Rodger Talbert shares how to identify dirt showing up on powder-coated film and where it comes from.
Over more than 30 years of annual compensation reviews, I have compiled a list of Dos and Don’ts that we follow at compensation review time and throughout the year. Alloy Sheet

Every year, improper chemical handling in industrial environments leads to injury and significant financial loss. Read about how to stay safe.
In the first part, a summary is presented on recently established nanotechnology initiatives in various countries around the world. Program funding levels and core activities will be compared to provide a basis for assessing business opportunities for various industries. The second part of the paper looks at specific examples of nanostructures made by electrochemical methods currently at various stages in their development, or already in use.
Users should be aware of differences in application performance, cure response and coating performance before making the change from a traditional TGIC polyester powder coating to a TGIC-free alternative.
With advantages over dry blasting such as cleaner parts, more consistent finishes, a cleaner work environment, a higher level of process control and the ability to automate, wet blasting has virtually no limitations when used for coatings preparation.
Products Finishing rounds up some of its recent travels — from international trade shows to facility tours to legislative meetings regarding environmental regulations affecting the finishing community.
With customer service experience in his background, this powder coater started his shop on a whim and has grown the business by keeping clients’ needs at the forefront.
Columnist Rodger Talbert explains the difference between a five-stage washer and a three-stage washer, and how one provides better corrosion protection over the other.
After slowing contraction for each of four months straight, Finishing activity leveled off in April. The scenario is similar across manufacturing segments, perhaps reflecting increased conservatism as interest rates and inflation fail to come down.
In this high-level overview of wastewater system maintenance and upgrades, Robin Deal and Brian Greene will review the critical components required for a fully-functional system and discuss their expected life span. Learn to navigate factors such as material degradation and technological advancements, examine the effects, and address issues of chemical usage on the equipment. This webinar is designed to equip you with the knowledge needed to ensure your wastewater system remains in optimal condition, highlighting the importance of understanding both the hardware requirements and the chemical interactions that can influence system longevity and performance. By implementing proactive maintenance strategies and informed chemical management practices, you can enhance the reliability and efficiency of your wastewater infrastructure, ultimately contributing to environmental sustainability and public health protection. Agenda: Essential equipment for wastewater systems Life span considerations for wastewater systems Impact of chemical usage on wastewater equipment
But is chemical removal or biological removal better for your operation? Or maybe it is a combination of the two for the knockout punch? Chemical removal has a long track record of proven success and is readily available, cost-effective and affords ease of operation. Biological removal is used as a final polish to achieve permit limits and reduce disposal costs. These microorganisms work under aerobic and anaerobic conditions with no caustics or acids as to not cause harm to pipes or wastewater equipment. During this webinar, you will learn about how to implement a total wastewater system that will ultimately have you using less chemistry. Agenda: When would you use chemical vs biologics for wastewater treatment — or can you use both? Who should consider using biologics for wastewater treatment? What do you need to know about maintaining a biologic system?
Zirconium conversion coatings provide advanced bonding and anti-corrosion treatment for all metals. They are formulated to replace conventional iron or zinc phosphate products in pretreatment applications with environmental, energy and wastewater treatment advantages. During this lively debate, our experts will help you decide which process will pack the bigger pretreatment punch for you – or will it be a combination of both? Agenda: Advantages and disadvantages of each application type Optimizing your process for reducing chemical consumption and cost Regulatory issues to be aware of
Wastewaters from metal finishing, production and cleaning processes may contain a number of contaminants that require removal to either compliantly discharge the wastewater or reuse it within your facility. Treatment for recovery and reuse sounds good — but is it appropriate for your wastewater and your process? If recovery is suitable, how do you accomplish it and what are the benefits? In this webinar, Evoqua Water Technologies will discuss applications, treatment and smart technology solutions for wastewater recovery, including a real-life example that resulted in improved operational efficiency. Agenda: Typical metal processing wastewater contaminants and conditions Points to consider when deciding if wastewater recovery makes sense Technologies — such as ion exchange and reverse osmosis — for wastewater recovery Digitally-enhanced ion exchange wastewater recovery How digitally-enhanced wastewater recovery can benefit your process and facility
A key component to attaining the most reliable and accurate measurements is the proper use and application of the correct calibration standards, tailored to the measurement task. Achieving accurate and reliable measurements increases quality, improves manufacturing efficiency and saves valuable resources. Taking all of this into account is the goal of coating thickness measurement. Please join Rob Weber and Melissa Agneta in this webinar as they discuss the calibration standard options and best practices for X-ray fluorescence (XRF) and dry film thickness (DFT) measurement instruments. Agenda: Instrument verification vs. calibration Different types of standards available for XRF and DFT guages Benefits of ISO 17025 traceable standards Recertification of standards for ISO compliance
After years of speculation and discussion, several factors have recently aligned to jumpstart a rapid industry movement in the switch from decorative hexavalent to trivalent plating. Across the industry, process and color standards are being adapted, RFQs are circulating and OEMs need shops who are equipped and ready. Applicators facing the decision-making process need to be prepared. There are a variety of conversations taking place globally and throughout the automotive industry on the use of sulfate vs. chloride and this webinar will address that discussion head-on, reviewing the pros and cons of each. Columbia Chemical will delve into the extensive field study tests outlining performance, color stability and corrosion results, and will provide an evaluation of new heat treatment data comparing the systems. Finally, it will provide an operational overview and cost comparison to aid in the decision making. Applicators, OEMs and Tier suppliers, design and materials engineers, and quality control will all benefit from this presentation. Agenda: Review of the pros and cons of chloride vs. sulfate Extensive field testing overview Evaluation of new heat treatment data Line adjustments: installation, operational overview and cost comparison
The course consists of 10 lessons. Each one contains a wealth of valuable, practical information. And if you score 70 or above on the optional exam, you’ll receive 1 credit toward certification as a Master Surface Finisher. MSF is the world’s most respected – and most widely recognized – designation for finishing industry professionals. Those passing 6 course exams earn the coveted MSF designation. Dates: June 4-7, 2024 Registration Deadline: June 8, 2024 Who Benefits: This training program is beneficial for operators and supervisors of contract and captive shops performing zinc and zinc alloy plating. The course is also beneficial for industry sales personnel. Goal The goal of this course is to provide students with information related to the metallurgy and corrosion behavior of zinc coatings. Students will also learn the differences between the various zinc plating and zinc alloy plating processes, including potential problems and how to prevent and solve them. The lessons in this course prepare students for a certification examination designed to demonstrate knowledge of technologies used in precious metals plating. At the conclusion of this course, attendees can expect to: Understand the basic behavior of zinc and zinc alloys in retarding the onset of corrosion in steel and other base metals. Have knowledge of the metallurgy and basic chemical principles involved in zinc and zinc alloy plating. Understand how barrel plating is different from rack plating. Know the various types of zinc plating solutions and be able to distinguish the features of each. Understand zinc alloy plating processes, including zinc-nickel, zinc-cobalt, tin-zinc, and tin-zinc-copper, their chemical make-up and operational conditions. Be prepared to take the examination, which is part of the Foundation MSF certification program.
