and Health, or NIOSH. Paints and coatings are complex mixtures of pigments, binders or resins, solvents, filler chemicals, and, increasingly, nanoparticles. The World Health Organization’s International Agency for Research on Cancer, or IARC, has classified the occupation of painter as a definitive Group 1 cancer risk, citing increased risk of lung and bladder cancer and mesothelioma, and limited evidence for childhood leukemia associated with maternal exposure as a painter. There is not enough evidence, however, to pinpoint which chemicals are causing the increased cancer risk.
Epoxy resins, within paint systems, are also complex mixtures. They typically contain two components that the worker mixes prior to applying the product. Part A contains the resin material, which is often BADGE and other diluents, and Part B contains solvent blends, polyamine hardeners or catalysts, nanomaterials and other additives including crystalline silica and flame retardants. Once the two parts are mixed, they react and form other chemicals.
“We are dealing with over 100 chemicals in these mixtures, prior to mixing A and B,” and then the mixing creates new chemicals, and “every single particle in the aerosol is this complex mixture of tens and tens of chemicals,” Dhimiter Bello, professor and associate dean for research at the Zuckerberg College of Health Sciences at the University of Massachusetts Lowell, told EHN.
Nevertheless, he added, “BADGE is a significant dominant exposure in epoxy systems. By all metrics we can prioritize the chemical at the very top as a chemical of concern.”
Workers may be exposed to BADGE, nanoparticles (which can carry chemicals deep into the lungs) and other chemicals while mixing the two parts, applying the product, and during the time it takes for the material to cure or harden. Curing can take anywhere from a few hours to days, depending on the product.
A spokesperson for the American Chemistry Council, Tom Flanagin, acknowledged in an email that, “Before the curing process, the starting building blocks, resins and hardeners may show hazardous properties and can produce irritating or sensitizing effects.” But he added that following basic precautions outlined in safety data sheets “helps epoxy systems to be handled safely.”
The curing process especially worries Ken Seal, an apprenticeship training representative at the International Union of Painters and Allied Trades Finishing Trades Institute, because safety data sheets don’t provide information on the chemicals created by the reaction. “When you mix epoxies together, and you’ve got that exothermic reaction going on, there's no [safety data sheet] out there that tells me what that reaction is.”
“If you've ever done an epoxy floor system, and you watched it curing, you can see a haze coming off the floor… and, wow, that's got to be dangerous,” he said.
The American Chemistry Council reports 13.1 million construction workers handle epoxy resins in the U.S. Thousands of new construction projects funded by the Infrastructure Investment and Jobs Act will increase epoxy resin use, and worker exposures.
More than 2,800 bridge projects were underway as of November 2022 with funding from the Infrastructure Act and many more projects are yet to come, along with hundreds to thousands of port, rail and clean transportation and water projects. Some 800,000 construction jobs will be created by the law, according to the U.S. Department of Labor.
“With that increased work volume and workload, you're going to see an increase in risk and hazard to workers,” Bernie Mizula, director of Environmental Health and Safety at International Union of Painters and Allied Trades Trades Institute, and a certified industrial hygienist and certified safety professional, told EHN.
If substances used on job sites are “very dangerous,” he continued, “we need to remove those things and try to substitute them with something less dangerous for the workers.” If that’s not possible, there’s a “hierarchy of controls,” he added, starting with engineering solutions, like ventilation, moving next to administrative controls (such as training requirements and health and safety site programs) and finally moving to personal protection — gloves, chemical resistant suits and respirators. Often, multiple controls are needed.
The International Union of Painters and Allied Trades provides a lot of training to its members about job hazards and how to protect themselves. “But we can only go so far because the employer has to have a written safety program and they have to train the workers,” Mizula said, adding that the general contractor on a construction site has overall responsibility for safety including providing a written hazard communications program and accessible means to all the safety data sheets for every chemical used on site.
OSHA spokesperson Kimberly Darby wrote in an email that, “OSHA is not pursuing regulatory action specific to epoxy resins and/or BADGE at this time. However, other current OSHA standards apply,” including regulations for hazard communication, respiratory protection and what’s known as the General Duty Clause.
The General Duty Clause is a catchall, or fail-safe, that inspectors can use when clear job hazards are present but there is no specific standard requiring protective measures. However, it’s “a much higher bar for the inspector,” David Michaels, an epidemiologist and professor at the George Washington University School of Public Health who served as Assistant Secretary of Labor for OSHA from 2009 to 2017, told EHN. Plus, he added, “If OSHA went into these workplaces, it wouldn’t even be clear what they would be measuring for” because there are no standards, or monitoring methods.
A chemical like BADGE doesn’t have a legal exposure limit, added Michaels, because “the OSHA standard setting process is broken.” First, it takes a tremendous amount of time and resources to develop a new standard. The agency must assess the economic and technological feasibility of controls and work with NIOSH to conduct human health studies to show that significant risks result from exposure and that a proposed standard would reduce those risks.
“You have to show that people are getting sick,” he said. “You can't just say animal studies suggest people will be sick. You need human studies to be able to make the statement that you will reduce exposure.”
