As equal rights icon Jo March would say: "Women!" With March being Women's History Month, we thought it'd only be right to…
Orlando is slamming itself onto Florida's foodie destination map this year. With nearly a hundred new restaurants and eateries set to make… Juice Glass Packing Machine
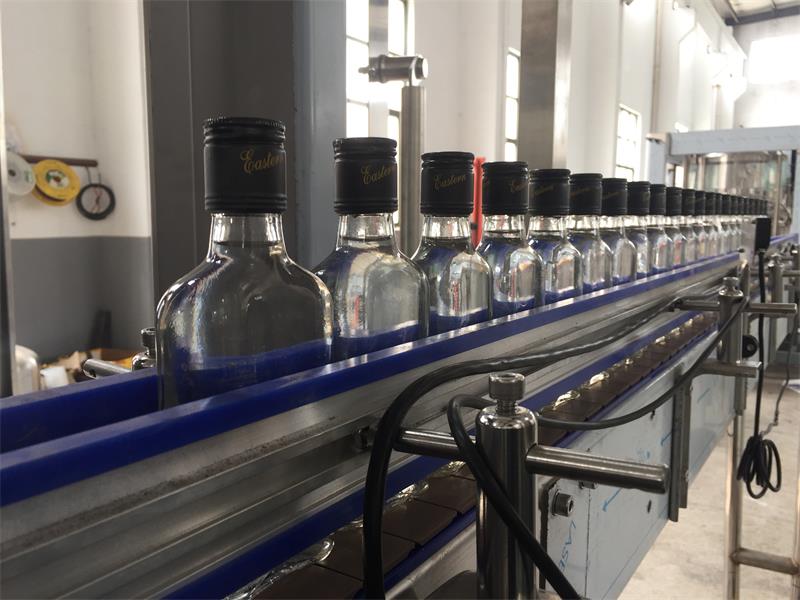
Feeling lucky? As we close in on St. Patrick's Day, Orlando Weekly turned to the city's best Irish pubs and restaurants perfect…
Now we know: Orlando can definitely savor some whiskey. This year at a new venue, Orlando Weekly's 2023 Whiskey Business took over…
Tuesday night was Valentine's Day in Orlando, sure, but it was also the night of the first "Love Hurts," a spicy eating…

Water Production Line Last weekend Audubon Park's Redlight Redlight hosted a Galentine's Day brunch and market. Locals ignored the oft-blustery weather and came out in…