The course consists of 21 lessons. Each one contains a wealth of valuable, practical information. And if you score 70 or above on the optional exam, you’ll receive 1 credit toward certification as a Master Surface Finisher. MSF is the world’s most respected – and most widely recognized – designation for finishing industry professionals. Those passing 6 course exams earn the coveted MSF designation. Dates: June 4-7, 2024 Registration Deadline: May 23, 2024 Who Benefits? This training program is beneficial for employees and supervisors working for Airline/Aerospace OEMs, aircraft rework facilities, Naval, Army, Marine and Air Force rework facilities and suppliers to the airline/ aerospace industry. Goal: The goal of this course is to provide the student with a broad range of information related to metal finishing operations that are common in the Airline/Aerospace industry.
SUR/FIN is the primary conference and trade show dedicated specifically to the surface technology industry. It is where leading surface technology companies connect, collaborate and contribute. And because it is the only conference and trade show sponsored by the National Association for Surface Finishing (NASF)—representing the $28 billion finishing industry—it attracts noted business leaders and prominent thinkers to a forum where relevant issues are addressed and technologies presented. Join noted business leaders, visionary thinkers and the who’s who of the industry as we delve into the most pressing issues and explore the latest cutting-edge technologies. Immerse yourself in an atmosphere of networking opportunities, enriching education and unbeatable collegiality. 2024 Show Dates: Wednesday, June 5: 2 p.m. – 6 p.m. Thursday, June 6: 11 a.m. – 6 p.m. Friday, June 7: 8:30 a.m. – 12 p.m.
As an annual conference and supportive community, Moms in MFG is designed exclusively to support working parents and caregivers in manufacturing. Moms in MFG is dedicated to empowering and connecting moms and caregivers in manufacturing. In addition, it aims to assist manufacturing companies in discovering how they can provide the necessary support and create a nurturing environment for caregivers in manufacturing. Through valuable content, networking opportunities, and collaboration with fellow industry professionals, Moms in MFG celebrates the unique journey of moms and caregivers in manufacturing.
MFASC Compliance Group Storm Water Pollution Prevention Plan Notice – Mandatory Training! General Industrial Storm Water Permit Required Annual Refresher Training 2024-2025 Compliance group registration form is due by June 17, 2024. Please email the form to Philip Moore 2024-2025 INSPECTION FORMS TO BE DISTRIBUTED BMP’s MONTHLY INSPECTIONS SMARTS STORM WATER SAMPLING AD HOC REPORTS ANNUAL REPORT LEVEL 1 & 2 EXCEEDANCE GROUP LEADER INSPECTIONS This is a mandatory training session for all Compliance Group Members. If you want to be a part of the MFASC Compliance Group you are required to be there!!!! *If you cannot attend – contact Philip Moore or you will be dropped from the MFASC group. **THIS TRAINING IS FREE FOR MEMBERS OF THE MFASC STORM WATER COMPLIANCE GROUP. NON-GROUP MEMBERS $950 PER COMPANY TO ATTEND. *Registrants will be e-mailed Zoom Webinar and call-in info. *Certificates will be mailed to attendees.
The Chicago Surface Finishing Foundation (CSFF) is proud to present this free training session to our members. Rectifiers need constant monitoring & maintenance for optimal performance. When an issue does arise, having a fundamental understanding of Preventative Maintenance and Troubleshooting of a rectifier will help minimize any down time. Our Presenter: Enrique "Ricky" Valentin, Project Manager for American Plating Power This Presentation will cover: Preventative Maintenance Activities The Benefits of a Preventative Maintenance Program When does Preventative Maintenance make Sense? Rectifier Preventative Maintenance Do's and Don’ts of Cleaning a Rectifier Visual Inspection Electrical Test & Troubleshooting of SCR and Switch Mode Rectifiers Registration for this event will come from the CSFF's Constant Contact REGISTER HERE
Thousands of people visit our Supplier Guide every day to source equipment and materials. Get in front of them with a free company profile.
Features stories and news on the adaptations of top shops, good habits, beneficial practices and successes that make a finishing shop a "Top Shop."
Young professionals are a vital asset to the finishing industry, and it is important to acknowledge those who are making great strides in shaping the industry's future.
Products Finishing is proud to announce a new awards program that recognizes individuals in the industry that are making important contributions to forward the surface finishing industry.
In these uncertain times, it is refreshing to hear from and learn about young talent in the surface finishing industry who are striving to make a difference within their organizations and the industry as a whole.
By replacing its immersion parts washer with a vacuum degreasing system, this machine shop is much more efficient, saving the company money, man hours and the health of the operators.
Finding a more accurate paint proportioner for its application enabled this auto parts manufacturer to save significant costs and labor while increasing capacity.
The grit wheels and discs are designed to stay sharper longer.
The EcoGun Ace features a rapid change system for color changes, making color changes faster and simpler.
Reduced ion electroless nickel technology operates at lower metal concentrations than conventional EN and has an important role in the future of sustainable EN processes.