Moreover, “OSHA knows from historical experience that every health standard will be contested in court by industries that are forced to make investments to protect workers, and they want to be sure that a standard is airtight,” he said.
The rigorous technical requirements for an OSHA standard are why the intervention-focused research of Dhimiter Bello and his wife, Anila, a research professor in the Department of Public Health at the University of Massachusetts Lowell, is so important. They not only monitored exposures to BADGE and its metabolites in humans, they studied how bridge painters were using personal protective equipment (i.e., respirators, gloves and coveralls) on job sites and how that may have correlated with their urinary levels of the chemical. The study group was too small for the Bellos to reach conclusions about the effectiveness of different types of personal protective equipment, but their research could help inform future NIOSH studies.
ACC spokesperson Tom Flanagin said, "Industry understands the main risk to workers [from epoxy resins] is via skin contact, and the correct use of personal protective equipment (PPE) and skin protectant is essential.” That may not be the case on construction job sites.
Mitchell Blum, a certified safety processional for MB Safety Consulting Inc. who conducts safety training for AMPP, the U.S. association for coating manufacturers, told EHN that industry is unaware of the dangers of BADGE in epoxy resin coatings because there’s little research on it and no OSHA requirements.
“When you look at that very specific ingredient, there's not a lot of information,” he said, adding that the recent studies on BADGE that EHN sent him “do not reflect, at this point, regulatory ideas. We don't have a reference as far as good, bad, [or] what to do.”
That’s especially true about research on skin issues, he said, “which are brand new to all of us. There are many non-regulatory people, universities and governmental agencies conducting studies as to how chemicals can permeate the skin. Until there is a regulatory review, testing of the skin will not happen in the construction industry anytime in the near future.”
The coating industry focuses its safety resources on protecting workers who remove old paints before applying new coatings because of the high lead content in older paints, said Blum, whose main clients are bridge painting contractors. “We’re suited up; we have a standard; we follow regulatory ideas. But on the coating application side, we are so far behind what we need to do. We don’t protect workers at this point.”
The American Chemistry Council reports 13.1 million construction workers handle epoxy resins in the U.S.
Meanwhile, back in Boston, the River Street bridge awaits repairs while the Massachusetts Department of Transportation completes the design phase. A general contractor hasn’t been chosen for the job, but with no OSHA limits to force contractors to protect the painters applying BADGE-laden epoxy resin coatings, union safety training — and membership — offer painters their best chance at protection.
“A union employee has routes,” Seal said. “They can go to a business agent and say, ‘this is what's going on at the job site. I'm afraid I’m going to get hurt. I’m afraid I’m going to get killed.’ And then the business agent steps in and takes care of the issue. A non-union person, an immigrant person, they don't have an out.”
Seal hopes the union’s training programs will help motivate its members to put safety first and shift the risk-taking bravado that permeated the trade when he started out 38 years ago. “We really hit heavily on the fact that the chemicals that you're getting in your body might not affect you during your career, but when you decide to retire, you might have issues. That's why lifespans have been really short in the construction trades.”
As for his own exposures on the job, Seal tries not to worry. “Right now, my health is good,” he said. “But I still worry that I'm going to go to the doctor one day, and they're going to tell me that, hey, you have issues because of the time in life that I started the trade."
This reporting is part of BPA's evil cousin: an ongoing series on the hazards and regulatory blind spots associated with BADGE, a chemical cousin of BPA. The series is generously supported by the Fine Fund.
Public data from a network of state air monitors around the Houston Ship Channel is hard to interpret and is often inadequate, leaving Latino-majority neighborhoods like Cloverleaf unaware of whether the air they breathe is safe.
Public data from a network of state air monitors around the Houston Ship Channel is difficult to interpret and often insufficient, leaving majority-Latino neighborhoods like Cloverleaf unsure whether the air they breathe is safe.
“It’s a win and a step forward.”
Dr. Lisbeth Iglesias-Ríos highlights her latest research examining poor work and health conditions for Michigan farmworkers.
Alejandra Martinez and Wendy Selene Pérez will report on the Texas Gulf Coast, focusing on environmental health, environmental justice and the impacts of the petrochemical industry on communities.
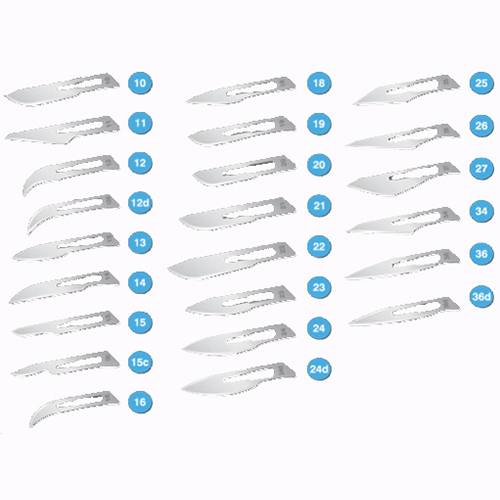
Disposable Products List “It is a victory and a step forward.”