10 Point Checklist to Improve Your Parts Cleaning Processes
A collection of four PF features that delve into the technologies, processes and people working to provide protection for the automobiles of today.
Survey and analysis, with Hubbard-Hall, of Products Finishing Top Shops benchmarking attitudes and practices concerning parts cleaning.
In this paper, a review of several process solutions, examining coolants, solvent cleaning, alkaline clean/etch and deoxidizing/desmutting, listing intended and unintended chemical reactions along with possible mechanisms that would favor corrosion formation.
by W. John Fullen, Boeing Research and Technology & Jennifer Deheck, Boeing, Seattle, Washington, USA
Editor’s Note: This paper is a peer-reviewed and edited version of a presentation delivered at NASF SUR/FIN 2014 in Cleveland, Ohio on June 10, 2014. A printable PDF version is available by clicking HERE.
Aluminum corrosion is commonly encountered when performing chemical process operations involving surface finishing, predominantly in preparation for paint application. The protective oxide film of aluminum is only stable in a pH range of 4.5 -8.5. However, many process solutions intentionally exceed this pH range for the purpose of cleaning, metal removal and subsequent smut removal. These process solutions are formulated so as not to cause deleterious pitting or preferential etching. However, the susceptibility of aluminum to pitting depends on many extraneous factors, such as chloride ion concentration, pH control and initial surface condition. Electrochemical measurements via potentiodynamic scans have been shown to be an effective tool in analyzing the propensity of certain process solutions to contribute to observed pitting conditions. In this paper, a review of several process solutions, examining coolants, solvent cleaning, alkaline clean/etch and deoxidizing/desmutting, listing intended and unintended chemical reactions along with possible mechanisms that would favor corrosion formation. Further explanation is provided for the role of incoming water that is used for process solution make-up and the myriad of rinse tanks. Recommendations are provided for electrolytic processes that might be prone to stray currents affecting auxiliary equipment and thereby introducing deleterious contaminants into process solutions as a result of the corrosion products of compromised piping, fittings and fasteners from heating and cooling units. Strict adherence to process specification controls, regular monitoring of suspect contaminants, sound housekeeping and part handling best practices can alleviate many aluminum part processing corrosion occurrences.
Keywords: aluminum, aluminum surface finishing, corrosion causes, corrosion troubleshooting
A protective oxide film of aluminum is only stable in a pH range of 4.5 to 8.5.1 Chemical operations for the metal surface of aluminum include many process solutions that intentionally exceed this pH range for cleaning, metal removal and subsequent smut removal. These process solutions are formulated to avoid deleterious pitting or preferential etching. However, the susceptibility of aluminum to pitting depends on many factors, such as chloride ion concentration, pH, dissolved oxygen in the corrosion environment and surface condition.2 Furthermore, aluminum alloys themselves can contribute to pitting problems due to preferential etching. For instance, aluminum 7075, which contains magnesium and zinc, is more prone to pitting than aluminum 2024 even though the primary alloying element is copper.3 The purpose of this paper is to highlight the major areas of aluminum corrosion that can be encountered during metal finishing operations with the benefit of effectively troubleshooting these occurrences when they inevitably happen.
Pitting potential is a term used to describe the likelihood of a metal to pit when electrochemically analyzed using a potentiodynamic scan of the metal and process solution system. A Boeing R&D effort was initiated to develop a usable test method that quantifies the pitting potential of a process solution relative to a selected alloy. The scope of the research has been limited to metalworking fluids and a degreasing solution, but the test method could be applied to other chemical process solutions.
For this electrochemical potentiodynamic method, potential (volts) versus current density (amps/cm2) is evaluated. The voltage starts cathodic (negative) and is slowly ramped up while measuring current. Two key voltage levels are marked on the scan. The first is corrosion potential (ECORR), which is the potential at electronic neutrality, also known as the open circuit potential. The other key voltage level is breakdown potential (Eb), which is the potential at which the anodic polarization curve shows a marked increase in current density, leading to breakdown of the passive film and pit initiation. Consequently, the closer Eb is to ECORR, the greater the probability that pitting will occur (Fig. 1).
Figure 1 - Pitting potential scan.
The benefit of this type of measure is that the value can be compared to other process solutions or to new-versus-aged processes to determine the likelihood that a process solution contributes to pitting. It is possible, then, that pitting potential values, where EPIT = Eb − ECORR, may be determined for reference materials. These values could enable the proactive dumping of tanks before the onset of corrosion issues. For instance, this test method has conclusively demonstrated that chloride ion concentration in the range of 100 to 150 ppm in conjunction with other interacting ion contaminants could contribute to pitting. And, chloride ion concentration greater than 150 ppm would most likely cause pitting.
Pitting problems can be the direct result of incoming materials, and often spot discoloration is the result of airborne contamination, incomplete degreasing and mill residue on as-received material.4 Alloying materials compromise the passivity of aluminum, as evidenced by pitting potentials that vary based on the alloying element. Any chemical processing of a particular aluminum alloy will exacerbate areas of highly concentrated second-phase particles.5 It is known that pitting will start at the flaw in an oxide film, especially when the flaws are already present before being immersed in an aggressive solution.6 For instance, in 7075 aluminum, two major types of constituent particle are present. The first is iron-containing (Cu2FeAl7) which acts as a cathode due to its higher electrochemical potential. The other major constituent particle is the magnesium-containing laves phase (MgZn2), which is anodic relative to the aluminum matrix. These types of flaws can be readily identified since they tend to cluster in a line along the rolling direction and can significantly shorten the fatigue life of parts so affected.7
Incoming spot discoloration can be the result of airborne contamination, incomplete degreasing and mill residue. For these reasons, careful inspection of metallic raw materials is crucial since follow-on chemical processing usually only leads to exacerbating the flaws instead of improving the existing condition.
It has been reported that more than half of all occurrences of metallic corrosion have been related to contact with microorganisms.8 In metal finishing operations, coolants that are not well maintained are often first noticed when they emit an odor similar to rotten eggs. This is attributable to small amounts of hydrogen sulfide released as a byproduct of the enzymatic action of sulfate-reducing bacteria (SRB).9 Further evidence of coolants that are not well maintained is analysis of the coolant concentration using a Brix refractometer. A reading that fails to show a clear line is an indication the coolant is inundated with tramp oils (Fig. 2).
Figure 2 - Tramp oil makes reading a Brix Refractometer difficult.
Disregarding the pure synthetics, most coolants have an oil emulsion base. Left unchecked, microorganisms assimilate organic material and produce organic acids including oxalic, lactic, acetic and citric. Furthermore, biofilm formation is generally considered more of a problem in the summer months because higher temperatures increase the rate of biological processes.10 The mechanism by which microbial corrosion of aluminum occurs is thought to be the result of microorganisms removing phosphate and nitrate more rapidly than calcium or iron from the media in which they grow. By means of this selective and differential utilization of ions, microorganisms make the medium in which they grow progressively more corrosive. This concept is consistent with the relative quantities of calcium, iron, nitrogen and phosphorus found in the microbial cell.11 This phenomenon is important to realize because nitrate is known to inhibit the formation of hydrogenase, which encumbers the corrosion of aluminum.12
Effective coolant cleanout measures have made use of peroxyacetic acid (PAA). PAA is a product used commonly in the food industry and is actually an equilibrium mixture of PAA, water, acetic acid and hydrogen peroxide:
CH3COOOH + H2O ⇔ CH3COOH + H2O2
This chemical has found favored use because the kill dose is achieved at relatively low concentrations (2 to 9 ppm)13 and short contact times (1 to 3 hours). Unlike other biocides, PAA is not affected by pH and water hardness.14 Furthermore, its decomposition products of acetic acid, water and oxygen are innocuous and environmentally acceptable. Other biocides would potentially require treatment before release to a publicly-owned municipality. For metalworking fluids, the use of PAA would be just before a dump. However, at Boeing this chemical has been incorporated for in situ use for chemical process operations, such as hard-metal acid etching in the rinse tanks.15 PAA is typically sold in a much diluted concentration. One such product is Purisan, which is commonly used in the food industry.
To estimate the amount of PAA needed, a helpful mathematical expression is:
Vb = 3.785[VTρpCd/Cnρb]
Vb = volume of the Purisan to be added in liters
VT = volume of the tank in gallons
ρp = specific gravity of the rinse water or process solution
Cd = concentration of the intended dilute biocide (~1×10-5)
Cn = neat concentration of PAA in the purisan (0.052) .
ρb = specific gravity of the Purisan (1.12)
Another mechanism of metalworking-fluid induced corrosion can be caused by coolant that is allowed to dry on the part, causing a condition in which a differential oxidation cell can form (Fig. 3).16 The corrosion pattern typically resembles a halo on the part surface.
Figure 3 - Formation of differential oxidation cell.
Finally, chloride contamination in coolant alone can be enough to cause pitting corrosion directly.17
Although relatively uncommon, aluminum corrosion can be caused by using acetone to solvent-clean parts in ambient light.18,19 Aluminum alloys that are copper rich such as 2024 are photoreactive. The mechanism is that the acetone, in the presence of water, is converted to acetic acid when in contact with the copper intermetallics:20
Consequently, solvent cleaning with acetone of 2024 aluminum should be avoided.21
The most efficient means of rinsing makes use of a double countercurrent rinse (DCCR) system (Fig. 4).22 Because two rinse tanks are used, the most abundant process solution is water, which can contribute significantly to aluminum pitting issues.
Figure 4 - Double countercurrent rinse.
At Boeing, seasonal variations of pitting occurrences have been noticed. This has been attributed to increased manganese concentration in the incoming water supply, caused by manganese dioxide being deposited by chemical and biological oxidation of dissolved manganese that occurs naturally in surface and ground waters throughout the United States. Consequently, the direct galvanic action of manganese can promote severe localized attack by promoting pitting and crevice corrosion through a combination of electrochemical effects, caused by galvanic coupling between manganese dioxide and the underlying metallic surface.23 Natural levels of chlorination in municipal waters are sufficiently high that manganese reacts with diatomic chlorine to form harmful chloride ions, which are well known to be deleterious to metals.24
MnO2 + 2Cl2 + 2H2O ⇒ MnO4- + 4H+ + 4Cl- - e-
Metal ion hydrolysis acidifies the nucleation site:
Al+3 + H2O ⇔ H+ + Al(OH)+2
This attracts charge-neutralizing counter-ions (chloride) that further disrupt the oxide structure:
Al(OH)+2 + Cl- ⇒ Al(OH)Cl+
Then, with water producing acidic conditions,
Al(OH)Cl+ + H2O ⇔ Al(OH)2Cl + H+
this self-sustaining process leads quickly to stable pitting corrosion.25
Since pitting corrosion will only occur in the presence of aggressive anionic species, ubiquitous chloride ions should be monitored. They alone can cause pitting corrosion26 because chloride ions are relatively small anions with high diffusivity that can interfere with passivation.
Other ions to monitor in rinse waters are copper and carbonate, since these cations have been known to increase the number and depth of aluminum pits.27
Typically the first tankline process solution is either an emulsion degreaser or alkaline cleaner.
Since aluminum is only stable in a pH range of 4 to 9, these types of process solutions need to have a corrosion inhibitor package as part of their formulation. Sodium metasilicate (Na2SiO3) is commonly used, but as the solution ages and is continuously exposed to process temperatures above ambient (115° to 170°F), these silicates irreversibly precipitate, leaving the parts vulnerable to alkaline attack (Fig. 5).28
Figure 5 - pH versus concentration of silicates.
The basic mechanism is as follows:
STTP + heat → lower pH → loss of silicates in solution → corrosion
Sodium tripolyphosphate (STTP) is an alkalinity builder constituent, and over time with heat in a hydrolysis reaction, it releases free acid. The free acid release lowers the solution pH. The lowered pH affects the corrosion-inhibitor package component (sodium metasilicate), putting it into a phase of irreversible precipitation (Fig. 6).
Figure 6 - Corrosion caused by alkaline degreaser with depleted silicates.
To prevent the scenario that leads to the phase of irreversible precipitation, the solution pH should be monitored and maintained with the addition of hydroxide (NaOH or KOH) at a pH level dependent on the solution concentration.29
In a production setting, corrosion is at times mistakenly attributed to the emulsion degreaser tank, when in fact the cause is contaminants getting on parts upstream of the tankline. In a recent study, Boeing Research and Technology (BR&T) was asked to identify contaminants that contribute to corrosion in Brulin 815 GD (aqueous degreaser) tanks. The study30 examined the effects of processing various degrease contaminants in Brulin solutions containing varying levels of sodium metasilicate. A key finding was that the following combination of conditions causes corrosion:
The fact that several conditions in addition to the use of the proprietary lubricant need to be met to initiate corrosion demonstrates the difficulty sometimes faced when trying to identify the cause of corrosion on a part (Fig. 7).
Figure 7 - Corrosion at hole edge.
Following the alkaline process solution is a rinsing operation. If part rinsing is not performed well, silicate residues that remain on the surface and then enter an acid solution could form an insoluble salicylic acid that might contribute to spot corrosion. This type of surfactant contamination is more likely when a difference in solution surface tension is noted, or perhaps if foaming is observed to be more than usual. Surfactant types can be anionic, cationic or nonionic, so these observations are dependent on the surfactant type used in the cleaner formulation.
Even if an alkaline cleaner is pristine, a poor part load choice can create a galvanic cell, such as when a large basket is used to process a small part load (Fig. 8).
Figure 8 - Small part in large basket.
Alkaline etch cleaning has a much higher pH and is intended to perform aluminum metal removal using predetermined etch rates combined with process recipe immersion times. This process involves intended and unintended chemical reactions that need to be understood so that contamination as a result of part processing is known. Below are likely balanced mechanistic chemical reactions for aluminum parts when processed with a formulated alkaline solution containing sodium sulfide.
It also is known that aluminum and copper react with caustic at different rates, potentially leaving loose copper loose containing intermetallic particles on the surface that may lead to galvanic attack in the following rinsing operation. In a similar manner, small amounts of laves phase (MgZn2) on the part surface can lead to a defect known as galvanizing or spangling on 6063 alloys. For this reason, alkaline etch cleaners are commonly formulated with additives such as sodium sulfide (Na2S) to prevent this from occurring. Any added constituent of an etch solution needs to be measured and monitored.31
Caustic with aluminum. First, the naturally occurring aluminum oxide surface is breached yielding sodium aluminate:
2Al2O3 + 2NaOH + Na2S ⇒ 4NaAlO2 + H2S(g)
The reaction with the base aluminum yields more sodium aluminate. The bubbling coming off the part is predominantly hydrogen gas, but the characteristic sulfurous odor of hydrogen sulfide indicates that this gas also is being emitted:
2Al + Al2O3 + NaOH + Na2S + 11H2O ⇒ 3Na[Al(OH)4] + Al(OH)3 + H2S(g) + 3H2(g)
6Al + 2NaOH + Na2S + 9H2O ⇒ Al2O3 + 4NaAlO2 + H2S(g) + 9H2(g)
The resulting sodium aluminate combines with water to form a hydrate, returning to the solution some of its alkalinity:
8NaAlO2 + 16H2O ⇒ 8NaOH + 4Al2O3•3H2O(s)
Caustic with copper-containing phases. Aerospace aluminum is commonly an alloy, and a formulated alkaline solution containing sodium sulfide will likely react with the alloying element. In the case of 2000-series aluminum, the main alloying element is copper. Its sulfides contribute to the formation of a characteristic nearly-black smut layer on the part surface. This likely reaction of the alkaline solution with copper follows. The black smut layer is also a spectral effect of the aluminum base metal being etched around the lesser affected intermetallic particles.
The alloying copper phase is breached, yielding base metals:
Al2Cu ⇒ 2Al + Cu
The reaction with metallic copper yields copper sulfide, and gases:
2Cu + OH- + S-2 +H2O ⇒ Cu2S + 2OH- + H2(g)
These copper oxides remain on the surface of the part and are dark in color, accounting for why aluminum parts are nearly black when coming out of the alkaline-etch rinse tank.
Undesirable etch tank reactions. In the course of part processing, undesirable reactions are unavoidable, such as the production of sodium thiosulfate:
2Na2S + 2O2 + H2O ⇒ Na2S2O3 + 2NaOH
Excessive sodium thiosulfate production will eventually lead to the formation of free sulfur, which can accumulate visibly on the solution surface:
6Al2O3 + 3Na2S2O3 + 3H2O + Na2S + 2NaOH ⇒ 2Al(OH)3 + 3SO2 + 3S + 10NaAlO2 + H2S(g)
Furthermore, alkaline etch process solutions are prone to irreversible hydration of aluminum hydroxide. When the solution is unintentionally cooled, it could result in alumina scale:
2Al(OH)3 ⇒ 2Al2O3 + 3H2O
2AlO(OH) ⇒ Al2O3 + H2O
If there is a sudden drop in aluminum concentration, the likely cause is the precipitation of aluminum oxide along with an increase in alkalinity. High alkalinity would then lead to preferential etching.
Therefore, during times of planned or inadvertent shutdowns, alkaline etch solutions need to be fully measured for all monitored constituent concentrations, etch rate and pH before the restart of part processing.
Following alkaline processing is a deoxidizing or desmut operation, depending on whether the prior operation was alkaline cleaning or alkaline etching. These acid solutions are commonly nitric-, sulfuric- or chromic-acid based. As was covered for alkaline etch processing, deoxidizing involves intended and unintended reactions that need to be known, so that contamination from part processing is understood. As an example, below are likely balanced mechanistic chemical reactions for aluminum parts when processed with a nitric-acid based deoxidizing solution.
Nitric acid (HNO3) with aluminum
The aluminum oxides and alloying element smut-layer compounds are made soluble by being converted into their respective nitrate forms:
Al2O3 + 6HNO3 ⇒ 2Al(NO3)3 + 3H2O
Al(OH)3 + 3HNO3 ⇒ Al(NO3)3 + 3H2O
The base aluminum further reacts, producing more soluble aluminum nitrate and hydrogen gas:
2Al + 3HNO3 + 3H2O ⇒ Al(NO3)3 + Al(OH)3 + 3H2(g)
Hydrofluoric acid (HF) with aluminum
The hydrogen fluoride component in this type of deoxidizer solution has numerous mechanisms that produce soluble aluminum fluoride, hydrogen gas, and aluminum hydroxide:
2Al +6HF ⇒ 2AlF3 + 3H2(g)
8Al + 6HNO3 +24HF ⇒ 8AlF3 + 3N2O(g) + 15H2O
Some of the aluminum hydroxide reacts, further producing a duo-anionic solid:
2Al +2HNO3 + 2H2O ⇒ 2Al(OH)3 + 2NO(g)
2Al(OH)3 + AlF3 ⇒ 3AlOF(s) + 3H2O
Hydrogen fluoride is consumed with the production of soluble ammonium nitrate.
Al +3HF + HNO3 ⇒ AlF3 + NH4NO3
Nitric acid and hydrofluoric acid with copper
Similar reactions of nitric acid on the smut layer and copper portion of the intermetallic phases produce soluble copper nitrate and gases:
CuS + 2HNO3 ⇒ Cu(NO3)2 + H2S(g)
Cu + 4HNO3 ⇒ Cu(NO3)2 + 2NO2(g) + 2H2O
To a lesser degree than with aluminum, the hydrogen fluoride is consumed producing copper fluoride and hydrogen gas:
Cu + 2HF ⇒ CuF2 + H2(g)
One of the more interesting aspects in the listing of these desmutting reactions is the large amounts of hydrogen fluoride being consumed. Thus, it is understood that as a desmut tank ages, hydrogen fluoride must be replenished on a regular basis. Failing to do so can (and has) led to incomplete removal of the smut layer. The parts would come out of the following rinse tank and appear to be clean, and actually would have a water-break-free surface. However, a low level of smut layer can remain and become a loose top layer of the following anodic oxide.
Although quite rare, one undesirable desmut tank reaction can occur because of sodium thiosulfate drag-out from an aged alkaline etch tank, resulting in elemental sulfur being formed:
Na2S2O3 + 2HNO3 ⇒ S(s) + H2O + SO2 + 2NaNO3
Also, loss of free fluoride can be attributed to drag-out of sodium aluminate from the etch tank:
3NaAl(OH)4 + 6HF ⇒ 2Al(OH)3 + 6H2O + Na3AlF6
Adding to the importance of hydrogen fluoride in the desmut process is the knowledge that aluminum fluoride tends to form dialuminum hexafluoride, and thereby a loss of free fluoride occurs:
AlF3 ⇒ Al2F6
This larger compound will passivate the aluminum surface if the pH is too high. Thus, older deoxidizer tanks need more nitric acid to counteract this Al2F6 formation effect.
Oftentimes, penetrant inspection indications are the first to notice that a problem may exist with the deoxidizer process solution in the form of contamination or incomplete smut removal. At Boeing, process perturbation experiments led to the conclusion that the combination of short deoxidizer immersion time and long rinse immersion times can cause incomplete smut removal. This condition is not readily apparent during processing, since a water-break-free surface is achieved and the part has no visible discoloration. However, if incomplete smut removal is suspected, the parts could be simply inspected by white-glove hand wiping of the part surface to check for loose nonvisible smut. Of course, possibly of more concern is that this condition left unabated could lead to catastrophic paint adhesion failures (Fig. 9).
Figure 9 - Paint adhesion failure during assembly.
Deoxidizer process solutions also are prone to anionic (chloride, Cl-) and cationic (copper, Cu+1, Cu+2) contamination that directly results in pitting. For this reason, the copper concentration for several process solutions is required to be measured and monitored.32 Some deoxidizers have additive products, called toners, to counteract the inevitable increase in copper contamination. For those that do not have additive products, the current prescribed remedy is to monitor and dump when approaching the copper limit.
At Boeing, process experience has led to the realization that chromium-based deoxidizers are superior to iron-based deoxidizers when used before chromate conversion coatings.33 The reasoning for this awareness follows.
For iron-based deoxidizers, ferric sulfate is present to oxidize the cuprous (Cu+1) residue that develops on aluminum after alkaline etching to cupric (Cu+2) sulfate. The cuprous is insoluble, whereas the cupric is soluble. As part of the reaction, the soluble ferric will convert to the insoluble ferrous. The nitric present in the product is there to convert the ferrous back to ferric, allowing it to continue oxidizing the copper. In addition, nitric can deoxidize the aluminum, but it will be consumed very quickly:
Fe+3 + Cu+1(s) ⇒ Fe+2(s) + Cu+2
HNO3 + Fe+2(s) ⇒ Fe+3
The ferrous that is not converted back will settle in the tank, or be circulated as an insoluble particle, and if enough of this material is present, it will carry over to the rinse tank. If the rinse is not properly maintained, it will carry over to the conversion coating tank, affecting salt spray performance.
If sodium sulfide (Na2S) is allowed to enter the deoxidizer bath from the alkaline etch, the sodium sulfide will compete with the ferric sulfate. Since the sodium sulfide is not as strong an oxidizing agent, it will not convert as much of the cuprous to cupric, thus allowing copper to remain on the surface of the aluminum and thereby negatively affect salt spray performance of the conversion coating.
The term stray current often is misused when an investigator is trying to capture some factors that cause problems such as pitting, burning or arcing. Stray and leakage current refer to those electrical currents that flow along paths other than between the cathodes and the parts. The most relevant use of that phrase is as it relates to powered equipment, where the current is no longer confined to the unit. However, standard electrical protocols relating to use of grounding and dielectric unions should mitigate current leakage of this sort.34 Testing can be done using a clamp-on ammeter to measure the stray current levels in the safety ground network at selected points throughout the facility.
Auxiliary equipment should be protected from stray current by the following guidelines.35 Water and steam connections to heat exchangers (and to any other electrically conducting immersion heater) should contain dielectric unions in both the inlet and outlet lines, and use nonconductive bolt washers and sleeves on mounting hardware to avoid making an electrical ground through which stray current will pass. As an example, steam coils can be cathodically protected by making good connection to tank walls. Use of a dielectric union is recommended to prevent stray current from flowing to adjacent equipment. Evidence of auxiliary equipment stray current is usually manifested in the associated piping, and not the parts but the resulting corrosion products will contaminate the process solution with soluble and insoluble iron (Fig. 10).
Figure 10 - Evidence of auxiliary equipment stray-current protocols being violated.
In the design and construction of an electrolytic process, consideration should be given to isolation of the tank itself. As an example, plating process specifications36 have flagnotes specific to this issue such as “Tank may be lined with insulation material to prevent stray current. Use a lining material that is chemically inert.”
Apart from defective equipment, another cause of unwanted electrical currents is known to be errant acid on tank lipboards and tank sides, known as operator-induced stray and leakage currents. These acid coated surfaces can provide a preferred current path other than through the electrolyte. This problem is not always readily detected. One observation of this problem is as follows:37
A load of parts are immersed in the tank and the power is activated. The voltage climbs to the normal hard anodizing voltage, initially about 20 to 25 V, and the estimated current is being drawn. After a few minutes or less, the voltage drops to about 15 V or less, yet the current remains constant. The rack is withdrawn from the solution. All electrical contacts are tight. After thoroughly rinsing all the non-conductive buss bar supports and the tank lipboard, the unexpected voltage drop is eliminated. Therefore, to avoid operator induced stray and leakage currents, the shop should at least daily rinse all tank surfaces and related facility components which are exposed to acid spray from the process.
All tank facilities used for electroprocessing need to use electrical ground connections. The integrity of these connections should be checked regularly. The detrimental effects of uncontrolled currents are especially pronounced in high voltage processes such as hard anodizing.
Boric-sulfuric acid anodizing (BSAA)38 replaced chromic acid anodizing (CAA)39 for commercial aircraft applications in the mid-1990s. Because of reformulation40 (incorporation of organic additive sodium benzoate), this process solution was made more resistant to biocontamination, especially from the fungal matter of Alternaria species.41 A side benefit is that this additive can form a stable complex with aluminum ions and the part is then theoretically further protected from direct pitting attack by chloride contamination.42
Part handling is an all-too-often-ignored part of the process that also can directly cause corrosion problems. Ungloved hands are a prevalent source of FOG (fat, oil, grease) laden contaminants that entrain anionic contaminants such as chloride. Also, placing parts that are still slightly wet onto clean Kraft paper in an attempt to keep freshly processed parts clean can lead to sulfate contamination. All papers are manufactured using a sulfuric-acid digestion process and when wetted, a small amount of that acid is leached from the paper that is in direct contact with the part.
Aluminum corrosion is commonly encountered when performing chemical process operations involving surface finishing, predominantly in preparation for paint application. Prior research and development efforts have established electrochemical measures using potentiodynamic scans to be an effective tool in analyzing the propensity of certain process solutions to contribute to pitting conditions.
Oftentimes it is only during chemical process operations that flaws of incoming materials are revealed. However, when the part details are pristine, many process operations in the tankline can be problematic. Typically, the first process fluids encountered are coolants, followed by solvent cleaning, alkaline clean/etch and deoxidizing/desmutting. Several of the tankline operations involve intended and unintended chemical reactions. Mechanistic evaluations of these processes were provided so that the propensity for aluminum corrosion can be better understood.
Further explanation was provided for the role of incoming water that is used for process solution make-up and the myriad of rinse tanks. Seasonal variation can account for mineral contamination of plant water used, and chemical reactions were provided as possible causal conditions for observed pitting.
When electrolytic processes are employed, stray current can affect auxiliary equipment, thereby introducing deleterious contaminants into process solutions because of the corrosion products of these piping, fittings and fasteners for heating and cooling units.
Finally, improper part handling can cause aluminum corrosion problems such as when wet parts are placed on brown Kraft paper.
Strict adherence to process specification controls, regular monitoring of suspect contaminants and sound general housekeeping best practices will alleviate many aluminum part processing corrosion occurrences.
1. J.D. Minford, Handbook of Aluminum Bonding Technology and Data, M. Dekker, New York, 1993; p. 110.
2. A.M. Beccaria & G. Poggi, British Corrosion Journal, 21 (1), 19-22 (1986).
3. W.B. Engel, Proc. Conf. Nat’l. Assoc. Corros. Eng., 1970; pp. 588-596.
4. J.W. Dunn, “Spot Discoloration on 7000 Series Aluminum Alloys,” Boeing (1963).
5. G.E. Kiourtsidis, et al., Corrosion Science, 41 (6), 1185-1203 (1999).
6. J.R. Galvele, in Passivity of Metals, R.P. Frankenthal & J. Kruger, Eds., The Electrochemical Society, Princeton, NJ, 1978: pp. 285-387.
7. N. Birbilis & R.G. Buchheit, J. Electrochem. Soc., 152 (4) B140-151 (2005).
8. A. A. Gerasimenko, Zashchita Metallov, 15 (4) (1979) (in Russian).
9. S.G. Choudhary, Hydrocarbon Processing, 77 (5), 91-102 (1998).
10. B. Little, P. Wagner & F. Mansfield, International Materials Review, 36 (6), 253-272 (1991).
11. G.C. Blanchard & C.R. Goucher, Developments in Industrial Microbiology, 6, 95-104 (1964).
12. Air Force Aero Propulsion Laboratory, “Mechanism of Microbiological Contamination of Jet Fuel and Development of Techniques for Detection of Microbiological Contamination,” Technical Documentation Report No. APL-TDR-64-70, Part I (1964).
13. J.F. Kramer, Proc. NACE Corrosion/1997, Paper No. 404, NACE International, Houston, TX, 1997.
15. WJ Fullen, Plating & Surface Finishing, 90 (5), 10-15 (2003).
17. E.W. Pfaff & F. Luke, Boeing Manufacturing Development Report (MDR) 2-41051, “Pitting Corrosion Problem of 7000 Al Alloys Production Parts,” (1990).
18. C.R. Clayton, G.P. Halada & S.V. Kagwade, in Proc. Symposium on Critical Factors in Localized Corrosion III, Jerome Kruger 70th Birthday Symposium, The Electrochemical Society, Pennington, NJ, 1999; pp. 223-233.
19. S.V. Kagwade, et al., J. Electrochem. Soc., 47 (11), 4125-4130 (2000).
20. SV Kagwade & CR Clayton, in Passivity and Its Breakdown, PM Natishan, et al., Eds., The Electrochemical Society, Pennington, NJ, 1998;p.631.
21. S.V. Kagwade & C.R. Clayton, Electrochimica Acta, 46 (15), 2337-2342 (2001).
22. JK Unangst & WJ Fullen, Plating & Surface Finishing, 91 (12), 44-49 (2004).
23. W.H. Dickinson & R.W. Pick, Proc. NACE Corrosion/2002, Paper No. 02444, NACE International, Houston, TX, 2002.
24. J. Tverberg, K. Pinnow & L. Redmerski, Proc.NACE Corrosion/1990, Paper no.151, NACE International, Houston, TX, 1990.
25. Z. Szklarska-Smialowska, Corrosion Science, 41 (9), 1743-1767 (1999).
26. G.S. Frankel, J. Electrochem. Soc., 145 (6), 2186-2198 (1998).
27. D. Wong & F.H. Cocks, Study of Aluminum Corrosion in Aluminum Solar Heat Collectors Using Aqueous Glycol Solution for Heat Transfer - Annual Technical Progress Report July 30, 1979 – July 31, 1980, U.S. Department of Energy (1980).
28. C. Saunders, K. Evans & N. Sagers, Wash Solution Bath Life Extension for the Space Shuttle Rocket Motor Aqueous Cleaning System, Thiokol Corporation, Brigham City, UT, 1991.
29. Boeing Process Specification BAC5763, revision L, “Emulsion Cleaning and Aqueous Degreasing” (Nov. 27, 2013).
30. Boeing Summary Report (SR) 12724 (Nov. 28, 2011).
31. Boeing Process Specification BAC5786, revision L, “Etch Cleaning of Aluminum Alloys” (Aug. 2, 2011).
32. Boeing Process Specification BAC5765, revision V, “Cleaning and Deoxidizing Aluminum Alloys” (Nov. 14, 2011).
33. WJ Fullen, Metal Finishing, 104 (12), 34-42 (2006).
34. Boeing Standard D38201-12, “Grounding and Shielding” (Aug. 4, 1999).
35. Boeing Standard D38512-19, “Chemical Heat Exchangers, In-Tank, Heat Exchanger/Plate” (Oct. 13, 2006).
36. Boeing Process Specification BAC5722, revision E, “Copper Plating” (June 3, 2008).
37. Boeing MDR 2-36249, “Hard Anodize Process Problems” (1981).
38. Boeing Process Specification BAC5632, revision D, “Boric Acid − Sulfuric Acid Anodizing” (Aug. 3, 2004).
39. Boeing Process Specification BAC5019, revision U, “Chromic Acid Anodizing” (June 3, 2005).
40. JC Oleund, WJ Fullen & DL Crump, US patent 6,149,795 (2000).
42. Y. Isobe, S. Tanaka & F. Hine, Corrosion, 46(10), 798-803 (1990).
W. John Fullen has been with the Boeing Company for more than 29 years, at present in the Boeing Research and Technology (BR&T) organization, first in advanced composites but predominantly in chemical technology in support of tankline operations and the Boeing supply base. Prior to that, he worked at H.B. Fuller Co. in the area of adhesives. He holds a B.S. in Chemical Engineering from the University of Minnesota.
Jennifer Deheck was employed at Boeing during the course of this study and worked as a Chemical Process Engineer.
How can I plate copper on aluminum?
How can you calculate the cost of powder coating a component if you only know its surface area? Powder coating expert Rodger Talbert has the answer.
Applications, plating solutions, brighteners, good operating practices and troubleshooting.
Choosing the best process for your operation.
New tools reduce cost and waste, lower manufacturing footprint of powder coating operations.
Hubbard-Hall wastewater treatment specialist Robin Deal discusses the latest trends in wastewater management.
Although Chevrolet has announced the end of the Camaro and Dodge is offering “Last Call” editions of the Charger and Challenger, the Ford Mustang is launching to its seventh generation.
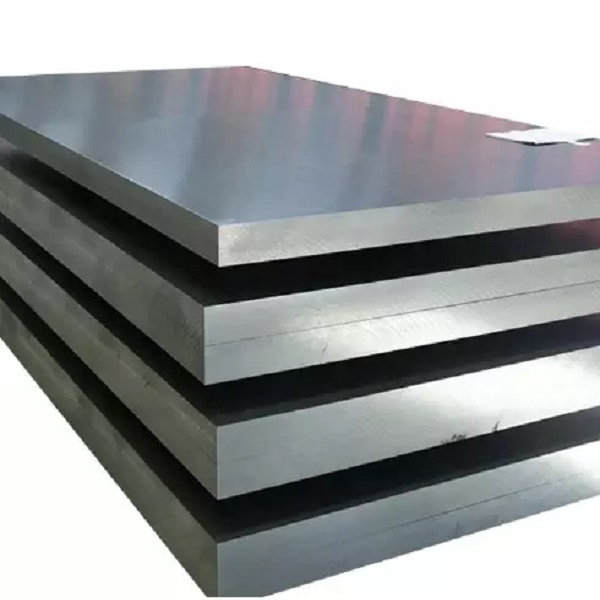
Alu Foil Products Finishing is the media brand devoted to all things finishing. Electroplaters, anodizers, liquid and powder coaters have all come to rely on Products Finishing magazine as their No. 1 source for surface finishing news and technology for more than 80 years. About Us